World’s First 3D Printed Living Seawall gets installed
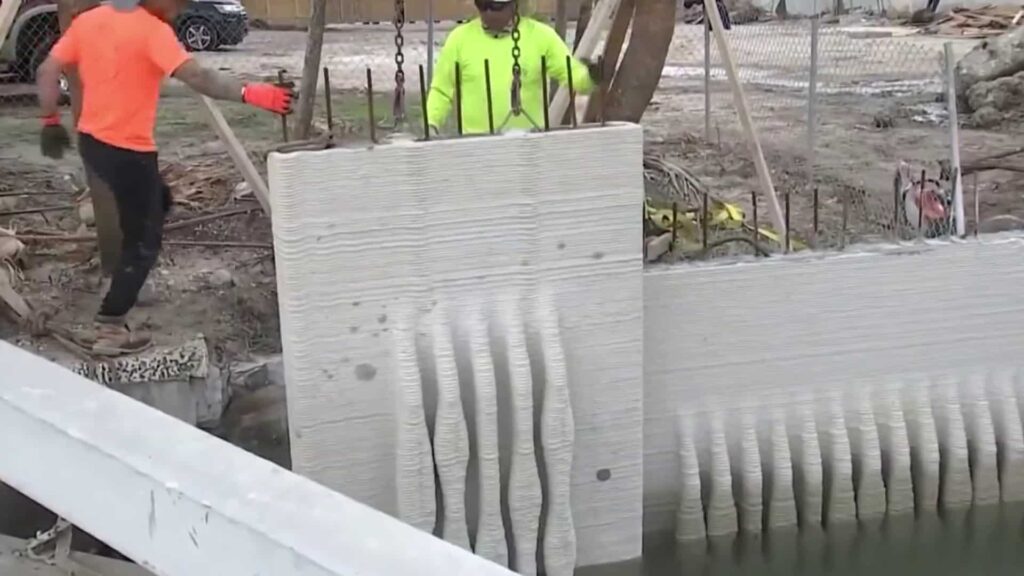
A future homeowner in Miami Beach has become the first to have Kind Designs’ Living Seawalls installed. Opting for this structure specifically to support the environment, they are the recipient of the world’s first 3D printed seawalls. While seawalls to prevent flooding are necessary along the Miami coastline, these Living Seawalls go a step further in environmental protection. In addition to safeguarding the land from erosion, flooding, storm surges, and sea-level rise, Kind Designs‘ Living Seawalls actively contribute to improving the local marine environment. Once installed along the shoreline, the Living Seawalls seamlessly support the needs of local marine ecosystems. Moreover, in addition to enhancing the sea, the seawalls also monitor its quality. Embedded sensors enable the Living Seawalls to measure information on water quality across as many as 15 different parameters.
The Best Eco Homes On The Market Right Now
Solar-powered swimming pools? Air-source heat pumps? Wildflowers on the roof? You name it, these homes have got it. If you’re searching for a luxurious contemporary property with an eco-friendly twist, look no further: these are best eco homes on the market. The Best Eco Homes on the Market Right Now Hollow Way Lane, Amersham This […]
Printing Swedish houses with algae
For the first time, a new material made from tiny cellulose fibers and algae has been tried as a more environmentally friendly option for construction.
Researchers from Chalmers University of Technology and the Wallenberg Wood Science Center in Sweden experimented with this sustainable material and found it can be used to create various architectural components using less energy than traditional methods.
The construction industry is a major contributor to global pollution, using half of the world’s fossil fuels, generating 40% of waste, and producing 39% of carbon dioxide emissions. To combat this, scientists are exploring biomaterials like nanocellulose, which is already used in biomedicine for its ability to be 3D printed into structures for tissue growth. This study marks the first attempt to use dried nanocellulose in architecture.
By mixing nanocellulose fibers with water and an algae-based substance called alginate, the researchers created a material that could be 3D printed. This blend provided flexibility to the material when it dried, enabling its use in architectural applications.
The use of 3D printing in architecture is seen as a resource-efficient method. Unlike traditional methods that produce waste, 3D printing requires fewer materials and less energy, particularly when using a robotic system that operates at room temperature. The properties of the nanocellulose hydrogel allow it to be easily printed and maintain its shape without requiring high temperatures.
The researchers tested various printing techniques to understand how the material behaves when dried in different shapes. These dried shapes could be used to create lightweight architectural elements such as room dividers, blinds, wall panels, and coatings for existing building components.
This study lays the groundwork for further exploration of nanocellulose in architectural design, highlighting the need for new approaches to incorporate biobased materials into buildings. Understanding the properties and design possibilities of these materials is crucial for creating sustainable and aesthetically pleasing structures that align with the goals of a circular economy.
Robotically 3D printed architectural membranes from ambient dried cellulose nanofibril-alginate hydrogel“, published in the journal Materials and Design.
#GreenBuilding #SustainableDesign #Nanocellulose #Architecture
Why this 3D-printed house could be a gamechanger
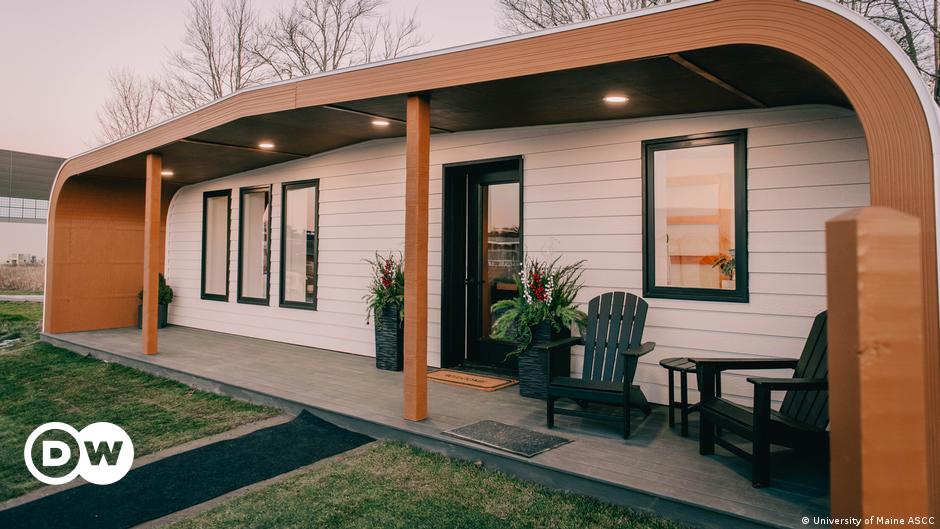
In this episode of Living Planet, we’re delving into a story about a remarkable 3D-printed house in the US state of Maine. It was made of 100% bio-based materials, which is good news for the construction sector, which accounted for nearly 40% of energy and cross-related CO2 emissions in 2021, according to the United Nation’s Environment Program.But this story is about much more than technology and innovation. Maine is one of the US states that has become a magnet for Americans searching for affordable houses in the wake of the pandemic. It’s also a state that’s seen its once booming paper industry dwindle to a handful of papermills, leaving a glut of sawdust from the timber industry with nowhere to go.
And as it turns out, a research team at the University of Maine was working on another project that turned out to be part of the solution to both of these problems.
In this episode, we speak with Mark Wiesendanger, director of development at MaineHousing; Habib Dagher, the executive director of the Advances Structures and Composites Center at the University of Maine; and Dr. Halil Tekinalp of the Department of Energy’s Oak Ridge National Laboratory.
You can read more about BioHome 3D here.
Press Release – Game-Changer in Additive Manufacturing: Mixed on Site Carbon Neutral Alternative to Cement Unveiled
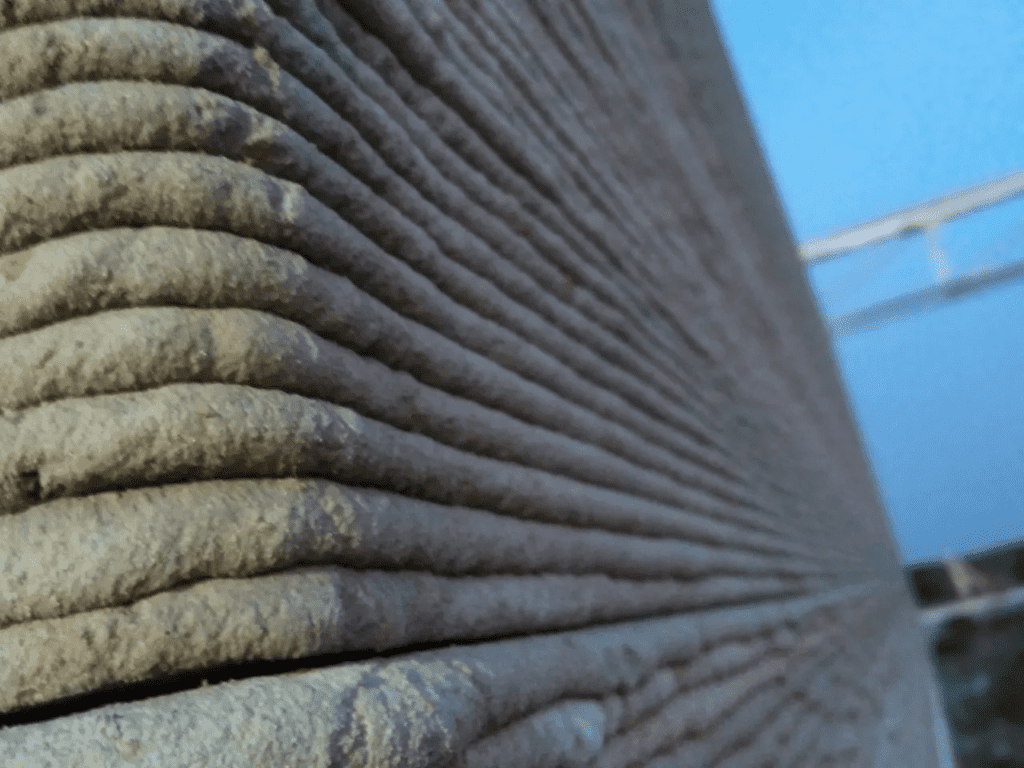
10/07/2023: Additive manufacturing company, Hive3D Builders, has developed a remarkable mixed on site carbon-neutral and stronger alternative to traditional cement. The printing material, which substitutes the mortar normally used in 3D concrete printing, is able to reduce construction’s CO2 emissions by 93%. Hive3D Builders is currently using this sustainable material to produce over 200 near-net-zero homes. This substance makes the already eco-friendly practice of additive manufacturing even more sustainable and is poised to revolutionize global construction.
Polluting Construction
The construction industry has long grappled with environmental challenges. Traditional concrete production contributes to 8% of global greenhouse gas emissions. 3D concrete printing technology generally has a lower carbon footprint than conventional building methods, mainly due to lower material usage, as well as a lower waste production rate. Along with the eco-friendly technology, additive manufacturing companies often strive to innovatively find sustainable solutions. An example of this is the manufacturer of Hive3D Builders’ printers, CyBe Construction. In the early days of 3D concrete printing, CyBe developed its own eco-friendly building material by using material that has up to 32% less CO2 emissions. Additionally, the material has the possibility to be produced locally.
Carbon-Neutral Material
Hive3D Builders (www.hive3dbuilders.com) take the production of eco-friendly building material one step further. By working with Eco Materials and Green Cement, they managed to develop a low-cost geopolymer cement replacement that has up to 93% less CO2 emissions. Due to geopolymer’s environmentally friendly properties, the substitute for the mortar that 3D concrete printing traditionally uses is almost completely carbon-neutral. Geopolymers have gained attention as a sustainable building material because they require less energy and produce fewer carbon dioxide emissions compared to traditional cement production. They can also utilize industrial waste materials such as fly ash, slag, and mining tailings, reducing the demand for natural resources and providing a solution for waste disposal. By combining this newfound material with the already eco-friendly properties of 3DCP, Hive3D Builders has unlocked tremendous potential for reducing carbon emissions in the building process. The current estimate is a reduction of 93% of the construction’s CO2 emissions. With this tremendous cut in greenhouse emissions, Hive3D Builders is at the forefront of sustainable construction technology.
Superior Strength
The implications of this innovation extend beyond its environmental benefits. Along with its reduction in CO2 emissions, the carbon-neutral material also offers superior strength and durability. This increased adhesion makes it an attractive alternative to traditional cement, offering immense potential for building more resilient structures. The strength of the material can be accredited to the geopolymer’s desirable properties. It is no wonder that geopolymers, oftentimes used as construction materials, were a key component in Hive3D Builders’ material. They exhibit advantages like excellent strength, high durability, and outstanding fire resistance.
Material Costs
3D concrete printing material generally has a significantly higher cost than regular concrete. This is because 3DCP does not use regular cement, but a mortar that dries notably quicker than regular concrete does. CyBe Mortar, for example, sets in three minutes and achieves structural strength in only one hour. This fast drying speed is needed because the bottom layers need to be strong enough to print the rest of the structure on. This special, fast-drying mortar, however, often comes at a higher cost than regular concrete does. Still, 3DCP is generally cheaper than regular construction. The technique has unique cost-saving properties due to a lower material need, as well as less necessary construction workers.
Hive3D Builders’ newly developed material, however, enjoys yet another advantage in this regard. Hive3D developed a unique system to automatically mix the cement replacement onsite with hyper-locally sourced aggregates to lower their material costs exponentially. By creating this system to automatically mix the cement replacement product onsite with locally sourced aggregates, the company is able to lower the cost of its printing mortar to a third of the price of other commercially available printing mortars. This low cost might pave the way for many hesitant construction companies to finally make the switch to 3DCP. The development of this new low-cost, carbon-neutral material is poised to shape the additive manufacturing industry.
Revolutionizing the Construction Industry
One of the main reasons that 3D concrete printing is not as common as you would expect it to be after hearing the advantages, is the fact that construction companies are often hesitant to change their way of working. The construction industry is booming, so big companies in the industry often don’t have the time or need to properly consider new building technologies like 3DCP. When they hear about the technique’s higher material price, they often lose interest, without taking into account the cost savings on other aspects. With Hive3D Builders adding a low material price to the material’s already impressive list of better sustainability and superior strength, the sustainable innovators might be able to convince headstrong construction giants to consider additive manufacturing as a cheaper, faster, and more sustainable alternative to their current construction methods. Using their partner CyBe Construction’s printer and Hive3D Builders’ carbon-neutral material, the company is set out to revolutionize the construction industry on a global scale.
Lafarge’s Impact on nidus3D’s Endeavor: Canada’s Largest 3D-Printed Housing Project
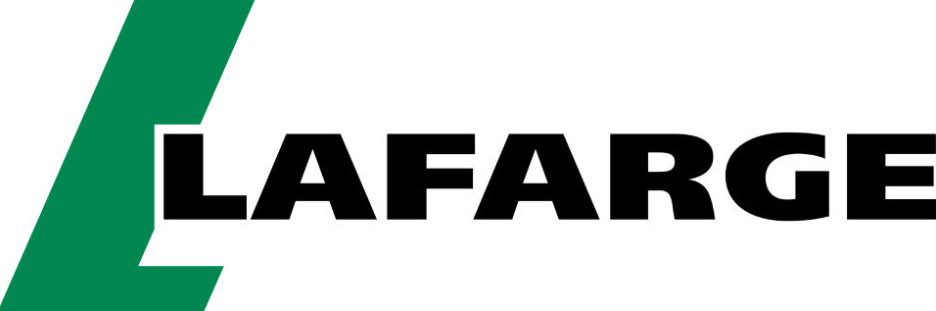
CALGARY, Alberta, January 11, 2024–(BUSINESS WIRE)–Lafarge Canada today announced its combined effort with nidus3D in supplying its OneCem low-carbon cement in Canada’s largest 3D-printed housing project, aimed at addressing the acute housing challenges faced by the SikSika Nation.While nidus3D has successfully completed 3D-printed housing projects in Ontario, this marks the first venture of its kind in Alberta. Located one hour’s drive east from the city of Calgary, the project named “Kakatoosoyiists” (Star Lodge) will consist of 4 buildings, comprising a total of sixteen units, each specifically designed to provide a supportive haven for individuals of SikSika Nation fleeing domestic violence or facing homelessness.This initiative directly confronts a pressing issue underscored by the Social Planning & Research Council of Hamilton. According to their report, Indigenous peoples in Canadian cities are eight times more likely to face homelessness compared to the general population.Lafarge is supplying its OneCem low-carbon cement for this project, recognized for its ability to deliver a reduced carbon footprint. When manufactured, the higher limestone content of OneCem translates into a reduction of greenhouse gas emissions—up to ten percent when compared to traditional Portland cement. OneCem achieves this sustainable advantage while maintaining its strength, durability, performance and workability.”Our shared goal with nidus3D extends beyond mere innovation,” says Brad Kohl, president and CEO of Lafarge Canada (West). “This project is about helping address the critical housing needs of the nation and foster a resilient, inclusive future through sustainable construction practices. We were proud to contribute to this project.”nidus3D, a leading innovator in 3D-printed housing, is excited to bring its expertise to Alberta.”Nidus3D is honoured and energized to be working with Siksika First Nation and Lafarge Canada on this innovative Canadian first,” says Ian Arthur, nidus3D’s president. “This multi-build development will not only provide much needed housing but show the immense potential of 3D construction printing to address Canada’s housing crisis. This project will demonstrate efficiencies and savings the technology can deliver through rapid, repeatable construction.”With the construction underway, this collaboration stands as a testament to the potential of combining expertise, resources, and a shared commitment to building not just structures but sustainable, supportive communities for a brighter future. The project is expected to be completed by March 31st, 2024.About nidus3DFounded in 2021, nidus3D is an innovative Canadian robotic construction company delivering rapid, low cost printed structures with automated, on-site3D concrete printing. As a process driven company, nidus3D is leading technology driven innovation in the construction sector to revolutionize the way homes are built. nidus3D has completed multiple proof-of-concept projects, including Canada’s first residentially-permitted 3D-printed structures and North America’s first two-story and three-story 3D-printed building and is currently scaling 3D construction printing across Canada. With its proven technology, nidus3D is ready to lead 3D construction printing into the future.About Lafarge Canada Inc.Lafarge Canada is a subsidiary of Holcim, a global leader in innovative and sustainable building solutions. Driven by its purpose to build progress for people and the planet, its 60,000 employees are on a mission to decarbonize building, while improving living standards for all. The company empowers its customers across all regions to build better with less, with its broad range of low-carbon and circular solutions, from ECOPact to ECOPlanet. With its innovative systems, from Elevate’s roofing to PRB’s insulation, Holcim makes buildings more sustainable in use, driving energy efficiency and green retrofitting. With sustainability at the core of its strategy, Holcim is becoming a net-zero company with 1.5°C targets validated by SBTi.www.lafarge.caView source version on businesswire.com: https://www.businesswire.com/news/home/20240111133773/en/ContactsKristen MarstonCommunications and Marketing Coordinator, Western CanadaLafarge Canada Inc.kristen.marston@lafarge.com Rafael Olvera GuelSales and Marketing ManagerNidus3Drafael.guel@nidus3D.com