Construction starts on 20 ‘Passive House’ new homes at former Leeds quarry site
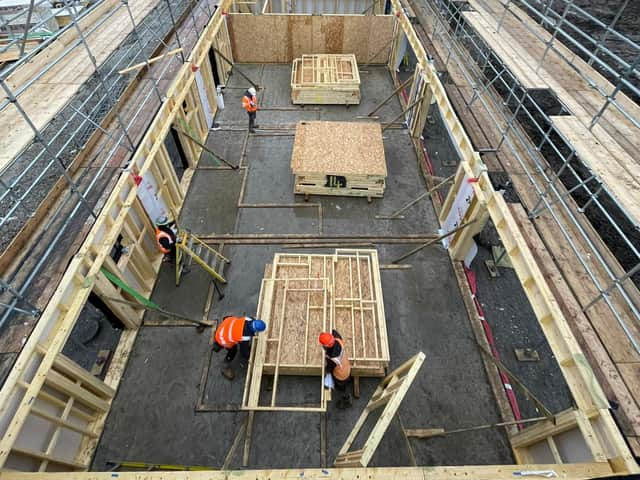
The former quarry site in Drighlington was purchased in 2022 by Leeds-based developer Pure Haus, and gained planning permission in August last year for the construction of the Spring Meadows scheme due to be completed in February 2025. The ultra-isolated timber frames have now arrived at the site for what will become 20 “eco-family” passive […]
Nate Sheets Photographs the First Certified Passive Home in Missouri
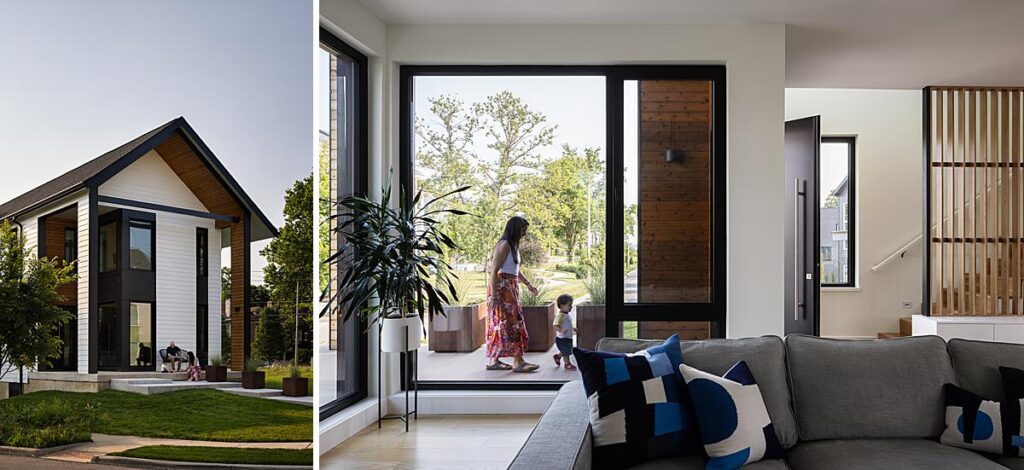
Project of the Week On this episode of Project of the Week, we’re back with POTW pro Nate Sheets and his gorgeous work. Today Nate will be taking us on a visual tour of the first certified passive house in Missouri, and giving us some insight along the way! Nate shares how he got linked […]
First Passive House Secures $70M Fannie Mae Loan
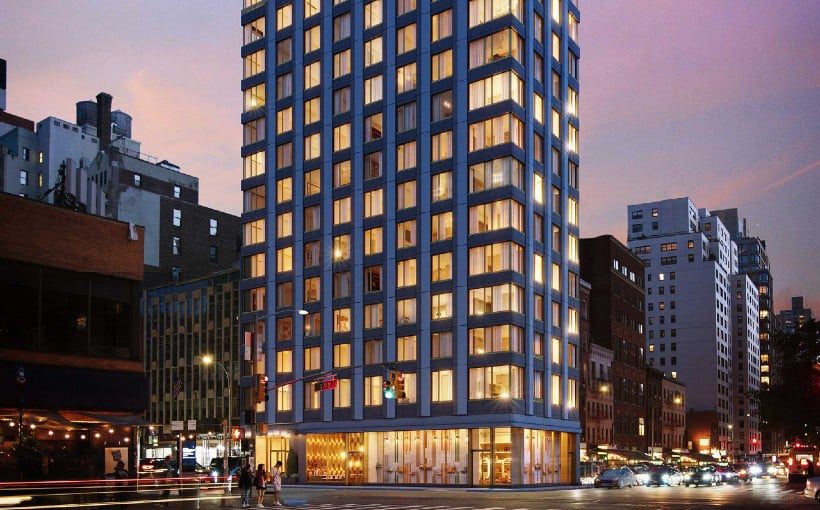
SMA Equities has secured a $70.635 million Fannie Mae loan to refinance 200 East 23rd St., a newly completed, 20-story mixed-use property in Gramercy Park. This will be the first property with a Passive House certification financed by Fannie Mae. The loan is a 10-year, interest-only fixed-rate Fannie Mae loan through Fannie Mae’s Near-Stabilization program. […]
Moises Sánchez plants a stucco cube holiday home in Mexico
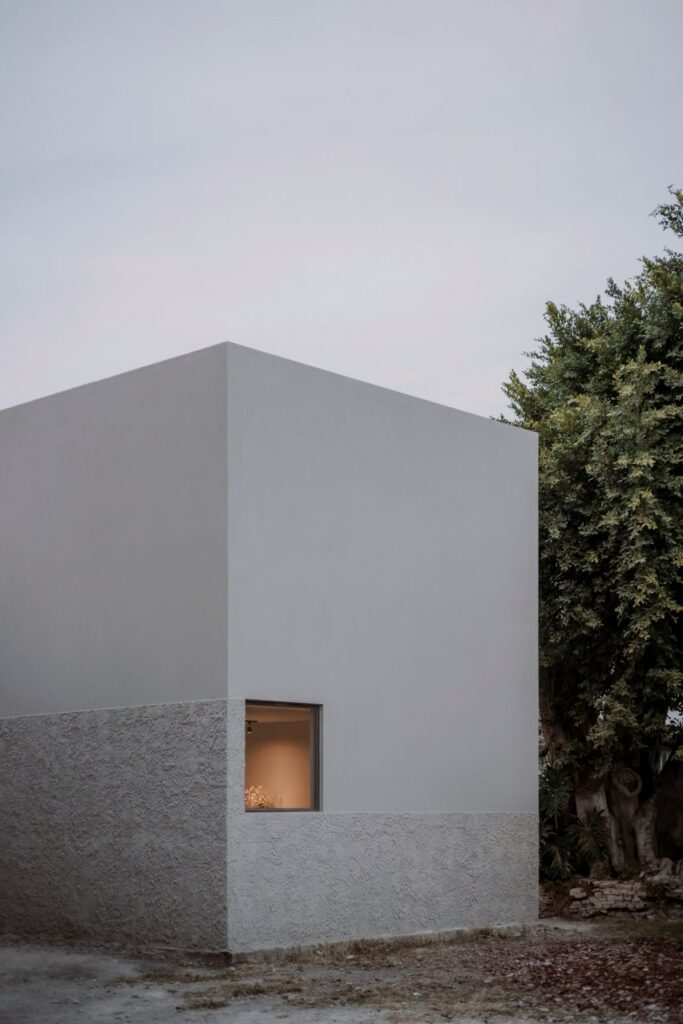
Guadalajara-based architect Moises Sánchez has created a stucco-clad, cube-shaped holiday home shaded by a large tree in western Mexico. The simple, 450-square foot (42-square metre) structure, known as Tonalli House, was completed in 2023 in Jocotepec, Jalisco, minutes from Lake Chapala, the country’s largest lake. Tonalli House is shaped like a cube “The project arises […]
CAZA employs passive cooling for concrete FR House in the Philippines
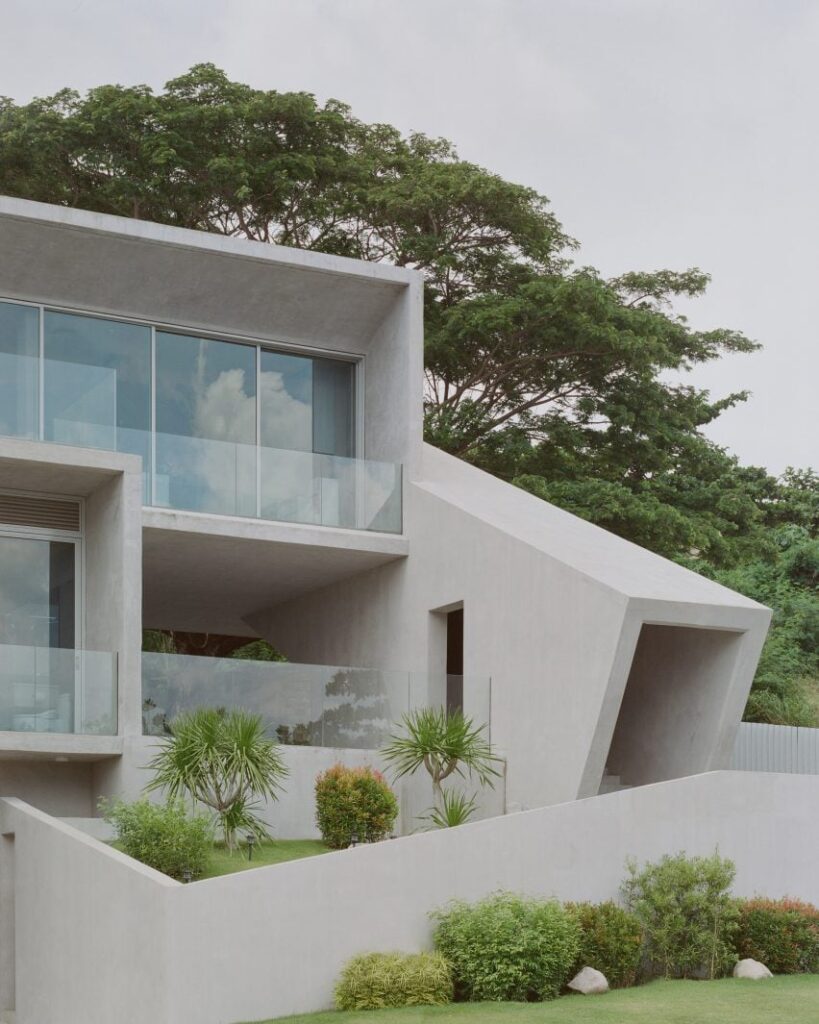
New York studio CAZA has completed a cast-concrete house in the Philippines, aiming to optimise passive cooling and natural ventilation. FR House comprises a series of “concrete cubes” that facilitate cross-ventilation and regulate the building’s temperature at the warmest times of the day. FR House is located on a sloping site in Punta Fuego According […]
ICON Unveils “House Zero” and Announces 2022 SXSW Activations
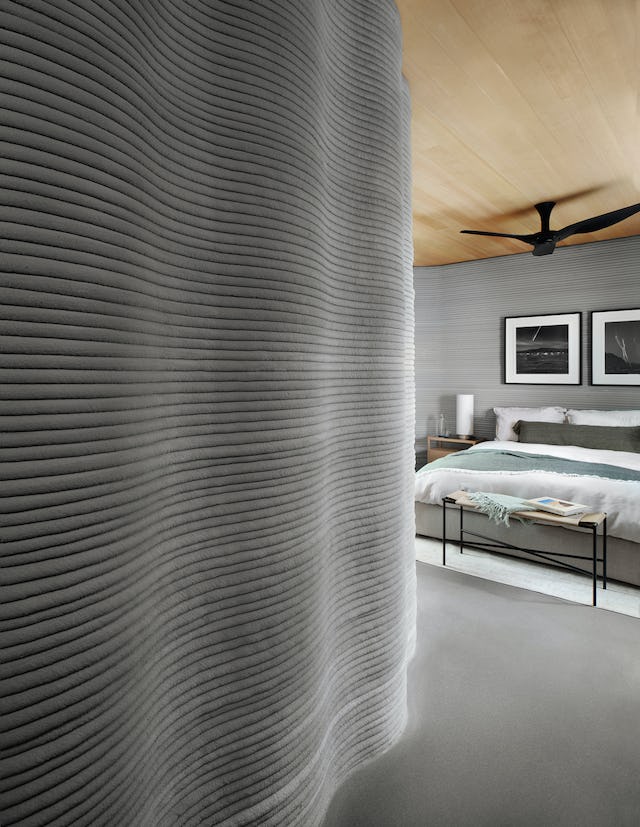
New 3D-printed Home Pushes the Boundaries of Resilient and Sustainable Architecture and Design; Official SXSW Event Tours of ICON’s “House Zero” Revealed for March 13-14, 2022
Photo: Casey Dunn
AUSTIN, TX, March 2, 2022 – ICON, the leader of advanced construction technologies pioneering large-scale 3D printing, today unveiled its newest 3D-printed home, “House Zero” in Austin, Texas. House Zero is the first in what ICON hopes will be an entirely new genre of homes that are specifically designed to utilize opportunities created by 3D printing. For this initial project in ICON’s “Exploration Series,” the team partnered with the award-winning Texas firm, Lake|Flato Architects.
[embedded content]
As an official SXSW partner, ICON will open the doors to “House Zero” for tours March 13-14, 2022 from 9am – 6pm (badge holders will have priority entrance). Sign up today for a tour of the world’s most beautiful 3D-printed home that illustrates the future of homebuilding at https://bit.ly/Tour_ICONHouseZero.
Photo: Casey Dunn
ICON co-founder and CEO, Jason Ballard, will also be delivering a featured talk at SXSW 2022 discussing the role robotics, architecture, materials science will play in solving many of humanity’s current challenges such as housing affordability, community health, sustainability, climate resiliency, and human potential. Moderated by PBS NewsHour correspondent and PBS NewsHour West anchor, Stephanie Sy, the featured session, “It’s Time to Build: a Conversation with Jason Ballard,” will take place on March 15, 2022 at 2:30pm at Hilton Austin Downtown in Salon H. Find out more — > https://bit.ly/SXSW_ICON
_ _ _ _
ICON’s House Zero
Located in East Austin, “House Zero,” was 3D printed by ICON’s next-gen Vulcan construction system and designed by Lake|Flato, known for their sustainable designs. Blending mid-century modernist ranch house aesthetics, the home features an elevated architectural and energy efficient design that highlights the benefits of resiliency and sustainability, with the digital possibilities of additive construction.
Photo: Casey Dunn
“House Zero is ground zero for the emergence of entirely new design languages and architectural vernaculars that will use robotic construction to deliver the things we need most from our housing: comfort, beauty, dignity, sustainability, attainability, and hope,” said Jason Ballard, co-founder and CEO of ICON. “Houses like this are only possible with 3D printing, and this is the new standard of what 3D printing can mean for the world. My hope is that this home will provoke architects, developers, builders, and homeowners to dream alongside ICON about the exciting and hopeful future that robotic construction, and specifically 3D printing, makes possible. The housing of our future must be different from the housing we have known.”
The innovative home, a 2,000+ sq-ft, 3 bedroom/2.5 bath home and a 350 sq-ft, a 1 bedroom/1 bath accessory dwelling unit, features ICON’s resilient 3D-printed wall system, which replaces a building system traditionally made up of multiple steps saving time, waste and cost. The walls of the home are made with a proprietary cementitious-based material, “Lavacrete,” insulation, and steel for reinforcing. Lavacrete provides thermal mass that slows heat transfer into the home and the combination of thermal mass, increased insulation, and an airtight wall increases the energy efficiency and reduces lifecycle costs.
Photo: Casey Dunn
Biophilic principles—the way that humans connect with nature and nature-inspired compositions —are behind much of “House Zero’s” design and best accomplished using ICON’s next-generation 3D-printing technology. The curved walls create structurally efficient self-stability, while rounded corners allow for softer, more naturalistic circulation routes throughout the home. Doorways and windows were strategically placed to accentuate accompanying landscapes; eastern-facing high clerestory windows illuminate the living room with soft, yet dynamic sunlight, minimizing the need for electrical lighting throughout the day.
“The 3D-printed wall design and its inherent biophilic quality conveys an ordered, yet non-rigid pattern invoking a rooted and timeless sense of natural refuge,” said Lewis McNeel, Associate Partner, Lake|Flato.
Photo: Casey Dunn
“While the organic nature of the 3D-printed concrete and curved walls are new design languages for us, House Zero was still entirely in line with the natural connections we seek in our architecture,” said Ashley Heeren, Associate, Lake|Flato. “The home expresses our shared passions for craft and performance in an inviting and comfortable family home constructed through a totally new way of building. It’s been a thrill for our team to work with ICON on such an innovative home design and be a part of the future of homebuilding.”
ICON continues to set new standards for delivering resilient, dignified housing at high-speed and lower cost. Raising $451 million to date in funding, ICON has delivered communities of 3D-printed homes in the U.S. and internationally and forged partnerships with world-renowned architects, builders and housing organizations missionally aligned to shift the paradigm of homebuilding. In fall 2020, ICON was awarded a research contract through the Air Force, which included funding from NASA to begin research and development of an off-world construction system planned to support future exploration of the Moon and beyond.
Photo: Casey Dunn
About ICON
ICON develops advanced construction technologies that advance humanity. Using proprietary 3D printing robotics, software and advanced materials, ICON is shifting the paradigm of homebuilding on Earth and beyond. For more information visit www.iconbuild.com or follow the conversation on Instagram, Twitter, Facebook, YouTube (@ICON3DTech).
About Lake|Flato
Established in 1984, Lake|Flato designs buildings that respond to the culture and climate of each unique place. Lake|Flato believes in creating environments that enrich communities and nurture life. In collaboration with clients, Lake|Flato creates buildings that are tactile and modern, environmentally responsible and authentic, artful and crafted. Lake|Flato’s work has received wide critical acclaim in more than 300 international, national and regional awards, including the American Institute of Architects Firm of the Year Award in 2004 and 13 Top Ten Green Project Awards from the AIA Committee on the Environment. Lake|Flato placed 1st in Architect Magazine’s 2019 Top 50, an annual ranking of the best U.S. firms, and was named one of the Ten Most Innovative Architecture Firms in the World by Fast Company. For more information visit https://www.lakeflato.com/.
First 3D Printed Net Zero Energy Home Made in Los Angeles
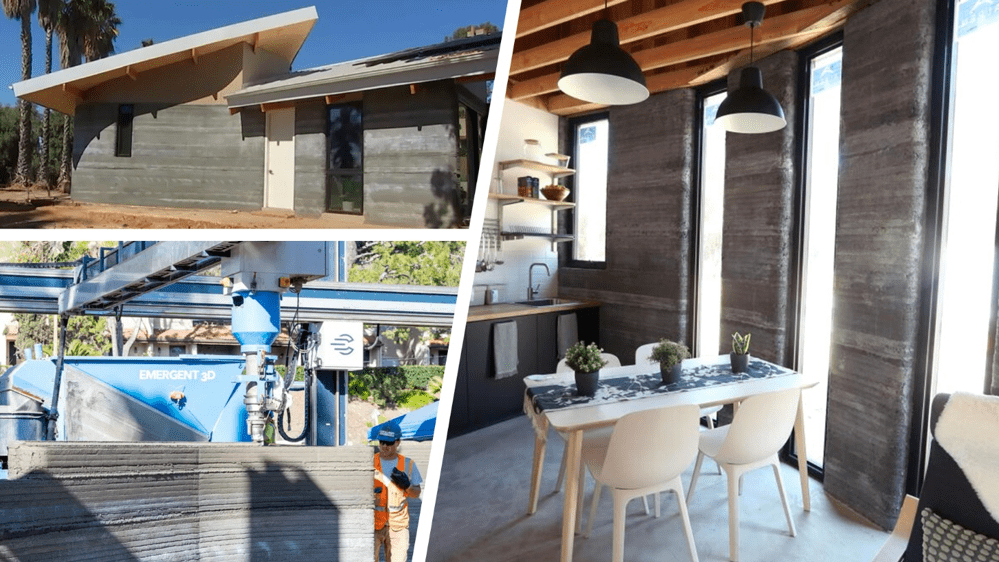
LA’s first 3D printed net zero house completed by Woodbury university students in collaboration with Emergent. Architecture Students from Woodbury University completed Los Angeles’ first fully permitted 3D printed net zero energy house. The house was part of a nationwide collegiate contest by the US Department of Energy. The walls of the 425 square-foot (40 m2) house, […]
150,000 Plastic Bottles Were Used to Create This 3D-Printed Tiny Home
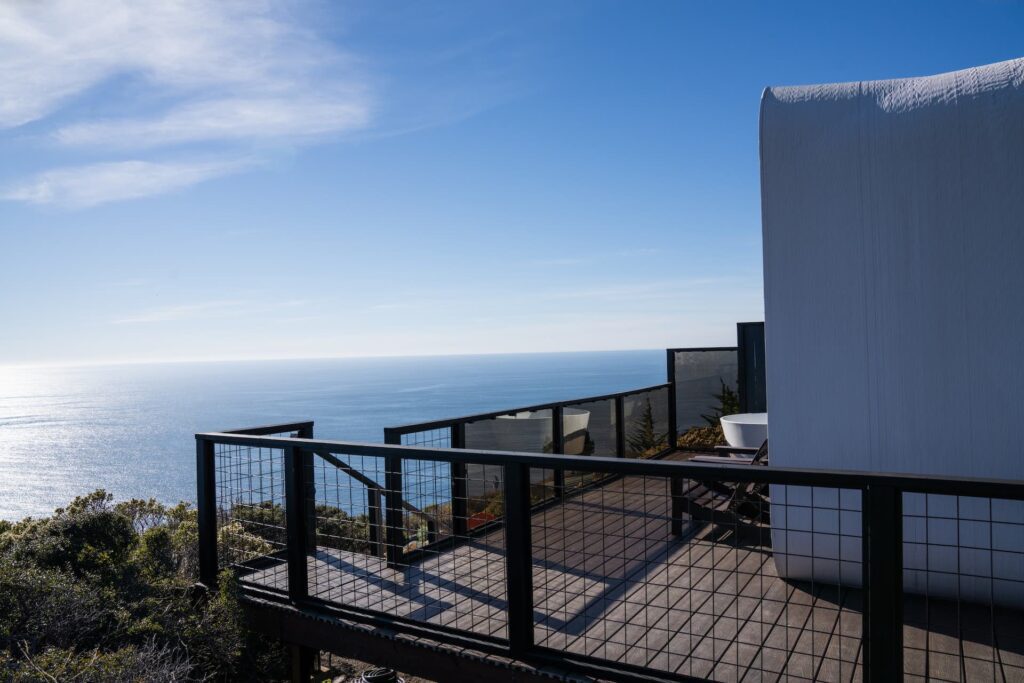
Welcome to Prefab Profiles, an ongoing series of interviews with people transforming how we build houses. From prefab tiny houses and modular cabin kits to entire homes ready to ship, their projects represent some of the best ideas in the industry. Do you know a prefab brand that should be on our radar? Get in touch! Ross Maguire has been a laborer on construction sites, holds a master’s in engineering, and started a few construction companies before moving from the U.K. to California in 2019. Soon after, he partnered with Gene Eidelman, a real-estate developer with a background as a construction executive, and the pair set out to find a better way to build residences. They founded Azure Printed Homes, which makes modular prefabs out of materials often treated as waste. “Each of our 3D-printed modules repurposes around 150,000 plastic bottles,” Ross tells us. “These modules are approximately 200 square feet in size and can be printed in just 24 hours.” Here, we ask the cofounder about the different models that Azure makes, how long it takes to fabricate them, and what’s included with the purchase. Azure Printed Homes offers several models ranging from 100-square-foot backyard studios for $19,900 to 900-square-foot homes that start at $200,000.What’s the most exciting project you’ve realized to date? We recently delivered one of our units to a remote site in Big Sur. The location offers awe-inspiring views of the rugged coastline. While we anticipated some challenges during the delivery and installation process, we were pleased to complete it within just 48 hours. This achievement is especially remarkable given the site’s isolation. Our customer is the owner of a wonderfully tranquil glamping vacation resort and shares our commitment to adopting a circular approach to creating living spaces. The sustainability aspect was a significant and appealing factor for the customer when choosing an Azure home. What does your base model cost and what does that pricing include? Our smallest model, the N-100, is 100 square feet and begins at $19,900. That includes all interior and exterior finishes, lighting, and power, making it ready for our customers to furnish. Each unit is prepped for a power connection, or alternatively, customers can opt to include a solar panel and battery, enabling the unit to operate independently of the electric grid. The entire manufacturing process for one unit takes only one week, and installation can be accomplished in just one day. After the shell is 3D-printed, the interiors are outfitted with wiring, plumbing (if the unit is larger than 120 square feet), and a client’s preferred interior finishes.What qualities make your prefab stand apart from the rest? Since our inception, we’ve observed a wide range of reasons why people are drawn to our units. Some are captivated by the unique designs and aesthetic appeal. Others are enticed by the remarkable speed and efficiency of our production process. Then there are those who simply look at the price tag and base their decision on cost alone. However, the overwhelming majority of our customers are deeply passionate about sustainability and the circular nature of our approach. Our innovative process revolves around utilizing waste materials as a primary supply source, resulting in a system that generates no waste. Being able to create something beautiful and unique from a waste supply line is something that we are hugely proud of, especially given that our end product aims to address the housing crisis. It’s a true testament to the saying “one person’s trash is another’s treasure.” Azure Printed Homes provides an online configurator that lets their clients adjust the layout of the unit. For example, while the kitchen is normally situated along the midline of the unit, in this model, it’s been moved against the envelope.Where is the prefab currently available? We currently manufacture our units in Southern California and we can load four of our smallest units onto one flatbed truck. We have already transported our units to the East Coast. Our growth plan is to set up multiple factories across the U.S. to serve neighboring states and reduce the delivery distances. Is your design currently pre-permitted in any U.S. municipalities? We work with third-party approval agencies across the country, enabling us to take care of all the building and safety requirements for the prefab module itself. The planning and utility approvals still need to be generated locally through the local municipality, but there is no need for approval of the design or fabrication itself. While the prefabs can be purchased with solar arrays and batteries, the company is currently developing water- and waste-treatment systems to make their homes more suitable for off-grid sites.Are there plans to expand to different parts of the world? We do plan to branch out across the country in the near future and aspire to serve countries and communities across the world that are underserved with housing options. We’ve already seen great interest from Europe, Australia, and East Asia, where housing demands are high and the supply is short, inefficient, and expensive. What aspects of an install do you manage? We advise customers through all stages from planning to moving in. We can also make introductions and connections through the journey when local knowledge and expertise are necessary. Although the methodology of producing our units is technologically advanced, we have insisted on making the design and installation as simple as possible for our customers and partners. Units of 360-square-feet in size or less can be ordered as ANSI-certified mobile models for an additional $5,000 to $10,000.How long can a client expect the process to take after they put down a deposit? The lead time is different for each of our different prefabs types. As a guide: Studios: 2-4 weeks Wheel based units: 4-6 weeks ADUs & Homes: 4-8 weeks What aspects of the design can a client customize? We currently have three different model designs that are available across a number of different sizes and layouts. For each option, we have “families” of finishes that our in-house design team have chosen to serve the different tastes and styles of our customers. The finish and color of the envelope can be customized. Other add-ons include air conditioning, underfloor heating, and expanded glazing.
Pinnacle Breaks Ground on Michigan’s First MF Passive Housing
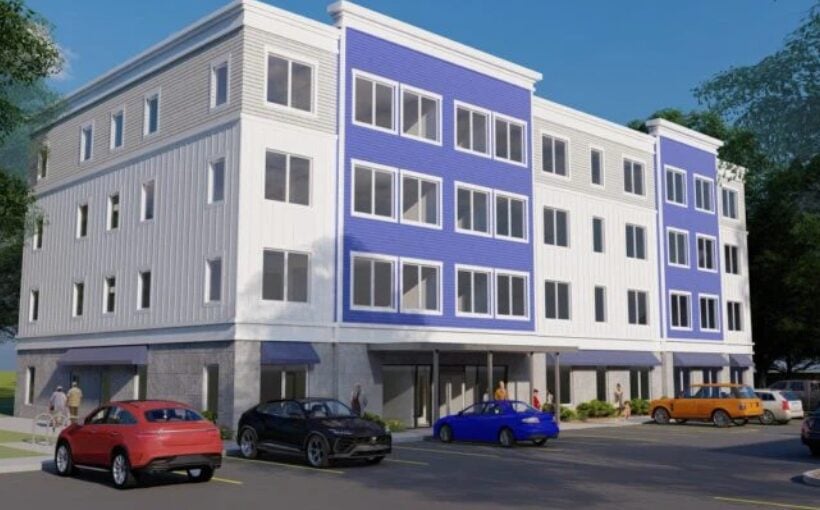
Pinnacle Construction Group, a Grand Rapids-based design-build firm, has started work on Michigan’s first multifamily certified passive housing development. Pinnacle began the project last month and will host an official groundbreaking ceremony next week for Samaritas Spring Lake, a 53-unit affordable housing rental project, reported Crain’s. The development will total 43 one-bedroom and ten two-bedroom […]
New passive house partnership allows lower cost financing for developers
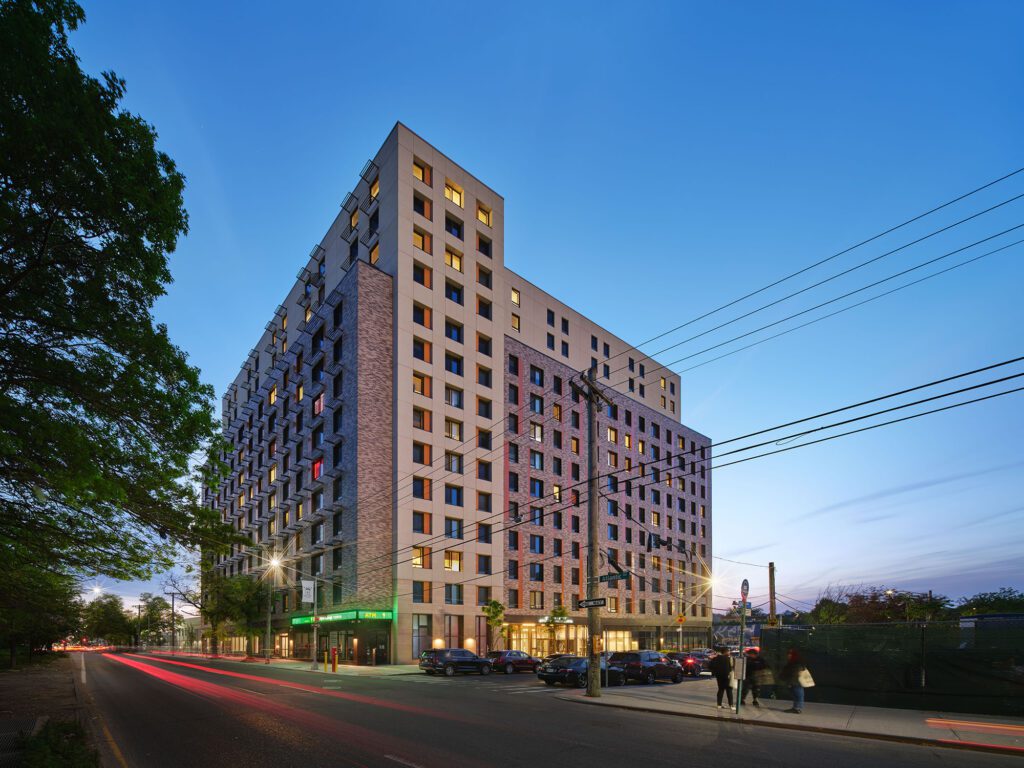
PACE Equity, the leader in Property Assessed Clean Energy (PACE) financing for development projects, along with decarbonization non-profit Phius, jointly announced a new compliance path for PACE Equity’s CIRRUS Low Carbon program at PhiusCon 2023. Through the new partnership, commercial real estate projects that are certified as Phius CORE or Phius ZERO passive house buildings […]
Training on passive house methods, state codes at CMCC Thursday
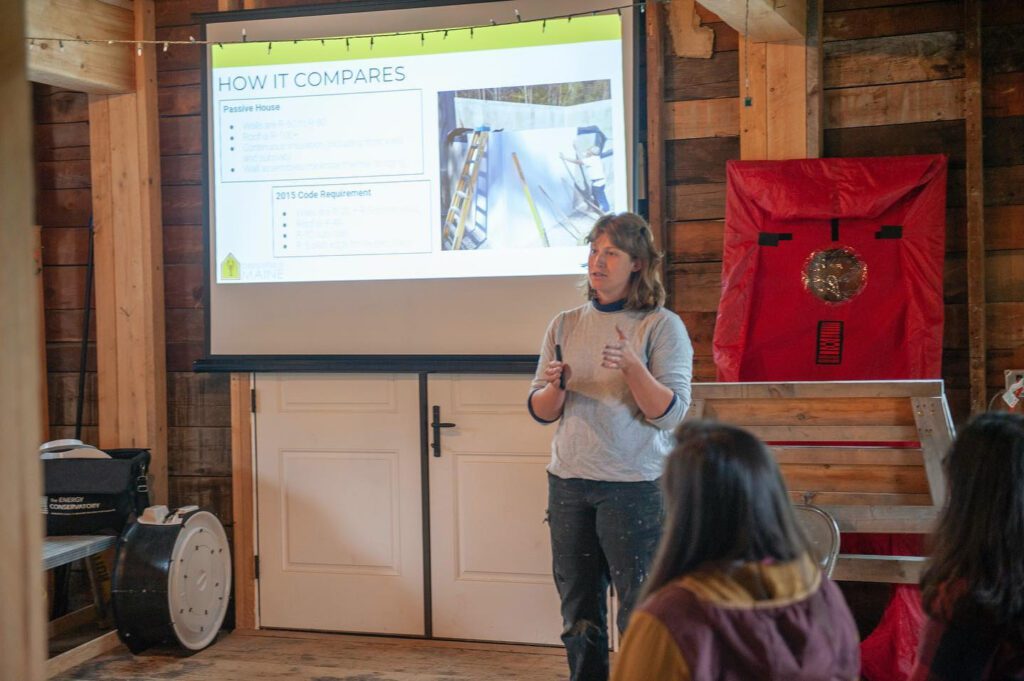
Participants follow a demonstration by Anna Heath during a passivhausMAINE training session. AUBURN — The nonprofit passivhausMAINE, which promotes sustainable and passive building throughout the state, is continuing its series of trainings to help hobbyist, homeowners, and new and experienced builders employ passive house principles. A full-day training session for $25 will take place […]
Partners break ground on state’s first multifamily passive housing project
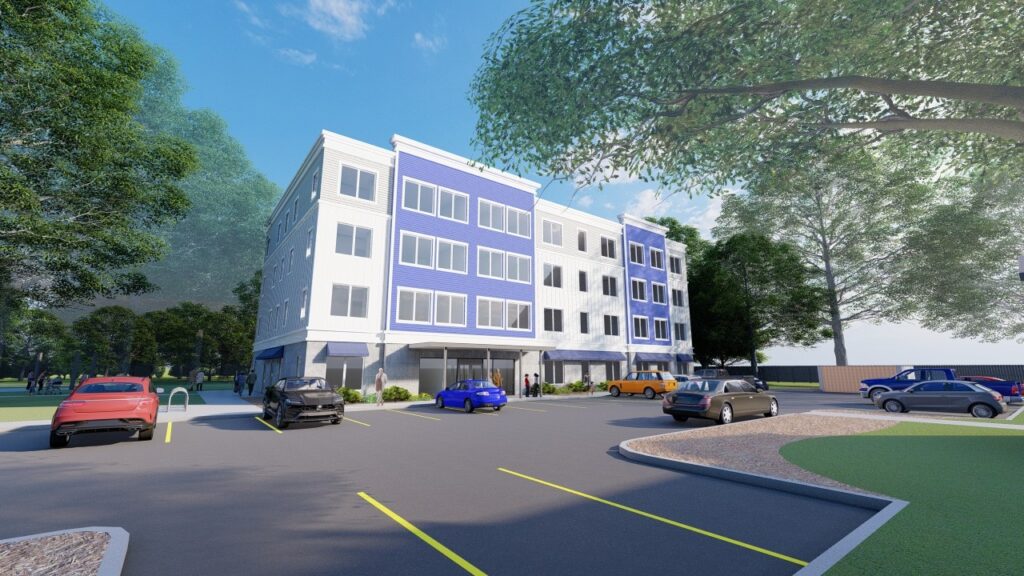
Pinnacle Construction Group has started building what will be the first multifamily certified passive housing development in the state of Michigan. The Grand Rapids-based design-build firm began site work last month and will hold a groundbreaking Jan. 12 for Samaritas Spring Lake, a 53-unit affordable housing rental project at 734 E. Savidge St. in Spring […]
Energy Efficient Windows Are Important To An Energy Efficient Home
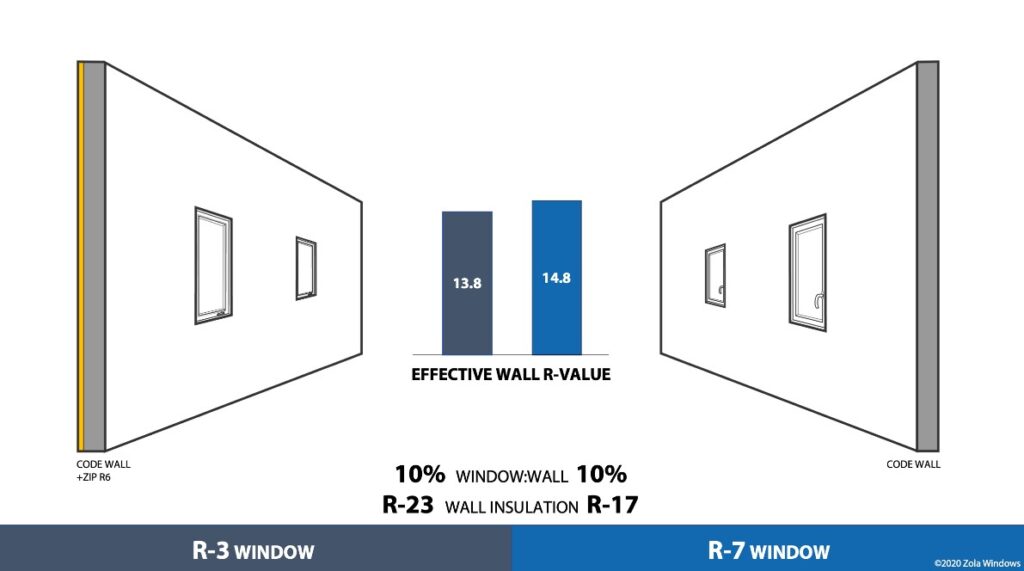
Recently, we published a story about how to decarbonize your life in 2024. One of the suggestions is to increase the insulating power of exterior walls and roofs but Zola Windows, in a blog post reprinted by Passive House News, points out that windows are often the weakest link in any insulation program. In fact, […]
FOREST INK: B.C. building code should consider Passive House design
While I support the new B.C. Standardized Housing Design Project, I am concerned with what is considered the definition of code-built. Standardized designs can substantially streamline the permitting process to make it easier for local governments to give building-permit approvals quickly and save builders and homeowners the costs that come from expensive design services. My […]
Is this the most energy-efficient way to build homes?
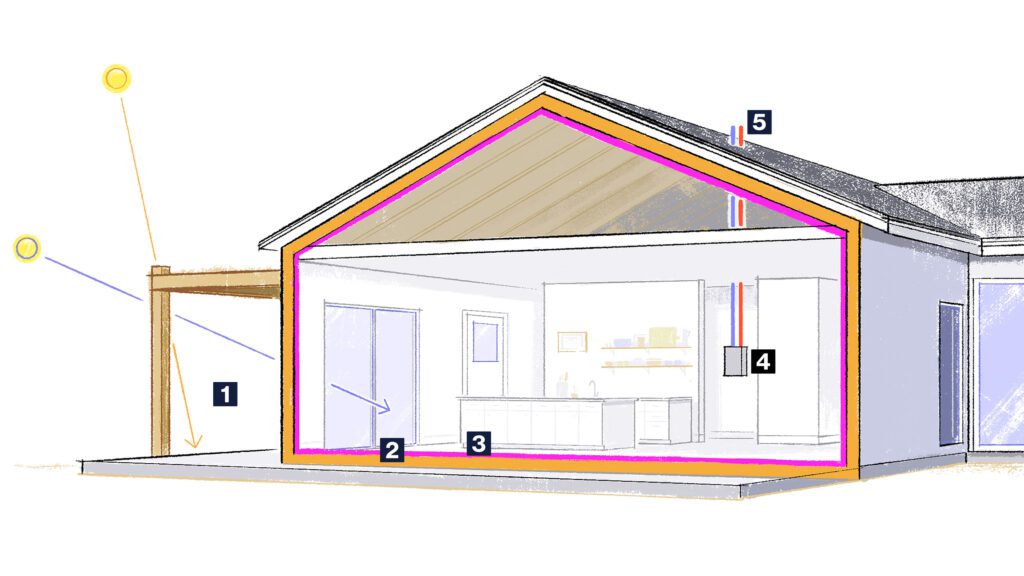
When the Canadian engineer Harold Orr and his colleagues began designing an ultra-efficient home in Saskatchewan in the late ’70s, responding to a provincial conservation mandate during the oil embargo, they knew that the trick wasn’t generating energy in a greener way, but using less of it. They needed to make a better thermos, not […]
276 units available at world’s biggest affordable Passive House, from $498/month
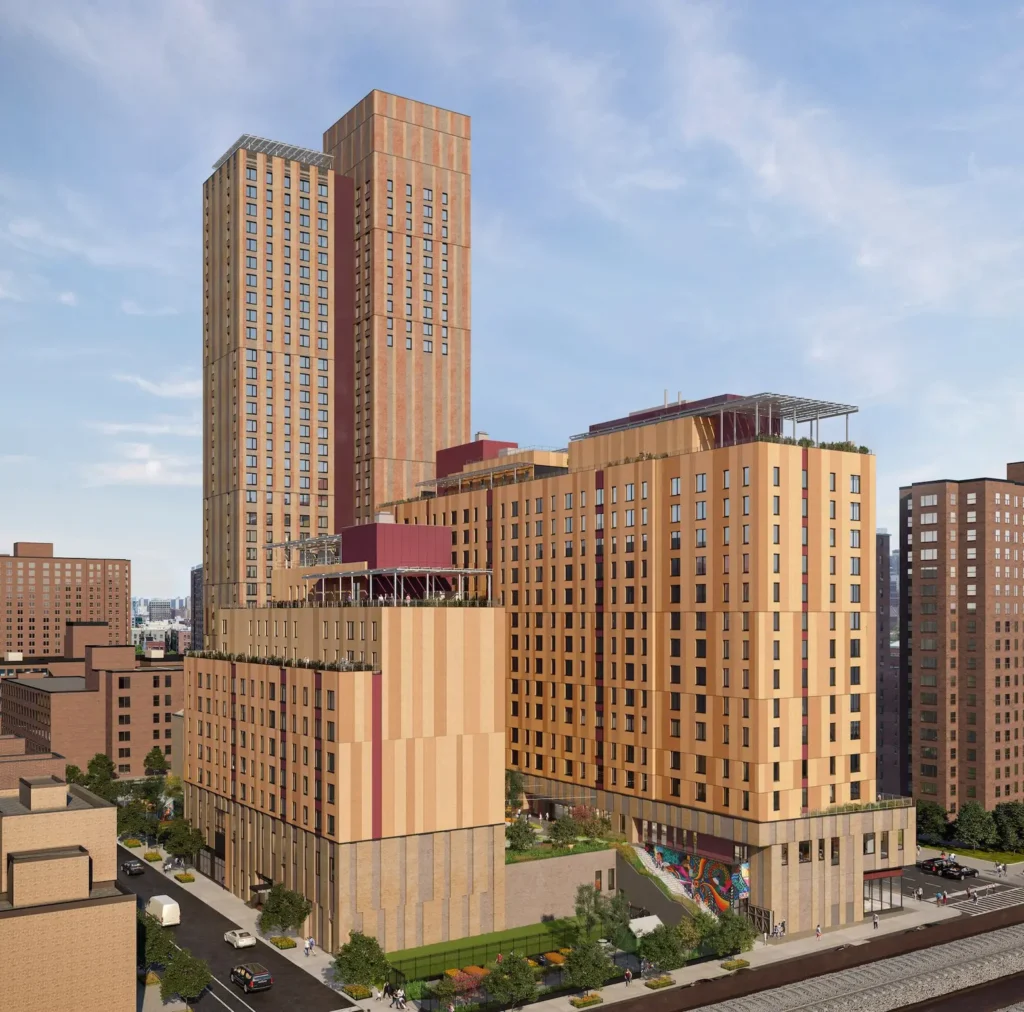
Renderings courtesy of the NYC Department of Housing Preservation and Development Applications are being accepted for 276 mixed-income units at the world’s largest fully affordable Passive House in East Harlem. Located at 50 East 112th Street, the building is the second phase of Sendero Verde, a mixed-use project with affordable housing, outdoor space, a school, […]
‘Passive House Design’ could be the future of sustainable living
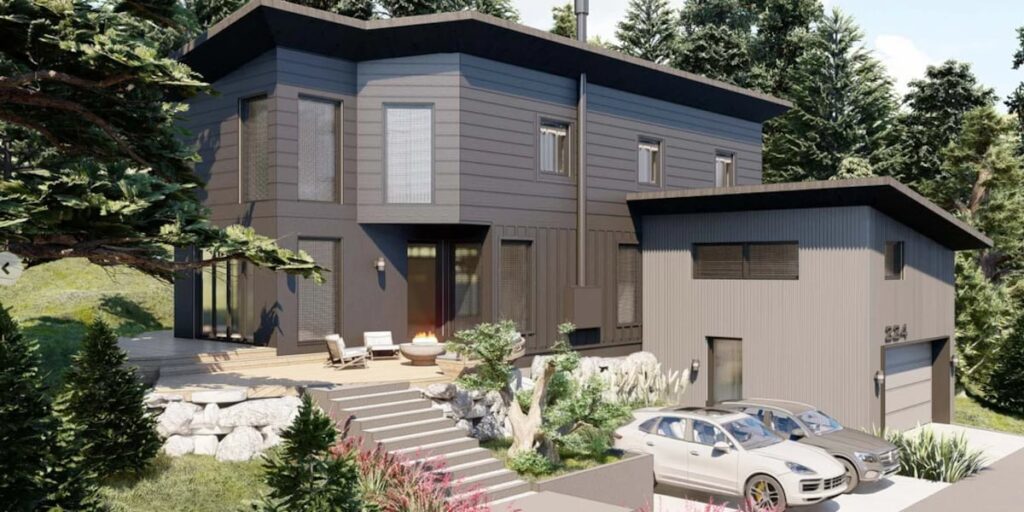
RENO, Nev. (KOLO) – What is a passive house? In layman’s terms, it essentially means that it is an energy-efficient home that is healthier for the environment. The future of how we build our homes can be part of the solution to saving the planet in the face of climate change. The American Institute of […]
Boston’s First Passive House-Certified Homes
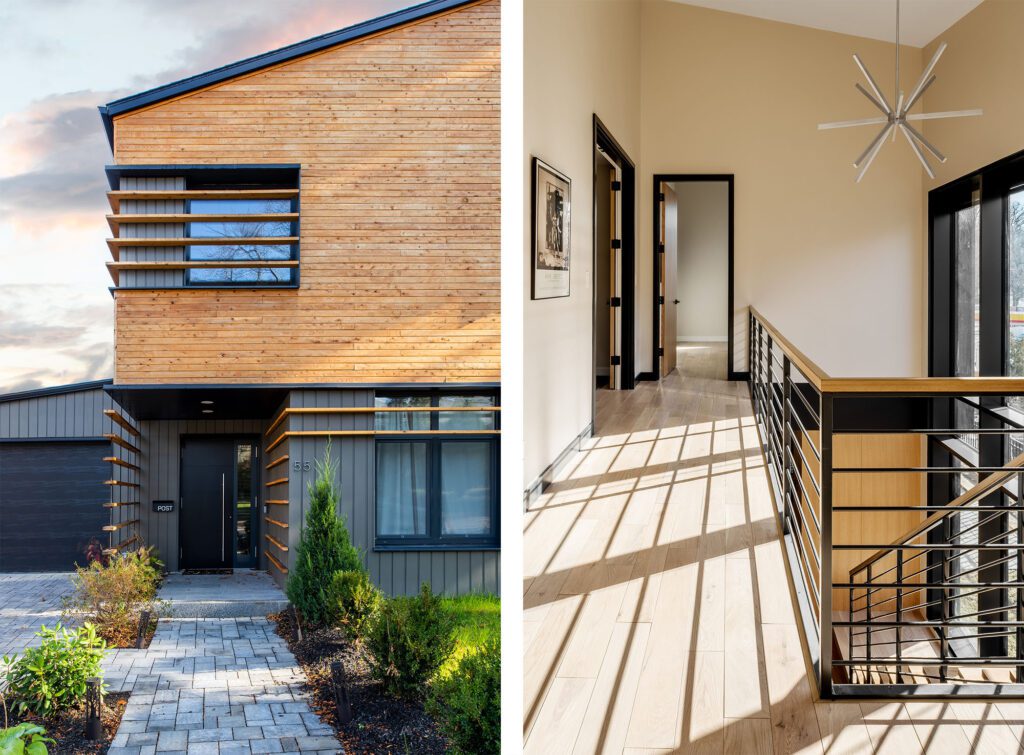
It was -10 degrees Fahrenheit during a brutal Boston winter. But inside one of three Brucewood Homes, it was a relatively pleasant 55 degrees—with the heating system turned off. The homeowner had switched off the heat to test the efficient, high-performance home. Another homeowner who had long suffered from seasonal allergies found that, in their […]
Project Profile: World’s Largest ‘Passive House’ Office Building
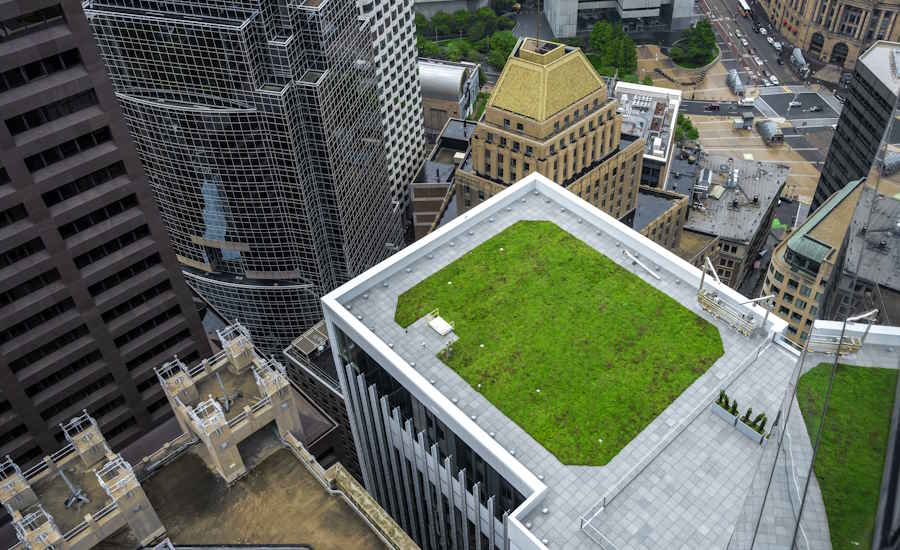
A typical building loses up to 25% of its heat through the roof. To ensure an office building in Boston could buck that trend, building designers and contractors turned to Elevate roofing and insulation systems by Holcim for the construction of the world’s largest “Passive House”-certified office building: the Winthrop Center in Boston. buzz Designed […]
Boston’s Winthrop Center Debuts as World’s Largest Passive House Office Building
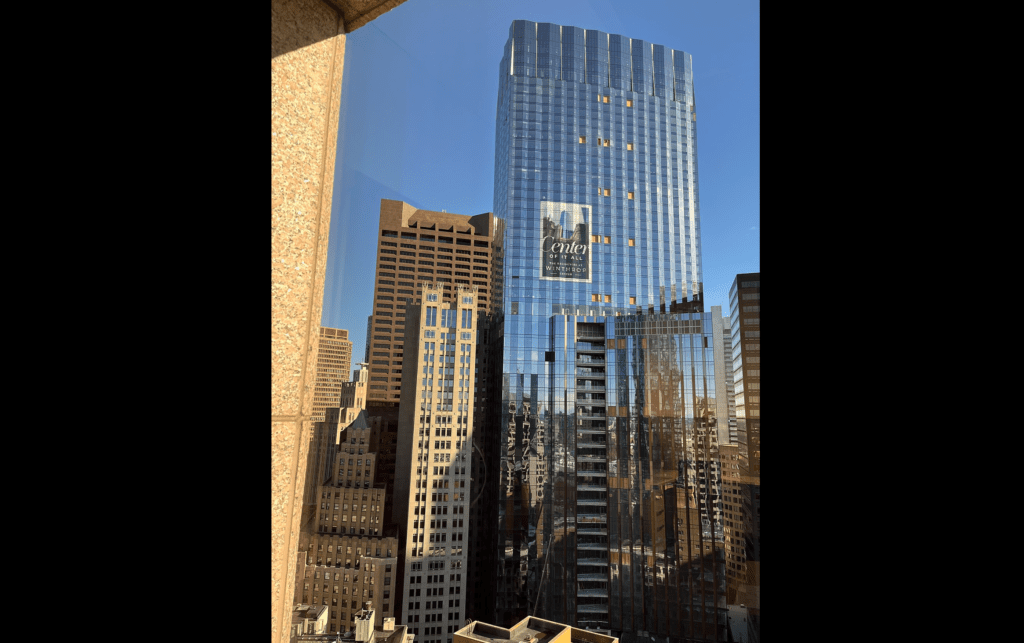
Today, the Boston’s Winthrop Center opened its doors; it is the world’s largest office building certified as a “passive house,” a testimony to advancements in energy-efficient building development. Passive house buildings comply with stringent requirements for heating, cooling, insulation, and natural lighting to maximize energy efficiency. Originating in the 1980s in Germany, these standards have been […]