Group of architects create region’s largest 3D-printed building in just 140 hours
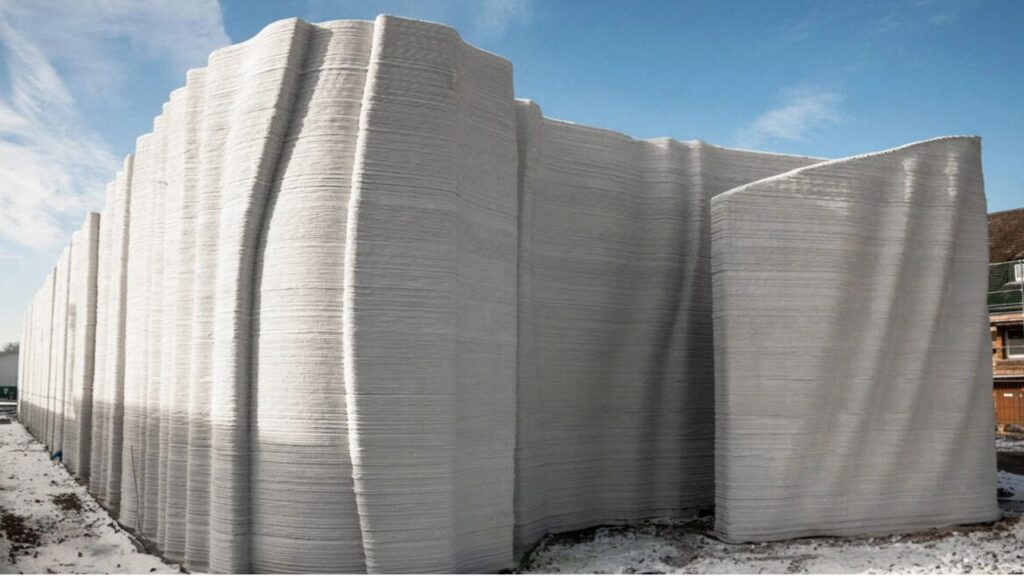
A large European structure, dubbed by its creators as the Wave House, took just 140 hours to build, thanks to 3D printing technology.
It’s the result of a collaboration of several firms and tech experts to build a unique, stylish cloud-computing data center in Heidelberg, Germany, the largest 3D-printed structure on the continent, according to a story by New Atlas.
In addition to a design that lives up to its ocean-themed name, the build is also another success story for the unique construction concept.
The printer, which looks like a scaffolding rig that moves across the top of the build site, lets loose a recyclable “cement-like mixture” in layers. The slurry comes out at 43 square feet per hour, forming the outside walls. The process releases “significantly less” air pollution than traditional methods, all per New Atlas.
The unique facility, at 600 square meters (about 6458 square feet), was designed by SSV and Mense Korte, printed by Peri 3D Construction for KrausGruppe, the developer.
“A challenge … in the Heidelberg project was solved by the architects … by giving the walls a wave design, a design feature that also gave name to the building: the Wave House. Such wave designed walls could not have been realized using conventional construction methods, so instead 3D construction printing technology was used due to the design freedom of this construction method,” said a press release about the project, quoted by New Atlas.
#cool_newsletter_f68c1387-cccd-4982-8bf7-77f2fc5e1d7e .cool_newsletter__inner span{color:#000000}
Join our newsletter
Good news, green hacks, and the latest cool clean tech — straight to your inbox every week!
A time-lapse video highlights the impressive size and maneuvering capability of the printer, showing it traveling back and forth over the structure, adding a layer of material with each pass.
[embedded content]
The result is a building that looks fit for a Hollywood movie set, with vertical ridges, cylindrical elements, and wave-like designs. A human crew finished the roof, doors, wiring, and some other parts of the build.
Standard materials used to construct buildings generate about 9% of global air pollution. What’s more, “raw resource use” is forecast to double by 2060. Steel, concrete, and cement are among the building elements noted in a United Nations report on the sector’s impact on planet overheating.
Other concepts being developed to clean up some of the pollution from the construction sector include a cement alternative made from fungus, called mycocrete. And in the United States, 3D-printed communities are growing, utilizing the efficiency of the tech.
The innovations are important in more ways than one. By reducing planet-warming air pollution, we can improve sustainability for our food system, as climate-worsened storms, droughts, and other weather patterns are impacting the agriculture sector, including food prices.
Unique 3D-printed buildings like the Wave House could become a more standard part of efforts to quickly and sustainably construct buildings. For typically utilitarian structures like data centers, the result can even be a bit artistic.
“The trend toward making data centers more in the vicinity of the users and therefore locate them in suburban areas and cities has created a need to make the data centers more visually appealing,” New Atlas reported, quoting the press release on the project.
Join our free newsletter for weekly updates on the coolest innovations improving our lives and saving our planet.
The Rise of 3D-Printed Prefabricated Homes
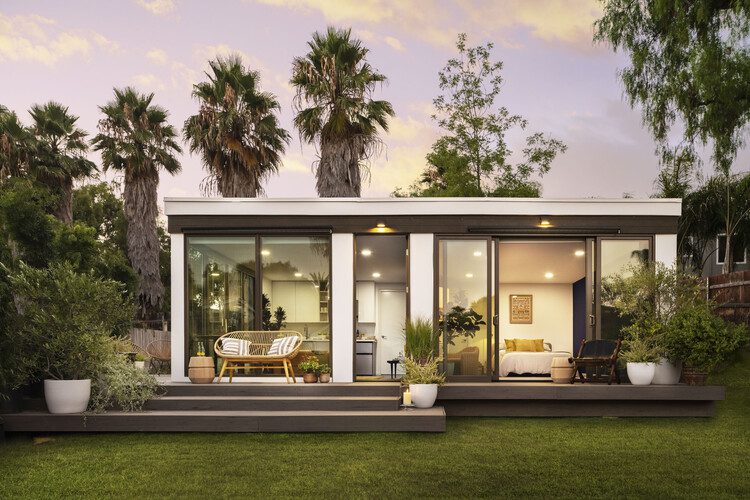
ADU / Mighty Buildings. Image © Paul VuShareShareFacebookTwitterMailPinterestWhatsappOrhttps://www.archdaily.com/1015506/the-rise-of-3d-printed-prefabricated-homesClipboard”COPY”CopyAs construction materials costs increase, builders and developers are seeking alternatives to traditional home construction methods to address housing shortages. In response, an expanding construction technology field is the 3D printing sector. This technology promises quicker, cheaper construction and the potential to extrude local and recycled materials. However, due to the slow-changing nature of the construction industry, a radical shift involving large-scale 3D-printing machines on-site and a complete overhaul of the construction process seems unlikely shortly. Prefabricated 3D printing modular housing offers a compelling solution, providing the benefits of 3D printing advancements while leveraging standard construction machinery and labor. In off-site 3D-printed construction, there is no need to transport massive 3D-printing machines on-site. Instead, components are printed in a controlled environment and then assembled on-site. These types of 3D-printed residential modular kits of parts are already being manufactured and are attracting significant investment.
3D printing company creates earthquake-resistant home built in 26 hours — here’s how it could revolutionize construction
COBOD, a 3D printing company based in Denmark, has created Guatemala’s first 3D-printed building — and even better, the prototype house is designed to be earthquake-resistant.The appeal of 3D-printing houses is simple: It can be done more quickly and with less human labor than any other construction method. As detailed by New Atlas, cement company Progreso partnered with COBOD to make the project happen. The Guatemala house, a one-floor, 527-square-foot dwelling, was completed in just 26 hours, divided over seven days.Cement company Progreso partnered with COBOD to make the project happen.COBOD’s BOD2 printer was able to follow a pre-planned blueprint to extrude layers of a cement-like mixture to form the house’s shell. From there, human builders installed windows, wiring, plumbing, and the house’s traditional Guatemalan roof made from palm thatching.The earthquake-resistant elements of the house’s design appear to be the curved walls and flexible, lightweight roof. COBOD explained that the curved walls in particular would have been very difficult to achieve without 3D printing (much less in just 26 hours).”Due to the use of 3D printing, the house features highly organic-shaped walls that would otherwise be extremely expensive, even unfeasible to complete with concrete blocks, the region’s predominant building material,” the company said in a press release published by New Atlas.Watch now: Alex Honnold test drives his new RivianThe ability to quickly and easily build houses that can withstand extreme weather could make a big difference in many people’s lives, as such events are becoming increasingly common due to changing weather patterns driven by the overheating of our planet.As of right now, COBOD is treating the Guatemala house as a simple prototype with no plans to create more, but that could change in the future.”The COBOD rep told us that the project was created as a research tool and there’s no immediate plans to create it on a larger scale,” New Atlas reported.COBOD is also responsible for a 3D-printed post office in India and Europe’s first 3D-printed two-story house, according to the outlet.Quickly erecting buildings isn’t the only way that people have been using 3D printing to help the planet, either. Other companies are using 3D printing to repurpose used coffee grounds into household items, create artificial limbs, create animal teeth to deter poachers, and even build structures for space exploration.Join our free newsletter for weekly updates on the coolest innovations improving our lives and saving our planet.
Are 3D Printed Data Centres a Viable Sustainable Solution?
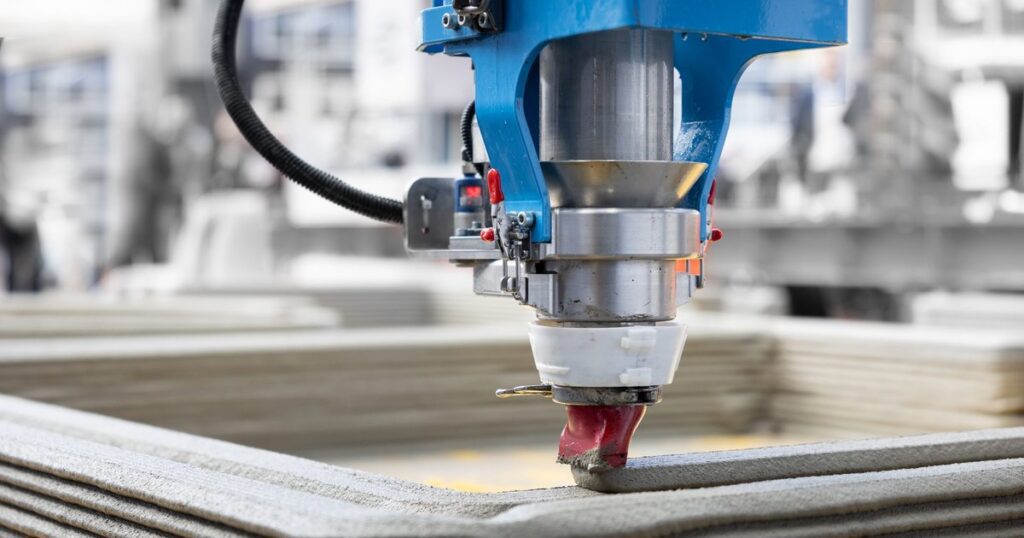
Speaking on the project’s completion, COBOD highlighted a growing trend towards making data centres more in the vicinity of the users and to therefore locate them in suburban areas and cities. As a result, data centre developers are starting to focus on the need to make data centres more visually appealing.Additionally, it was a cost-saver, with Hans-Jörg Kraus, Managing Partner of KRAUS GRUPPE Heidelberg, commenting on the amount saved via 3D construction printing.
“I cannot tell you what it would cost if we had made the data centre conventionally,” he said. “3D construction printing made this project economically viable”.
In addition to saving time and cost, constructing 3D printed data centres could also lead to more customised solutions being created to suit a wide range of functions and situations. This is ideal for a data centre facility, given that supply and demand is swelling rapidly around the world on account of technologies such as artificial intelligence (AI).
3D printed construction has also been hailed as energy efficient, as it means that developers are using fewer resources and creating less waste. Enhanced sustainability solutions can result in greater economic success for businesses, which could be particularly useful when considering the amount of power and energy data centres currently use.
This type of construction could result in data centres being able to experiment more with the appearance and contents of their site and creating more opportunities for innovation.
Associated challenges: Does this plan have a design flaw?
Despite such forward-thinking progress, 3D printed data centres could result in some challenges, including job cuts, design inaccuracies and even a lack of reinforcement if not considered correctly.
As 3D printed buildings enter further into public consciousness, and even city centres, debates could arise over the strength of these structures and how much they can contain.
Speaking in a LinkedIn post, General Manager Cloud at Cyberlink AG, Maximilian Wellenhofer, comments on how data centres would need to incorporate reinforcement techniques to address these potential issues.
“These challenges notwithstanding, the project in Heidelberg – and the broader push towards 3D-printed structures – opens up a dialogue about the future of construction in high-risk areas, including those prone to earthquakes,” he highlights. “The industry must address structural integrity and resilience against natural disasters, ensuring these innovative structures can withstand such events without compromising safety or functionality.”
He adds: “This approach not only highlights the potential for more efficient building methods but also prompts a significant question: can the architectural design of 3D-printed structures be optimised for natural cooling processes to reduce power consumption for cooling?”
******
Make sure you check out the latest edition of Data Centre Magazine and also sign up to our global conference series – Tech & AI LIVE 2024
******
Data Centre Magazine is a BizClik brand
Canada to allocate $600 million for new construction tech including 3D printing
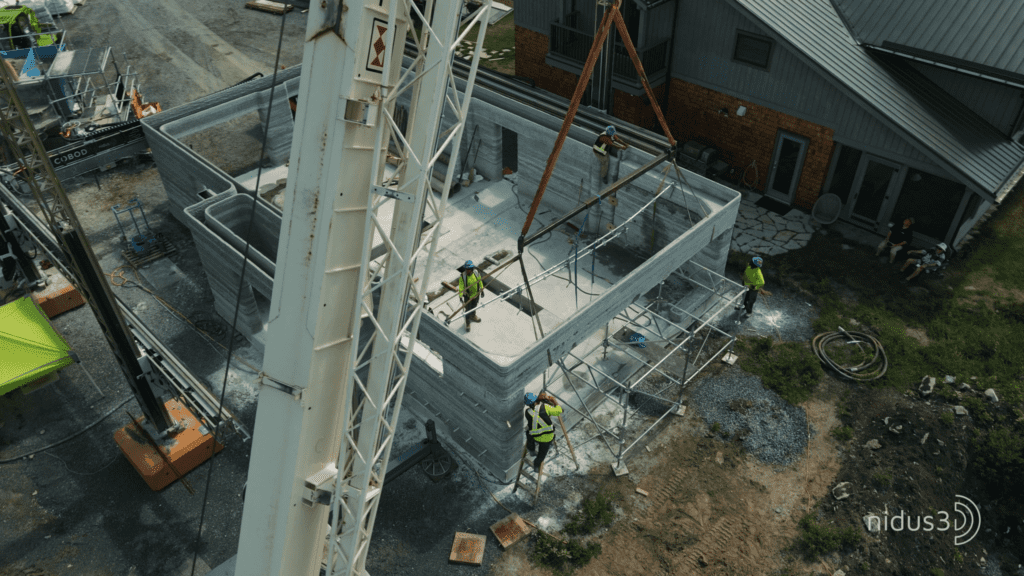
Stay up to date with everything that is happening in the wonderful world of AM via our LinkedIn community.
In countries and areas like the US, Canada, China, Russia, the Middle East or Africa, the enormous availability of land often clashes with insufficient housing. New technologies such as 3D printing can help build houses better, cheaper, more sustainably and faster. For this reason, Canadian Prime Minister Justin Trudeau has announced an over $600 million package that will research and develop new ideas and technology like prefabricated housing factories, mass timber production, penalization, 3D printing, and pre-approved home design catalogs.
“We’re changing the way we build homes in Canada,” the Rt. Hon. Justin Trudeau, Prime Minister of Canada, said in a statement. “In Budget 2024, we’re supporting a new construction approach, with a focus on innovation and technology. This will make it easier and more cost-effective to build more homes, faster. You should be able to live in the community you love, at a price you can afford.”
A 2-story building built by Canadian 3D construction printing company nidus 3D using a COBOD 3D printer.
In Canada, housing is one of the biggest pressures on people. Young Canadians are renting more than ever and being priced out of their communities. Families are finding it difficult to get a good place to settle down. Seniors are being forced to downsize. The cost to build homes is too high, and the time it takes to finish projects is too long. We’ve already taken bold action to build more homes, faster, improve access to housing, and make homes more affordable – and we know there is more to be done.
Trudeau, who is known to be very much aware of the latest technological and scientific development, said the Country needs to build more homes and needs to do so like never before, at prices Canadians can afford. That means investing in ideas and technology like prefabricated housing factories, mass timber production, penalization, 3D printing, and pre-approved home design catalogs.
The upcoming Budget 2024 introduces several measures aimed at addressing housing challenges. Among other things, it entails the establishment of a new $50 million Homebuilding Technology and Innovation Fund, to leverage an additional $150 million from private sector entities and other levels of government. This fund will facilitate the expansion, commercialization, and adoption of innovative housing technologies and materials, particularly for modular and prefabricated homes. Next Generation Manufacturing Canada will lead this initiative.
Built by Twente Additive Manufacturing (TAM), the Fibonacci house was the first 3D printed house in Canada. It was built in 2020 and is listed on Airbnb.
The budget also allocates another $50 million to streamline and modernize home-building processes through regional development agencies. This funding builds upon the progress of numerous ongoing innovative projects nationwide, including endeavors focused on modular housing, mass timber construction, robotics, 3D printing, and automation.
A significant $500 million is earmarked to bolster rental housing, offering low-cost financing via the Apartment Construction Loan Program. This support will aid new rental housing projects employing innovative construction methods, including those by prefabricated and modular housing manufacturers, alongside other homebuilders.
Additionally, a modernized Housing Design Catalogue is slated for launch to standardize up to 50 efficient, cost-effective, and livable home blueprints. With an $11.6 million allocation from Budget 2024, this catalog will encompass templates for modular homes, row housing, and fourplexes, intended to simplify and expedite housing approvals and construction timelines for housing manufacturers, provinces, territories, and municipalities.
These measures are designed to bolster made-in-Canada ideas and technologies while fostering growth in the home-building sector. They leverage innovation to facilitate the necessary scale and pace of construction to alleviate housing shortages. However, they are considered as initial steps toward more comprehensive solutions. The government plans to further engage with stakeholders from the housing, construction, and building materials sectors, as well as labor unions, experts, and other partners, to formulate a comprehensive Canadian industrial policy for homebuilding, aimed at ensuring fairness for future generations.
Trudeau pushes 3D-printed homes to solve Canada housing crisis
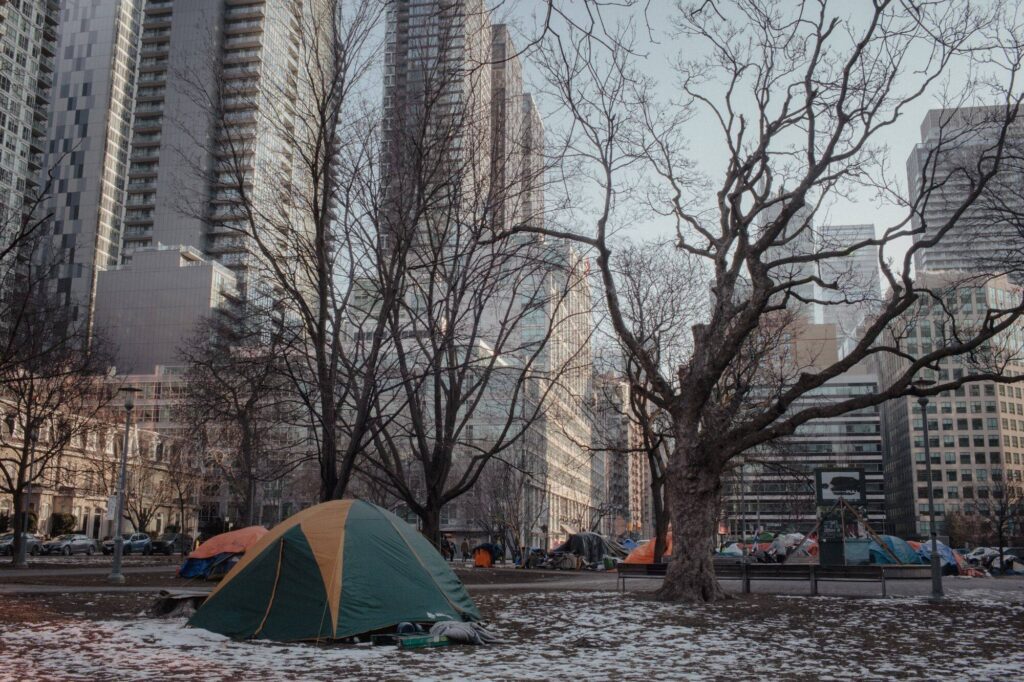
Canada’s Prime Minister Justin Trudeau announced measures aimed at making it easier and cheaper to build new homes, with an emphasis on prefabricated modular housing.The federal government will provide C$50 million (US$36.8 million) to a new fund meant to “support the scale-up, commercialisation and adoption of innovative housing technologies and materials,” Trudeau’s office said in a news release.A further C$50 million will go through regional development agencies to help modernise homebuilding “through modular housing, mass timber construction, robotics, 3D printing and automation”, the release said.Trudeau also announced C$11.6 million to support the creation of a catalogue of preapproved home designs to reduce the cost and time it takes to build housing – a strategy first used during World War II.The unhoused find shelter in makeshift tent encampments at Clarence Square park in Toronto, Ontario, Canada, in February. Photo: BloombergEarlier this week, Trudeau announced a top-up to a C$55 billion fund to provide low-cost financing for apartment building construction.On Friday he said C$500 million of that would be used for new rental housing “using innovative construction techniques from prefabricated and modular housing manufacturers”.The prime minister and his cabinet have made a series of announcements this week on housing measures that will be in the April 16 budget.Trudeau has been under fire over the past year due to Canada’s soaring cost of housing and is trailing badly in the polls to Conservative Party Leader Pierre Poilievre.Colleges face millions in losses amid Canada’s foreign student crackdownMelissa Lantsman, deputy leader of the Conservatives, described Trudeau’s pre-budget announcements as “frantic” and accused him of re-branding and recycling policies that do not get homes built.She said her party’s plan to provide a bonus to cities that increase homebuilding by 15 per cent annually – and fine those that do not – would be more effective.While Trudeau has pushed provinces and cities to allow up to four units on every lot, Lantsman said her party would allow communities to decide which types of housing work for them.“We just want to see more approvals and less gatekeepers in the way,” she said.
D.R. Horton Invests in 3D Printing Robot Manufacturer Apis Cor
.cms-textAlign-left{text-align:left;}.cms-textAlign-center{text-align:center;}.cms-textAlign-right{text-align:right;}
Apis Cor
Apis Cor’s 3D-printed concrete walls for a residential house in Melbourne, Florida.
D.R. Horton, the largest company on the 2023 BUILDER 100 list, has invested in Apis Cor, a manufacturer of construction 3D-printing robotic technologies. “Access to D.R. Horton’s extensive expertise and infrastructure can boost the adoption and scalability of our breakthrough technology in the market and help us make our technology available for every home building in the country sooner,” says Apis Cor CEO and co-founder Anna Cheniuntai. The two companies said they will work together on a multi-unit construction projection in South Florida after the finalization of the new 3D-printed wall system, which Apis Cor estimates will result in “a significant increase in productivity.”Apis Cor, one of the 25 finalists for the 2024 Ivory Prize for Housing Affordability, was founded in 2016 to address the labor shortages in the housing industry that impact home building’s ability to meet the growing demand for housing. While 3D printing provides the freedom to create different shapes and patterns, Cheniuntai says Apis Cor did not set out to “reinvent” the wall with its technology and printing process. “We decided to make our walls [as] similar as possible to what is already being built in the industry. We tested our material in a third-party lab, [and] we tested the wall samples in independent labs,” Cheniuntai says. “We provided this data to home builders saying we build the same houses that have been built for hundreds of years. We have figured how to get the houses permitted for our specific technology, and all the houses we have printed are fully permitted.”To date, the company has produced buildings that range from The Dubai Municipality in the United Arab Emirates—what is touted as the largest 3D-printed structure in the world—to a fully permitted, 2,200-square-foot single-family model home in Melbourne, Florida. The company’s 3D-printing technology aims to empower builders with advanced robotic solutions to help fill the gap in the limited pool of skilled labor, increase productivity, and build more houses. “As of now, we are focused on single-family housing in the United States. That is where we aim to have the biggest impact,” Cheniuntai tells BUILDER. “Our mission is to empower everyone with our technology so they can increase productivity [and] so home builders can build more homes. If you have more houses and supply and demand start meeting each other, that will eventually drive the costs down.”As part of the relationship with D.R. Horton, the home builder will provide advisory support to Apis Cor through its team of construction experts. “As a strategic investor, we are always interested in highly innovative companies. We’ve seen many technologies in the space and are very impressed with what Apis Cor has achieved and demonstrated so far with their mobile, proprietary printer ‘Frank,’” says Brad Conlon, senior vice president of business development for D.R. Horton. “We look forward to what we can achieve together to expedite the commercialization of this promising technology.”3D printing is a tool that can be utilized to help create more inventory and achieve greater affordability, according to Cheniuntai.“The 3D-printing solution just by itself is not the [sole] solution to the affordable housing problem. We believe it’s an important piece of the puzzle to help home builders build more houses,” Cheniuntai says. “The more predictable the [building] process is, the more cost-effective builders can build and the faster they can build. We believe addressing the most labor-intensive part of construction—the wall structure, the shell of a house—will help [builders] get all subcontractors committed to the schedule so the house is built within the schedule that was originally planned.” Keep the conversation going—sign up to our newsletter for exclusive content and updates. Sign up for free.
Portugal’s first 3D printed house
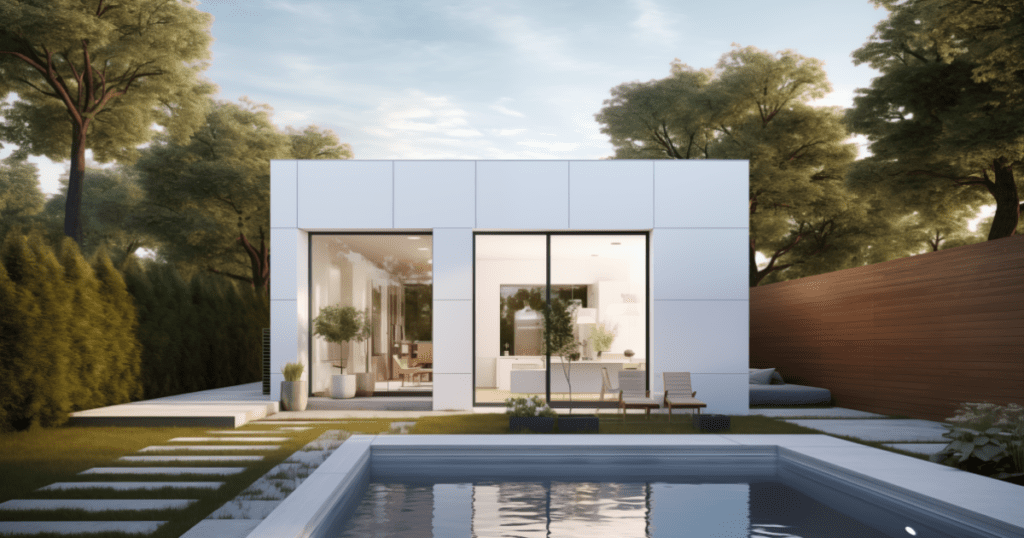
Could 3D printing be the future for housing? Today we’re taking a look at what will be the first Portuguese house “built” using a 3D printer in Portela da Villa, in Torres Vedras. It will be built by Litehaus.The company that links cutting-edge technology to the real estate sector aims to “bring a sustainable and innovative solution to the [construction] industry, which is responsible for 42% of carbon emissions”. The process of creating this residential unit was carried out using technologies such as Artificial Intelligence, in an initial phase of creativity and projection, and 3D printing already in its building.In a statement, Litehaus explains that it wants to focus on the production of modular buildings and 3D-printed houses, which consume 67 per cent less energy to manufacture. The aim, it says, is to build 100 houses a year in Portugal.”We’re here to make the sector wary. This technology allows us to produce up to 45m2 of walls in just 20 hours,” says Simi Launay, Litehaus’ Chief Creative Officer.”Litehaus is embarking on a mission to redefine living spaces, fusing AI technology, 3D printing and modular homes to create buildings that echo simplicity, innovation and sustainability. Our goal is to build 70% faster and 20% cheaper, building homes that epitomise elegance and minimalism harmonised with Portugal’s natural beauty,” he adds.
ICON announces new technologies, such as AI platform
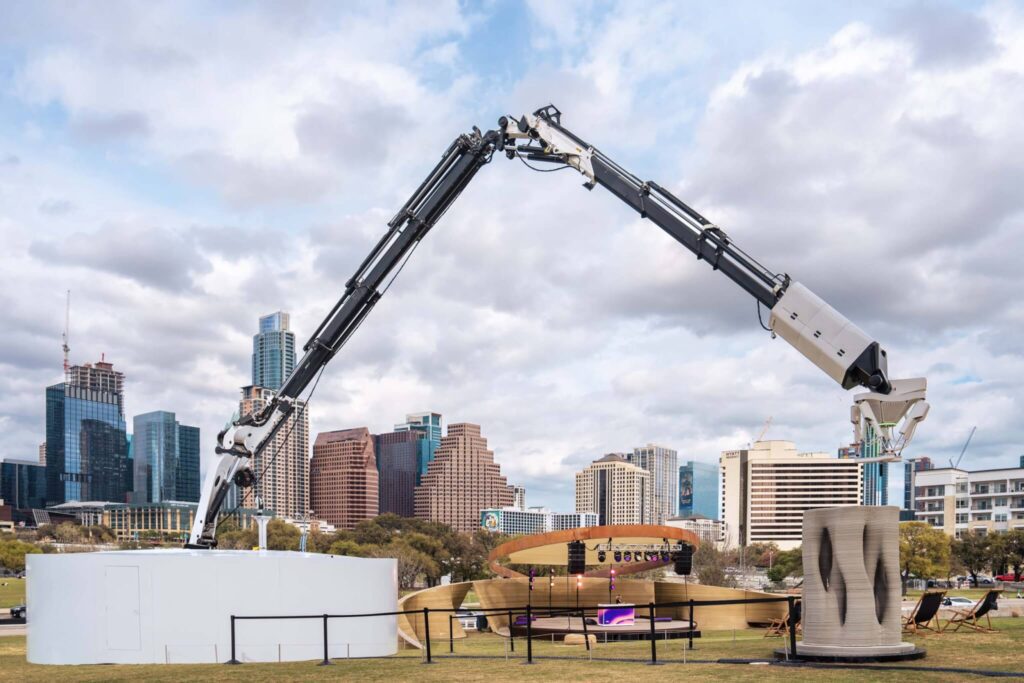
ICON, the 3D printing company behind tentative lunar habitats and the world’s largest 3D-printed community, announced an abundance of new initiatives and technological advances at SXSW in Austin, Texas. From a new robotic construction system capable of erecting multistory structures, a low-carbon concrete, and an artificial intelligence platform, it’s fair to say that for ICON the future of the built environment lies in untapped and yet-to-be realized technologies.
“When we launched the company and the first permitted 3D-printed house in 2018 during SXSW, we set out to both decrease the cost and increase the quality of building instead of choosing one or the other,” Jason Ballard, ICON cofounder and CEO, said at this week’s SXSW event. “We didn’t want to just be the best at 3D printing, we wanted to be the best at building, period.”
Phoenix at work on-site in Austin where a 3D-printed performance venue is underway (Roger Ho)
Since its 2018 debut ICON has made an indelible stamp on the built environment. It has always billed its portfolio of 3D-printed buildings as affordable and efficient. A new digital catalog registers the myriad residential project types ICON has the means to work on.
ICON Unveils New Technology
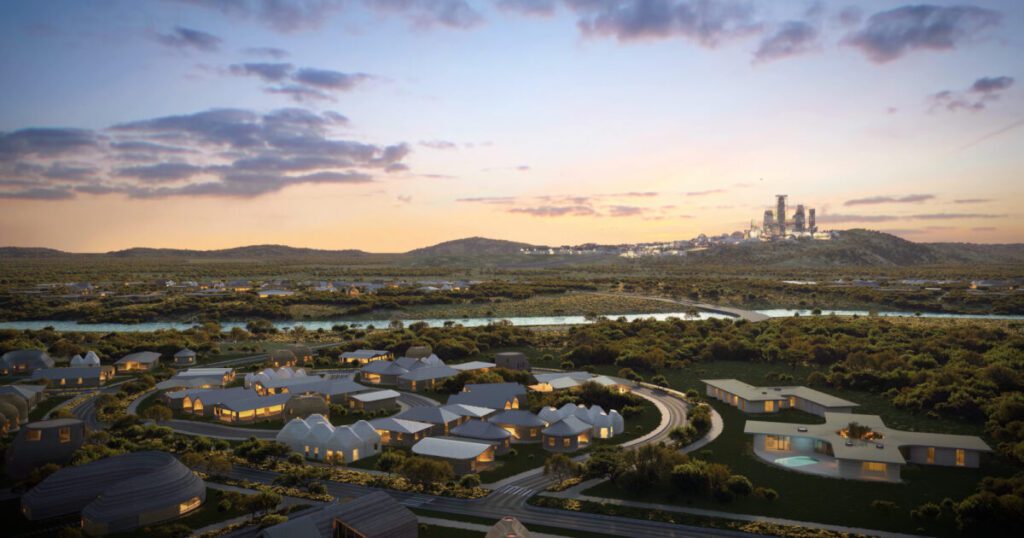
During SXSW, Leading Construction Technology Company ICON Announces A Multi-story 3D Printer, A New AI Tool for Architecture and Project Management, A Digital Catalog of Home Designs, and Advanced Low-carbon Concrete
AUSTIN, TX, March 12, 2024 – At a large event during SXSW® dubbed “Domus Ex Machina” ICON, the pioneer of advanced construction technologies and large-scale 3D printing, announced a new suite of products and technologies designed to further automate construction including a radical new robotic printer that enables multi-story construction, a new low-carbon building material, a digital catalog for residential architecture with more than 60 ready-to-build home designs, and an AI Architect™ for home design and construction. ICON believes that together these technologies make its construction technology platform a faster, more sustainable way to build high-quality housing affordably around the world.
“This is the moment we’ve really been working for these past six years,” said Jason Ballard, ICON Co-Founder and CEO. “When we launched the company and the first permitted 3D-printed house in 2018 during SXSW, we set out to both decrease the cost and increase the quality of building instead of choosing one or the other. We didn’t want to just be the best at 3D printing, we wanted to be the best at building, period. Now, I believe we can say that is a reality. I am so proud of the work ICON has done to get to where we are today– not only the promise, but the reality of technology, architecture and materials that will allow us to build better than anyone in the world.”
ICON’s new suite of robotics, software and materials include:
Phoenix™: ICON’s new multi-story robotic construction system introduces the capability of printing an entire building enclosure including foundations and roof structures. By increasing speed and size and decreasing setup time and the number of required operators, this advanced robotic system will reduce ICON printing costs by half. ICON is now taking orders for projects using Phoenix starting at $25/square foot for wall systems or $80/square foot including foundation and roof. This cost to build is lower than the most recent publicly available data for conventional construction of wall systems*. This wall system cost would represent a savings of up to $25,000 for the average American home versus conventional construction. The first engineering prototype of Phoenix has completed a 27-foot-tall architectural demonstration structure, now on display in Austin, TX.
CODEX™: ICON’s digital catalog of ready-to-print home architecture features more than 60 designs across five collections: Texas modern, fire resilient, storm resilient, affordable, and avant garde. The aim of CODEX is to make high-design and high-performance residential architecture available at all price points. CODEX allows builders, developers, and home buyers to build with ICON quickly and affordably using world-class architecture. ICON’s aim is for CODEX to be the most comprehensive digital catalog of buildable home designs in the world. It empowers ICON customers to select preferred designs as a starting point for their master planned communities and developments. ICON will continue to introduce new collections and will also partner with and compensate architects all over the world to feature their designs. Three of the CODEX collections available today were designed by BIG-Bjarke Ingels Group. Architects can submit their designs and developers can explore the collections and initiate projects with ICON today at https://codex.iconbuild.com.
CarbonX™: ICON’s CarbonX is a new low-carbon extrudable/printable concrete formula. When paired with ICON’s wall system and robotic construction methods, ICON’s CarbonX formula is the lowest carbon residential building system ready to be used at scale. A white paper co-authored with the MIT Concrete Sustainability Hub, “Reducing carbon emissions in the built environment: A case study in 3D-printed homes” (published March 12, 2024), features a case study of 3D-printed homes employing CarbonX. The life cycle assessment results of the white paper show that the embodied and operational impacts of 3D-printed homes are lower than stick-framed construction. ICON will be shipping CarbonX to the field in April 2024. ICON has also announced that it will make its material available to other projects and customers, not only its own 3D-printed projects. Future formulations of CarbonX are already in development to reduce carbon footprint even further and are expected to be announced in the coming year.
Vitruvius™: An AI system for designing and building homes. The ultimate goal of Vitruvius is to take human and project inputs and produce robust architecture, plans, permit-ready designs, budgets, and schedules. Launched today with an open beta, Vitruvius will help anyone design homes and generate floor plans, interior renders, and exterior renders in minutes based on their own desires, budgets, and feedback. By the end of this year, Vitruvius will progress all the way through schematic designs and in the following year ICON believes its AI architect will be able to produce full construction documents as well as permit-ready designs, budgets, and schedules. What truly makes Vitruvius unique is the combination of design and construction know-how. That knowledge is what allows Vitruvius to produce designs that can actually be built. Join the list to be the first to experience Vitruvius beta at vitruvius.ai.
Ballard continued, “In the future, I believe nearly all construction will be done by robots, and nearly all construction-related information will be processed and managed by AI systems. It is clear to me that this is the way to cut the cost and time of construction in half while making homes that are twice as good and more faithfully express the values and hopes of the people who live in them. We are going to need the same velocity of ambitious technological breakthroughs that we’ve experienced in these past few years, but we know where we are headed. Going forward, ICON is an AI and robotics company focused on transforming the way we build and accelerating what we believe is a very exciting future. Vitruvius will become the default method for ICON in designing custom homes. We intend to be selling and building Vitruvius-designed homes beginning this year.”
During the showcase event, Initiative 99™ winning designs were also revealed from phase I of the global architecture competition to reimagine affordable housing that could be built for $99,000 or less without sacrificing beauty, dignity, comfort, sustainability, or resiliency. More than 60 countries from all over the world were represented in the submissions with six winners and ten honorable mentions being awarded prize money from the $1M prize purse during the event and presented by Wells Fargo, lead supporter of the competition. The first, second, and third place designs in each category will each have their home designs featured as a collection in ICON’s CODEX.
Wells Fargo also announced on stage their foundation has committed $500,000 in grant funding to Mobile Loaves & Fishes, the Austin nonprofit that has been faithfully serving the area’s homeless community for more than 25 years, to help bring to life Initiative 99-designed homes and see multiple homes built at Community First! Village (CFV) to serve the underhoused community. Upon completion of Phase II of the global design competition, ICON and Mobile Loaves & Fishes will select one winning design for ICON to deliver multiple units within CFV’s expansion of their master planned development in Austin, TX.
“ICON’s innovative 3D-printed technology paired with these beautiful, imaginative Initiative 99 designs represent a model for the future of affordable housing. Wells Fargo is proud to help make these homes a reality,” said Darlene Goins, President of the Wells Fargo Foundation.
ICON and partner Liz Lambert also unveiled further plans to expand the new El Cosmico™ in Marfa, TX to include Initiative 99 winning designs where the existing bohemian campground is located. This adds to the newly designed and reimagined 60+ acre expansion of El Cosmico in far west Texas that will feature a hotel, hospitality amenities, and homes. The project breaks ground this year.
The latest announcements from ICON will provide the tools and technology to deliver more beautiful and resilient neighborhoods, communities and subdivisions enabled by the design freedom and new possibilities of 3D-printing.
“If you are a person who wants to own an ICON home, we want to hear from you so that we know what to design, where to build and what your hopes are for your own future,” Ballard said. “If you are a developer who needs support to deliver your project ahead of schedule and under budget and feel good about what you’ve created in the world, we want to build with you. If you are a builder who wants to take the most advanced construction tools in the world with you into the field, we want to work with you. If you are an architect, who wants to help us develop entirely new design languages and architectural vernaculars that align with your culture, values and imagination, we want to work together. We want to bring the entire industry together and equip everyone with the tools to properly build our future.”
ICON’s DOMUS EX MACHINA highlights can be viewed on ICON’s YouTube® channel. Visit www.iconbuild.com to get in touch and learn more.
*According to the National Association of Home Builders report released Feb 1, 2023.
About ICON
ICON is a construction technology company developing robotic and AI systems to lower the cost and increase the speed and quality of construction. For more information visit www.iconbuild.com or follow onX™, Instagram®, Facebook®, YouTube®, or Threads® (@ICON3DTech).
©2024 ICON Technology, Inc. All rights reserved.
Initiative 99 Winners Revealed
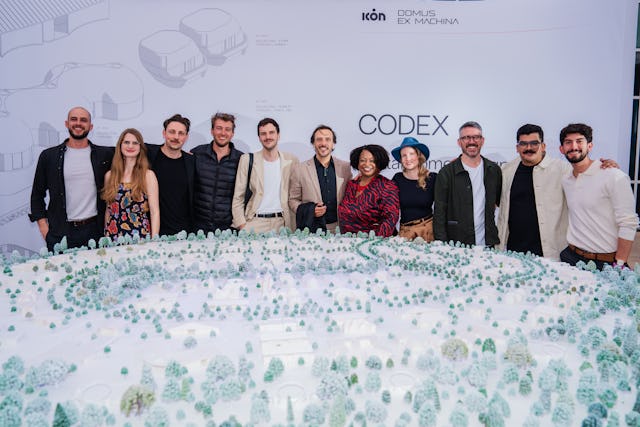
Global Architecture Competition to Reimagine Affordable Housing Will See Winning Designs Become Reality as Multiple Homes Will Be 3D Printed to Serve the Under-housed
Six winners of Initiative 99 phase one and Wells Fargo Foundation president Darlene Goins (Photo by Roger Ho)
During ICON’s official SXSW 2024 event yesterday, DOMUS EX MACHINA, ICON announced the phase I winners of Initiative 99, the global architecture competition to reimagine affordable housing that can be built for $99,000 or less. Joining ICON’s Melodie Yashar, VP of Building Design and Performance on stage to present the winners was Darlene Goins, president of the Wells Fargo Foundation who was the lead sponsor of the competition. As part of the announcement, Goins announced that the Wells Fargo Foundation is committing $500,000 in grant funding to Austin-based nonprofit Mobile Loaves & Fishes to help bring to life Initiative 99-designed homes and see multiple homes built at Community First! Village to serve the underhoused community.
Upon completion of Phase II of the competition, ICON and Mobile Loaves & Fishes will select one winning design for ICON to deliver multiple units within Community First! Village’s expansion of their growing development.
More than 60 countries from all over the world were represented in the submissions with six winners and ten honorable mentions being awarded prize money from the $1M prize purse during the event and presented by Wells Fargo, lead supporter of the competition.
The first, second, and third place designs in each category will each have their home designs featured in a collection in ICON’s CODEX, a new digital catalog of ready-to-print home architecture that allows builders, developers, and home buyers to build with ICON quickly and affordably using world-class architecture.
Full list of winners and those receiving honorable mentions from Phase 1 of Initiative 99:
Winners in the Student Category
1st prize: Casa Fami (Spain)2nd prize: Juan Felipe Molano (Colombia)3rd prize: Victoria Roznowski (Germany)
Winners in the Open Category
1st prize: MTspace Studio (New Zealand)2nd prize: For Everyday Life (United Kingdom)3rd prize: Beta Realities (Germany)
Honorable Mentions in the Student Category
Fusco-Ayala (USA)Canavati+Carneiro+Kazmaz (USA)Henry Aldridge (UK)LGK (USA)NEXT-LIVING (Spain)
Honorable Mentions in the Open Category
Willowprint (Germany)Sameep Padora and Associates (India)Guerin Glass Architects (USA)JK3D (USA)ConCave (various locations)
Look behind-the-scenes at a short documentary about the winners and their stories behind their inspiration for their winning designs.
[embedded content]
To learn more about the winning designs, visitwww.Initiative99.com.
North America’s First 3D printed 3-Story Building
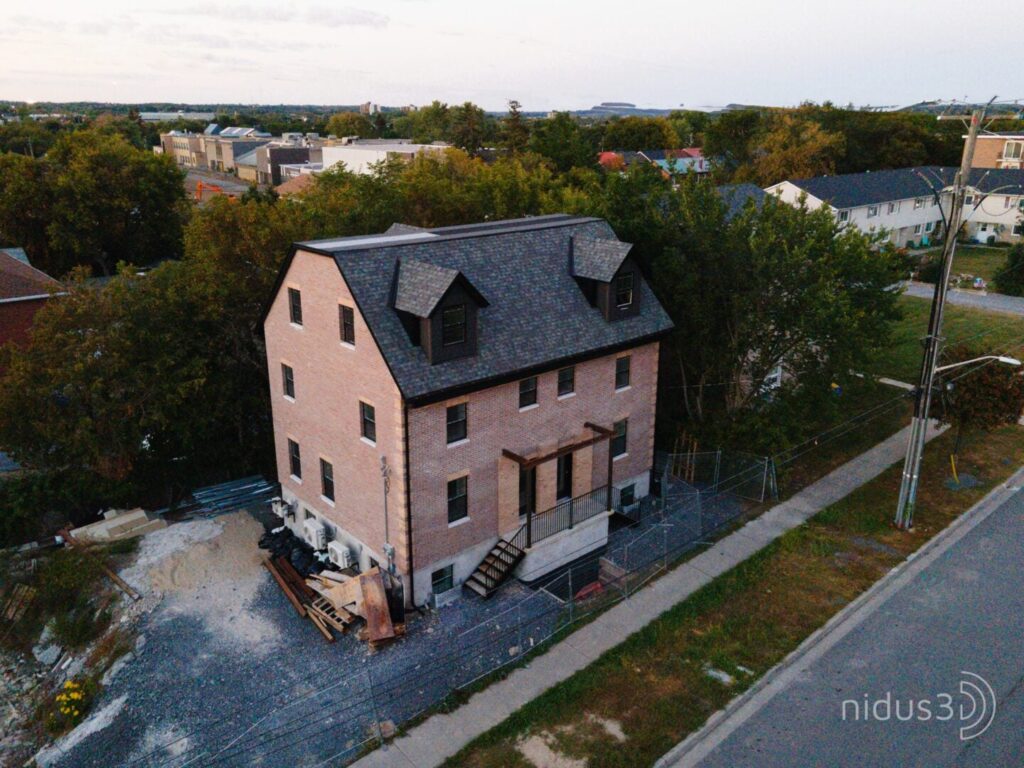
North America’s first 3D printed 3-story building has been completed near Toronto, Canada by nidus3D using a COBOD construction 3D printer. The townhouse has a usable floor area of 420 m2 (4,500 SF) and includes the world’s first 3D printed basement, a widespread feature in many Canadian and US homes in colder regions. Tenants will […]
Detroit’s First 3D-Printed House & Other Top Stories
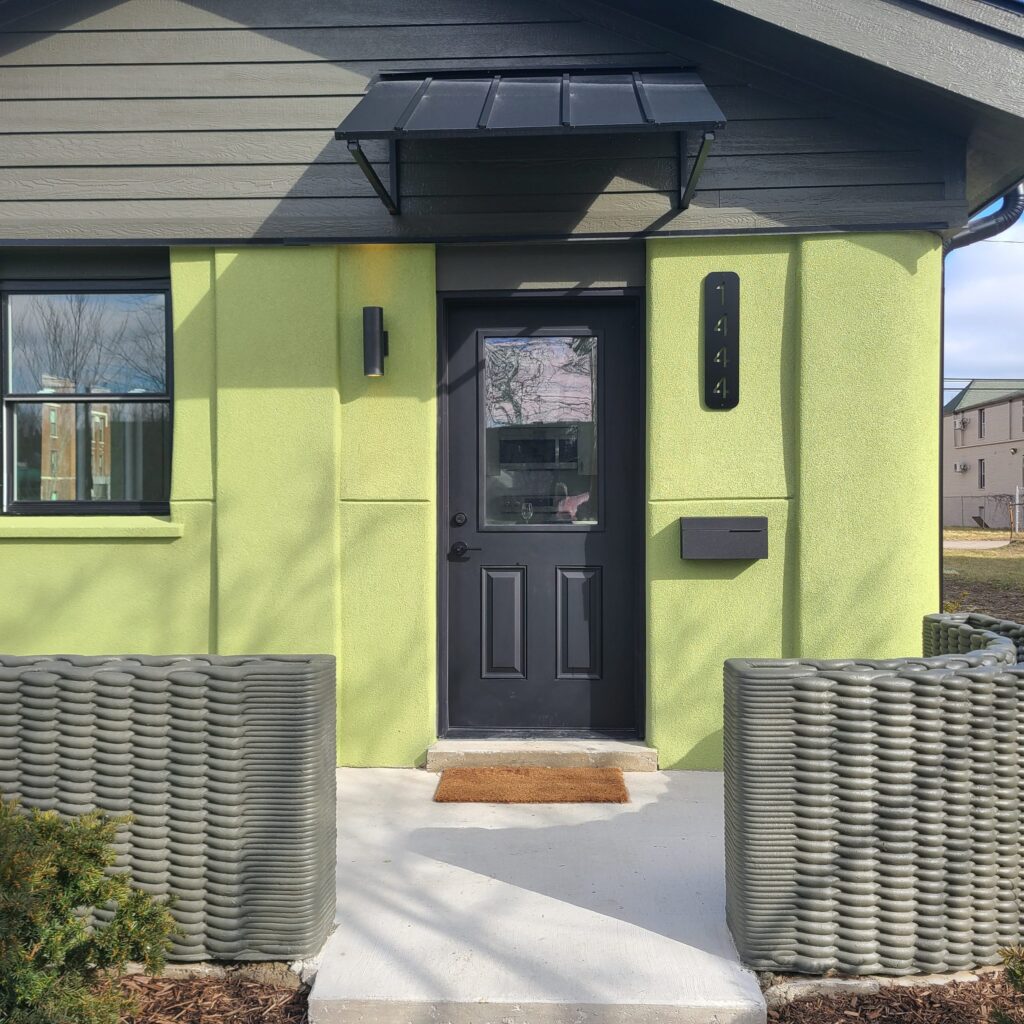
Detroit’s First 3D-Printed Home is on the MarketConstruction of Detroit’s first 3D-printed home, located in the Islandview neighborhood, is now complete and on the market with an asking price of $224,500. Citizen Robotics and developArchitecture first kicked off construction for the 988-square-foot, two-bedroom home in October of 2022. The home is the first of its kind in Detroit and will be more efficient in lowering utility costs for residents.New Cocktail Bar to Open in Detroit This SpringSaksey’s Cocktail Lounge, an intimate cocktail bar, is slated to open to the public in the lower level of Gilly’s Clubhouse & Rooftop this spring. The lounge offers many unique features, including tableside mixology service, live entertainment, a rich food menu, and more.Unique Museums to Visit in MichiganWhether you’re a history buff looking to dive into an interesting subject, a gamer with an eye for technology, a fashion fanatic, or just looking for your next adventure, these unique Michigan museums leave plenty to be discovered.Curtis Chin Discusses His Book Everything I Learned, I Learned in a Chinese Restaurant, A Memoir Curtis Chin, who was born in Detroit and raised there and in Troy, grew up at Chung’s, a beloved Cantonese restaurant stationed along the Cass Corridor in Detroit’s New Chinatown that was owned and operated by generations of Chin’s paternal family. His recently published first book, the memoir Everything I Learned, I Learned in a Chinese Restaurant, is about growing up Asian in 1980s Detroit and coming out to his working-class immigrant family.Buddy’s Pizza is Set to Open 23rd Location in CantonBuddy’s Pizza will be opening its newest carry-out location on Feb. 26 on Ford Road in Canton. With this addition, the originator of Detroit-style pizza will be operating 23 locations, including six other carry-out restaurants and 16 full-service restaurants.Indoor Waterparks in Michigan to Chase Away the Winter BluesMichigan is home to waterparks that are filled with fun for the entire family to enjoy, and thanks to a number of indoorwaterparks in metro Detroit and beyond, a waterpark can be a weekend vacation destination any time of year. Check out these five options for your next staycation. Meet Detroit’s Monument ManLocal sculptor Austen Brantley creates art that honors Black history for Detroit’s public parks — and beyond. has already made his mark in Detroit’s public parks, honoring icons of the past. His first public project was installed in 2019, the statue of slain civil rights activist Viola Liuzzo in a park named after her on Detroit’s west side. Check out our interview with Brantley to learn more about his work.Meet Chef and Author Abra BerensSouthwest Michigan chef and author Abra Berens talked to Hour Detroit about her career as a chef that earned the title of James Beard semifinalist , the cookbooks she wrote while also working as a chef in Chicago, and her rise to prominence.7 Metro Detroit Spots for Eggs BenedictWhether you’re looking for a tried-and-true take on eggs Benedict or want to branch out for a unique taste, consider ordering from one of these metro Detroit restaurants the next time you’re craving the savory breakfast dish.Lenten Fish Fries in Metro DetroitDuring Lent, many Catholics will refrain from eating meat, except for fish and seafood, on Fridays. Naturally, several fish fries are taking place throughout Lent in metro Detroit. Here are the details on some of those events.Want more reads delivered straight to your inbox? Sign up for the Hour Detroit’s newsletters today.
First 3D-printed home in the Midwest celebrated in Detroit ribbon cutting
DETROIT (WXYZ) — Today, the builders of the first 3D-printed home in the Midwest held a ribbon-cutting ceremony. The home is located at 1444 Sheridan Street in Detroit’s Islandview Neighborhood.It’s a 2 bedroom, 1 bathroom, 988 square feet, single-family home. 7 Action News first reported on the construction project back in October.Evelyn Woodman, the co-founder of Citizen Robotics, said the project is 15 months in the making.She and her father, Tom, started the project.She said one key highlight of the home is it has a universal design. The home is accessible for people with disabilities.“As the homeowner continues to age, or should they have any physical disabilities they would have no problem getting around in this home,” Woodman said.She said the concrete walls are built with a 3D printer, and the materials used help save on energy costs for the homeowner.Mildred Malone, who has lived across the street for 76 years said, “Oh, this place is larger than I thought.”7 Action News showed Malone photos of the interior.She said she’s lived in her home all her life. So, she’s seen a lot of change, including the condos she said were constructed about 15 years ago.Malone said of the 3-D home, “I think it’s good. I think it’s good. It’s something different we haven’t seen before.”“Maybe they’ll put some more up,” she said.Malone, who inherited several plots of land on both sides of the street from her parents, said she’s not opposed to parting with some of it for the sake of more single-family homes.“I might consider it maybe, but not the house and not the immediate land,” she said.Sam Stragand is the senior program manager for the Detroit Partnership on Economic Mobility through the University of Michigan Poverty Solutions.“I’m excited about it. It certainly is not a solution on its own,” he said.7 Action News discussed the home’s listing price of $224,500 with him. “The median housing value in Detroit is about $80,000. So, this is a house that’s worth more than twice as much as the average house in Detroit. At the same time, it is… I think that in order to develop more affordable housing we are going to need to encourage technological progress in home building,” Stragand said.Woodman said the price comparison is a conversation that comes up routinely.She explained, “We think it’s not comparable to compare this new build, it’s airtight, it’s energy-efficient, it’ll have low maintenance over time, and low heating and cooling costs over time. So, what we’re focused on is affordability over the life span of a home.”Woodman said since this is the first build of its kind that they’ve done, construction costs were expected to be higher and they’re hoping it’ll come down over time. Citizen Robotics said it desires to build more 3-D homes in the future.
Detroit’s First 3D-Printed Home is Now Available for Sale
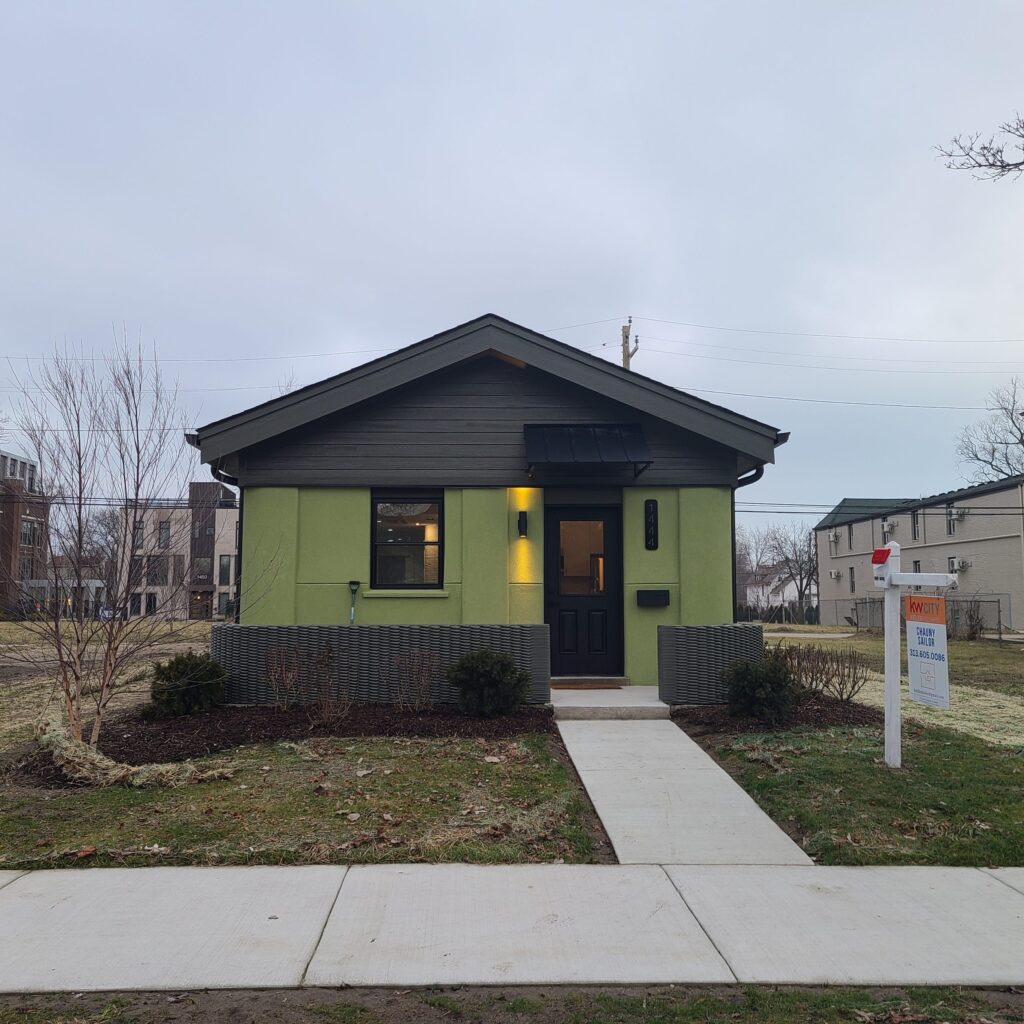
Construction of Detroit’s first 3D-printed home, located in the Islandview neighborhood, is now complete and on the market with an asking price of $224,500.Citizen Robotics and developArchitecture first kicked off construction for the 988-square-foot, two-bedroom home in October of 2022. The home, which is located at 1444 Sheridan St., is the first of its kind in Detroit and will be more efficient in lowering utility costs for residents.“This home proves that, by leveraging digitalization and robotics, we can solve for many of the problems that plague the homebuilding industry. We can build right-sized homes, with fewer workers, that cost less to heat and cool. We can build homes with features to support living at any stage of life,” said Tom Woodman, co-founder and executive director of Citizen Robotics, in a press release.Citizen Robotics is an organization that encourages the adoption of robotics and automation in home building in an effort to provide affordable and sustainable housing. developArchitecture is a metro Detroit architecture firm focused on small businesses, 3D-printed structures, and tenant improvements.The home was printed with a cementitious mortar using a giant robotic arm. The innovation behind 3D-printed homes makes for a more efficient building process that involves less labor, fewer expenses, and more sustainable materials.The home received nearly $160,000 in funding from the Michigan State Housing Development Authority (MSHDA)’s Neighborhood Enhancement Program, which covered the construction materials for the house.“As we move quickly with solutions to address Michigan’s housing crisis, we are serious about investing in innovation and piloting new ideas, and the 3D-printed house is a great example of that,” said Amy Hovey, MSHDA chief executive officer and executive director, in a press release. “We need all types of housing for Michiganders, and we are committed to exploring programs and partnerships that advance our goal to not only increase housing supply but also lower construction costs, reduce environmental impacts, and maintain affordability for homebuyers and renters.”Moving forward, Citizen Robotics and developArchitecture plan to host workshops throughout the state that will educate others about 3D printing designs and processes.For more information on the home, visit developarchitecture.com and citizenrobotics.org. For more community news and events, visit hourdetroit.com.
VeroTouch Debuts 3D Printed Home in BV, Announces Inclusion in Chaffee County Ascent Accelerator – by Carly Winchell
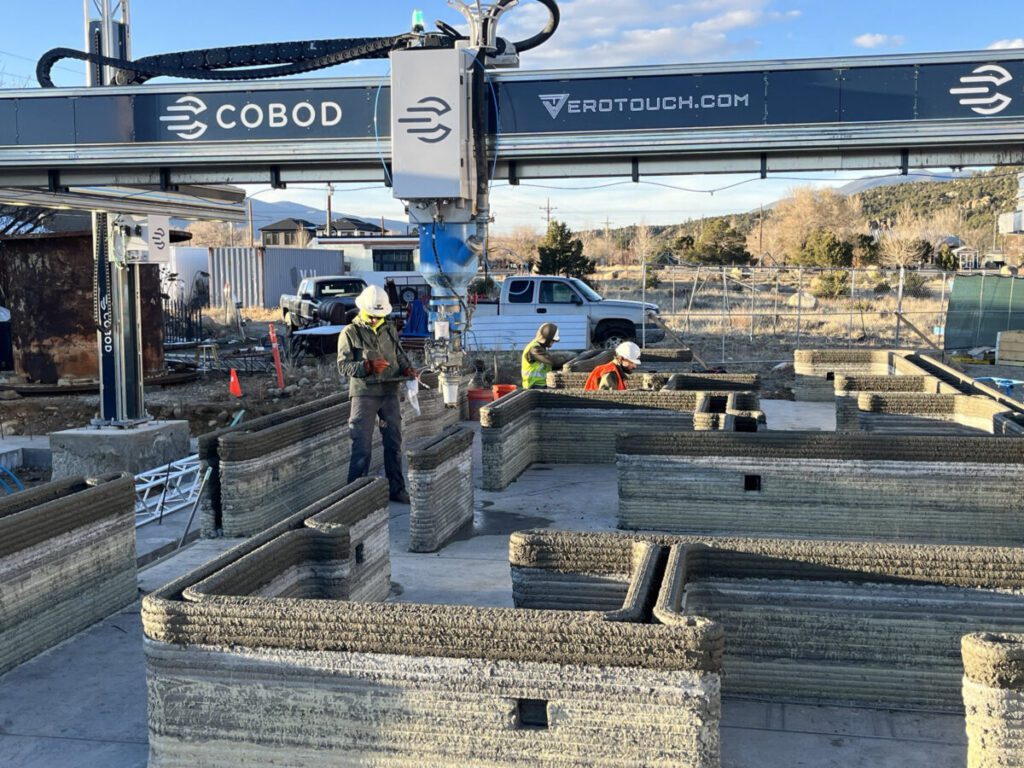
Work takes place on site of a VeroTouch 3D printed home in Buena Vista. VeroTouch courtesy photo.
Salida technology company VeroTouch has debuted Colorado’s first 3D-printed home in Buena Vista. VeroTouch was established in 2023. The company uses all Colorado materials and has systems for recycling any concrete waste as well as a water reclamation system to reuse water during construction. Its spokesmen say it seeks to enhance manufacturing and construction efficiency, precision, and cost-effectiveness through its offering of comprehensive design, engineering, automation, and construction services.
This innovative company has also earned a spot in the 2024 cohort of the Chaffee County Ascent Accelerator program.
“We are thrilled to unveil our cutting-edge solutions to the vibrant Colorado community, setting new standards for excellence and efficiency in the industry. Positioned at the forefront of technological advancements, VeroTouch is poised to redefine the manufacturing and construction industries,” explains a VeroTouch press release.
VeroTouch 3D printed home. Photo by Carly Winchell.
The introduction of Colorado’s very first 3D-printed home in Buena Vista is a major milestone for the company. This unveiling underscores the company’s pioneering advancements in construction and additive manufacturing technology and positions VeroTouch as a leader in innovative housing solutions. They are now working on printing a second home next door to the first.
These residences resulted from a strategic partnership with South Main Developer Jed Selby.
“Nestled in the charming enclave of South Main, an idyllic new urbanism neighborhood along the banks of the Arkansas River, these homes symbolize a noteworthy achievement in VeroTouch’s unwavering dedication to cutting-edge building solutions,” is how the company’s press release references it.
VeroTouch began working with South Main to construct their first homes because South Main is forward thinking and provided VeroTouch the opportunity to build their processes, teams, and company and figure out how to take this new technology and scale it.
VeroTouch was recently accepted into the Chaffee County Ascent Accelerator Program, a move that validates the company’s potential contributions to local economic development. The program provides valuable resources, mentorship, and networking opportunities, and compels those companies included in each cohort toward success.
Chaffee County EDC executive director Jake Rishavy recognized VeroTouch’s potential as he spoke about the company’s inclusion in the program.
“It’s rare and exciting in the economic development world to have the opportunity to support a company that is not only creating in-demand, high-paying jobs in a small mountain community but doing so while addressing one of our community’s most pressing needs—housing,” said Rishavy. “We’re eager to leverage what we believe is an unsurpassed network of business growth advisors in support of VeroTouch’s ongoing success in blending innovation and community impact.”
VeroTouch was co-founded by Chief Executive Officer (CEO) Grant Hamel and Chief Engineer Officer Elliott Harvey, P.E. It derives its name from the Latin word “vërus,” which means truth. The company touts a steadfast commitment to science-based manufacturing and construction principles.
The addition of “touch” to “vero” emphasizes the company’s “dedication to streamlining processes, empowering individuals to tackle tasks requiring creativity, intuition, and a personal touch.”
VeroTouch Chief Executive Officer (CEO) Grant Hamel and Chief Engineer Officer Elliott Harvey, P.E. VeroTouch courtesy photo
The company also speaks of a strong sense of community, with a commitment to addressing societal challenges through cooperative efforts. It focuses on what it calls “the Focal 5” of housing, education, labor and wage gaps, sustainability, and elder care.
The company actively seeks to mentor and empower the next generation of thinkers and builders. VeroTouch has partnerships with Salida and Buena Vista Schools and Colorado Mountain College and offers internship opportunities to high school and college students. VeroTouch also provides apprenticeships to help workers enter the field.
The VeroTouch team says they are “comprised of innovative doers and dreamers” and fosters a collaborative work environment by encouraging creativity and continuous learning.
Reinventing the Way Housing is Made
Ark Valley Voice managing editor Jan Wondra sat down to discuss VeroTouch with founders Hammel and Harvey over Zoom.
What should we know about VeroTouch?
“VeroTouch is a multi-facted company,” replied Hammel, citing their internships, apprenticeships, and in-house education alongside their professional design, engineering, and construction capabilities.
“We are trying to figure out new ways to look at the construction industry through being a tech company in that industry. It’s kind of the last hurrah of what we’re doing as humans and it hasn’t had tech injected into it quite as much as some of the other industries. We found that to be something that we needed to bring our expertise in and say hey, ‘What can we do here to reduce the cost of the biggest burden on everybody in their lives?” explained Hammel.
Hammel continued, saying housing is the largest expense in most people’s lives and VeroTouch’s goal is to figure out how to use technology to reduce costs of housing by increasing efficiency in the construction industry. “We have to find a way to be more efficient and that’s what we’re doing,” said Hammel.
How much does a 3D Printed home cost?
Hammel explained that VeroTouch strives to innovate and discover how to build a better product overall. “What we’re doing is building a better product for the same market price. . . What the industry is full of is a lot of over promise and under delivery and we’re not interested in that.”
In addition to high installation rating, A1 fire rating, Energy Star certification, and work toward LEED certification, Hammel cites more design freedom as a benefit of 3D-printed homes. Curves that can be produced by a 3D printer are expensive to replicate using traditional building methods. As long as designs meet the structural capabilities of the material and design, VeroTouch can do it.
3D-printed homes also have the benefit of more flexibility during the construction process with design necessarily occurring up front, details can be adjusted as they build the home from the bottom up. “We can make those adjustments quite a bit easier because it’s all programming,” said Hammel
Homes can also be finished using more traditional methods to make them look like any other house, or people can save on costs by foregoing these extra details and painting the 3D printed product. The concrete with aggregate material used by VeroTouch resembles smooth coat stucco when finished this way.
Renovation is also possible. Hammel explained walls can be printed offsite and installed and confirmed that this is structurally sound. There can also be a mixture of 3D-printed exterior with a traditionally framed interior. Customizability is key.
What parts of the home are 3D printed?
Detail of a VeroTouch 3D Printed Home in process. VeroTouch courtesy photo
The forms for foundations and walls are printed. Hammel reported creating twenty-two inches of stem wall in three-and-a-half hours of printing. He also explained this form of construction comes with “low physical burden labor” and opens the doors to greater diversity in the workforce.
VeroTouch believes their automation engineer Ashley Fant is the first female print operator in the country. “We can talk more about how this industry is injecting new exciting talent into the construction world, pulling from other places because people are just excited about this technology,” commented Hammel.
Though printing times are comparable to traditional building times, Hammel explained that it reduces complexity in the construction process.
“The difference is it reduces the subcontractor costs; if you do it in-house, all those other points along your project management, it makes it easier. Since you’re planning everything ahead of time, which you have to do, which is a little bit different than what construction typically does. . . As we’re going up we can start building those components [electrical, plumbing, conduit, etc.] as we go. So it’s kind of like a holistic manufacturing thing.”
Just like any other construction company, VeroTouch has standards they must meet during the building process. They have had their material tested and continue to refine it. They take in variables throughout the day and adjust the materials to meet the conditions.
“We obviously want to build homes that are better, and stronger, and that’ll last longer, so they are more sustainable for our communities over a long period of time and have a high energy rating,” explained Hammel. “We’re not just trying to meet those standards, we’re really trying to exceed them.”
How did you come to put this in Salida?
Hammel and Harvey have worked together for nearly a decade, so they came into this venture with a strong relationship and broad experiences.
“We realized we were really quite quick at getting things done and developing automated processes on the engineering and design side just to get things done faster,” said Hammel.
Hammel was initially looking to open his tech startup in Austin, Texas. But he visited some friends in the area and decided to move to Salida instead. “This is really an environment that supports entrepreneurship,” said Hammel. “Everybody says it’s rural, but it feels like a place that isn’t really rural.”
Hammel lived in Wichita and Kansas City for most of his life and Harvey hails from the suburbs of Kansas City as well, which is where they met. They decided to bring their tech startup to Chaffee County because the valley is so supportive of entrepreneurship and the environment opens up opportunities for getting to know and work with the community in ways that aren’t possible in larger cities like Denver.
What is the competitive environment for VeroTouch?
“There should always be multiple ways of solving a problem,” replied Hammel.
Looking at the field of construction, Hammel said that it hadn’t changed as much as other industries, and he believes that robots and automation is a way to fix the labor problem in the industry and generate interest in the trades again.
“It’s my belief that in X amount of years, robots will be building our homes and we wanted to be in the forefront of that area,” said Hammel.
He estimated there are probably about a dozen other companies actively doing what VeroTouch is doing now, but added the tech construction industry isn’t an easy path to take.
“We didn’t get into this because we thought that we were going to plug in a machine that was going to build 100 houses. We knew we were going to have to help develop the technology, push an industry that’s traditionally been highly labor-based into the technological age, and start reducing some of these burdens that we’re seeing across our communities.”
How are you planning to scale this operation?
VeroTouch got its equipment and began operating in the middle of 2023. While they haven’t been operating long, Hammel says their accomplishments have already been significant.
“We wanted to see that we can make it work,” said Hammel. “We’re starting to prove this out and it’s starting to really make sense and we’re starting to really understand it. We see what the needs are for the technology, how to build a company around this, and how to develop that full holistic plan for developments, and now we’re figuring out what that means and what additional pieces of technology we may need.”
How is this startup being funded?
VeroTouch has pursued grants and intends to continue to do so in the future. Currently, the company is funded entirely by Colorado-funded private equity.
Could you talk about the 5 Focal Points, one of which was education?
“My belief and the basis of our company is that we have to reinject knowledge back into industry,” replied Hammel. “Partnership with business and education is extremely important because they are providing the product for the businesses, and so businesses have to step up and say hey I’m here, how can I help.”
Hammel believes it is the responsibility of businesses to help educators and lift some of the burdens faced by teachers and schools. VeroTouch currently works with Colorado Mountain College (CMC) apprenticing a CMC graduate, and they are visiting other campuses around the area. They sponsor internships and apprenticeships to help deliver what they refer to as “high-paying, enjoyable jobs” without as much pressure to pursue the collegiate path, which has become the standard.
“What we need to do is bring business into the classroom and the students out of the classroom and into business,” declared Hammel.
Could you talk about the Ascent Accelerator Program?
Hammel and Harvey had just returned from their first three-hour session with the program before meeting with AVV. During the first session, they got the chance to meet the other cohort members.
Mock up of finished VeroTouch 3D printed homes. VeroTouch courtesy photo.
“Jake and Tim I think are some of the best people I’ve ever met in my life… I couldn’t say enough positive things about them,” said Hammel of Rishavy and Ascent Accelerator Tim Martinez.
Hammel met them before moving to Salida and cited them as among the reasons why VeroTouch decided to make their debut in Chaffee County. He also praised the Ascent Accelerator program in the area, calling it a “massive success.”
“A rural program having that type of stats on an accelerator is unbelievable. We’re very, very excited to be a part of it,” said Hammel.
The program lasts for twelve weeks and is mapped out to target priority areas for businesses including deep dives on financials, business structure, and goals. It also works to connect cohort members with the right people to get the answers needed to be better and succeed as a company.
What is your plan for this year?
Hammel and Harvey say the house in Buena Vista is more than a pilot. “We’re spending a lot of time to make it a beautiful, livable house. It’s definitely a product,” said Hammel.
“We didn’t just start printing,” explained Hammel, who broke down the process of experimentation to ensure a quality product, which sometimes includes printing something and tearing it down to do it better. VeroTouch is printing the second house next door and hopes to continue working with the public to find better ways to get into a more attainable market.
Hammel said they received some criticism about building in South Main and that not being attainable, but he explained that they understand and South Main is simply a starting point for the company. The high standards of the neighborhood have given them the freedom to experiment and find ways to create more attainable housing in the future.
The Wrap-up on VeroTouch
VeroTouch doesn’t just provide construction. “We’re a full-scale engineering and design company,” said Hammel.
They completed a site plan for a recreational complex in Poncha Springs pro bono, and are eager to provide site plans for elder care, which is another one of their focal five issues. Their diversity of experience in manufacturing allows them to use different experiences and apply them to the construction tech industry.
“We’re a community company. Making money is very important, but Eli and I are not into this to buy land, put a bunch of houses on it, flip it, and run out of town. We’re here to see how we can build this community both from the education side, the operational side, and build the industry up, so we’re really here to do what matters and that’s where our hearts are at,” concluded Hammel.
More information on VeroTouch is available at VeroTouch.com.
Interview MT/Sprout: CyBe prints houses with a 3D concrete printer: quicker, cheaper, and more sustainable
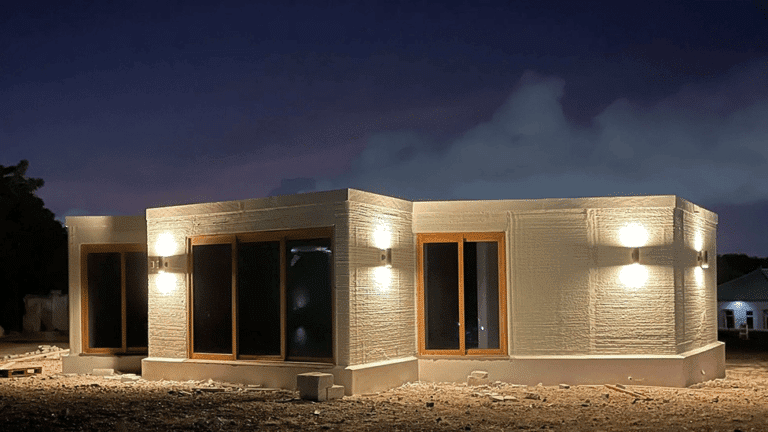
Building with a 3D concrete printer is four times faster, eighty percent more sustainable, and up to thirty five percent cheaper. Houses created in a factory setting, that is the matter CyBe Construction concerns itself about. A first funding round will yield the necessary funds.
Berry Hendriks, CEO and founder of CyBe Construction in Oss, has the blood of a contractor running through his veins. Ever since he was eight, he has been running around on construction sites. Berry Hendriks is the son of the CEO of Hendriks Construction, one of the top-five construction companies in the Netherlands
He is the eldest son of the fourth generation of Hendriks Construction. From a young age, he has been working at the family-owned company. Berry, however, has always been more interested in 3D technology than traditional technology. A 2012 YouTube video, where a professor showed a simulation of a machine printing concrete, sparked his ambitions.
Hendriks is excited, his father is not. Berry left the company in 2013 and started his own company: CyBe Construction. “To do great things that have an impact on the world: faster, cheaper, and more sustainable than conventional construction.”
Selling technology is more profitable
The first step was developing CyBe’s own machine, as well as concrete made for printing houses. “Known concrete suppliers, like Lafarge, Holcim, and Sika, told me I was crazy. Printing concrete was impossible. Many construction companies told me the same thing. The concrete wouldn’t set fast enough.”
Hendriks proved them wrong. CyBe’s concrete sets in three minutes, and reaches structural strength within the hour. “They then told me it is all fun and games in theory, but there is no way this technology will be faster, cheaper, and more sustainable than traditional construction.”
“I see building ourselves as a part of our marketing, it is all about credibility.”
At the innovation initiative Climate-Kic in Delft, Hendriks learns that it is “more profitable to sell the technology than it is to build yourself.” The core business activity of CyBe becomes selling 3D concrete printers. Today, they sell printers in 35 countries around the world. “Every day, this number grows.”
Gaining own experience
Nonetheless, Hendriks believes it is important for CyBe to build on their own. On numerous places around the world, Hendriks, working with his own team, has been the general contractor for construction projects. One of these places is Teuge-Apeldoorn, in the Netherlands, where the Vergaderfabriek has been built. CyBe is also building in the US and South-Africa.
He explains that architects design buildings based on bricks. These designs should be adjusted for printed buildings. Furthermore, there is the cost calculation, applying for the right permits, complying with the local rules and regulations…
All of this is fairly complex, so it is more than convenient to have some experience with this. Hendriks knows that having this experience makes it easier to support clients that want to buy a printer. “I see building ourselves as a part of our marketing, it is all about credibility.”
a home built with a 3D concrete printer
Net-zero construction
Later this year, CyBe is planning on building the first-ever, 3D printed, four-story apartment in Eindhoven. CyBe wants this project to be produced in-house, so that the construction can be limited to almost no nitrogen pollution. This will be the start of the home-factory in Oss, where CyBe plans to produce houses in a factory setting.
Concrete printers print layers of four centimeters. This makes the walls less massive (8-12 cm) than traditional concrete walls (30-40 cm), meaning less concrete is needed. Additionally, the binder for the concrete is a lot better for the environment, resulting in a decrease in CO2 emissions of up to eighty percent.
Sustainable construction: check. Concrete printing can bring back construction time from twenty five weeks to five weeks. This quicker construction, in turn, has an impact on the costs. If you choose to print the floors and walls on the construction site, you can save about ten percent of the costs. “Production in our factory to be installed on-site later saves you about thirty five percent of the costs in the Netherlands.”
Getting ready for investors
If you take into account all the benefits, CyBe Construction is a real gamechanger. So why aren’t contractors forming a line outside CyBe’s doors? “I have had this type of discussion with Hendriks Construction too. It is all about change management. You can buy a 3D concrete printer, but you also have to teach people how to use it. Business processes, as well as your supply chain, have to be adjusted.”
“These are the kind of complexities our company has to deal with. Nonetheless, our growth is good. Last year, we doubled our revenue. This year, our growth will be about 120 percent, up to 10 million euros. We are going to expand our team to sixty employees.”
Up until now, Hendriks has done everything by bootstrapping, thanks to a loan from his family’s company, but “those have been paid back.” At this point, he is the only shareholder. “If we want to make serious steps in the future, we have to be ready for investors.”
To the stock exchange
“We have been working on this for a couple of months now. This isn’t the best time to ask the bank for a loan. That’s why we want to have our first funding round next year. We want this to yield around 5 million euros.”
“The ambition is to reach a unicorn status, but in my own way.”
CyBe wants to use this money to increase and expand its sales. “Our new factory in Texas and the home-factory in Oss require a lot of capital. If you want to grow fast, you need strategic partners that generate sales for you.”
Hendriks is foreseeing a second and third funding round, as well as eventually going to the stock exchange. The ambition is to reach a unicorn status. “But if investors don’t want to do it my way, I won’t do it at all. We have a track record of ten years, we have clients, we are up and running. We just want to go quicker.”
CyBe Construction scores in the US
Business in the US is going so well by now, that CyBe has opened an LLC in Florida at the start of this year. The reason business is going so well in the US has to do with the fact that quick and cheap construction allows for low insurance rates.
“There are lots of wooden homes in Florida, Texas, and Mississippi. If a hurricane comes along, these homes are gone. Due to climate change, contractors want to switch to concrete construction, but they do not have the infrastructure or the employees to do so.”
“We reduce the need for employees, and we build more firmly. A concrete column, a printed structure, is steadier than one made of wood. If a hurricane comes along, the home will still be there afterwards. This allows the homeowner to pay lower insurance rates. This is a big reason for why business is booming in the US.”
a concrete printer doing its job in Florida
Number 1 worldwide
“People ask me if we are the Tesla, the Facebook, or the Uber of construction. I tell them: no, we are simply the CyBe of construction. Maybe we will reach a similar status as Tesla did in the car industry.”
Of course there is a lot of competition, he explains. “Icon has earned over 850 million dollars in the US over the last two years. I remember helping Icon’s founder with his graduation. Basically, all those competing companies are in our slipstream.”
“We are number one worldwide, because we do more than just selling machines or building construction projects. We have our own team of architects, construction managers, and ecological engineers from the University of Wageningen. We do both: we sell the entire concept of construction.”
Carbon-neutral homes
“We help our clients with their first building, which they can then show to local authorities to get the permits for a second or third project. We do everything for our clients’ success. If they have enough projects, they’ll eventually come knocking on our door for additional printers.”
“There is a tremendous shortage on the housing market, and not everyone can live on Mars.”
CyBe continues innovating, with the goal to build net-zero houses, completely environmentally neutral. “We are working on geopolymer concrete, which is like concrete 3.0. This will allow us to print CO2-neutral.”
CyBe Construction can solve the housing shortage problem
“We want to build the biggest community worldwide, and then work together with them. We connect our partner in Miami who is printing frame walls with our partner in France who is doing the same. This way, they can learn from each other. This is the power of our way of working.”
Hendriks notes that there is a huge potential worldwide. “We share this world with eight billion people. There is a tremendous shortage on the housing market, and not everyone can live on Mars, we need to fix this problem here.”
“In Indonesia, they’re experiencing a housing shortage of ten million houses. We are working together with a contractor from India, who’s building 200,000 homes a year. This is three times as much as the amount of homes built in the Netherlands, all construction companies combined.”
“In South-Africa, close to Johannesburg, we are working on a joint venture to start constructing homes ourselves. There, they have a backlog in housing construction of around two and a half million homes. From that perspective, the housing crisis in the Netherlands is relatively small.”
This text is a translation of MT/Sprout’s interview with Berry Hendriks that was published on 24-04-2023. All credits go to Karin Swiers. The original article can be read here.
Press Release – The Future of New Zealand Construction: From Abstract Vision to Concrete Achievements
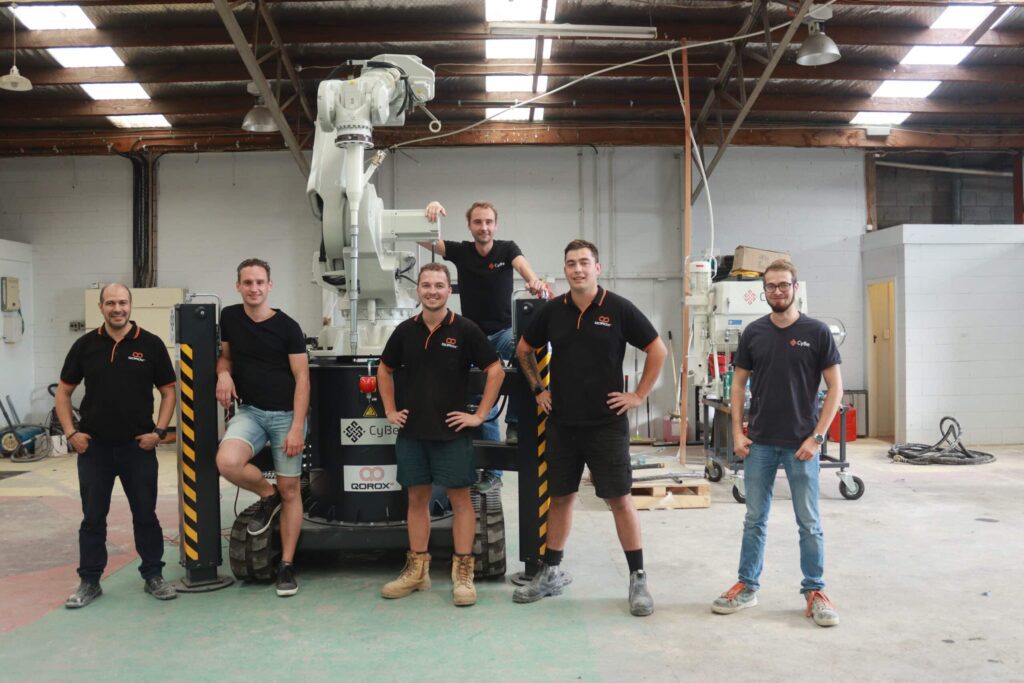
QOROX heeft goed gebruik gemaakt van hun positie als geautoriseerde reseller van CyBe printers. Ze hebben hun eerste 3D-printer al verkocht aan hun partners van Iconic Construction. De deal voorzag Iconic van een CyBe RC (Robot Crawler), waardoor het bedrijf nu ook kan profiteren van alle voordelen die aan 3D-printen verbonden zijn. Iconic Construction is opgericht in 2009 met het doel om de standaard in de industrie te verhogen door het leveren van vakmanschap met trots. Het bedrijf steunt op integriteit, groei, teamwork en creativiteit, en combineert deze waarden om tot de best mogelijke bouwoplossingen te komen. 3D-printtechnologie past perfect binnen dit principe om gebouwen van de hoogst mogelijke kwaliteit te realiseren. Na een verleden van diverse renovatie- en nieuwbouwprojecten, is Iconic nu klaar voor de volgende stap. Enthousiast als ze zijn, hebben ze al twee projecten klaarliggen om hun tanden in te zetten. Het eerste project is Lowe Road Studio, de eerste 3D-geprinte Airbnb van Nieuw-Zeeland, die aan de rand van Hamilton gebouwd zal worden. In dit autonome, op zonne-energie gedreven gebouw kunnen mensen ervaren hoe het is om in een 3D-geprinte ruimte te slapen. Ze zullen binnenkort ook beginnen aan The Vicarage, een multifunctionele commerciële voorziening die gebouwd wordt op de grond waar vroeger de priester woonde. Dankzij hun nieuw aangeschafte 3D-printer kan het bedrijf deze twee projecten veel sneller voltooien dan ze met traditionele bouwmethoden zouden kunnen, terwijl ze hun standaard van hoge kwaliteit en vakmanschap behouden.
Orascom and COBOD bring 3DCP to Egypt
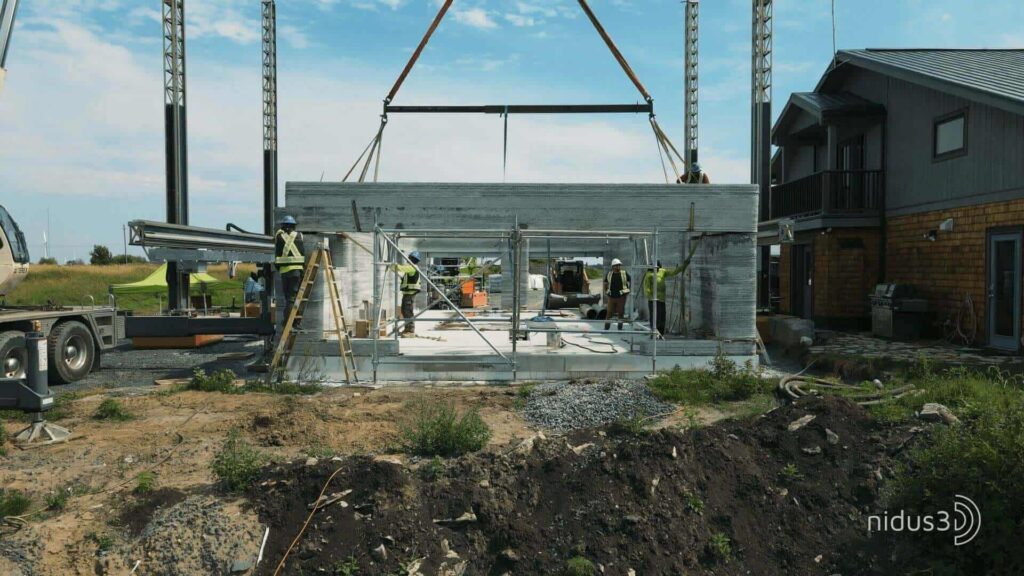
The partnership, owned 76% by Orascom Construction and 24% by COBOD, will play a leading role in the technological advancement of the construction sector in Egypt. Not only is this new technology more cost and time efficient compared to traditional methods of construction, but it is also more environmentally sustainable as it reduces material consumption, […]
Zoom On The Tallest 3D Printed Building COBOD International
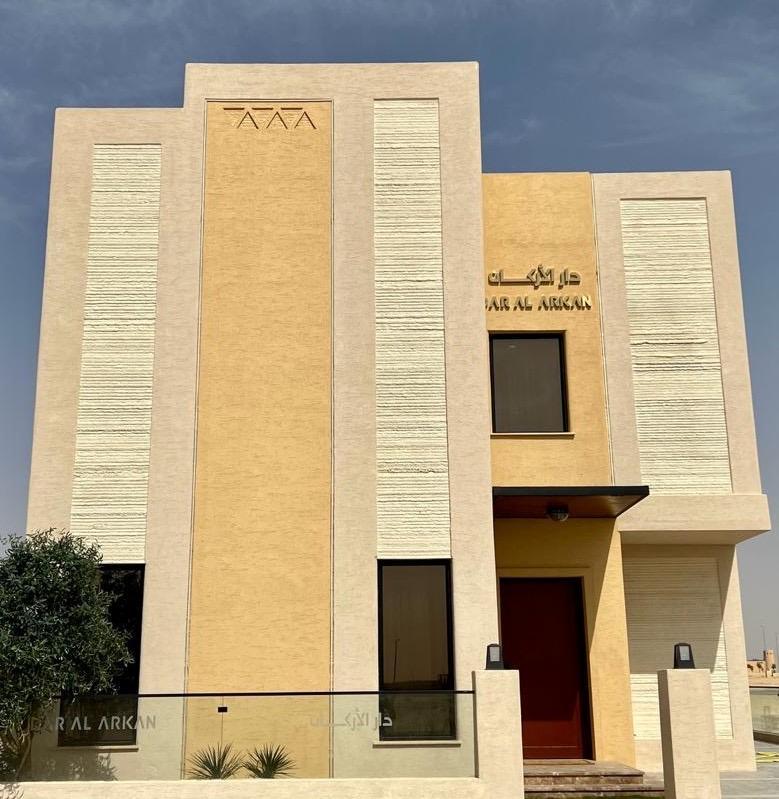
The world’s tallest 3D printed building is now complete and it is in many ways impressive. The 3-story, 9,9 m tall building compromises 345 m2/3713,55 ft2 and was made by the leading Saudi Arabian real estate developer, Dar Al Arkan, using a COBOD 3D construction printer. The villa features several smart home features and the […]