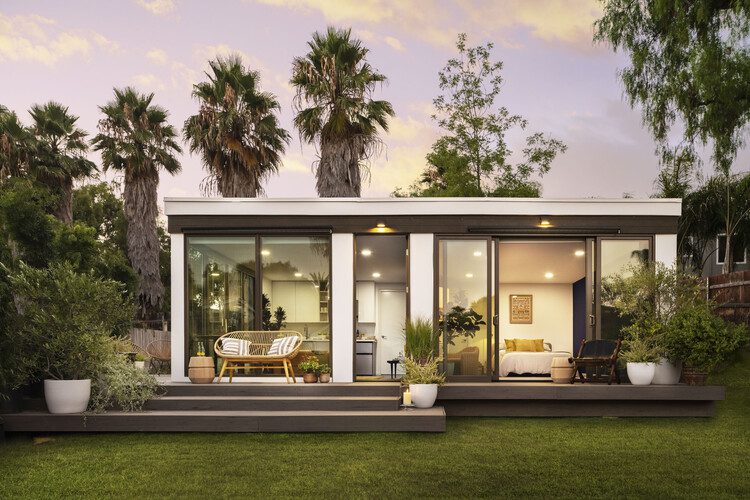
As construction materials costs increase, builders and developers are seeking alternatives to traditional home construction methods to address housing shortages. In response, an expanding construction technology field is the 3D printing sector. This technology promises quicker, cheaper construction and the potential to extrude local and recycled materials. However, due to the slow-changing nature of the construction industry, a radical shift involving large-scale 3D-printing machines on-site and a complete overhaul of the construction process seems unlikely shortly.
Prefabricated 3D printing modular housing offers a compelling solution, providing the benefits of 3D printing advancements while leveraging standard construction machinery and labor. In off-site 3D-printed construction, there is no need to transport massive 3D-printing machines on-site. Instead, components are printed in a controlled environment and then assembled on-site. These types of 3D-printed residential modular kits of parts are already being manufactured and are attracting significant investment.

Extensive research and technological advancements in 3D printing aim to expedite construction, reduce costs, and promote the use of decarbonized materials. According to a 2018 study in the academic journal IOP Conference Series Materials Science and Engineering, 3D printing in construction can cut costs by at least 35%. This technology also allows for a myriad of material exploration, which has led to extensive research into recycled, energy-efficient, and local material extrusion. Major tech firms like ICON have been doing much research in this area. With projects built in Austin, they have explored opportunities using low-carbon concrete, aesthetic possibilities, and user customizability of 3D-printed homes.
Related Article
From Decarbonization to Ornamental Expression: Innovative 3D Printed Projects From 2023
While exciting, most of this on-site printing technology faces challenges that make its immediate widespread implementation unlikely. These include questions on the quality of the material extruded on-site, site constraints regarding the scale of the machinery needed, and the expertise required to operate such machinery.
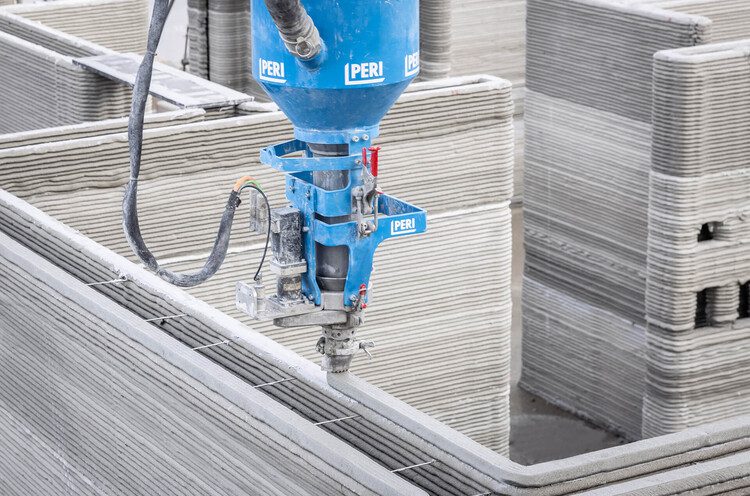
On the other hand, the off-site modular 3D printing of homes shows excellent potential for immediate implementation. In addition to the advantages of 3D printing, producing printed off-site modular housing units or kits of parts allows for higher quality of built elements, reduced waste, and even less costly production due to the possibility of producing them in large quantities. In an interview with Habitat for Humanity, Adithya Jain, co-founder of Tvasta Manufacturing Solutions, mentions that prefabricated 3D-printed homes can be more cost-efficient than on-site 3D printing and work better within crowded urban environments. Their 3D-printed India-based projects are made of homes made in pieces in their studio and then assembled on-site.
Mighty Buildings is a San Francisco-based startup making advancements in the prefab 3D printed field. They produce 3D-printed prefabricated kits of parts for residential structures. Their kit systems are made of pre-built, factory-made 3D printed panels that can be customized to any plan. These are then assembled on-site, cutting construction times by more than half. According to an interview with Tech Crunch, their composite material is made of 60% recycled glass. It cures with ultra-violet light and has five times concrete’s tensile and flexural strength while weighing 30% less. These can be assembled rapidly on-site using standard machinery and labor. When conceived in 2017, the company aimed to sell directly to consumers, including selling ADUs, but is now working to build entire communities.
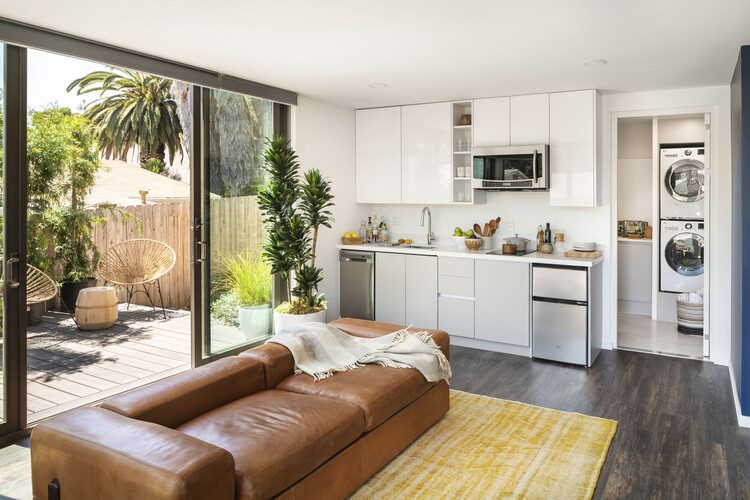
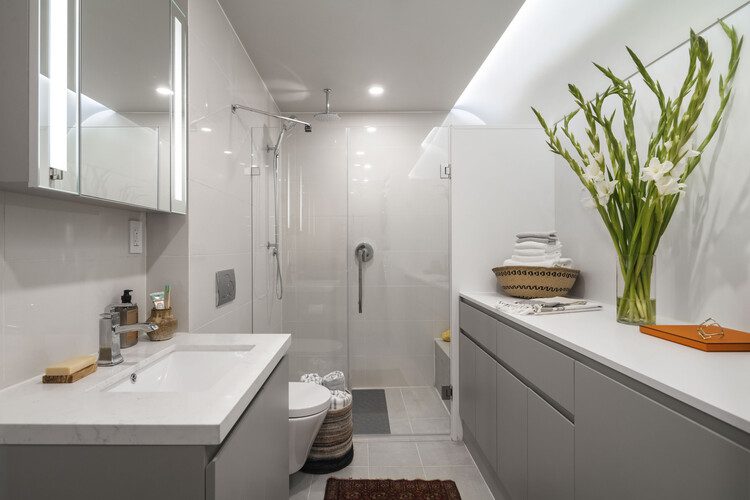
Azure makes entire 3D-printed modular prefabricated homes out of plastic bottles. They work directly with customers, providing 3D-printed backyard studios, offices, and tiny houses. According to Azure, each of their 3D-printed modules recycles around 150,000 plastic bottles. They are an average of 200 square feet in size and can be printed in just twenty-four hours. The structures are built watertight and are already insulated. The manufacturing process for a unit takes about one week, and the installation can be done in just one day. That includes all interior and exterior finishes, lighting, and power. They also provide customization options that allow people to adjust the layout of each module.
Investment in this sector is growing. Both Mighty Buildings and Azure have received large amounts of investment funding, hinting that these industries are expected to expand quickly soon. While this may not single-handedly solve issues with housing affordability, it may inject innovation into an industry that has long been characterized by stagnation. By serving as a pragmatic middle ground, 3D-printed prefabrication has the potential to introduce innovative materials and methods that have eluded the industry for decades and finally bring this technology to the public.
This article is part of the ArchDaily Topics: Modular Housing, proudly presented by BUILDNER, the original minimalist windows since 1992.
BUILDNER celebrates architecture competitions as an effective tool for achieving progress by fostering groundbreaking ideas that push the industry forward. “Through academic and project competitions, we are building an inclusive and diverse community of architects and designers, by promoting critical topics such as affordable, sustainable and small-scale housing to address global challenges. Our goal is to inspire the next generation of designers to propose innovative solutions and challenge the status quo.”
Every month we explore a topic in-depth through articles, interviews, news, and architecture projects. We invite you to learn more about our ArchDaily Topics. And, as always, at ArchDaily we welcome the contributions of our readers; if you want to submit an article or project, contact us.