First low CO2 3D printed building in Copenhagen
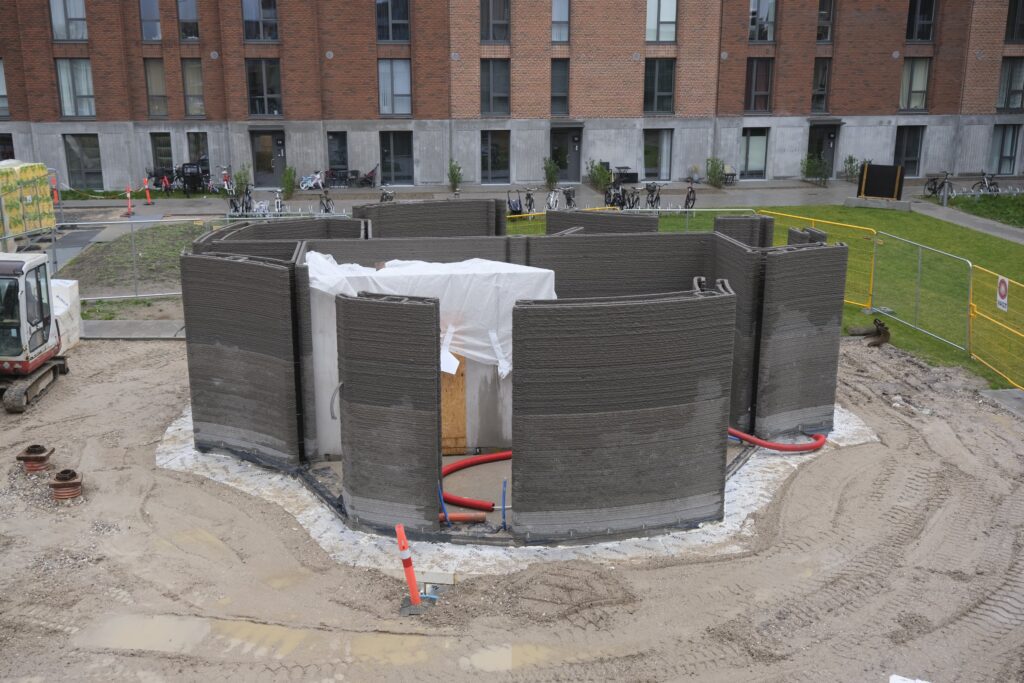
First low CO2 concrete building 3D printed in Copenhagen made by 3DCP Group – a 72 m2 (775 SF) community building. A couple of weeks ago AKF, the large Danish real estate developer, in partnership with Danish 3DCP Group, 3D printed a community building in greater Copenhagen area measuring 72 m2 (775 SF). The building will […]
First 3D Printed Net Zero Energy Home Made in Los Angeles
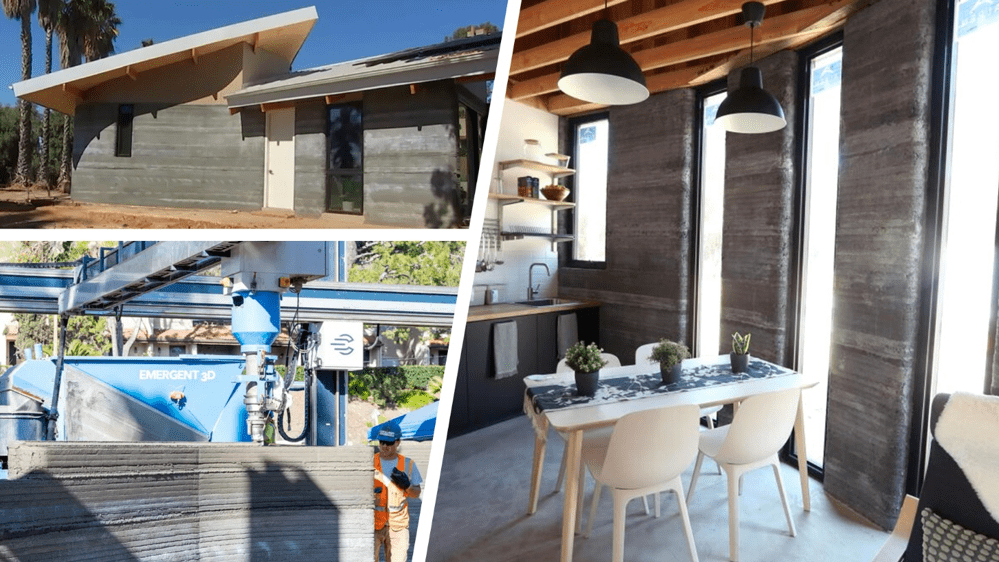
LA’s first 3D printed net zero house completed by Woodbury university students in collaboration with Emergent. Architecture Students from Woodbury University completed Los Angeles’ first fully permitted 3D printed net zero energy house. The house was part of a nationwide collegiate contest by the US Department of Energy. The walls of the 425 square-foot (40 m2) house, […]
3D-printing: How to build sustainable housing for three billion
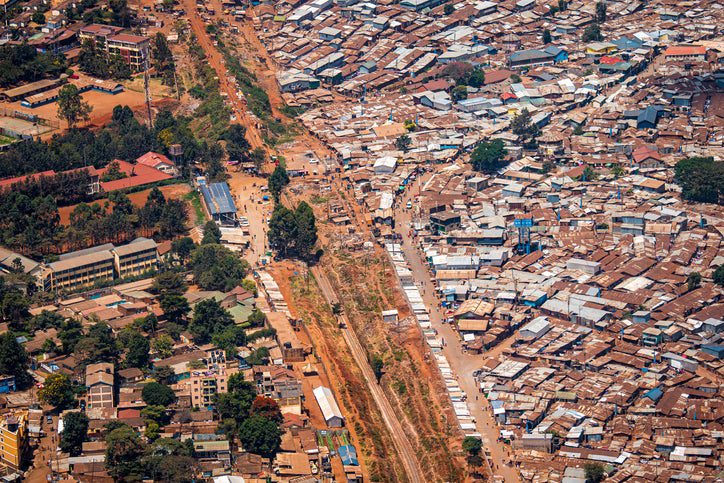
An aerial shot of the Kibera slum, Africa’s largest slum, in the heart of Nairobi. Credit: Stock image via Getty Images. There is a global sustainable housing crisis. Not only is the built environment –including construction and energy use – responsible for around 40% of annual greenhouse gas emissions, but there are billions of people […]
3D-printed, organic formations by external reference engulf la manso store in barcelona
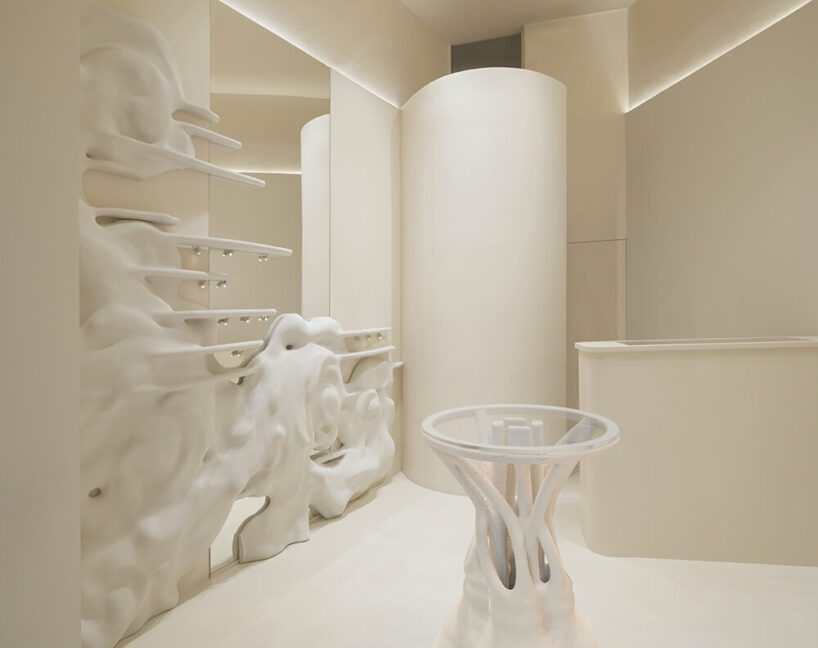
inside la manso store by external reference in barcelonaSpanish architecture studio External Reference has been commissioned to design the first flagship store for La Manso, a contemporary costume jewelry brand, in the heart of Barcelona‘s Eixample district. The 25 sqm boutique is located just a few meters away from the house where Adriana Manso, the brand’s young founder, was born. Turning plastic pieces into a form of luxury, La Manso aims to usher in a new era, bringing it closer to the world of haute couture with unique and iconic designs. Following this vision, External Reference’s Carmelo Zappulla combines the floral elements of the store’s impressive modernist facade with the contemporary plasticity of the brand’s products to create captivating 3D-printed displays, reinterpreting classic decorations with a careful mix of craftsmanship, design, and technology.image courtesy External ReferenceLaMáquina’s 3d-printed displays echo plasticity & floral motifsThrough 3D-printed pieces exclusively designed by LaMáquina, Carmelo Zappulla (see more here) envisions the store‘s interior as an extension of the building exterior. Organic forms take center stage, turning the facade’s ornaments into large rosettes with futuristic glitches and bas-reliefs arranged at different heights, ranging from 90 centimeters to 1.70 meter. These elements exhibit La Manso’s jewelry and accessories around a small center table, carefully illuminated by adjustable mini-spotlights. Using mirrored surfaces, the space expands, while a neutral and elegant coating establishes an abstract backdrop for the iconic pieces. As part of the exhibition, the jewelry is illuminated to highlight the uniqueness of each piece, creating an intimate and deliberate atmosphere that invites exploration and the discovery of the perfect item.In addition, the store hosts a small showcase that, following the owner’s wishes, recovers the style of mythical jewelry stores, inviting passersby to glimpse at the objects in total freedom from the street. image courtesy External Referencemerging indoors and outdoors, physical and digitalExternal Reference’s conceptual design for La Manso extends to the street by repeating, mirroring, and reinterpreting the brand’s logo, infusing it with three-dimensional elements present within the interior’s creative language. In the detail of the sign, strategically placed under the corner bow window that embraces the surrounding streets with its decorations, a coherent visual connection is established between the retail store and urban environment. External Reference, as in its long history of exploring new 3D printing technologies applied to design and architecture, has relied on the experience of LaMáquina to create the store’s custom-made furniture. ‘The purpose is to build a captivating and immersive brand experience that invites users to transcend the digital realm and immerse themselves in a physical space where they can personally contemplate each piece,’ reflects the studio. image © Anna Mas | @annamas_photoimage courtesy External Referenceimage courtesy External Referenceimage © Anna Mas
Crafting waves: The poetic façade of Studio RAP’s 3D printed ‘Ceramic House’
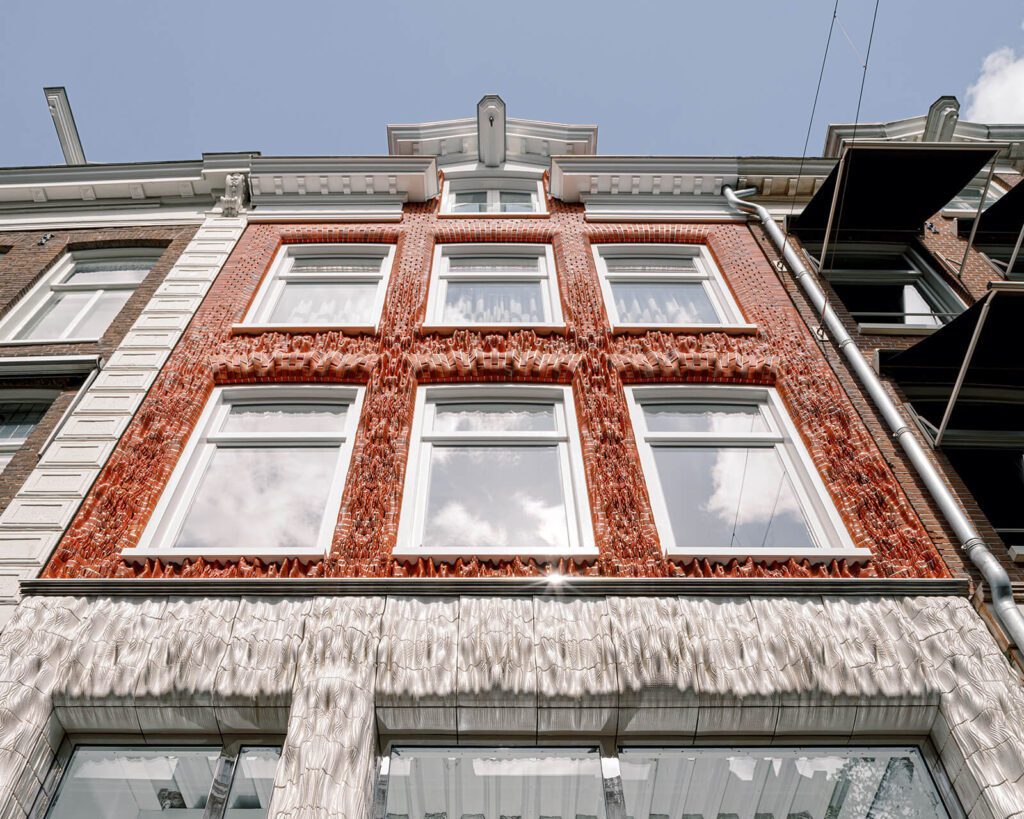
Elegant creases, interlooping yarns and stitch patterns; these are not just elements of a finely crafted garment but the poetic design language of Dutch design practice, the Studio RAP’s Ceramic House. In the world of architecture, the façade is the face of the building. Nestled in the heart of Amsterdam’s P.C. Hoofstraat, this boutique design transcends conventional norms and becomes a canvas, creating an organic, wave-like poetry. Far beyond a static exterior, this façade is a living testament to the delicate dance of form and function. It seamlessly blends tradition with innovation, not merely as a visual spectacle but as a tactile and immersive experience, inviting onlookers into a world where architecture becomes an art form.
Studio RAP takes inspiration from knitwear to redefine Amsterdam’s shopping street Image: Riccardo De Vecchi
In the genesis of the Ceramic House, the studio received a concise yet ambitious design brief from a client renowned for iconic architectural creations. Tasked with adorning Amsterdam’s shopping street with a unique boutique façade, the challenge was clear: conceive a retail design that transcends the ordinary. To meet this, the studio delved into the unexplored, seeking inspiration not from conventional architectural norms but from the world of knitwear.
When 3D printing meets knitwear inspiration, the artistic journey of the Ceramic House Image: Riccardo De Vecchi
The studio was in the midst of experimenting with 3D printing ceramic tiles for a previous project, New Delft Blue, when the idea of a façade entirely clad in 3D-printed ceramic tiles took shape. The result was the Ceramic House, an architectural masterpiece inspired by the artistry of knitting.
The Ceramic House harmoniously integrates with Amsterdam’s historic tapestry Image: Riccardo De Vecchi
Amsterdam, with its cobbled stone streets and historic canals, is an architectural tapestry that weaves together the past and the present. Amidst this, the house stands as a distinct thread, weaving its own narrative. The key to the success of this project lies in its harmonious integration with the surroundings. Studio RAP meticulously replicated the silhouette of the original façade, maintaining the tripartite structure of the street. Expressive at ground level, the façade transforms as it ascends, synchronising with the surrounding structures. Architectural elements like rowlock arches and cross-bond brickwork echo the neighbouring buildings but with a contemporary twist. The connection of flushes between the new and adjacent facades, achieved through 3D scanning, showcases a commitment to precision, ensuring that the house stands as a luxury boutique seamlessly blending with its historical environment.
Textile-inspired layers come to life at the Ceramic House Image: Courtesy of Studio RAP
The Ceramic House redefines architecture with algorithmic artistry Image: Courtesy of Studio RAP
Digital design algorithms, a language of their own, become the brushes in Studio RAP’s hands. The Ceramic House explores the reinterpretation of glazed ceramics, infusing the historical city of Amsterdam with a new design vocabulary. The scale, size, type, and colour of the ornaments and materials are all carefully synced with the neighbouring buildings to allow a seamless integration of traditional and contemporary architecture. The façade’s intricate layers, inspired by textiles, mimic the elegance of creases and stitch patterns. An organic, wave-like quality unfolds as viewers approach, unveiling new elements within the bespoke 3D-printed ceramic tiles. This is not just architecture, it is a symphony of algorithmic design and historical resonance.
Studio RAP pushes boundaries with 3D printing and a collaboration with robotic precision Image: Courtesy of Studio RAP
With inspiration drawn from the rich ceramic collection of the Rijksmuseum, the national museum of The Netherlands, the studio pioneers large-scale 3D printing technology. This isn’t merely printing tiles; it is an art form where architects collaborate seamlessly with advanced robotic systems. The result is highly differentiated and algorithmically designed details, showcasing a commitment to pushing the boundaries of architectural design.
The studio’s narrative of 3D printing, tradition and artistic expression Image: Courtesy of Studio RAP
The significance of using these innovative technologies lies in the studio’s vision to enrich the world with a new architectural language. Breaking barriers, they utilise 3D printing to gain unprecedented control over design, expression and precision. It is not just about industry digitisation; it is about preserving the cherished qualities of artisanal craftsmanship. Collaborating with Royal Tichelaar, one of the oldest companies in The Netherlands for ceramics and glazes, adds a touch of tradition to this technological partnership.
The Ceramic House welcomes with 3D-printed ceramic tiles and a blend of form and function Image: Courtesy of Studio RAP
Laser-cut stainless-steel cassettes frame abstract ornamentation, a modern twist on tradition Image: Courtesy of Studio RAP
At street level, the house beckons with large 3D-printed ceramic tiles glazed in pearl white, subtly touched with yellow by Royal Tichelaar. Visually expressive at eye level, these tiles transition gracefully to a flush alignment with the ground, creating a harmonious aesthetic. Ascending higher, the façade unfolds another layer, showcasing 3D-printed bricks glazed in three shades of red. The abstract ornamentation dances with the original masonry cross bond, housed within the laser-cut stainless-steel cassettes, a nod to historical flushes.
The ‘pearl-stitch’ speaks a language of tradition and avant-garde sophistication Image: Courtesy of Studio RAP
For Studio RAP, 3D printing and algorithmic design aren’t just tools; they are the essence of the Ceramic House’s identity. Drawing inspiration from the art of knitwear, these strategies amplify the intricate layers of the façade design. There is a fascinating parallel between traditional knitting patterns and the tiles; both following conceptual instructions. The result is what the studio calls the “pearl-stitch”, a unique architectural expression merging historical ceramics with the allure of knitwear-inspired details. It is not just a building, it is a conversation between traditional architecture and the avant-garde.
The Ceramic House is an invitation to explore architectural intricacies Image: Courtesy of Studio RAP
As visitors approach the Ceramic House, a layered experience unfolds. From a distance, it seamlessly blends with the legacy of the street. Come closer, the undulating façade sparks curiosity, and the pearl stitch pattern emerges. Opening the door is an invitation to feel the texture, a tactile exploration of bespoke details. Each unique tile ensures that every visit unveils a new detail, creating a timeless and layered experience. It is not just a façade; it is an immersive journey through layers of innovation and tradition.
Ceramic House reflects Studio RAP’s transformative role in design Image: Courtesy of Studio RAP
The Ceramic House isn’t an isolated project; it is a concrete manifestation of Studio RAP’s broader vision. Situated in Rotterdam, the team redefines the traditional role of architects. They aren’t just architects, they are entrepreneurs, craftsmen and innovators. The studio challenges conventions, injecting greater excitement and diversity into the world through innovative design.
Studio RAP’s Ceramic House project is a blend of tradition and excitement Image: Courtesy of Studio RAP
In the words of the studio, “The Ceramic House project reshapes architectural expression by seamlessly blending tradition and innovation, reintroducing bespoke details to architecture. It’s more reshaping; it’s a revolution that challenges the status quo and presents a fresh architectural style. The project is a testament to the Studio RAP’s commitment to infuse the world with greater excitement and diversity through architectural innovation.”
Studio RAP shapes the future of architecture with a hands-on, innovative approach Image: Riccardo De Vecchi
Studio RAP isn’t just an architectural design company; it is a harbinger of change, challenging conventional ways of building. With architects, designers, roboticists, programmers and researchers collaborating in an industrial atmosphere surrounded by robots in Rotterdam, the studio embarks on a hands-on approach to solving problems in the building industry. Studio RAP doesn’t just create expressive buildings, it reimagines the entire architectural profession, embracing innovation as the cornerstone of its practice.
Studio RAP’s ceramic house sparks curiosity in the possibilities of façade design Image: Riccardo De Vecchi
The Ceramic House stands not just as a building but as a testament to the marriage of tradition and innovation. As we trace the undulating façade and feel the tactile allure of each bespoke tile, we are invited into a realm where architecture becomes an immersive journey. Beyond its physical form, the house embodies a question: What other uncharted territories can façade design explore? Studio RAP’s revolution extends beyond a single, prompting us to ponder the possibilities that lie ahead in the dynamic tapestry of architectural innovation.
[embedded content]
Feel the texture, experience the details; the Ceramic House invites you on an immersive journey through the intersection of tradition and the avant-garde Video: Oculus Film
Project Details
Name: Ceramic House Location: P.C. Hooftstraat, Amsterdam (NL) Client: Warenar Real Estate Architect: Studio RAP Co-Architect: Gietermans & Van Dijk Contractor facade cladding / 3d-ceramic-printing: Studio RAP Firing and glazing: Royal Tichelaar Main contractor: Wessels Zeist (VolkerWessels) Film: Oculus Film
These 3D-printed homes take just 4 days to build — here’s how they could solve one state’s massive housing shortage
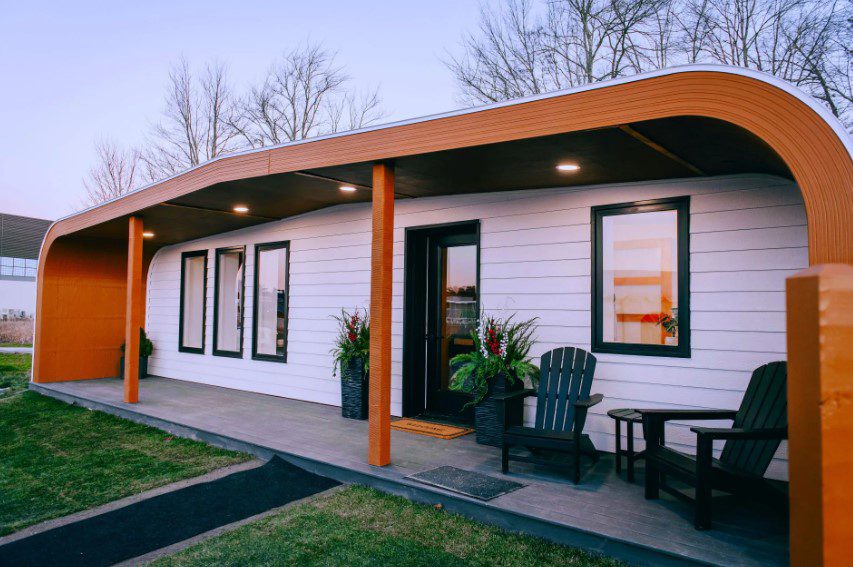
A recyclable 3D-printed home made from natural materials has been revealed to the public, and this may only be the beginning.
The design is part of a project to create a “factory of the future” for sustainable, eco-friendly home development by way of 3D printing technology. The 600-square-foot home, composed of wood fibers and sawmill waste, known as bio-resins, was the creation of researchers from the University of Maine.
This new type of home is a breakthrough considering how current 3D technology used to build homes often requires materials that create lots of carbon pollution when produced, like the concrete needed to build the walls. The new homes do not use concrete, instead using wood components, except for the foundation.
The first fully 3D-printed house was displayed to the public in Beckum, Germany, in 2021. According to an article from Inhabitat, Janet Mills, the governor of Maine, said homes like the newly printed one could be a solution to Maine’s housing shortage of 20,000 units.
Traditional construction generates 27% of planet-warming gases globally. 3D-printed houses produce much less waste than conventional construction since builders only need to print exactly what they need, and minimal space is needed for storage materials.
Also, there is no need for energy consumption that is normally required to move the same parts from one place to another.
#cool_newsletter_53e74c5a-ee3d-46f7-9b1c-f120b3daa4ca .cool_newsletter__inner span{color:#000000}
JOIN OUR NEWSLETTER
Good news, green hacks, and the latest cool clean tech — straight to your inbox every week!
Companies in the building technology space are catching wind of this shift. Mighty Buildings, a 3D printing construction company from California, has partnered with Fortera, a materials technology company that produces eco-friendly cement.
Four billion tons of cement are produced each year, contributing 8% of global carbon emissions. Fortera’s eco-friendly cement reduces harmful carbon pollution by 60% compared to traditional cement.
Aside from being much more environmentally sustainable, creating 3D-printed houses may also become more cost-effective sooner than later. According to German architect Waldemar Korte, this homebuilding method of the future may become cheaper than traditional methods within the next five years.
“We are much faster at building,” Korte said to Deutsche Welle. Korte’s 3D-printed home was built in four days. “We need fewer people, and that helps when you have a dearth of skilled people in the industry.”
According to UN-Habitat, as many as three billion people will be in need of better housing by the end of this decade. 3D printing technology for building houses can help solve this issue in an efficient and environmentally sustainable manner.
The world’s first 3D-printed neighborhood has already been created in Mexico. Meanwhile, a 2021 report stated that the global 3D construction market will grow by 91% between 2021 and 2028.
Considering recent advances in artificial intelligence, the next 3D-printed homes may be getting propped up sooner than many of us would have expected.
Join our free newsletter for weekly updates on the coolest innovations improving our lives and saving our planet.
Cool Picks
SAGA builds the largest 3D-printed circular-shaped house in Scandinavia
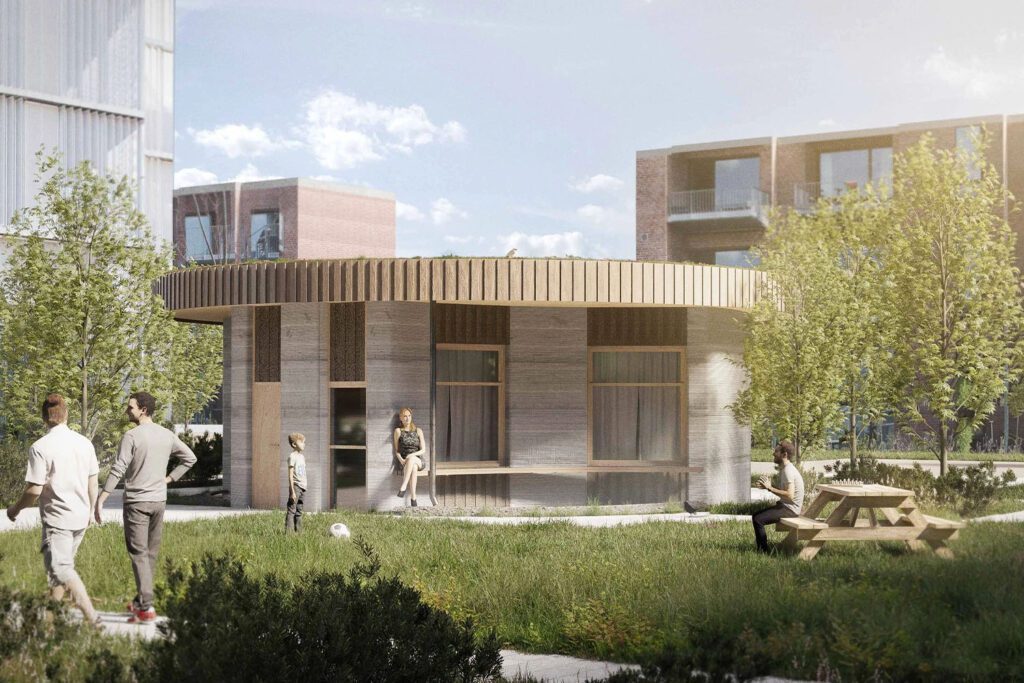
This website uses cookies so that we can provide you with the best user experience possible. Cookie information is stored in your browser and performs functions such as recognising you when you return to our website and helping our team to understand which sections of the website you find most interesting and useful.
9 Examples of 3D-Printed Houses
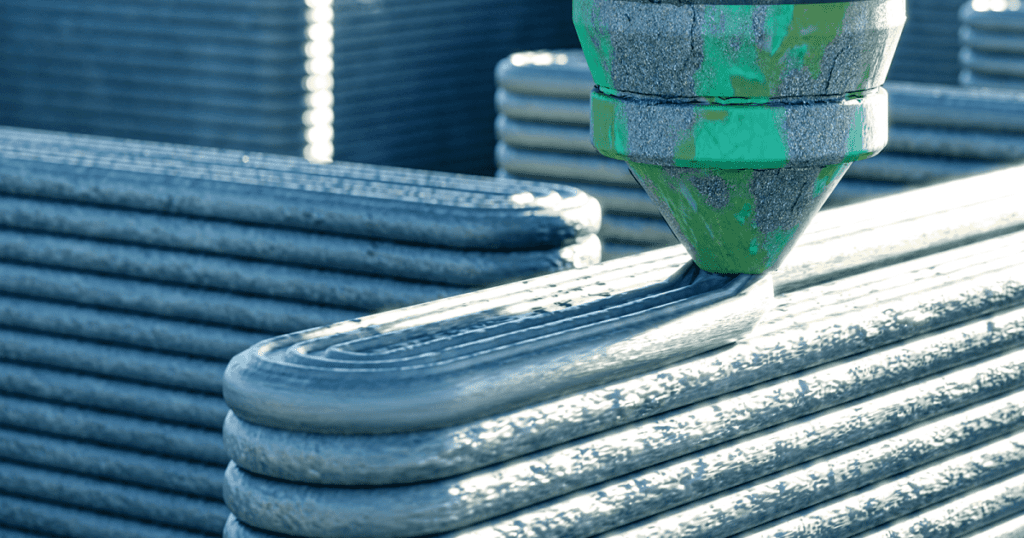
It’s a rare occasion when something debunks the “too good to be true” principle, such as 3D printing an entire house in less than 24 hours. And yet, here we are.What Are 3D-Printed Houses?Three-dimensional-printed houses are structures that are built layer by layer using an industrial-grade, 3D-printing technology. This method of additive manufacturing is also known as construction 3D printing.As tenants move into 3D-printed houses in the first years of their commercial listing debut, 3D printing is on a 23 percent compound annual growth rate over the decade to come, according to Grand View Research. These dwellings — often sharing a gray, shapely appearance with a ribbed texture — are even piquing the interest of NASA, which funded a $57 million project to develop tech for moonside 3D-printed infrastructure.Highly customizable and free of form, construction 3D printing is a new-age tech on the verge of market disruption, holding the potential to mass produce housing.What Are 3D-Printed Houses?Three-dimensional-printed houses are life-size dwellings that use 3D printing as its primary means of construction. With minimal human oversight, these highly customizable structures can be built on-site or off-site within a matter of hours at a fraction of the cost.Typically, 3D-printed houses feature free-form, curvilinear shapes made out of a cement mix. Projects span from inhabitable beta prototypes under study to move-in-ready affordable housing and even high-end luxury homes.Aside from time and money, several other reasons explain additive manufacturing’s disruption to the construction market. Many see this type of low-waste, computerized homebuilding delivered from an industrial-scale printer as a way to shelter unhoused communities and a gateway to sustainable, biodegradable housing solutions.How Are 3D-Printed Houses Built?Industrial-sized 3D printers build entire multi-unit housing developments one tiny layer at a time. This repetitive process puts the “additive” in “additive manufacturing.”Following a digital blueprint, a 3D printer will dispense a paste-like mixture. This will consist of choice ingredients — often a cement blend — but can range from sand and special polymers to bio-resins, like soil, clay or wood flour, which is a fine sawdust mixed with a corn-based binder.How Long Does It Take To 3D Print a House?Nowadays, industrial-sized 3D printers have made it possible to print an entire house in less than 24 hours.Keep in mind that a project’s “printing time” may exclude time for any second-fix installations or construction time necessary to piece together a project printed on-site and transported to its final location.And if you’re trying to build something of scale, like a house, the 3D printer itself has to outsize it. Made out of a steel, quad-truss framework — the kind you’d see as part of a concert stage — these industrial-grade 3D printers form a sort of hollow cube. On top, a robotic arm zips along a track, following pre-programmed instructions being read from the blueprint.Much like your desk-side inkjet printer, the mixture is then heated during a thermal extraction process. The paste squeezes through a nozzle, bringing the digital rendering into physical form. Before the next layer is applied, the mixture is solidified by a concrete dryer. This process repeats until all uploaded building elements are complete.It’s important to note that additive construction work sites are not entirely autonomous. Aside from the setup and breakdown of the equipment, human oversight is necessary to ensure there are no technical hiccups. Specialists must be on-site to cut holes for second-fix installments, such as plumbing, electrical wiring, doors and windows.How Much Does a 3D-Printed House Cost?Of course, this number will vary from project to project, and face further price contingencies based on the hired companies and materials used (let alone geographic location, size, amenities, design complexity, and so on). With that being said, developers stateside and abroad report average cost savings of 30 percent.Three-dimensional-printed houses first hit the U.S. market at the start of 2021. The 1,407-square-foot house — complete with three bedrooms, two baths and a two-car garage in Riverhead, New York — listed as “the world’s first 3D-printed home for sale” for $299,999 on Zillow.com.ICON, a 3D-printing construction company, said it could produce a 600 to 800-square-foot, economy-sized building for as low as $4,000 in 24 hours, as reported by Business Insider.Models on the more affluent side of the market can surpass $1 million. Known as House Zero, the mid-century, ranch-style luxury home is a 2,000-square-foot property with a 350-square-foot accessory dwelling unit. Just based on size and location, Zillow estimated the price of this four bedroom, three-and-a-half bath estate at $723,000 to $908,000, according to online specialty magazine All3DP. However, its one-of-a-kind, exceptional design may push it into the seven-digit price range.When Will 3D-Printed Houses Become Available?Examples of 3D-Printed Houses[embedded content]An error occurred.Unable to execute JavaScript. Try watching this video on www.youtube.com, or enable JavaScript if it is disabled in your browser.BioHome3D is a 3D-printed house constructed out of 100 percent bio-based materials. | Video: 3DPrint.comBioHome3DThe University of Maine Advanced Structures and Composites Center is 3D-printing housing structures exclusively from bio-resins and wood fibers to combat labor shortages and widen access to affordable housing. The demo project, known as BioHome3D, begins with a 600-square-foot prototype that features a fully 3D-printed floor and roof. As a whole, the one-bedroom, one-bathroom building is 100-percent recyclable, made up entirely of biodegradable materials, including wood flour. As a prototype, BioHome3D is equipped with monitoring sensors, measuring thermal, environmental and structural elements, to gather resilience-based data to better inform future designs.[embedded content]An error occurred.Unable to execute JavaScript. Try watching this video on www.youtube.com, or enable JavaScript if it is disabled in your browser.All East 17th Street Residences feature minimal architectural aesthetics. | Video: FindYourDENEast 17th Street ResidencesThese four Austin, Texas properties by construction 3D-printing company ICON feature open-floor plans, minimal architectural aesthetics and private yards. Varying in size, these residences feature two to four bedrooms and range from 1,000 to 2,000-square-foot homes. Each ground floor level is built with a proprietary cement-based material, dubbed “Lavacrete,” to last longer than traditional construction materials, according to the company’s website. The second story incorporates old-school methods, and is constructed out of black metal cladding and rich-colored timber. They share a color palette of green, white and terracotta and have all been sold.[embedded content]An error occurred.Unable to execute JavaScript. Try watching this video on www.youtube.com, or enable JavaScript if it is disabled in your browser.Mikkel Brich, CEO and founder of 3DCP, talks about the future of 3D-printed construction. | Video: COBODHouse 1.0With the help of 3D-printing construction manufacturer COBOD, Danish startup 3DCP Group constructed Europe’s first 3D-printed tiny house last year in just five weeks; however, the structure itself printed in just 22 hours. Located in Hostelbro, Denmark, this 398-square-foot structure is composed of three sections that merge at an open, triangular-shaped core. Inspired by the no-frills aspect of student living, the space is economically laid out and contains all the necessary amenities — a bathroom, open-plan kitchen, living room and loft-style bedroom on a raised level. Sebastian Aristotelis, architect at Saga Space Architects who designed House 1.0, said that the project was built at the lowest possible cost, with developers opting for inexpensive materials, like concrete, and constructing the project using a low-to-no waste approach.More on 3D Printing 25 3D-Printing Companies to Know[embedded content]An error occurred.Unable to execute JavaScript. Try watching this video on www.youtube.com, or enable JavaScript if it is disabled in your browser.Watch 3D-printing construction company ICON build House Zero, a luxury 3D-printed house. | Video: ICONHouse ZeroICON teamed with architectural firm Lake|Flato to build a three-bedroom, two-and-a-half bath residence just outside of downtown Austin, Texas. Its curved walls and rounded corners are insulated with Lavacrete and reinforced with steel. Paired with a one-bedroom, one-bath accessory dwelling unit, ICON’s website styles the 2,350-square-foot property — which printed in under two weeks — as a “mid-century modernist ranch house aesthetics.” Given its design to consume net-zero energy, Time named House Zero to its Best Inventions of 2022 list. In the months since, ICON has broken ground on a 100-home project, projected to be the largest 3D-printed residential community in the United States.[embedded content]An error occurred.Unable to execute JavaScript. Try watching this video on www.youtube.com, or enable JavaScript if it is disabled in your browser.Kamp C was built in one piece. | Video: Kamp CKamp CIn just three weeks, Belgian company Kamp C 3D printed its namesake demo house in one piece, at the property location. Developers claim that the building holds a compressive strength three times greater than conventional brick, which is largely credited to a special printer supplied by COBOD, a 3D-printing construction company. Smooth surfaces and thick layers fortify the trial model. Unlike other projects at the time — and even now — this house features two stories and was constructed in one piece. It’s just under 27 feet tall, about the size of a residential telephone pole, and spans 967 square feet. Its sustainable design uses low-energy floor and ceiling heating, sourced from solar panels and a heat pump.[embedded content]An error occurred.Unable to execute JavaScript. Try watching this video on www.youtube.com, or enable JavaScript if it is disabled in your browser.Mense-Korte is the first 3D-printed house to pass the building regulations of a national government. | Video: The B1MMense-KorteMense-Korte’s 3D-printed house, located in Beckum, Germany, is the first in the world to become fully certified by a national government’s building regulation. This modernist, three-bedroom, three-bathroom home measures 1,722 square feet of living space, complete with a sophisticated interior and smart-home technology. Fortified by multi-shell walls casted with in-situ concrete, the curvy structure took nearly eight months to build, including 100 hours of active printing time. Amenities like a fireplace, bathtubs and a balcony are integral to the design, with spaces specifically molded for second-fix installations.More on 3D Printing Utility 5 3D Printing Applications in Construction[embedded content]An error occurred.Unable to execute JavaScript. Try watching this video on www.youtube.com, or enable JavaScript if it is disabled in your browser.The Quatro residences are built to consume as much energy as they generate. | Video: Mighty BuildingsMighty House QuatroNestled away in a gated, hilltop community in southern California, Ehrlich Yanai Rhee Chaney Architects have built a 20-home, net-zero development that aims to consume as much energy as it generates. Constructed in around four months, each home includes two bedrooms and two bathrooms across a 1,171-square-foot space built on top of a hot spring aquifer. Fitted in a modern, minimal aesthetic, these properties include a swimming pool, hot tub, fire pit and floor-to-ceiling windows. The project collaborator, construction company Mighty Buildings, models its manufacturing process after the automotive industry. Operating highly scalable micro-factories, its 3D-printing methods perform at twice the speed of traditional construction, and, as an additive manufacturer, its projects generate 99 percent less waste, according to the company’s website. Mighty Buildings has also developed a proprietary light stone material that cures into a stone-like composite with four times the tensile and flexural strength of concrete materials currently in common practice of architectural 3D printing.[embedded content]An error occurred.Unable to execute JavaScript. Try watching this video on www.youtube.com, or enable JavaScript if it is disabled in your browser.Project Milestone was printed in five days and 24 separate parts. | Video: Real Estate & Interior Design Project MilestoneProject Milestone — which consists of five 3D-printed concrete dwellings — was the world’s first commercial housing project in its medium, with full intent to legally house residents. The first of these 1,011-square-foot dwellings was printed in 120 hours on-site as 24 separate parts. Matching their backdrop of Eindhoven, a techy city in the Netherlands known for its cutting-edge design, Project Milestone houses resemble elongated boulders with smooth, rounded edges. With extra-thick insulation and a connection to the heat grid, these structures score high marks in energy efficiency, according to online media platform 3D Natives. Its first tenants, Dutch couple Elize Lutz and Harrie Dekkers, received their key on April 30, 2021.[embedded content]An error occurred.Unable to execute JavaScript. Try watching this video on www.youtube.com, or enable JavaScript if it is disabled in your browser.Sourced from local clay, Tecla serves as a proof of concept for sustainable architecture. | Video: WASP TeamTeclaIn development with 3D-printing firm WASP, Italy-based studio Mario Cucinella Architects set out to create bioclimatic, low-carbon proof-of-concept housing in response to escalating climate emergencies and housing crises worldwide. Standing out from the crowd, Tecla’s tan, double-dome structure is constructed out of 350 layers of locally sourced clay from a nearby riverbed. A portmanteau of “technology” and “clay,” Tecla is a 538-square-foot structure that stands at about 15 feet tall and features two skylights. The eco-habitat is made entirely out of organic, bio-materials. Of the 200 hours it took to fully construct the project, the active printing time lasted 72 hours.How much does a 3D-printed house cost?3D-printed houses cost about $10,000 to $400,000 on average, but pricing can vary based on the house’s location, size, amenities and materials used.How long does it take to 3D print a house?To 3D print a house, it may take about 24 hours to three weeks, excluding time for second-fix installations or material transportation if pieces are not printed at the final house location.Where can I buy a 3D-printed house?Some real estate marketplaces like Zillow, or some homeownership assistance programs like Habitat for Humanity, can sell 3D-printed houses.