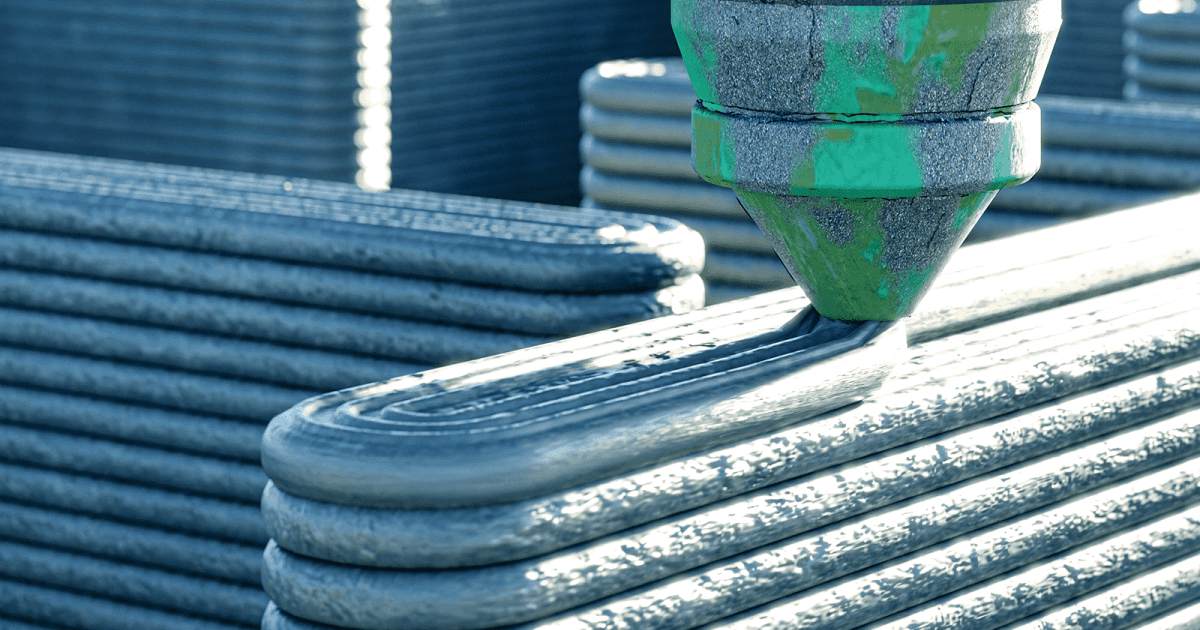
It’s a rare occasion when something debunks the “too good to be true” principle, such as 3D printing an entire house in less than 24 hours. And yet, here we are.
What Are 3D-Printed Houses?
Three-dimensional-printed houses are structures that are built layer by layer using an industrial-grade, 3D-printing technology. This method of additive manufacturing is also known as construction 3D printing.
As tenants move into 3D-printed houses in the first years of their commercial listing debut, 3D printing is on a 23 percent compound annual growth rate over the decade to come, according to Grand View Research. These dwellings — often sharing a gray, shapely appearance with a ribbed texture — are even piquing the interest of NASA, which funded a $57 million project to develop tech for moonside 3D-printed infrastructure.
Highly customizable and free of form, construction 3D printing is a new-age tech on the verge of market disruption, holding the potential to mass produce housing.
What Are 3D-Printed Houses?
Three-dimensional-printed houses are life-size dwellings that use 3D printing as its primary means of construction. With minimal human oversight, these highly customizable structures can be built on-site or off-site within a matter of hours at a fraction of the cost.
Typically, 3D-printed houses feature free-form, curvilinear shapes made out of a cement mix. Projects span from inhabitable beta prototypes under study to move-in-ready affordable housing and even high-end luxury homes.
Aside from time and money, several other reasons explain additive manufacturing’s disruption to the construction market. Many see this type of low-waste, computerized homebuilding delivered from an industrial-scale printer as a way to shelter unhoused communities and a gateway to sustainable, biodegradable housing solutions.
How Are 3D-Printed Houses Built?
Industrial-sized 3D printers build entire multi-unit housing developments one tiny layer at a time. This repetitive process puts the “additive” in “additive manufacturing.”
Following a digital blueprint, a 3D printer will dispense a paste-like mixture. This will consist of choice ingredients — often a cement blend — but can range from sand and special polymers to bio-resins, like soil, clay or wood flour, which is a fine sawdust mixed with a corn-based binder.
How Long Does It Take To 3D Print a House?
Nowadays, industrial-sized 3D printers have made it possible to print an entire house in less than 24 hours.
Keep in mind that a project’s “printing time” may exclude time for any second-fix installations or construction time necessary to piece together a project printed on-site and transported to its final location.
And if you’re trying to build something of scale, like a house, the 3D printer itself has to outsize it. Made out of a steel, quad-truss framework — the kind you’d see as part of a concert stage — these industrial-grade 3D printers form a sort of hollow cube. On top, a robotic arm zips along a track, following pre-programmed instructions being read from the blueprint.
Much like your desk-side inkjet printer, the mixture is then heated during a thermal extraction process. The paste squeezes through a nozzle, bringing the digital rendering into physical form. Before the next layer is applied, the mixture is solidified by a concrete dryer. This process repeats until all uploaded building elements are complete.
It’s important to note that additive construction work sites are not entirely autonomous. Aside from the setup and breakdown of the equipment, human oversight is necessary to ensure there are no technical hiccups. Specialists must be on-site to cut holes for second-fix installments, such as plumbing, electrical wiring, doors and windows.
How Much Does a 3D-Printed House Cost?
Of course, this number will vary from project to project, and face further price contingencies based on the hired companies and materials used (let alone geographic location, size, amenities, design complexity, and so on).
With that being said, developers stateside and abroad report average cost savings of 30 percent.
Three-dimensional-printed houses first hit the U.S. market at the start of 2021. The 1,407-square-foot house — complete with three bedrooms, two baths and a two-car garage in Riverhead, New York — listed as “the world’s first 3D-printed home for sale” for $299,999 on Zillow.com.
ICON, a 3D-printing construction company, said it could produce a 600 to 800-square-foot, economy-sized building for as low as $4,000 in 24 hours, as reported by Business Insider.
Models on the more affluent side of the market can surpass $1 million. Known as House Zero, the mid-century, ranch-style luxury home is a 2,000-square-foot property with a 350-square-foot accessory dwelling unit. Just based on size and location, Zillow estimated the price of this four bedroom, three-and-a-half bath estate at $723,000 to $908,000, according to online specialty magazine All3DP. However, its one-of-a-kind, exceptional design may push it into the seven-digit price range.
When Will 3D-Printed Houses Become Available?
Examples of 3D-Printed Houses
An error occurred.
BioHome3D is a 3D-printed house constructed out of 100 percent bio-based materials. | Video: 3DPrint.com
BioHome3D
The University of Maine Advanced Structures and Composites Center is 3D-printing housing structures exclusively from bio-resins and wood fibers to combat labor shortages and widen access to affordable housing. The demo project, known as BioHome3D, begins with a 600-square-foot prototype that features a fully 3D-printed floor and roof. As a whole, the one-bedroom, one-bathroom building is 100-percent recyclable, made up entirely of biodegradable materials, including wood flour. As a prototype, BioHome3D is equipped with monitoring sensors, measuring thermal, environmental and structural elements, to gather resilience-based data to better inform future designs.
An error occurred.
All East 17th Street Residences feature minimal architectural aesthetics. | Video: FindYourDEN
East 17th Street Residences
These four Austin, Texas properties by construction 3D-printing company ICON feature open-floor plans, minimal architectural aesthetics and private yards. Varying in size, these residences feature two to four bedrooms and range from 1,000 to 2,000-square-foot homes. Each ground floor level is built with a proprietary cement-based material, dubbed “Lavacrete,” to last longer than traditional construction materials, according to the company’s website. The second story incorporates old-school methods, and is constructed out of black metal cladding and rich-colored timber. They share a color palette of green, white and terracotta and have all been sold.
An error occurred.
Mikkel Brich, CEO and founder of 3DCP, talks about the future of 3D-printed construction. | Video: COBOD
House 1.0
With the help of 3D-printing construction manufacturer COBOD, Danish startup 3DCP Group constructed Europe’s first 3D-printed tiny house last year in just five weeks; however, the structure itself printed in just 22 hours. Located in Hostelbro, Denmark, this 398-square-foot structure is composed of three sections that merge at an open, triangular-shaped core. Inspired by the no-frills aspect of student living, the space is economically laid out and contains all the necessary amenities — a bathroom, open-plan kitchen, living room and loft-style bedroom on a raised level. Sebastian Aristotelis, architect at Saga Space Architects who designed House 1.0, said that the project was built at the lowest possible cost, with developers opting for inexpensive materials, like concrete, and constructing the project using a low-to-no waste approach.
More on 3D Printing 25 3D-Printing Companies to Know
An error occurred.
Watch 3D-printing construction company ICON build House Zero, a luxury 3D-printed house. | Video: ICON
House Zero
ICON teamed with architectural firm Lake|Flato to build a three-bedroom, two-and-a-half bath residence just outside of downtown Austin, Texas. Its curved walls and rounded corners are insulated with Lavacrete and reinforced with steel. Paired with a one-bedroom, one-bath accessory dwelling unit, ICON’s website styles the 2,350-square-foot property — which printed in under two weeks — as a “mid-century modernist ranch house aesthetics.” Given its design to consume net-zero energy, Time named House Zero to its Best Inventions of 2022 list. In the months since, ICON has broken ground on a 100-home project, projected to be the largest 3D-printed residential community in the United States.
An error occurred.
Kamp C was built in one piece. | Video: Kamp C
Kamp C
In just three weeks, Belgian company Kamp C 3D printed its namesake demo house in one piece, at the property location. Developers claim that the building holds a compressive strength three times greater than conventional brick, which is largely credited to a special printer supplied by COBOD, a 3D-printing construction company. Smooth surfaces and thick layers fortify the trial model. Unlike other projects at the time — and even now — this house features two stories and was constructed in one piece. It’s just under 27 feet tall, about the size of a residential telephone pole, and spans 967 square feet. Its sustainable design uses low-energy floor and ceiling heating, sourced from solar panels and a heat pump.
An error occurred.
Mense-Korte is the first 3D-printed house to pass the building regulations of a national government. | Video: The B1M
Mense-Korte
Mense-Korte’s 3D-printed house, located in Beckum, Germany, is the first in the world to become fully certified by a national government’s building regulation. This modernist, three-bedroom, three-bathroom home measures 1,722 square feet of living space, complete with a sophisticated interior and smart-home technology. Fortified by multi-shell walls casted with in-situ concrete, the curvy structure took nearly eight months to build, including 100 hours of active printing time. Amenities like a fireplace, bathtubs and a balcony are integral to the design, with spaces specifically molded for second-fix installations.
More on 3D Printing Utility 5 3D Printing Applications in Construction
An error occurred.
The Quatro residences are built to consume as much energy as they generate. | Video: Mighty Buildings
Mighty House Quatro
Nestled away in a gated, hilltop community in southern California, Ehrlich Yanai Rhee Chaney Architects have built a 20-home, net-zero development that aims to consume as much energy as it generates. Constructed in around four months, each home includes two bedrooms and two bathrooms across a 1,171-square-foot space built on top of a hot spring aquifer. Fitted in a modern, minimal aesthetic, these properties include a swimming pool, hot tub, fire pit and floor-to-ceiling windows. The project collaborator, construction company Mighty Buildings, models its manufacturing process after the automotive industry. Operating highly scalable micro-factories, its 3D-printing methods perform at twice the speed of traditional construction, and, as an additive manufacturer, its projects generate 99 percent less waste, according to the company’s website. Mighty Buildings has also developed a proprietary light stone material that cures into a stone-like composite with four times the tensile and flexural strength of concrete materials currently in common practice of architectural 3D printing.
An error occurred.
Project Milestone was printed in five days and 24 separate parts. | Video: Real Estate & Interior Design
Project Milestone
Project Milestone — which consists of five 3D-printed concrete dwellings — was the world’s first commercial housing project in its medium, with full intent to legally house residents. The first of these 1,011-square-foot dwellings was printed in 120 hours on-site as 24 separate parts. Matching their backdrop of Eindhoven, a techy city in the Netherlands known for its cutting-edge design, Project Milestone houses resemble elongated boulders with smooth, rounded edges. With extra-thick insulation and a connection to the heat grid, these structures score high marks in energy efficiency, according to online media platform 3D Natives. Its first tenants, Dutch couple Elize Lutz and Harrie Dekkers, received their key on April 30, 2021.
An error occurred.
Sourced from local clay, Tecla serves as a proof of concept for sustainable architecture. | Video: WASP Team
Tecla
In development with 3D-printing firm WASP, Italy-based studio Mario Cucinella Architects set out to create bioclimatic, low-carbon proof-of-concept housing in response to escalating climate emergencies and housing crises worldwide. Standing out from the crowd, Tecla’s tan, double-dome structure is constructed out of 350 layers of locally sourced clay from a nearby riverbed. A portmanteau of “technology” and “clay,” Tecla is a 538-square-foot structure that stands at about 15 feet tall and features two skylights. The eco-habitat is made entirely out of organic, bio-materials. Of the 200 hours it took to fully construct the project, the active printing time lasted 72 hours.
How much does a 3D-printed house cost?
3D-printed houses cost about $10,000 to $400,000 on average, but pricing can vary based on the house’s location, size, amenities and materials used.
How long does it take to 3D print a house?
To 3D print a house, it may take about 24 hours to three weeks, excluding time for second-fix installations or material transportation if pieces are not printed at the final house location.
Where can I buy a 3D-printed house?
Some real estate marketplaces like Zillow, or some homeownership assistance programs like Habitat for Humanity, can sell 3D-printed houses.