The Best Eco Homes On The Market Right Now
Solar-powered swimming pools? Air-source heat pumps? Wildflowers on the roof? You name it, these homes have got it. If you’re searching for a luxurious contemporary property with an eco-friendly twist, look no further: these are best eco homes on the market. The Best Eco Homes on the Market Right Now Hollow Way Lane, Amersham This […]
The 3D-Printed Affordable Housing of the Future Will Be Recyclable
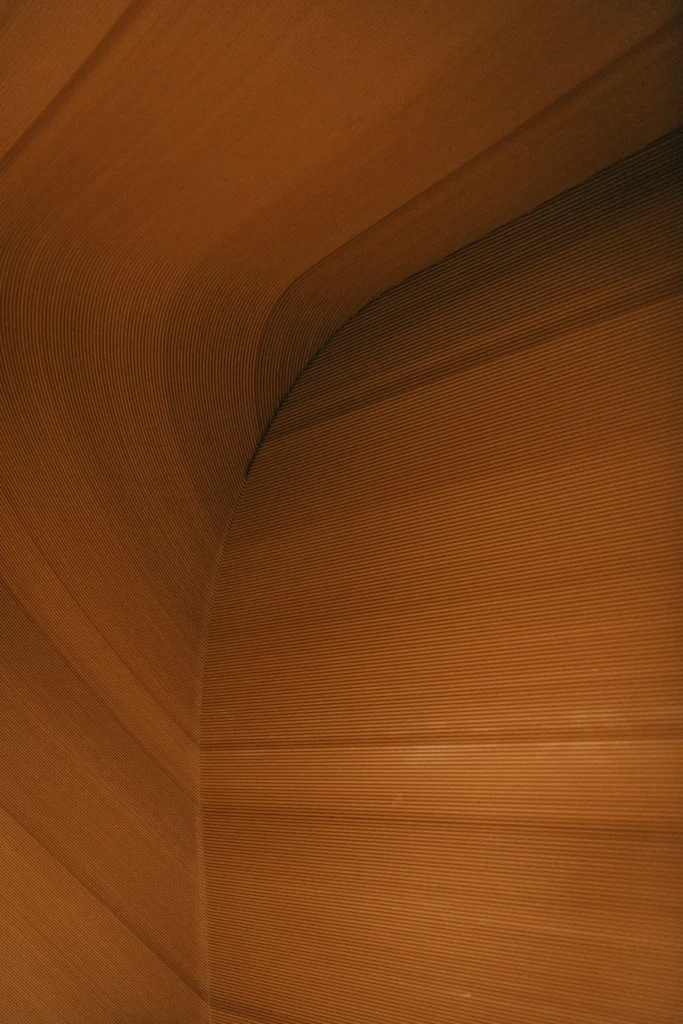
According to the University of Maine, the state’s sawmills produce nearly one million tons of wood residuals every year. Since each 600-square-foot unit requires approximately 10 tons of wood residuals, 100,000 housing units could theoretically be produced every year using just sawmill residuals.
Crushed by negative news?
Sign up for the Reasons to be Cheerful newsletter.
The University of Maine’s Advanced Structures and Composites Center received $3.3 million in funding for this project last year, and its collaboration with Penquis has set out to build a ready-to-live neighborhood with nine 3D-printed homes for people experiencing houselessness. As the team undergoes the final regulatory hurdles, Bird anticipates that houses could be ready to live in as early as this spring.
“The wood fiber material that’s used in the mix is essentially waste wood here in Maine,” says Jason Bird. Courtesy of the University of Maine ASCC
Once this pilot project is completed and the team at the University of Maine reaches full commercial capacity, Bird says the team will be able to print a home in as little as two days.
“That would include the shell of the house — the roof, walls, floors system,” Bird explains. “Long-term [infrastructure projects] could include cabinets, countertops, bath fixtures. And what gets me so excited about this project is that the technology isn’t just solving a local problem, it could be replicated around the world.”
Dr. Habib Dagher, executive director of the Advanced Structures and Composites Center, confirms that the technology is intended to be widely replicated.
“The goal of this research is to create a system for constructing homes that alleviates strains on the supply chain and addresses labor shortages, while providing economical and sustainable housing,” says Dr. Dagher. “This technology can be used anywhere in the world that has access to bio-based raw materials. We are focused on scaling up production technology to drive down costs and increase availability.”
And after enduring a year of extreme weather in Maine, with sensors reporting temperatures ranging from 1 degree to 105 degrees Fahrenheit, BioHome3D met all sustainability, strength, and durability requirements for US building codes, as well as the design requirements of the International Code Council code.
“Doing this project in a place like Maine, which has some of the most extreme temperatures in the continental US, is vital because it can prove that this material can endure huge temperature swings,” says Sarah Goehrke, founder of Additive Integrity, a consulting service that focuses on the examination and sustainable acceleration of industrial 3D printing. “The fact that BioHome3D survived for a year is very important proof going forward.”