INDIA’S AND THE WORLD’S FIRST 3D PRINTED POST OFFICE
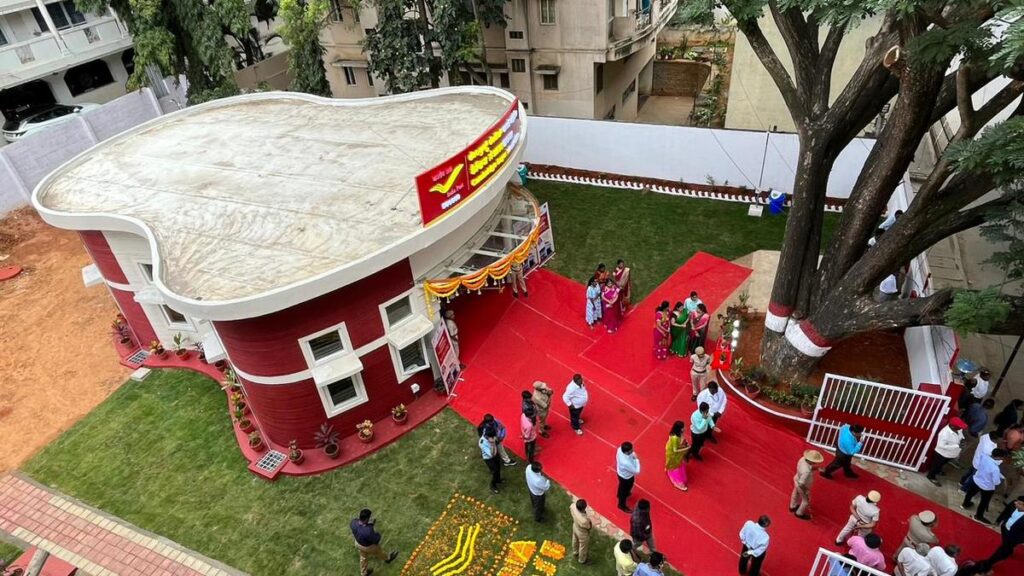
L&T used COBOD’s 3D printing technology to cut execution time by 80% and reduce cost by 40% India’s and the world’s first 3D printed post office opened for business last week. The 1,021 square feet (94,9 m2) building was begun in March 2023 and executed in just 43 days, two days ahead of schedule. Using […]
Guatemala’s First 3D Printed Building
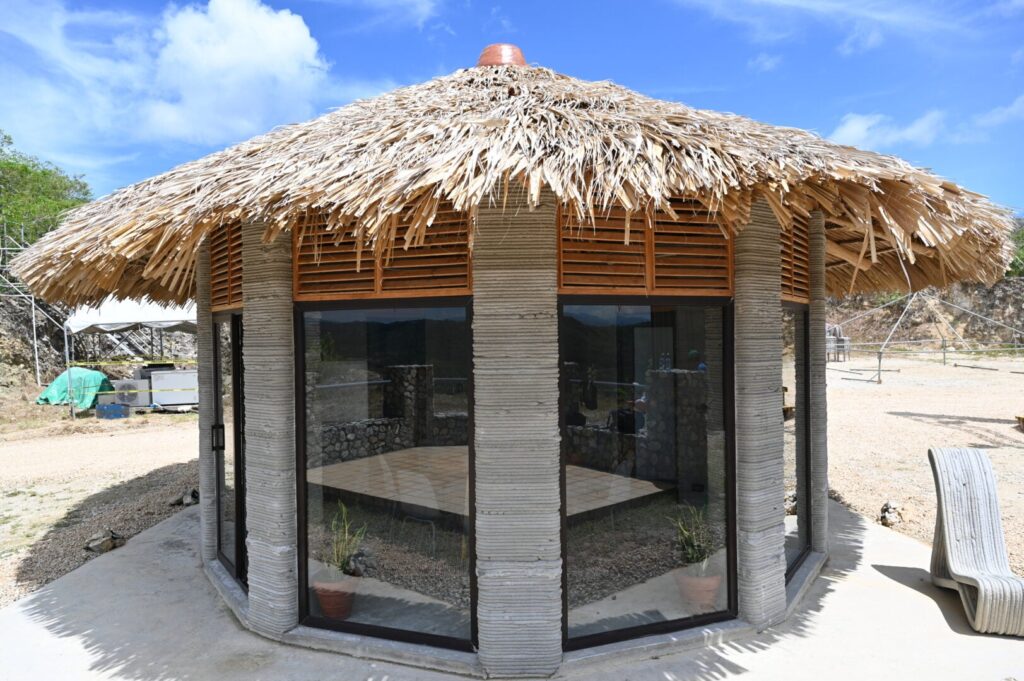
Progreso, a leader in Central and South America’s cement industry, recently inaugurated Guatemala’s first 3D printed house. The small organically shaped house of 49 m2 (527 SF) was made using a printer from COBOD International and combines this modern construction technique with the traditional palm leaves rancho-roof type ideal for seismic regions. The pioneering project […]
Europe’s First 3D Printed Publicly Funded House
First 3D social housing apartment building in Germany and Europe. The three floors building contains a total of 651 m2 (7.150 SF) and will have six apartment units between 61 m2 (670 SF) and 81m2 (890 SF). Third project from PERI 3D Construction in Germany this year using COBOD’s 3D construction printer, where the technology […]
Emaar Unveils Dubai’s First 3D Printed Villa
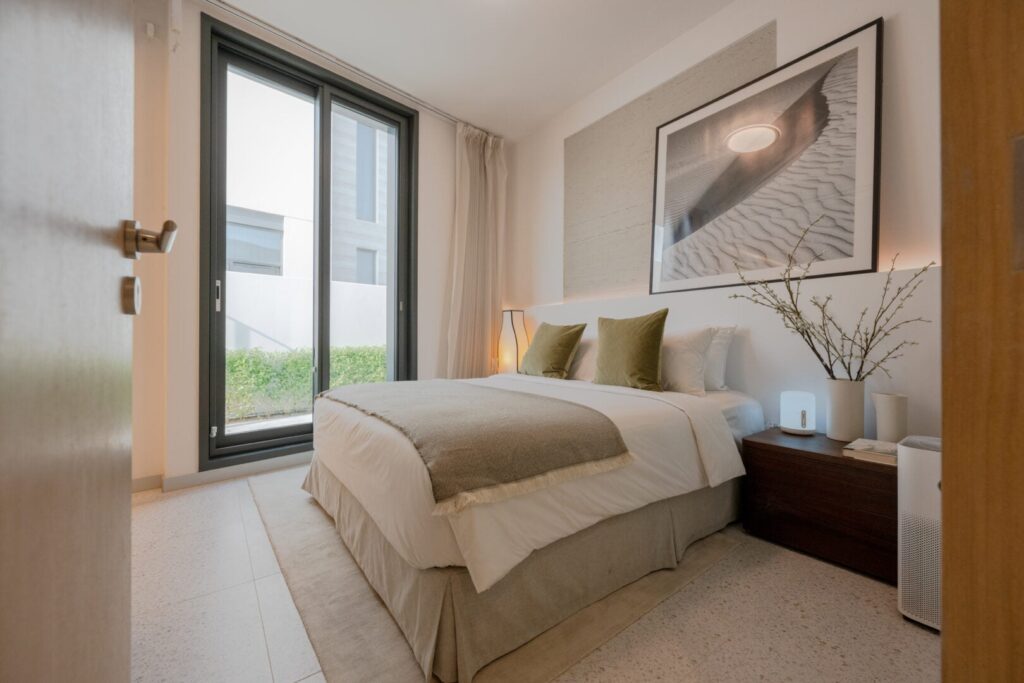
Last week, at a launch event involving Xiaomi’s Smart Living concept, Emaar finally revealed Dubai’s first 3D printed villa, which was previously delayed due to COVID-19. The 202 m2 (2,175 SF) villa with an integrated car park, 3 bedrooms and 4 bathrooms, represents one of the most stunning examples of what 3D printing can do for […]
First low CO2 3D printed building in Copenhagen
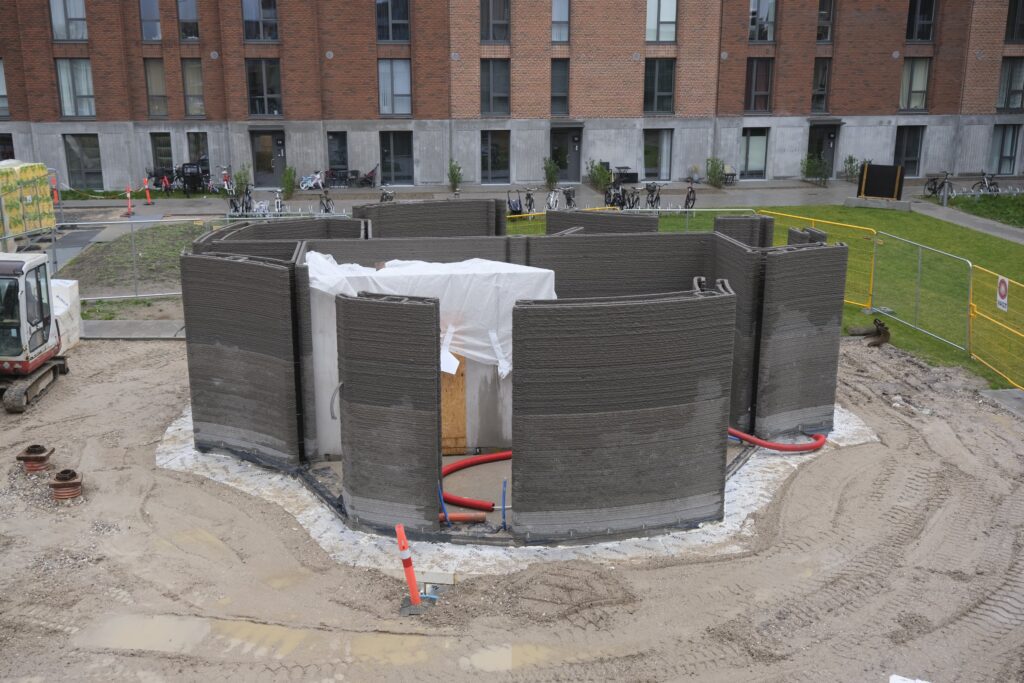
First low CO2 concrete building 3D printed in Copenhagen made by 3DCP Group – a 72 m2 (775 SF) community building. A couple of weeks ago AKF, the large Danish real estate developer, in partnership with Danish 3DCP Group, 3D printed a community building in greater Copenhagen area measuring 72 m2 (775 SF). The building will […]
First 3D Printed Net Zero Energy Home Made in Los Angeles
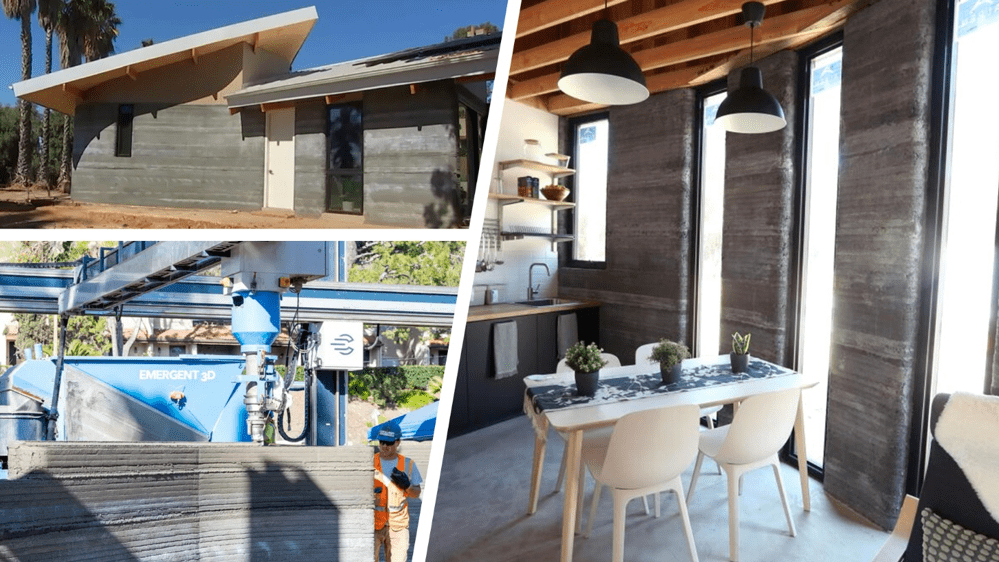
LA’s first 3D printed net zero house completed by Woodbury university students in collaboration with Emergent. Architecture Students from Woodbury University completed Los Angeles’ first fully permitted 3D printed net zero energy house. The house was part of a nationwide collegiate contest by the US Department of Energy. The walls of the 425 square-foot (40 m2) house, […]
Can 3D printing help solve North Texas’ affordable housing crisis?
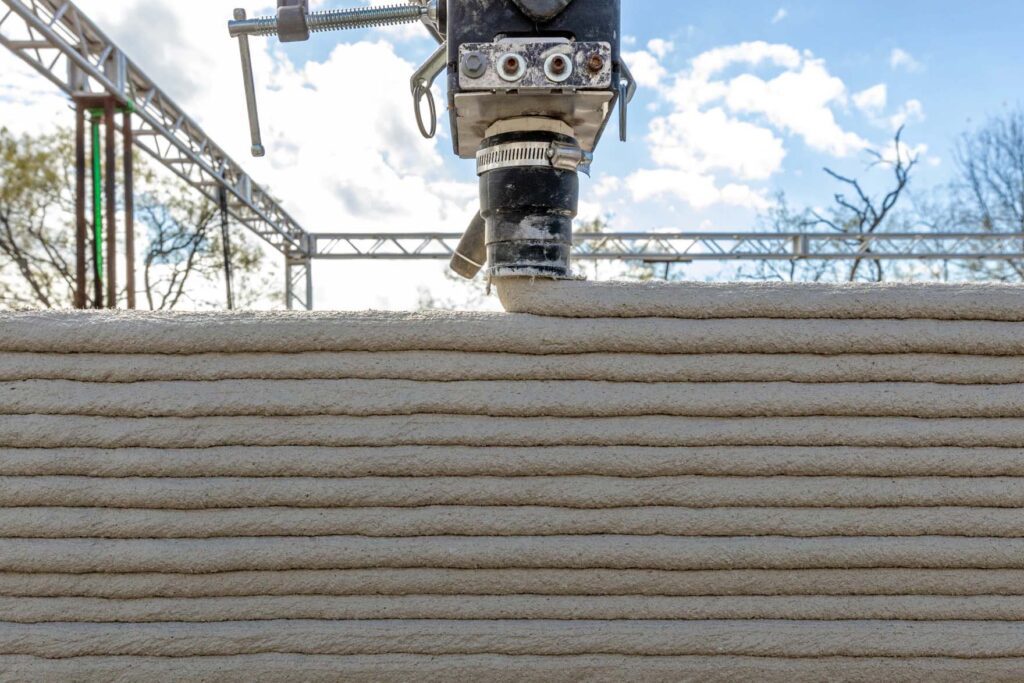
From KERA News:
On a sunny winter morning at a property off a rural dirty road in Kaufman, southeast of Dallas, a construction crew is working on building a barn — but this isn’t your traditional building site.
Instead of working with hammers and power drills, this small crew is letting a robot do most of the work.
“Probably the easiest way to describe it is a robot that has a soft serve ice cream cone machine at the end of it,” said Craig Pettit, CEO of Printed Technologies, a company that builds 3D printed homes, “and so we’re just pushing concrete out just like that, like ice cream cone machine would.”
As North Texas continues to see unprecedented growth, entrepreneurs like Pettit are hoping to solve the housing affordability crisis by turning to this innovative, automated technology.
Pettit and his business partner Lance Thrailkill say their crew is constantly improving the concrete mix used to print.
“That’s what we’ve really been tinkering with is different mixes and every mix is different,” Thrailkill said. “The print comes out different and dries quicker or slower depending on how much water is in there.”
The company has so far built at least six structures with a 3D printer, including houses, throughout North Texas.
A 3D printing nozzle layers the walls of a barn in Kaufman, Texas, on Dec. 20, 2023. “Probably the easiest way to describe it is a robot that has a soft serve ice cream cone machine at the end of it, and so we’re just pushing concrete out just like that,” Printed Technologies CEO Craig Pettit said.Johnathan Johnson / KERA
Thrailkill said the new technology could soon change the housing market. It’s one of the reasons he’s invested in the business.
“We really want to help solve the affordable housing crisis here in America and really, worldwide,” he said.
Right now, the cost of 3D printing a house is about the same as building with traditional methods. Pettit said many start-ups, like Printed Technologies, are racing to develop a more affordable way to build.
“One of the things that I’ve done over the past three years is just simplify everything within the technology to make it easy to set up, make it easy to take down,” Pettit said.
Tim Landau is another industry entrepreneur and the owner and CEO of Hive 3D Builders. His company built what could be one of the largest single family homes made by a 3D printer in Burton, east of Austin.
Like Thrailkill, Landau says what sparked his interest in 3D printing was trying to solve the affordability gap.
“That gap is, you know, specifically, it’s the difference between what the median income person can afford for a house and what the median price for a house is,” Landau said.
A completed 3D printed house in Burton, Texas, between Austin and Houston.Courtesy Hive 3D Builders
Another issue is the supply gap — how many houses are on the market. A recent report found Dallas alone needs as many as 60,000 more homes to meet demand.
“It’s kind of a solvable problem,” Laundau said. “You know, your big production builders, they can ramp up and build more houses to close that gap.”
But when newly built houses are upwards of half a million dollars or more, Landau said the only solution is to do something different.
“Everything points to more automation, whether it’s 3D printing or other forms of automation to help narrow those gaps,” Landau said.
3D printing also reduces the number of people needed to build a house. It usually only takes a two- to four-person crew.
It’s also a quicker process — Printed Technologies can print the frame of a 1,700-square-foot home in about two weeks.
That might sound like it’s replacing much-needed jobs, but according to Associated Builders and Contractors, there’s a shortage of more than half a million workers in construction.
Landau says 3D printing helps alleviate that labor shortage.
“So it’s supposed to not eliminate jobs,” he said. “It’s supposed to take the place of jobs that right now we don’t have anyone to do.”
3D printing nozzle layering the walls to a barn in Kaufman, TX on Dec 20, 2023.Johnathan Johnson / KERA News
Still, this new, burgeoning industry does face its challenges. Right now, the cost of printing a home is just as much as building one traditionally. There also isn’t a huge demand for 3D printed homes in the Dallas area, according to the Dallas Builders Association.
A spokesperson for the association said the technology does have the potential to solve the ongoing housing and labor shortages.
Landau says right now the industry could go one of two ways — one is that it becomes a niche industry for people who can afford customized 3D printed homes. The other is, if companies find ways to lower the extra cost, it could become the new normal.
That’s what Lance Thraillkill at Printed Technologies sees happening.
“In the next five to ten years, it’ll be adopted, across, you know, the entire United States and worldwide would be my expectation,” he said. “And how much that is embraced will be dependent on the cost.”
That means someday in the not too distant future, houses and even entire neighborhoods could be built — at least partially — by robots.
Lafarge’s Impact on nidus3D’s Endeavor: Canada’s Largest 3D-Printed Housing Project
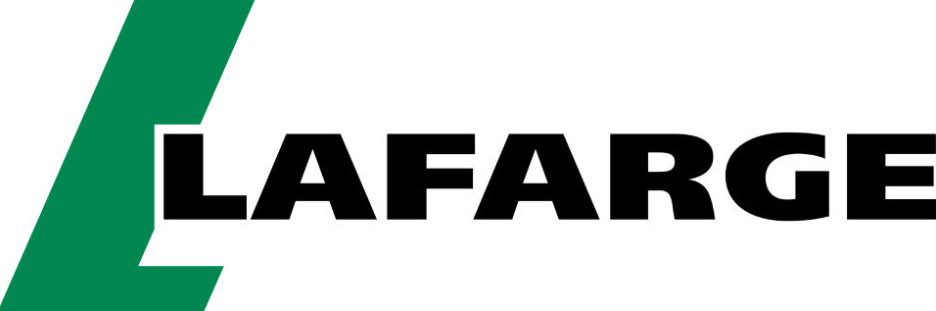
CALGARY, Alberta, January 11, 2024–(BUSINESS WIRE)–Lafarge Canada today announced its combined effort with nidus3D in supplying its OneCem low-carbon cement in Canada’s largest 3D-printed housing project, aimed at addressing the acute housing challenges faced by the SikSika Nation.While nidus3D has successfully completed 3D-printed housing projects in Ontario, this marks the first venture of its kind in Alberta. Located one hour’s drive east from the city of Calgary, the project named “Kakatoosoyiists” (Star Lodge) will consist of 4 buildings, comprising a total of sixteen units, each specifically designed to provide a supportive haven for individuals of SikSika Nation fleeing domestic violence or facing homelessness.This initiative directly confronts a pressing issue underscored by the Social Planning & Research Council of Hamilton. According to their report, Indigenous peoples in Canadian cities are eight times more likely to face homelessness compared to the general population.Lafarge is supplying its OneCem low-carbon cement for this project, recognized for its ability to deliver a reduced carbon footprint. When manufactured, the higher limestone content of OneCem translates into a reduction of greenhouse gas emissions—up to ten percent when compared to traditional Portland cement. OneCem achieves this sustainable advantage while maintaining its strength, durability, performance and workability.”Our shared goal with nidus3D extends beyond mere innovation,” says Brad Kohl, president and CEO of Lafarge Canada (West). “This project is about helping address the critical housing needs of the nation and foster a resilient, inclusive future through sustainable construction practices. We were proud to contribute to this project.”nidus3D, a leading innovator in 3D-printed housing, is excited to bring its expertise to Alberta.”Nidus3D is honoured and energized to be working with Siksika First Nation and Lafarge Canada on this innovative Canadian first,” says Ian Arthur, nidus3D’s president. “This multi-build development will not only provide much needed housing but show the immense potential of 3D construction printing to address Canada’s housing crisis. This project will demonstrate efficiencies and savings the technology can deliver through rapid, repeatable construction.”With the construction underway, this collaboration stands as a testament to the potential of combining expertise, resources, and a shared commitment to building not just structures but sustainable, supportive communities for a brighter future. The project is expected to be completed by March 31st, 2024.About nidus3DFounded in 2021, nidus3D is an innovative Canadian robotic construction company delivering rapid, low cost printed structures with automated, on-site3D concrete printing. As a process driven company, nidus3D is leading technology driven innovation in the construction sector to revolutionize the way homes are built. nidus3D has completed multiple proof-of-concept projects, including Canada’s first residentially-permitted 3D-printed structures and North America’s first two-story and three-story 3D-printed building and is currently scaling 3D construction printing across Canada. With its proven technology, nidus3D is ready to lead 3D construction printing into the future.About Lafarge Canada Inc.Lafarge Canada is a subsidiary of Holcim, a global leader in innovative and sustainable building solutions. Driven by its purpose to build progress for people and the planet, its 60,000 employees are on a mission to decarbonize building, while improving living standards for all. The company empowers its customers across all regions to build better with less, with its broad range of low-carbon and circular solutions, from ECOPact to ECOPlanet. With its innovative systems, from Elevate’s roofing to PRB’s insulation, Holcim makes buildings more sustainable in use, driving energy efficiency and green retrofitting. With sustainability at the core of its strategy, Holcim is becoming a net-zero company with 1.5°C targets validated by SBTi.www.lafarge.caView source version on businesswire.com: https://www.businesswire.com/news/home/20240111133773/en/ContactsKristen MarstonCommunications and Marketing Coordinator, Western CanadaLafarge Canada Inc.kristen.marston@lafarge.com Rafael Olvera GuelSales and Marketing ManagerNidus3Drafael.guel@nidus3D.com
3D-printing: How to build sustainable housing for three billion
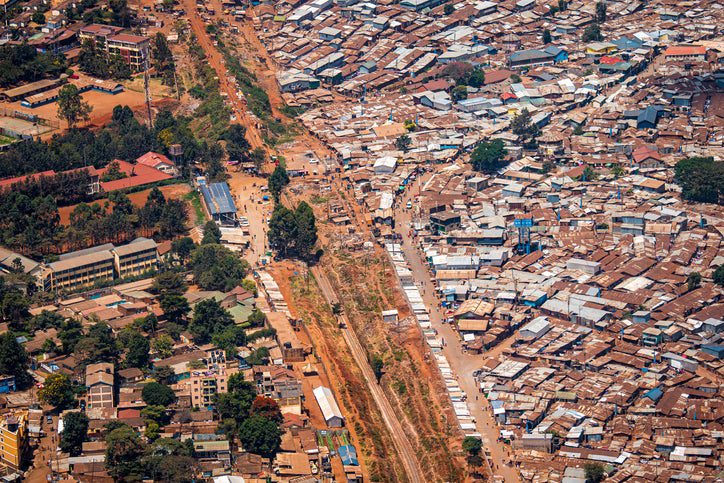
An aerial shot of the Kibera slum, Africa’s largest slum, in the heart of Nairobi. Credit: Stock image via Getty Images. There is a global sustainable housing crisis. Not only is the built environment –including construction and energy use – responsible for around 40% of annual greenhouse gas emissions, but there are billions of people […]
Can 3D printing help solve North Texas’ affordable housing crisis?
On a sunny winter morning at a property off a rural dirty road in Kaufman, southeast of Dallas, a construction crew is working on building a barn — but this isn’t your traditional building site. Instead of working with hammers and power drills, this small crew is letting a robot do most of the work.“Probably the easiest way to describe it is a robot that has a soft serve ice cream cone machine at the end of it,” said Craig Pettit, CEO of Printed Technologies, a company that builds 3D printed homes, “and so we’re just pushing concrete out just like that, like ice cream cone machine would.”As North Texas continues to see unprecedented growth, entrepreneurs like Pettit are hoping to solve the housing affordability crisis by turning to this innovative, automated technology.Pettit and his business partner Lance Thrailkill say their crew is constantly improving the concrete mix used to print.“That’s what we’ve really been tinkering with is different mixes and every mix is different,” Thrailkill said. “The print comes out different and dries quicker or slower depending on how much water is in there.”
Johnathan Johnson
/
KERAA 3D printing nozzle layers the walls of a barn in Kaufman, Texas, on Dec. 20, 2023. “Probably the easiest way to describe it is a robot that has a soft serve ice cream cone machine at the end of it, and so we’re just pushing concrete out just like that,” Printed Technologies CEO Craig Pettit said.
The company has so far built at least six structures with a 3D printer, including houses, throughout North Texas.Thrailkill said the new technology could soon change the housing market. It’s one of the reasons he’s invested in the business.“We really want to help solve the affordable housing crisis here in America and really, worldwide,” he said.Right now, the cost of 3D printing a house is about the same as building with traditional methods. Pettit said many start-ups, like Printed Technologies, are racing to develop a more affordable way to build.“One of the things that I’ve done over the past three years is just simplify everything within the technology to make it easy to set up, make it easy to take down,” Pettit said.Tim Landau is another industry entrepreneur and the owner and CEO of Hive 3D Builders. His company built what could be one of the largest single family homes made by a 3D printer in Burton, east of Austin.Like Thrailkill, Landau says what sparked his interest in 3D printing was trying to solve the affordability gap.“That gap is, you know, specifically, it’s the difference between what the median income person can afford for a house and what the median price for a house is,” Landau said.
Courtesy
/
Hive 3D BuildersA completed 3D printed house in Burton, Texas between Austin and Houston.
Another issue is the supply gap — how many houses are on the market. A recent report found Dallas alone needs as many as 60,000 more homes to meet demand.“It’s kind of a solvable problem,” Laundau said. “You know, your big production builders, they can ramp up and build more houses to close that gap.”But when newly built houses are upwards of half a million dollars or more, Landau said the only solution is to do something different.“Everything points to more automation, whether it’s 3D printing or other forms of automation to help narrow those gaps,” Landau said.3D printing also reduces the number of people needed to build a house. It usually only takes a two- to four-person crew.It’s also a quicker process — Printed Technologies can print the frame of a 1,700-square-foot home in about two weeks.That might sound like it’s replacing much-needed jobs, but according to Associated Builders and Contractors, there’s a shortage of more than half a million workers in construction.Landau says 3D printing helps alleviate that labor shortage.“So it’s supposed to not eliminate jobs,” he said. “It’s supposed to take the place of jobs that right now we don’t have anyone to do.”
Johnathan Johnson
/
KERA News3D printing nozzle layering the walls to a barn in Kaufman, TX on Dec 20, 2023.
Still, this new, burgeoning industry does face its challenges. Right now, the cost of printing a home is just as much as building one traditionally. There also isn’t a huge demand for 3D printed homes in the Dallas area, according to the Dallas Builders Association.A spokesperson for the association said the technology does have the potential to solve the ongoing housing and labor shortages.Landau says right now the industry could go one of two ways — one is that it becomes a niche industry for people who can afford customized 3D printed homes. The other is, if companies find ways to lower the extra cost, it could become the new normal.That’s what Lance Thraillkill at Printed Technologies sees happening.“In the next five to ten years, it’ll be adopted, across, you know, the entire United States and worldwide would be my expectation,” he said. “And how much that is embraced will be dependent on the cost.”That means someday in the not too distant future, houses and even entire neighborhoods could be built — at least partially — by robots.Got a tip? Email Pablo Arauz Peña at parauzpena@kera.orgKERA News is made possible through the generosity of our members. If you find this reporting valuable, consider making a tax-deductible gift today. Thank you.
Partners break ground on state’s first multifamily passive housing project
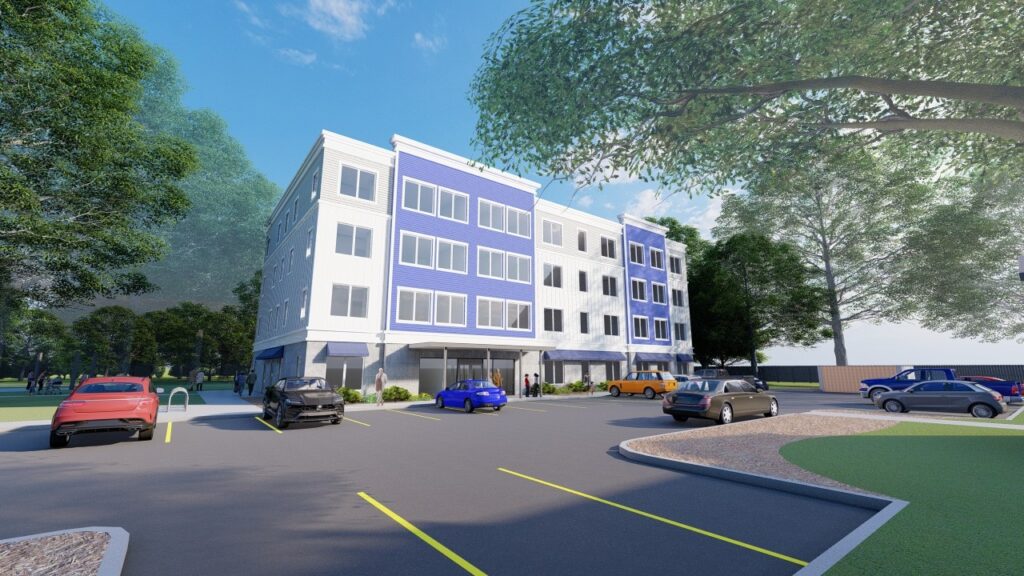
Pinnacle Construction Group has started building what will be the first multifamily certified passive housing development in the state of Michigan. The Grand Rapids-based design-build firm began site work last month and will hold a groundbreaking Jan. 12 for Samaritas Spring Lake, a 53-unit affordable housing rental project at 734 E. Savidge St. in Spring […]
3D-printed, organic formations by external reference engulf la manso store in barcelona
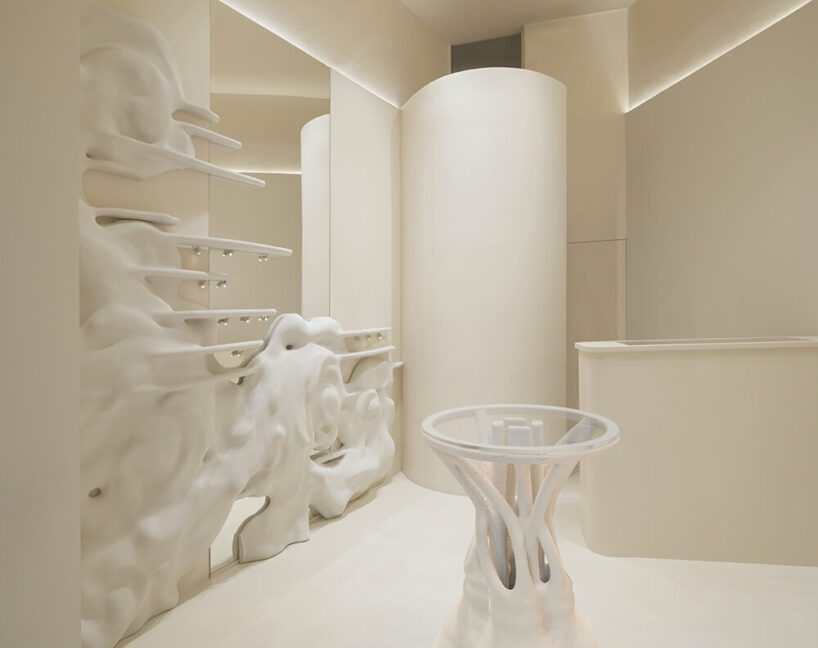
inside la manso store by external reference in barcelonaSpanish architecture studio External Reference has been commissioned to design the first flagship store for La Manso, a contemporary costume jewelry brand, in the heart of Barcelona‘s Eixample district. The 25 sqm boutique is located just a few meters away from the house where Adriana Manso, the brand’s young founder, was born. Turning plastic pieces into a form of luxury, La Manso aims to usher in a new era, bringing it closer to the world of haute couture with unique and iconic designs. Following this vision, External Reference’s Carmelo Zappulla combines the floral elements of the store’s impressive modernist facade with the contemporary plasticity of the brand’s products to create captivating 3D-printed displays, reinterpreting classic decorations with a careful mix of craftsmanship, design, and technology.image courtesy External ReferenceLaMáquina’s 3d-printed displays echo plasticity & floral motifsThrough 3D-printed pieces exclusively designed by LaMáquina, Carmelo Zappulla (see more here) envisions the store‘s interior as an extension of the building exterior. Organic forms take center stage, turning the facade’s ornaments into large rosettes with futuristic glitches and bas-reliefs arranged at different heights, ranging from 90 centimeters to 1.70 meter. These elements exhibit La Manso’s jewelry and accessories around a small center table, carefully illuminated by adjustable mini-spotlights. Using mirrored surfaces, the space expands, while a neutral and elegant coating establishes an abstract backdrop for the iconic pieces. As part of the exhibition, the jewelry is illuminated to highlight the uniqueness of each piece, creating an intimate and deliberate atmosphere that invites exploration and the discovery of the perfect item.In addition, the store hosts a small showcase that, following the owner’s wishes, recovers the style of mythical jewelry stores, inviting passersby to glimpse at the objects in total freedom from the street. image courtesy External Referencemerging indoors and outdoors, physical and digitalExternal Reference’s conceptual design for La Manso extends to the street by repeating, mirroring, and reinterpreting the brand’s logo, infusing it with three-dimensional elements present within the interior’s creative language. In the detail of the sign, strategically placed under the corner bow window that embraces the surrounding streets with its decorations, a coherent visual connection is established between the retail store and urban environment. External Reference, as in its long history of exploring new 3D printing technologies applied to design and architecture, has relied on the experience of LaMáquina to create the store’s custom-made furniture. ‘The purpose is to build a captivating and immersive brand experience that invites users to transcend the digital realm and immerse themselves in a physical space where they can personally contemplate each piece,’ reflects the studio. image © Anna Mas | @annamas_photoimage courtesy External Referenceimage courtesy External Referenceimage © Anna Mas
ET Explainer: Building the future, exploring 3D printing in construction
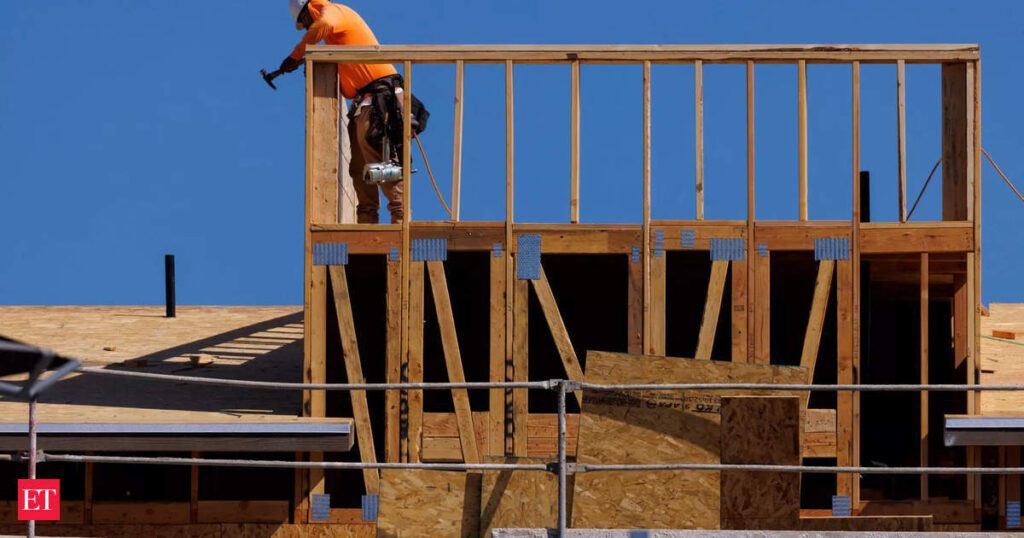
Three-dimensional (3D) printing, also known as additive manufacturing, has been making significant progress globally across various sectors such as manufacturing, aerospace, healthcare, automotive, energy, electronics, fashion, and consumer goods. In real estate and construction, 3D printing is being explored with projects ranging from small structures to entire buildings. Recently, L&T and IIT Madras developed India’s first 3D-printed post office in Bengaluru’s Cambridge Layout, while Godrej Constructions built an office near Mumbai in just 40 hours. Given the swift progress in technology and the growing investments in the industry, it is only a matter of time before 3D printed houses become a tangible reality in India through 3D printing services. 1. What is 3D Printing Technology:3D printing, also known as additive manufacturing, revolutionizes traditional manufacturing processes. It involves creating objects layer by layer from digital models. This method allows for the production of intricate and customized designs by depositing materials in a precise manner.2. How is this utilised in the real estate and construction sector?In real estate and construction, 3D printing transforms the conventional approach by enabling the construction of buildings and components layer by layer. This technology offers unprecedented advantages, including the ability to create complex designs efficiently and with minimal material waste.3. What are key benefits of 3D printing’s usage in realty and construction?3D printing enhances construction timelines by automating the building process, resulting in increased speed. This acceleration is complemented by improved efficiency, as the technology minimizes material waste, promoting sustainable construction practices. Additionally, 3D printing provides a remarkable level of flexibility, enabling the construction of highly customized structures that can effectively address a wide range of architectural demands.4. How does it stack up against conventional construction methods in terms of cost, efficiency, and durability?Despite the potential for higher initial investment costs, 3D printing in construction yields long-term savings through decreased labor and material expenses. The technology’s efficiency is underscored by rapid construction times, which significantly contribute to the overall efficiency of a project. The durability of 3D-printed structures is contingent upon the materials employed, and ongoing advancements in materials science aim to further enhance their robustness, ensuring a lasting and resilient built environment.5. Can this be used for construction of a large scale or tall superstructure project?The 3D printing technology is scalable and has been effectively applied to large-scale projects like houses and bridges. The process involves layer-by-layer construction, enabling flexibility and adaptability to diverse project sizes. While the technology has proven successful in the construction of expansive structures, challenges arise when applying it to extremely tall buildings. The construction of skyscrapers presents technical complexities such as structural stability, material strength, and printing precision over extended heights. Researchers in the field are actively addressing these challenges to expanding its applicability to even more ambitious and vertically challenging projects in the future.6. What are its limitations based on the progress made by this technology so far?Current material options for 3D printing are more limited compared to traditional construction materials. Challenges may arise for constructing very large or intricate structures, necessitating ongoing research and development. Skilled technicians are essential to operate and maintain 3D printers effectively, ensuring optimal performance.7. Which are the marquee projects globally built through this technology so far?–Dubai’s “Office of the Future”: An office building constructed using advanced 3D printing methods.–Nantes, France: A noteworthy 3D-printed house showcasing innovation in residential construction.–China: Various construction initiatives employing 3D printing methods, demonstrating its efficiency and sustainability in different projects.8. Job Loss Concerns:While 3D printing technology transforms traditional roles, it is more likely to lead to a shift in job requirements rather than widespread blue-collar job losses. New opportunities emerge in roles focused on operating, maintaining, and advancing 3D printing technologies.9. What sort of regulatory changes need to be made for 3D printing technology’s use in real estate and construction? Any global benchmark on this yet?Regulatory frameworks require adaptation to accommodate the unique aspects and standards of 3D printing in construction. Establishing clear safety guidelines is crucial to ensuring the structural integrity of 3D-printed buildings.Regulatory frameworks for 3D printing in construction are still evolving, and there is no one-size-fits-all global benchmark. Different countries are developing standards based on their experiences, technological advancements, and the evolving nature of 3D printing in the construction sector.
This wildly massive 3D-printed home is the first of its kind: ‘[It] can withstand the hurricanes and heavy storms’
This January, design studio Hannah constructed the first multistory building in the U.S. made by a 3D printer, reports Evan Garcia of Reuters.The process of 3D printing creates objects from a digital blueprint. “Working entirely automatically, the printer creates a model over a period of hours by turning a 3D CAD drawing into lots of two-dimensional, cross-sectional layers — effectively separate 2D prints that sit one on top of another,” says Chris Woodford of Explain That Stuff! The machine puts down many layers of liquid material such as melted plastic, slowly building up a precise shape as each layer hardens.In most cases, this technique is used on a small scale to make figurines, household items, and parts for manufacturing companies. Using 3D printing technology for concrete buildings is newer, but companies like Gensler and WinSun have been doing it since the mid-2010s, as Architect Magazine reports.What makes this project different is that it’s the first multistory house constructed using this method in the U.S. “One of the things about printing a second story is you require, you know, the machine,” says architect Leslie Lok, who designed the new home. “And of course, there are other challenges: structural challenges, logistic challenges when we print a second-story building.”The home Hannah built is a two-story, three-bedroom, 4,000-square-foot house, Garcia reports. The design takes about 330 hours total to print, using a machine that weighs more than 12 tons.The use of 3D printing could represent a major shift in the construction industry. A 3D building takes fewer workers to construct since most of the materials are actually put in place by the machine.The printer also works faster than the average construction crew, which takes about seven months on average, according to the U.S. Census Bureau. This could mean faster, cheaper home construction.Meanwhile, concrete is a strong material, which Garcia says, “can withstand the hurricanes, heavy storms, and other severe weather in Texas that is becoming more frequent and severe due to climate change.”Investing in a sturdy 3D-printed house could be a smart choice for residents. Garcia reports that this 3D-printed house has already been sold.Join our free newsletter for weekly updates on the coolest innovations improving our lives and saving our planet.
3D printing technology building transitional housing for Siksika Nation

Work on the foundations has already begun and by Oct. 16 the printer will begin running on the 3D concrete layers that will be used to construct four fourplexes on the Siksika Nation.“I’ve been thinking about using the technology to build housing out here and it sort of went from there and to putting together a proposal and getting funding and then ultimately starting to build the project,” said Ryan Hall, housing manager of Siksika Housing on the southern Alberta First Nation.
3D concrete printing technology—a method to create a three-dimensional object layer-by-layer–has been around for about a decade, he says. In the last few years, it has become more commercially viable.
This past summer, Hall began talking with nidus3D, a Kingston, Ont.-based company that does 3D construction. On the strength of that partnership, the University of Calgary School of Architecture and Planning was drawn into the project and the three worked together to develop the 16 transitional units.
The exterior walls for the fourplex are constructed using 3D concrete printing technology. (Rendering provided)Kakatoosoyiists, which means Star Lodges, will be the largest 3D concrete printed housing project in Alberta.
The 3D printer operates on site. A robotic arm, directed by railings that have been installed on site, layers the concrete where it is required. The exterior walls will be laid on top of a concrete slab-on-grade foundation.
Hall said they had considered using the 3D technology for interior walls, as well, but opted to go with conventional walls inside. It’s less print time, he says, and saves money.
The print time to do the exterior walls is about one week per building.
Electrical, plumbing, windows and finishing work will then be undertaken.
“We’re still trying to figure out some supply chain issues to acquire materials, but I think in the new year, they’ll be ready. Our contract requires that they are done by March 31,” said Hall.
Kakatoosoyiists will consist of 16 one-bedroom-one-bathroom units grouped in fourplexes. Each unit will be about 600 square feet. They will serve as homes for single or double occupation. Double occupation could be partners or a mother and child.
As transitional homes, they could be occupied from six months to two years, says Hall.
The units are intended for Nation members who are experiencing a housing crisis, whether they are moving back from Calgary because they can no longer afford the rent or they are fleeing domestic violence.
“Whatever it is, they’ll have supports in place that could be done through home visitation or maybe providing them a service (to help) them move into permanent housing,” said Hall.
As for permanent housing, Hall says that’s a three-to-five-year plan which will see Siksika Nation build three- or four-bedroom homes.
There is a possibility that 3D printed concrete technology could be used there too as it would provide a faster turn around. A company can be hired to do the work or the Nation could look at undertaking the work itself.
“I would consider this a pilot project,” said Hall. “And one of the ideas is, if it makes sense to us after we’re done, and I’ve done sort of an analysis on this, maybe the nation would buy a machine and actually design and build our own housing.”
Using their own design will allow Siksika Nation to incorporate Blackfoot knowledge, which is exactly what Kakatoosoyiists has done with Elder Eldon Weasel Child having input.
The roof is designed to look like a tipi, with wood beams projecting like tipi poles. Inside, there are interior spaces in the bedrooms to accommodate sacred bundles as sacred bundle holders may someday be residents. There is also a gathering area off the main entrance.
Hall says their innovative construction project is garnering some attention from Indigenous communities in Alberta, especially, because they are able to get input from Elders to design the homes, which is not something that can be done with prefabricated homes.
3D printing technology also provides for a sustainable way of building as it minimizes waste, reduces carbon emissions, and utilizes locally sourced materials.
Hall says he had no problems convincing chief and council to embrace the cutting-edge technology, especially since service sites were already available. A band council resolution was required for the funding application.
The project is funded at $2.6 million from Indigenous Services Canada.
Local Journalism Initiative Reporters are supported by a financial contribution made by the Government of Canada.
3D printed home built in Muscatine using robotic printing system
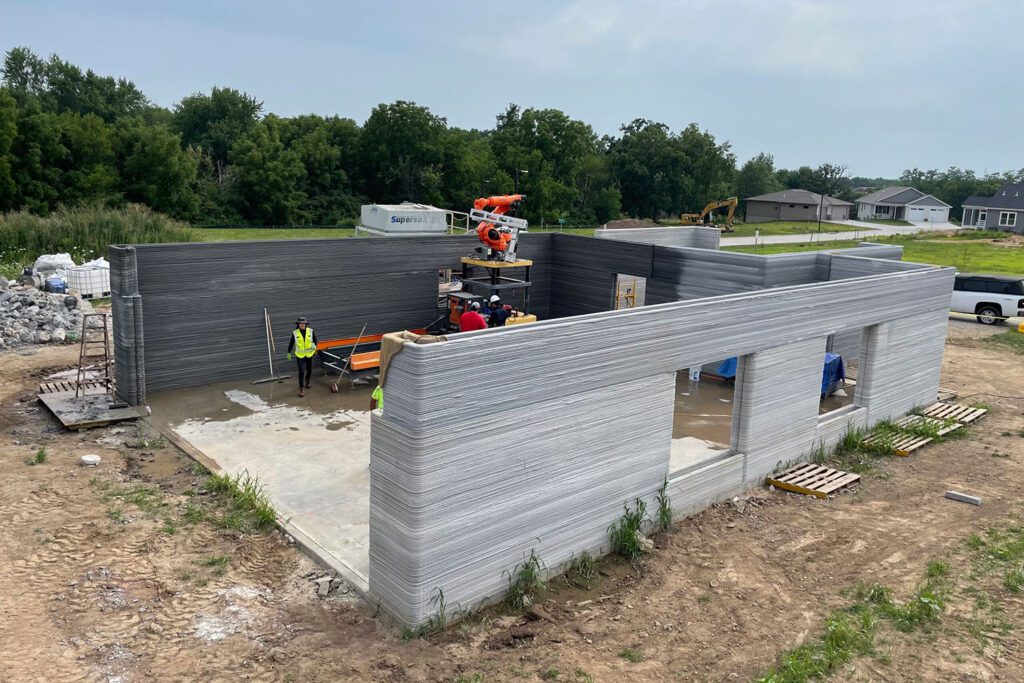
3D printing technology has the potential to transform the US homebuilding industry by offering faster, cheaper, and better solutions for housing. Surprisingly, 3D-printed structures that were once considered impossible to build are now becoming a reality, and progress is happening at an impressive speed.
Alquist 3D, a leading 3D construction company, recently completed the first 3D-printed house in Muscatine, Iowa, using RIC Technology’s advanced robotic arm-based 3D printing system. The construction began in October of this year, and the company finished printing the home’s ten-foot-tall exterior walls in November.
The new 3D printing system by RIC Technology employs advanced robotic arms to build the entire house in a highly automated process, freeing up human labor from dangerous and tiring work.
Compared to conventional gantry-based 3D construction systems that can cost thousands of dollars in labor and equipment rental fees and take up to 3 days to set up, the new system eliminates the need for a massive framework to support the printer head during the printing process. Transporting the gigantic gantry-based system to a construction site typically requires disassembly and the use of three semi-trucks, a large-scale crane, and a telehandler.
RIC Technology’s robotic arm system has some unique advantages over other systems on the market. Its retractable design and compact size make it easy to transport and quick to set up, which can significantly reduce labor and transportation costs. The robotic arm system requires no assembly and can be operational in 2-4 hours. Additionally, this system can cut construction costs in multiple areas, including transportation, setup, and daily operations.
“Compared to gantry-based 3D printing, our robotic arms can reduce costs by about $16,000 per home,” said Ziyou Xu, founder of RIC Technology. “Robotic arm-based 3D printing is one of the most promising solutions to address the global housing shortage crisis.”
In addition, 3D-printed houses promise significant energy savings, lowering the energy expenses of the occupants by 30% due to the insulation features of the houses. 3D-printed homes are also very resilient to withstand natural disasters and extreme weather conditions, such as the harsh winter in Iowa.
According to Xu, the technology enables builders to construct more affordable, resilient, and durable homes with fewer resources and lower costs. That is why the City of Muscatine, in partnership with The Community Foundation and Alquist 3D, began building a set of 10 homes in Muscatine, Iowa, using RIC’s groundbreaking system.
It was the second site Alquist 3D built on in Muscatine. The first house, which initially broke ground in May, was supposed to showcase the company’s innovative technology, which had already been used for Habitat for Humanity projects. However, the project faced a setback in late November when Alquist had to demolish the first of these ten homes before it could be completed. The reason was that the printing mix failed to reach the required 5,000-psi strength level, raising doubts among structural engineers about the durability of the material.
RIC Technology’s innovative technology is not only being used in Muscatine but also in other parts of the world, such as Australia and Rwanda. The company is committed to revolutionizing the 3D printing industry by providing cost-effective, time-saving, and labor-reducing solutions for the global housing market.
Crafting waves: The poetic façade of Studio RAP’s 3D printed ‘Ceramic House’
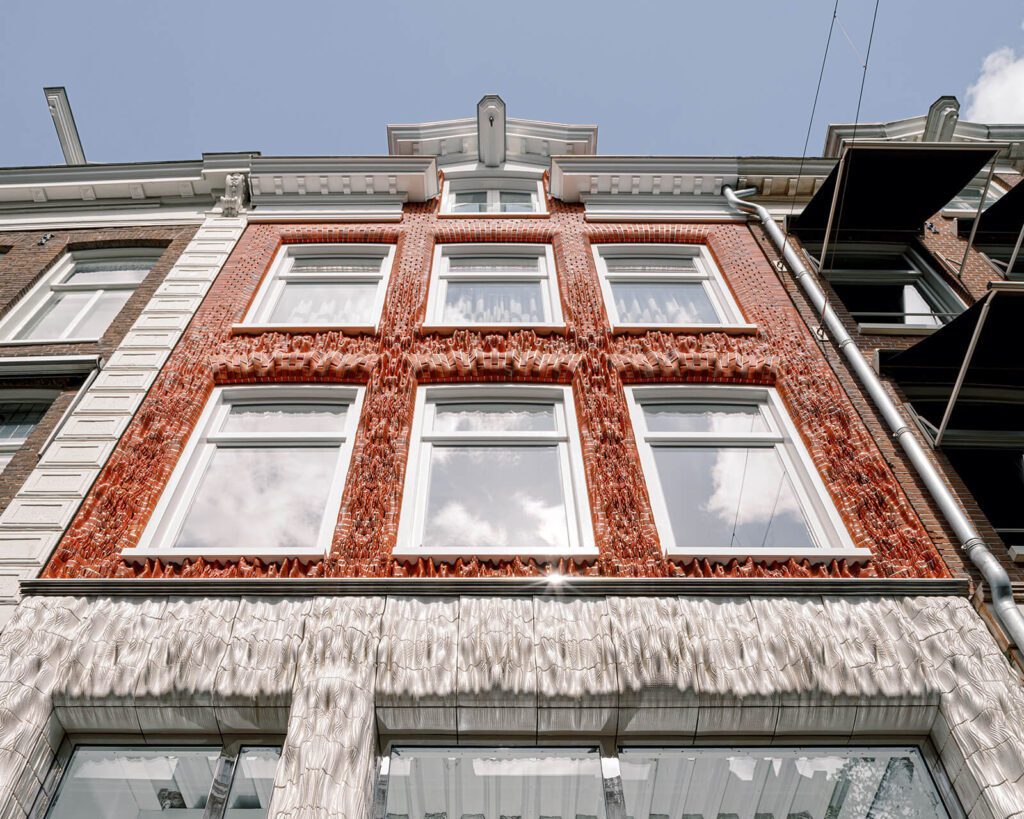
Elegant creases, interlooping yarns and stitch patterns; these are not just elements of a finely crafted garment but the poetic design language of Dutch design practice, the Studio RAP’s Ceramic House. In the world of architecture, the façade is the face of the building. Nestled in the heart of Amsterdam’s P.C. Hoofstraat, this boutique design transcends conventional norms and becomes a canvas, creating an organic, wave-like poetry. Far beyond a static exterior, this façade is a living testament to the delicate dance of form and function. It seamlessly blends tradition with innovation, not merely as a visual spectacle but as a tactile and immersive experience, inviting onlookers into a world where architecture becomes an art form.
Studio RAP takes inspiration from knitwear to redefine Amsterdam’s shopping street Image: Riccardo De Vecchi
In the genesis of the Ceramic House, the studio received a concise yet ambitious design brief from a client renowned for iconic architectural creations. Tasked with adorning Amsterdam’s shopping street with a unique boutique façade, the challenge was clear: conceive a retail design that transcends the ordinary. To meet this, the studio delved into the unexplored, seeking inspiration not from conventional architectural norms but from the world of knitwear.
When 3D printing meets knitwear inspiration, the artistic journey of the Ceramic House Image: Riccardo De Vecchi
The studio was in the midst of experimenting with 3D printing ceramic tiles for a previous project, New Delft Blue, when the idea of a façade entirely clad in 3D-printed ceramic tiles took shape. The result was the Ceramic House, an architectural masterpiece inspired by the artistry of knitting.
The Ceramic House harmoniously integrates with Amsterdam’s historic tapestry Image: Riccardo De Vecchi
Amsterdam, with its cobbled stone streets and historic canals, is an architectural tapestry that weaves together the past and the present. Amidst this, the house stands as a distinct thread, weaving its own narrative. The key to the success of this project lies in its harmonious integration with the surroundings. Studio RAP meticulously replicated the silhouette of the original façade, maintaining the tripartite structure of the street. Expressive at ground level, the façade transforms as it ascends, synchronising with the surrounding structures. Architectural elements like rowlock arches and cross-bond brickwork echo the neighbouring buildings but with a contemporary twist. The connection of flushes between the new and adjacent facades, achieved through 3D scanning, showcases a commitment to precision, ensuring that the house stands as a luxury boutique seamlessly blending with its historical environment.
Textile-inspired layers come to life at the Ceramic House Image: Courtesy of Studio RAP
The Ceramic House redefines architecture with algorithmic artistry Image: Courtesy of Studio RAP
Digital design algorithms, a language of their own, become the brushes in Studio RAP’s hands. The Ceramic House explores the reinterpretation of glazed ceramics, infusing the historical city of Amsterdam with a new design vocabulary. The scale, size, type, and colour of the ornaments and materials are all carefully synced with the neighbouring buildings to allow a seamless integration of traditional and contemporary architecture. The façade’s intricate layers, inspired by textiles, mimic the elegance of creases and stitch patterns. An organic, wave-like quality unfolds as viewers approach, unveiling new elements within the bespoke 3D-printed ceramic tiles. This is not just architecture, it is a symphony of algorithmic design and historical resonance.
Studio RAP pushes boundaries with 3D printing and a collaboration with robotic precision Image: Courtesy of Studio RAP
With inspiration drawn from the rich ceramic collection of the Rijksmuseum, the national museum of The Netherlands, the studio pioneers large-scale 3D printing technology. This isn’t merely printing tiles; it is an art form where architects collaborate seamlessly with advanced robotic systems. The result is highly differentiated and algorithmically designed details, showcasing a commitment to pushing the boundaries of architectural design.
The studio’s narrative of 3D printing, tradition and artistic expression Image: Courtesy of Studio RAP
The significance of using these innovative technologies lies in the studio’s vision to enrich the world with a new architectural language. Breaking barriers, they utilise 3D printing to gain unprecedented control over design, expression and precision. It is not just about industry digitisation; it is about preserving the cherished qualities of artisanal craftsmanship. Collaborating with Royal Tichelaar, one of the oldest companies in The Netherlands for ceramics and glazes, adds a touch of tradition to this technological partnership.
The Ceramic House welcomes with 3D-printed ceramic tiles and a blend of form and function Image: Courtesy of Studio RAP
Laser-cut stainless-steel cassettes frame abstract ornamentation, a modern twist on tradition Image: Courtesy of Studio RAP
At street level, the house beckons with large 3D-printed ceramic tiles glazed in pearl white, subtly touched with yellow by Royal Tichelaar. Visually expressive at eye level, these tiles transition gracefully to a flush alignment with the ground, creating a harmonious aesthetic. Ascending higher, the façade unfolds another layer, showcasing 3D-printed bricks glazed in three shades of red. The abstract ornamentation dances with the original masonry cross bond, housed within the laser-cut stainless-steel cassettes, a nod to historical flushes.
The ‘pearl-stitch’ speaks a language of tradition and avant-garde sophistication Image: Courtesy of Studio RAP
For Studio RAP, 3D printing and algorithmic design aren’t just tools; they are the essence of the Ceramic House’s identity. Drawing inspiration from the art of knitwear, these strategies amplify the intricate layers of the façade design. There is a fascinating parallel between traditional knitting patterns and the tiles; both following conceptual instructions. The result is what the studio calls the “pearl-stitch”, a unique architectural expression merging historical ceramics with the allure of knitwear-inspired details. It is not just a building, it is a conversation between traditional architecture and the avant-garde.
The Ceramic House is an invitation to explore architectural intricacies Image: Courtesy of Studio RAP
As visitors approach the Ceramic House, a layered experience unfolds. From a distance, it seamlessly blends with the legacy of the street. Come closer, the undulating façade sparks curiosity, and the pearl stitch pattern emerges. Opening the door is an invitation to feel the texture, a tactile exploration of bespoke details. Each unique tile ensures that every visit unveils a new detail, creating a timeless and layered experience. It is not just a façade; it is an immersive journey through layers of innovation and tradition.
Ceramic House reflects Studio RAP’s transformative role in design Image: Courtesy of Studio RAP
The Ceramic House isn’t an isolated project; it is a concrete manifestation of Studio RAP’s broader vision. Situated in Rotterdam, the team redefines the traditional role of architects. They aren’t just architects, they are entrepreneurs, craftsmen and innovators. The studio challenges conventions, injecting greater excitement and diversity into the world through innovative design.
Studio RAP’s Ceramic House project is a blend of tradition and excitement Image: Courtesy of Studio RAP
In the words of the studio, “The Ceramic House project reshapes architectural expression by seamlessly blending tradition and innovation, reintroducing bespoke details to architecture. It’s more reshaping; it’s a revolution that challenges the status quo and presents a fresh architectural style. The project is a testament to the Studio RAP’s commitment to infuse the world with greater excitement and diversity through architectural innovation.”
Studio RAP shapes the future of architecture with a hands-on, innovative approach Image: Riccardo De Vecchi
Studio RAP isn’t just an architectural design company; it is a harbinger of change, challenging conventional ways of building. With architects, designers, roboticists, programmers and researchers collaborating in an industrial atmosphere surrounded by robots in Rotterdam, the studio embarks on a hands-on approach to solving problems in the building industry. Studio RAP doesn’t just create expressive buildings, it reimagines the entire architectural profession, embracing innovation as the cornerstone of its practice.
Studio RAP’s ceramic house sparks curiosity in the possibilities of façade design Image: Riccardo De Vecchi
The Ceramic House stands not just as a building but as a testament to the marriage of tradition and innovation. As we trace the undulating façade and feel the tactile allure of each bespoke tile, we are invited into a realm where architecture becomes an immersive journey. Beyond its physical form, the house embodies a question: What other uncharted territories can façade design explore? Studio RAP’s revolution extends beyond a single, prompting us to ponder the possibilities that lie ahead in the dynamic tapestry of architectural innovation.
[embedded content]
Feel the texture, experience the details; the Ceramic House invites you on an immersive journey through the intersection of tradition and the avant-garde Video: Oculus Film
Project Details
Name: Ceramic House Location: P.C. Hooftstraat, Amsterdam (NL) Client: Warenar Real Estate Architect: Studio RAP Co-Architect: Gietermans & Van Dijk Contractor facade cladding / 3d-ceramic-printing: Studio RAP Firing and glazing: Royal Tichelaar Main contractor: Wessels Zeist (VolkerWessels) Film: Oculus Film
This 20-foot tall 3D printer can produce entire homes in just 24 hours — all thanks to this surprising material
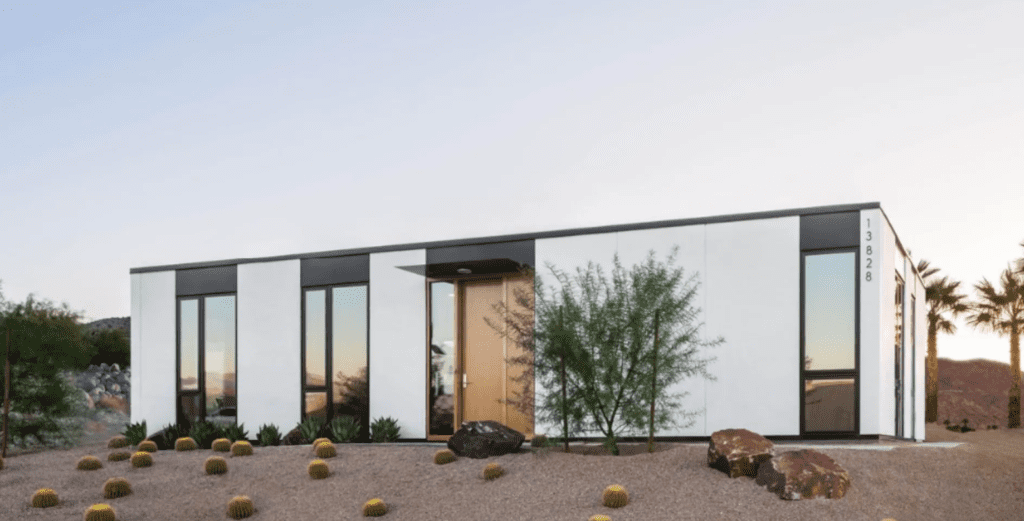
Mighty Buildings, a new business from Oakland, California, promises to build — or really, print — a house in 24 hours.
It’s part of an innovation in the home construction sector that’s five years in the making, according to the company’s website.
Warp News reports that Mighty Buildings is different from similar companies because the team can print the roof, ceiling, and other parts of the home with extreme speed.
“Because we’re building homes for people to live in, we’ve been very deliberate in carrying out our vision to make housing better. This isn’t software that can be debugged on the fly,” Slava Solonitsyn, the CEO and co-founder of Mighty Buildings, told Dwell. “We’re now ready to scale our production with full confidence in our certifications and code compliance of both our material and technology.”
The printer, which is 20 feet tall, produces composite stone panels from recycled materials. The process automates much of the work — around 80% — in large part because the company can print a home’s entire structural shell, reducing the amount of assembly needed later, Dwell reports.
The company cites several global problems that this method is meant to address, including high home prices, population growth outpacing construction projects, and supply chain shortages.
#cool_newsletter_53e74c5a-ee3d-46f7-9b1c-f120b3daa4ca .cool_newsletter__inner span{color:#000000}
JOIN OUR NEWSLETTER
Good news, green hacks, and the latest cool clean tech — straight to your inbox every week!
Sustainability is another major goal. The company claims its process and materials produce just 1% as much waste compared to homes constructed by conventional means. The printing process uses 60% recycled materials at this point, and the team hopes to create zero air pollution by the year 2028.
These advancements also cut costs, saving prices for homebuyers. Mighty Buildings claims that its printed homes cost 45% less than comparable houses in the California market.
Dwell reports that available models include 350-square-foot studios and a three-bedroom, two-bathroom home. The latter option is priced at around $285,000.
Mighty Buildings is currently taking orders. The company’s website showcases a community in Southern California with 30 printed homes in the desert. The houses look futuristic in design, combining modern hardware with sustainable technology, including rooftop solar panels. Soon, the company hopes to take its concept nationwide.
“With a strong foundation in robotics, manufacturing, and sustainability, the Mighty Buildings founding team knows the different facets of the issues that face modern housing,” Eric Migicovsky, a partner at the startup accelerator Y Combinator, told Dwell. “Accessory dwelling units are just the start in further building out their unique approach to building.”
Join our free newsletter for weekly updates on the coolest innovations improving our lives and saving our planet.
Cool Picks
Floating, 3D-printed, skinny and green: Top 10 Houses of 2023
From a svelte residence that stays cool with the breeze, to a cutting-edge 3D-printed housing development, plus a prototype bamboo dwelling designed to handle flooding, our selection of the top 10 houses of 2023 showcases the finest residential design that we’ve seen throughout the year.In this look at the year’s best houses, we attempt to showcase a wide range of residential design, from smaller simple dwellings to larger luxury homes, with some impressive sustainability and clever space-saving ideas.The projects hail from various countries, including the United States, England, Norway, Scotland, Australia, and Vietnam.In no particular order, read on below for our selection of the top 10 houses of 2023 and be sure to hit the gallery for a closer look at each.Chic Vid House – STD Design Consultant
The Chic Vid House, by STD Design Consultant, is located in a bustling area of Ho Chi Minh City, on a plot measuring just 3.9 m (almost 13 ft) in widthTriệu Chiến
STD Design Consultant has made fine use of a very cramped inner-city plot in Vietnam with a tall and skinny residence named the Chic Vid House.The home is located in a bustling area of Ho Chi Minh City, on a site measuring a mere 3.9 m (almost 13 ft) in width, plus a more reasonable 19.6 m (64 ft) in length. The space-saving dwelling features an operable facade to naturally control ventilation and sunlight. Its interior is spread over five stories, with tasteful decor and furniture that’s carefully arranged to flatter the narrow space.Floating Bamboo House – H&P Architects
The Floating Bamboo House, by H&P Architects, is designed for people whose lives are river-based and at threat due to climate changeLe Minh Hoang
H&P Architects has designed a floating house envisioned for river-based populations under threat from climate change, especially those living on and around Vietnam’s Mekong Delta.The Floating Bamboo House is constructed from bamboo stems, as well as weaved bamboo sheets, leaves, corrugated iron, and bamboo screens. This is all joined together using simple latches and ties, and it floats using plastic drums attached to the home’s underside. Its interior measures 36 sq m (roughly 390 sq ft) and features a flexible layout spread over two levels. Though still in the prototype stage, it will eventually include a kitchen area, as well as a bathroom and bedrooms, and have freshwater storage tanks and septic tanks installed.Green House – Hayhurst and Co
Green House is arranged around a large internal courtyard with a first floor balcony areaKilian O’Sullivan
Recently hailed as the Royal Institute of British Architects 2023 House of the Year, Green House, by Hayhurst and Co, is a lush and light-filled family residence in London.It’s fronted by an eye-catching facade made up of sliding polycarbonate roofing sheets, which allow daylight to permeate within. It was part-built using sustainably sourced timber, while roof-based solar panels help reduce its grid-based electricity use. The home is arranged around a large internal courtyard, with a first floor balcony, and features an atrium designed to promote stack ventilation. The interior’s rooms are quite large but can be easily subdivided using curtains if required, ensuring flexibility if the family’s needs change in the future.Wolf Ranch – BIG, Icon, Lennar
Wolf Ranch was created by BIG, Icon, and Lennar. Its first residents began arriving in September, 2023Lennar/Icon
Though 3D-printed architecture is still relatively niche, this ambitious development of a hundred 3D-printed homes named Wolf Ranch looks set to become a major step forward in it going mainstream in the United States. Located near Austin, Texas, the project’s first model home was recently revealed and residents started moving in a few months ago.The 100 3D-printed houses range from 1,500 – 2,100 sq ft (roughly 140 – 195 sq m), all on one floor and their overall design is inspired by traditional Texas ranches. They come in eight different floorplans and offer either three or four bedrooms and two or three bathrooms.Helvetia – Austin Maynard Architects
Helvetia, by Austin Maynard Architects, has been transformed from a drab and rather dark home into a light-filled residence that features multiple gardensDerek Swalwell
Austin Maynard Architects recently breathed new life into a dilapidated terrace house in Melbourne, Australia, increasing natural light inside and adding a generous atrium and multiple garden spaces.Helvetia started out as a family home in the late 19th century before being turned into two dwellings in the 1960s. It was then reconfigured yet again in the 1980s into separate apartments that were dark and uninspired. Rather than knock this awkward collection of buildings down and start afresh, the studio kept what it could and worked around the structural issues. The main entrance has been moved, a light-filled extension added, and a host of greenery and green tech, such as solar panels, installed along the way.Woven – Giles Miller Studio
Plastic fantastic: Woven’s exterior doesn’t look all that lush at the moment but its intricate trellis-like plastic screen will become increasingly covered with greenery over timeRachel Ferriman
UK-based Giles Miller Studio’s first residential project is named Woven. The remarkable home is wrapped in an intricate screen made up of a recycled thermoplastic polymer.Woven is located in Kent, England, near the beach, and serves as a family retreat. Its trellis-like screen is quite complex and draws inspiration from the twisted patterns of rattan weave, wrapping almost the entire home, helping to shade its ample glazing. It also has several plants on it that will continue to cover it in greenery over time. Structurally, Woven consists of steel and cross-laminated timber, as well as some concrete in the foundations. Its interior is very nicely done and the understated color palette puts the focus on the natural beauty of the unfinished wood.Transmitter Bunker – Corstorphine & Wright
The Transmitter Bunker, by Corstorphine & Wright, involved transforming a WWII-era bunker into a unique vacation home that’s currently available to rentWill Scott
A WWII-era concrete bunker once used to protect Britain against the Luftwaffe has been transformed into a vacation home in southern England. Corstorphine & Wright, with engineers Symmetrys, retained the character of the bunker, while adding a comfortable interior.The Transmitter Bunker was commissioned in early 1941 and was part of the UK’s Chain Home radar system, serving a crucial role during the Battle of Britain. Other than the large new glazed section, which is meant to bring to mind bomb damage, the exterior of the shelter looks largely left alone. Its interior measures 60 sq m (645 sq ft), and is arranged around a spacious living room that puts the focus on the view.Casa Annunziata – Specht Architects
Casa Annunziata, by Specht Architects, came about when the owners of an ornate 18th century mansion decided to downsize their home to something more modernDror Baldinger
A glass house is always going to be a love-it-or-hate-it kind of deal, but the Mansfield, Massachusetts-based Casa Annunziata, by Specht Architects, is more practical than most.It came about when the owners of an 18th Century mansion decided to downsize and wanted something suitable for themselves and their art collection. The home is arranged simply on one floor and is wrapped in extensive glazing, with an overhanging roof to offer shade and reduce heating and cooling requirements. Almost the entire home is on show, including the bedrooms and even areas of the bathrooms, while the interior decor is very minimalist and open.House Dokka – Snøhetta
House Dokka is perched on massive wooden columns anchored firmly into the rockSnøhetta
Snøhetta has collaborated with engineer Tor Helge Dokka for an impressively energy efficient residential project located in Norway. Named House Dokka, the three-bedroom family house runs off-the-grid with a solar panel array, allowing it to produce more energy than it requires over the span of a few years – which is no mean feat in such a northern country.The home is very well insulated and was constructed using locally produced cross-laminated timber and glued-laminated timber. Interestingly, not a single nail was used during construction, making any eventual recycling much easier than a standard build.Hundred Acre Wood – Denizen Works
Hundred Acre Wood was designed by Denizen Works and is located in rural ScotlandGilbert McCarragher
Hundred Acre Wood was designed by Denizen Works. The project took eight years to realize and is located in Scotland, in a beautiful rural area overlooking Loch Awe.The exterior of the house is finished in recycled TV screens. This actually began as a joke referencing the owner’s dislike of television and matured into a real plan consisting of recycled TV screens crushed into an aggregate, resulting in an attractive silvery look. Its overall form also riffs on historic Scottish architecture as well as the sculptural works of Spanish artist Eduardo Chillida, while the interior is arranged around a very spacious central hall designed to accommodate a large Christmas tree.
Startup CEO says ‘the house of the future costs as much as a car’ — here’s how the company plans to make it happen
New technology from Japanese startup Serendix may eventually turn the dream of home ownership from the seemingly impossible into the possible for many Americans — and help us give our planet an assist in the process.Serendix, which hopes to make housing more affordable, recently combined 3D printing and CNC machining to build a house for the cost of roughly $37,600, according to Adele Peters of Fast Company.Compare that with the median cost of a house in the United States: approximately $431,000, according to The Ascent, a review platform of The Motley Fool.“The house of the future costs as much as a car,” Serendix CEO Kunihiro Handa told Peters.Handa added that the company’s goal is to fully automate the housing industry — much like Japan did with the auto industry more than 40 years ago.3D printing has been around since the 1980s, when Dr. Hideo Kodama created a machine that hardened material with UV light, according to The American Society of Mechanical Engineers. As the technology — and the laws surrounding its use — has evolved, so have the opportunities for its application.Today, an array of 3D-printing materials is available. According to Fast Company, in order to keep costs down, Serendix utilized concrete to print the walls of its 538-square-foot “barnacle” unit, giving an individual or a couple a bit of extra stretching room than a typical 100- to 400-square foot tiny house.[embedded content]The home design is constructed around steel columns and includes one bedroom, one bathroom, a living room, and a kitchen. An incredible time-lapse video shows how they come together.An added bonus? Small homes are eco-friendly because they need less energy to run, so your bank account and the Earth will be thankful. While an average-sized home in the U.S. is responsible for approximately 28,000 pounds of harmful carbon pollution per year, tiny homes emit around 2,000, according to the American Institute of Architects.Serendix told Peters that its 3D-printed house only took 44 hours and 30 minutes to build. The efficiency of the construction time means that negative environmental impact is reduced. Globally, the construction industry is responsible for 39% of polluting heat-trapping gases.Photo Credit: SerendixSerendix has five printers, according to Peters, each of which can construct 50 houses per year, and the company intends to add more in 2024 in order to reach a goal of 850 per year.There’s no word yet on when the company’s technology could be available in the U.S.Join our free newsletter for weekly updates on the coolest innovations improving our lives and saving our planet.