Arkansas’s First-Ever 3D-Printed Homes Project Gets Approved
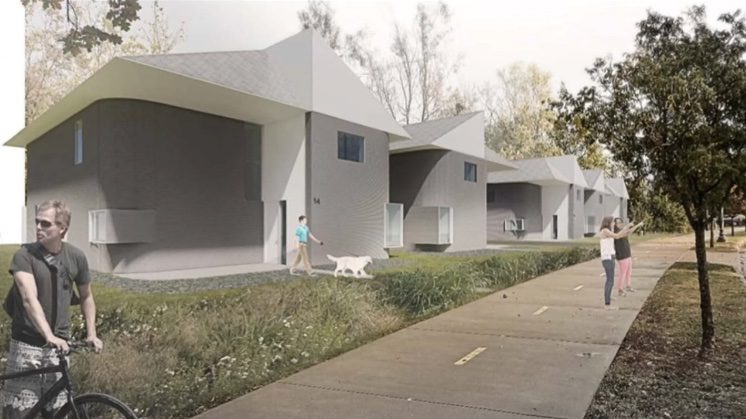
Arkansas’s first-ever inaugural 3D-printed housing project has received the green light from the Rogers City Council, which approved selling an acre of land to the Northwest Arkansas Council Foundation for the development. The project is aimed at addressing housing affordability.The foundation’s affordable housing division, Groundwork Northwest Arkansas, will use 3D-printed concrete technology to build two-story duplexes at 920 S First Street for those earning below 80 percent of the area’s median income. The sale of land was sanctioned at $50,000.“This will be one of, if not THE, first two-story residential 3D-printed homes in the U.S., and it is the first 3D-printed home in Arkansas,” Groundworks Executive Director Duke McLarty said.For the project, Groundwork will partner up with Alquist 3D, a company known for using robotic technology to create 3D-printed concrete homes, capable of building a 1,500-square-foot home in 30 hours.“At least four structures” comprising “at least eight units of housing” are expected to come from the project. These will feature two-story duplexes ranging from 1,300 to 1,600 square feet.Construction is expected to begin in late spring or summer, with occupancy anticipated by late 2024.To learn even more information about this groundbreaking project, click here.READ ALSO: ASO PLACES FINAL BEAM ON NEW $11.75M MUSIC CENTER
3D printed concrete housing coming to Rogers
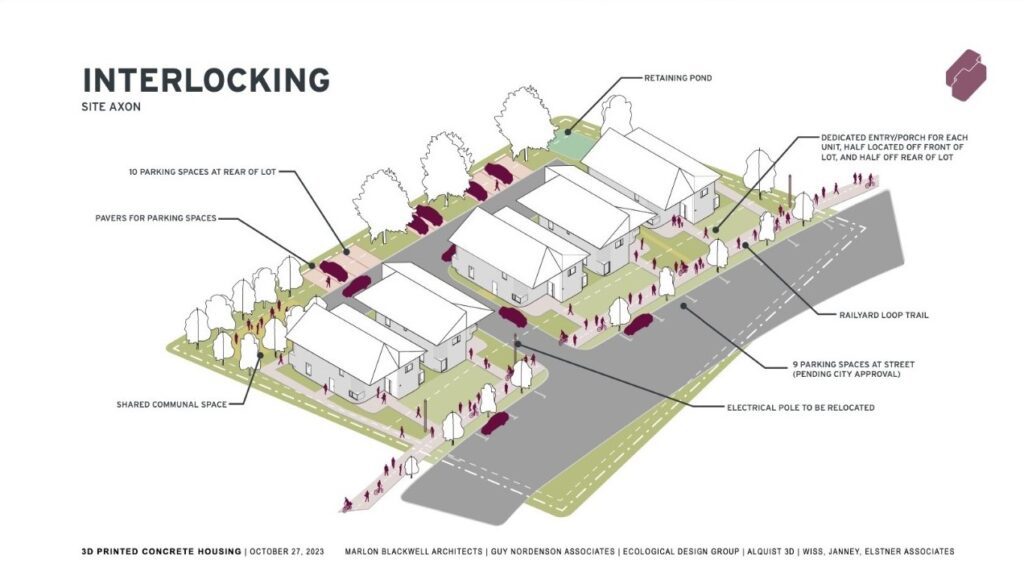
ROGERS, Ark. (KNWA/KFTA) — The city of Rogers approved to sell city-owned land to the Northwest Arkansas Council’s subgroup “Groundwork” to develop and produce a 3D-printed home.
This will be the first 3D-printed home in the state of Arkansas and the first two-story printed homes in the entire country according to Duke McLarty, executive director of Groundwork Workforce Housing for Northwest Arkansas.
He says there’s going to be a lot of people who are learning a lot through this process.
“With the goal that if a developer identifies cost savings through using 3D printed concrete as opposed to a normal just lumber approach, a lot of the barriers and potential constraints of that construction will have already been identified and worked out through our demonstration process,” McLarty said.
Renderings of 3D Printed concrete housing, provided by Duke McLarty, executive director of Groundwork Workforce Housing for Northwest Arkansas.
McLarty says Groundwork is the business community’s response to affordability. They are trying to raise awareness and work with municipalities, cities, and major employers and identify roles that each of them can play to try to bring some level of affordability back to the region.
“We think about it a lot as bringing some level of affordability back to each community in our region, because right now, many communities are not affordable for much of our population,” he said.
McLarty says the site is designed for four or five duplexes that are two stories located on 920 South 1st Street in Rogers.
He says he chose this location because it was close to downtown Rogers.
“They each have their own appeal, but many of them are no longer affordable for a lot of people in our region.”
There is also a bike path in front of the land, which McLarty sees as a huge advantage.
“People who work in the downtown Rogers Restaurants and bars and coffee shops and retail establishments could easily live in one of these and get to and from work on a bicycle and really would lessen their reliance on an automobile,” McLarty said.
Stormie Kuth is a renter in Downtown Rogers and she says ‘for something new like this to come in would be amazing.’
She says she would like to be a homeowner one day but renting might be her reality for the rest of her life because of unaffordable housing.
Kuth says she is happy that there will be more affordable housing in the area because it is an issue.
“I’m lucky that I am paying what I am paying. But I know a lot of people are struggling right now,” Kuth said.
She says she’s heard stories of local children having to stop going to school in the area and move into rural areas instead because it was more affordable for their families.
“Which is absolutely terrible and traumatizing,” she said.
Kuth says she would consider living in a 3D printed home but it would depend on the affordability and sustainability of it.
3D-printed homes have electrical and plumbing installed similarly to a traditional home but there are some differences.
McLarty says “So instead of, you know, lumber and drywall or a printer comes on site, it has a robot arm and it layers concrete to build these walls.”
He continues saying once the concrete dries, drywall can be put on the inside.
“It would feel and look no different than most homes that we’re used to in northwest Arkansas. It can be painted, it can be, you know, a typical and normal roof can be put on it,” he said.
He says 3D printed homes take a lot less manpower, less time to construct, and can be more affordable than traditional homes.
“They’re much stronger, you know, to say, extreme weather events, tornadoes, hurricanes. They’re also much more energy efficient; they’re just a tighter seal, so they’re not as drafty. Studies have shown them to be as much as 30% more energy efficient,” he said.
They’re also more fire-resistant than a wood-built home and don’t rot.
McLarty says, “I think it’s likely to catch on in the US and I’m doing my best to prepare at least our region to be in a good place, when that happens, we’re in a good place to capitalize.”
3D-printed homes are a little cooler than traditional homes and have echoes.
“I think folks will find ways to put rugs down and things like that to kind of dampen echoes, but I’m excited about it as well,” McLarty said.
He says their goal is to have eight to ten families who couldn’t afford to live in Rogers, call it home one day.
Their second goal is to get the development community, municipal community, real estate community, fire inspectors, and building inspectors comfortable with this new approach.
“So that when the next developer comes in and wants to use 3D printed concrete, all of those entities say, “No problem, we know what this is. You know, we’ve experienced it. We’ve seen it print. We’ve been on-site when electrical was being run through the wires,” he said.
He hopes this will give developers another tool to expedite development and keep growth going in Northwest Arkansas.
He says the sale price of the home is unknown but they are currently working on trying to find a builder to build the duplexes and they’re expecting some bids back in the upcoming weeks.
But they are targeting someone that makes around 80% of the area’s median income which is about $75,000 or $80,000 a year.
McLarty says, “We will income verify them to ensure that that the end product is going to the family that really needs it and it’s not someone who just thinks it’s cool and you know likes the location and likes the design it will have a mission focused buyer in the end.”
McLarty says they’re also narrowing in on a developer and finalizing their land purchase from the city of Rogers.
“There are a few things on the site that need to be done that we were hesitant to do until we had ownership of that land,” he said.
He says this project should be underway in late spring or summer with dirt work, roads, parking spots, and then the homes.
He hopes everything will be completely finished by the end of the year or early 2025.
McLarty says, “I mean that’s one of the advantages of using this approach is once, you know, kind of the plumbing and the underground work is in place, the robot can show up and they can print a 2000 square foot home in 36 hours or so with as few as two people.”
There will be an opportunity for the public to come by, look inside the walls, and get comfortable with this approach.
“I think some residents, if asked, do you want a traditionally built home or a 3D printed home, they might, you know, just opt for the traditionally built home because they don’t know. This will give them an opportunity,” he said.
Kuth says she thanks the city of Rogers for doing this and hopes surrounding areas and towns would follow their lead.
“Especially in lower-income towns, like Lowell especially,” she said.
The 3D-Printed Affordable Housing of the Future Will Be Recyclable
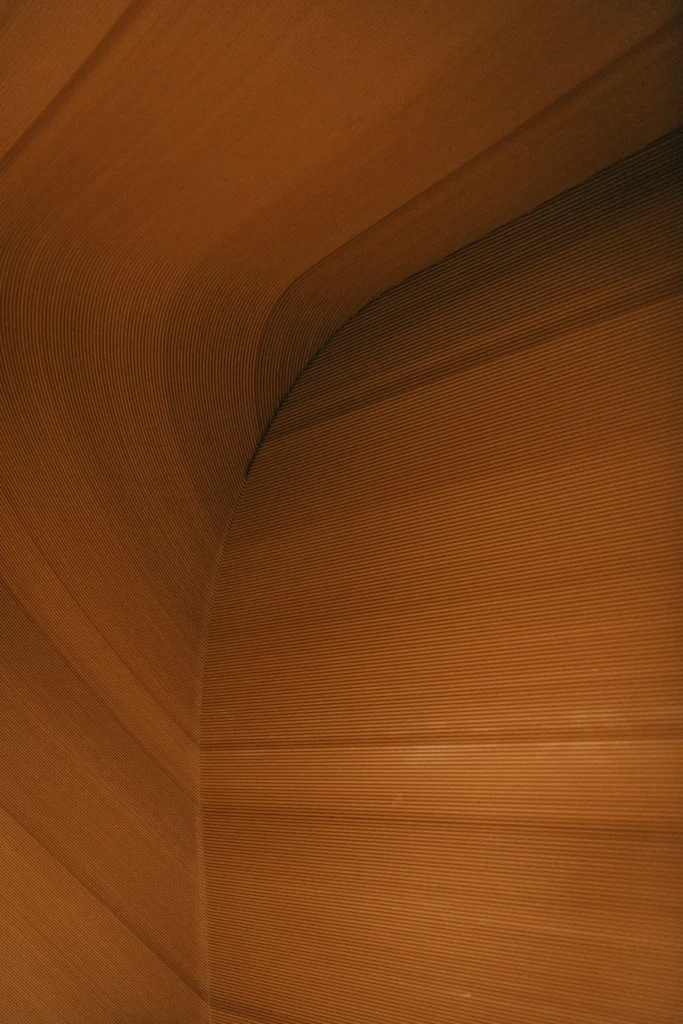
According to the University of Maine, the state’s sawmills produce nearly one million tons of wood residuals every year. Since each 600-square-foot unit requires approximately 10 tons of wood residuals, 100,000 housing units could theoretically be produced every year using just sawmill residuals.
Crushed by negative news?
Sign up for the Reasons to be Cheerful newsletter.
The University of Maine’s Advanced Structures and Composites Center received $3.3 million in funding for this project last year, and its collaboration with Penquis has set out to build a ready-to-live neighborhood with nine 3D-printed homes for people experiencing houselessness. As the team undergoes the final regulatory hurdles, Bird anticipates that houses could be ready to live in as early as this spring.
“The wood fiber material that’s used in the mix is essentially waste wood here in Maine,” says Jason Bird. Courtesy of the University of Maine ASCC
Once this pilot project is completed and the team at the University of Maine reaches full commercial capacity, Bird says the team will be able to print a home in as little as two days.
“That would include the shell of the house — the roof, walls, floors system,” Bird explains. “Long-term [infrastructure projects] could include cabinets, countertops, bath fixtures. And what gets me so excited about this project is that the technology isn’t just solving a local problem, it could be replicated around the world.”
Dr. Habib Dagher, executive director of the Advanced Structures and Composites Center, confirms that the technology is intended to be widely replicated.
“The goal of this research is to create a system for constructing homes that alleviates strains on the supply chain and addresses labor shortages, while providing economical and sustainable housing,” says Dr. Dagher. “This technology can be used anywhere in the world that has access to bio-based raw materials. We are focused on scaling up production technology to drive down costs and increase availability.”
And after enduring a year of extreme weather in Maine, with sensors reporting temperatures ranging from 1 degree to 105 degrees Fahrenheit, BioHome3D met all sustainability, strength, and durability requirements for US building codes, as well as the design requirements of the International Code Council code.
“Doing this project in a place like Maine, which has some of the most extreme temperatures in the continental US, is vital because it can prove that this material can endure huge temperature swings,” says Sarah Goehrke, founder of Additive Integrity, a consulting service that focuses on the examination and sustainable acceleration of industrial 3D printing. “The fact that BioHome3D survived for a year is very important proof going forward.”
3D-printed housing development planned for Rogers
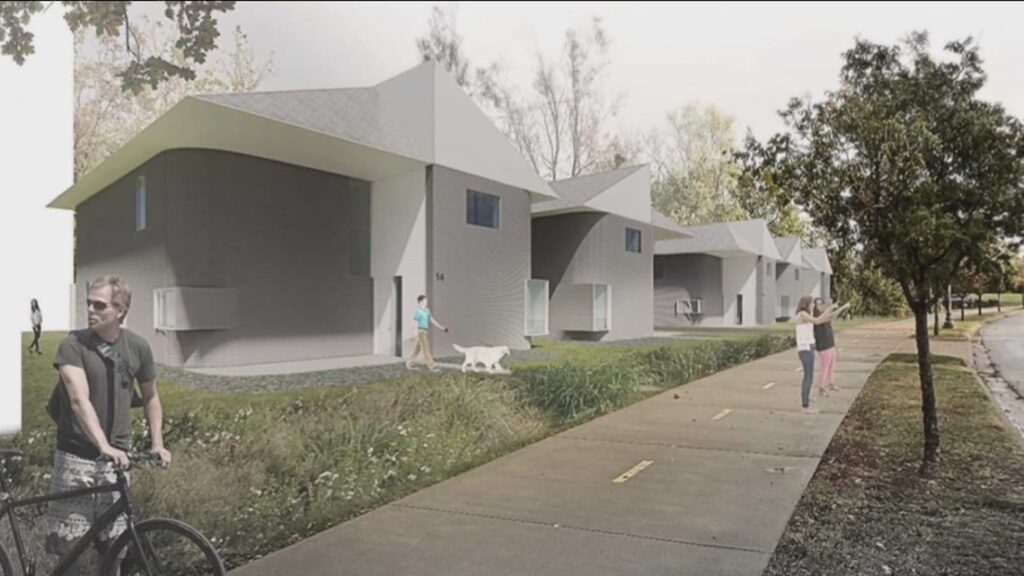
Rogers City Council sold $50,000 worth of land to the Northwest Arkansas Council to head this project.
ROGERS, Ark. — The Rogers City Council voted Tuesday night to sell a piece of land to the Northwest Arkansas Council subgroup “Groundwork” to build the first 3D-printed homes in the state.
The city voted to sell the land on South 1st St. for $50,000 on Jan. 23. These homes will be sold to buyers whose annual income does not exceed 80% of the area median income. Right now, the group plans for four to five duplexes on the site that are two stories.
“One of our goals is for this housing to provide some level of affordability with some proximity to one of our downtown’s. So, in theory, someone could potentially live there, work at a coffee shop, or work at one of the restaurants in Downtown Rogers and have a short walk or a short bike ride or short commute to and from work,” Duke McLarty, Executive Director for Groundwork, said.
McLarty said things like plumbing and electrical will be installed in these houses in a traditional manner, but the walls will be made out of concrete.
“Where the 3D printing part comes in is essentially the outside walls. A robot will show up on site, it has an arm, and concrete comes out of this arm in a way that almost looks like soft serve ice cream. It’s layered on top of each other to build those walls,” McLarty said.
One of the organization’s goals for this development is to show that housing can be affordably produced using these technologies and be a blueprint for similar projects in the area.
“Studies have shown that they’re 30% more energy efficient. It’s very resilient to extreme weather. It doesn’t rot. There’s no risk of termites there’s no risk of water damage,” McLarty said. “This is really going to be an educational journey that the City of Rogers is proving to be a great partner on. We’re going to bring building officials and fire officials from not just Arkansas, but throughout the heartland, to come here, see this and experience it at different stages.”
The first-of-its-kind project has officials for the city excited and hopeful, as they see the need.
“We’ve put a lot of work into making Rogers as developer friendly as we can be for affordable housing projects. And we’re talking about workforce housing projects that so many of our citizens need,” John McCurdy, Director of Community Development for the City of Rogers, said.
“The more that we can have people who live close to where they work, and where they spend their money, the fewer people on the streets, and I mean, it’s just it’s a win-win for everybody,” McCurdy said.
McLarty said they’re hoping to break ground on the development by late spring or early summer and hopefully have residents move in by the end of the year.
[embedded content]
Watch 5NEWS on YouTube.
Download the 5NEWS app on your smartphone:
Stream 5NEWS 24/7 on the 5+ app: How to watch the 5+ app on your streaming device
To report a typo or grammatical error, please email KFSMDigitalTeam@tegna.com and detail which story you’re referring to.
Why this 3D-printed house could be a gamechanger
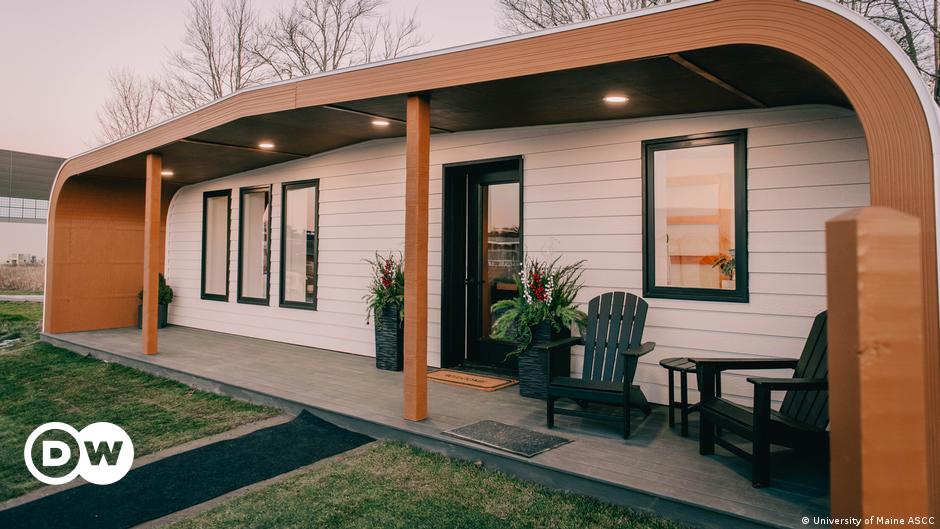
In this episode of Living Planet, we’re delving into a story about a remarkable 3D-printed house in the US state of Maine. It was made of 100% bio-based materials, which is good news for the construction sector, which accounted for nearly 40% of energy and cross-related CO2 emissions in 2021, according to the United Nation’s Environment Program.But this story is about much more than technology and innovation. Maine is one of the US states that has become a magnet for Americans searching for affordable houses in the wake of the pandemic. It’s also a state that’s seen its once booming paper industry dwindle to a handful of papermills, leaving a glut of sawdust from the timber industry with nowhere to go.
And as it turns out, a research team at the University of Maine was working on another project that turned out to be part of the solution to both of these problems.
In this episode, we speak with Mark Wiesendanger, director of development at MaineHousing; Habib Dagher, the executive director of the Advances Structures and Composites Center at the University of Maine; and Dr. Halil Tekinalp of the Department of Energy’s Oak Ridge National Laboratory.
You can read more about BioHome 3D here.
Press Release – Game-Changer in Additive Manufacturing: Mixed on Site Carbon Neutral Alternative to Cement Unveiled
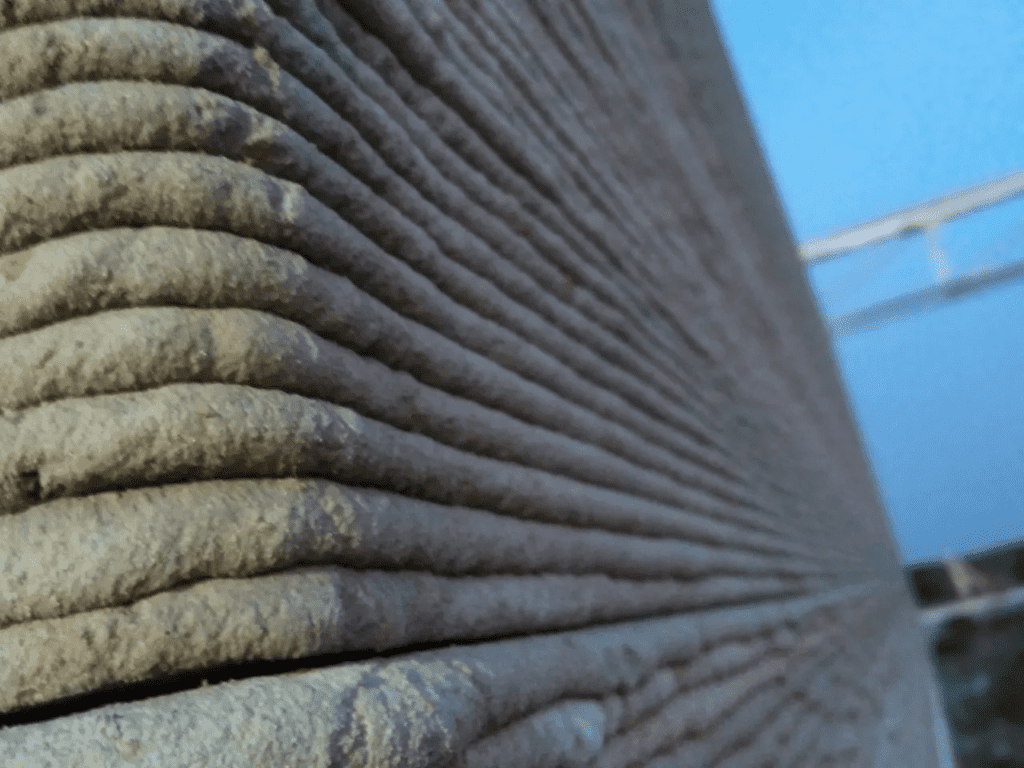
10/07/2023: Additive manufacturing company, Hive3D Builders, has developed a remarkable mixed on site carbon-neutral and stronger alternative to traditional cement. The printing material, which substitutes the mortar normally used in 3D concrete printing, is able to reduce construction’s CO2 emissions by 93%. Hive3D Builders is currently using this sustainable material to produce over 200 near-net-zero homes. This substance makes the already eco-friendly practice of additive manufacturing even more sustainable and is poised to revolutionize global construction.
Polluting Construction
The construction industry has long grappled with environmental challenges. Traditional concrete production contributes to 8% of global greenhouse gas emissions. 3D concrete printing technology generally has a lower carbon footprint than conventional building methods, mainly due to lower material usage, as well as a lower waste production rate. Along with the eco-friendly technology, additive manufacturing companies often strive to innovatively find sustainable solutions. An example of this is the manufacturer of Hive3D Builders’ printers, CyBe Construction. In the early days of 3D concrete printing, CyBe developed its own eco-friendly building material by using material that has up to 32% less CO2 emissions. Additionally, the material has the possibility to be produced locally.
Carbon-Neutral Material
Hive3D Builders (www.hive3dbuilders.com) take the production of eco-friendly building material one step further. By working with Eco Materials and Green Cement, they managed to develop a low-cost geopolymer cement replacement that has up to 93% less CO2 emissions. Due to geopolymer’s environmentally friendly properties, the substitute for the mortar that 3D concrete printing traditionally uses is almost completely carbon-neutral. Geopolymers have gained attention as a sustainable building material because they require less energy and produce fewer carbon dioxide emissions compared to traditional cement production. They can also utilize industrial waste materials such as fly ash, slag, and mining tailings, reducing the demand for natural resources and providing a solution for waste disposal. By combining this newfound material with the already eco-friendly properties of 3DCP, Hive3D Builders has unlocked tremendous potential for reducing carbon emissions in the building process. The current estimate is a reduction of 93% of the construction’s CO2 emissions. With this tremendous cut in greenhouse emissions, Hive3D Builders is at the forefront of sustainable construction technology.
Superior Strength
The implications of this innovation extend beyond its environmental benefits. Along with its reduction in CO2 emissions, the carbon-neutral material also offers superior strength and durability. This increased adhesion makes it an attractive alternative to traditional cement, offering immense potential for building more resilient structures. The strength of the material can be accredited to the geopolymer’s desirable properties. It is no wonder that geopolymers, oftentimes used as construction materials, were a key component in Hive3D Builders’ material. They exhibit advantages like excellent strength, high durability, and outstanding fire resistance.
Material Costs
3D concrete printing material generally has a significantly higher cost than regular concrete. This is because 3DCP does not use regular cement, but a mortar that dries notably quicker than regular concrete does. CyBe Mortar, for example, sets in three minutes and achieves structural strength in only one hour. This fast drying speed is needed because the bottom layers need to be strong enough to print the rest of the structure on. This special, fast-drying mortar, however, often comes at a higher cost than regular concrete does. Still, 3DCP is generally cheaper than regular construction. The technique has unique cost-saving properties due to a lower material need, as well as less necessary construction workers.
Hive3D Builders’ newly developed material, however, enjoys yet another advantage in this regard. Hive3D developed a unique system to automatically mix the cement replacement onsite with hyper-locally sourced aggregates to lower their material costs exponentially. By creating this system to automatically mix the cement replacement product onsite with locally sourced aggregates, the company is able to lower the cost of its printing mortar to a third of the price of other commercially available printing mortars. This low cost might pave the way for many hesitant construction companies to finally make the switch to 3DCP. The development of this new low-cost, carbon-neutral material is poised to shape the additive manufacturing industry.
Revolutionizing the Construction Industry
One of the main reasons that 3D concrete printing is not as common as you would expect it to be after hearing the advantages, is the fact that construction companies are often hesitant to change their way of working. The construction industry is booming, so big companies in the industry often don’t have the time or need to properly consider new building technologies like 3DCP. When they hear about the technique’s higher material price, they often lose interest, without taking into account the cost savings on other aspects. With Hive3D Builders adding a low material price to the material’s already impressive list of better sustainability and superior strength, the sustainable innovators might be able to convince headstrong construction giants to consider additive manufacturing as a cheaper, faster, and more sustainable alternative to their current construction methods. Using their partner CyBe Construction’s printer and Hive3D Builders’ carbon-neutral material, the company is set out to revolutionize the construction industry on a global scale.
Press Release – Miami Startup, Kind Designs, Leverages 3D Concrete Printing to Rescue our Oceans
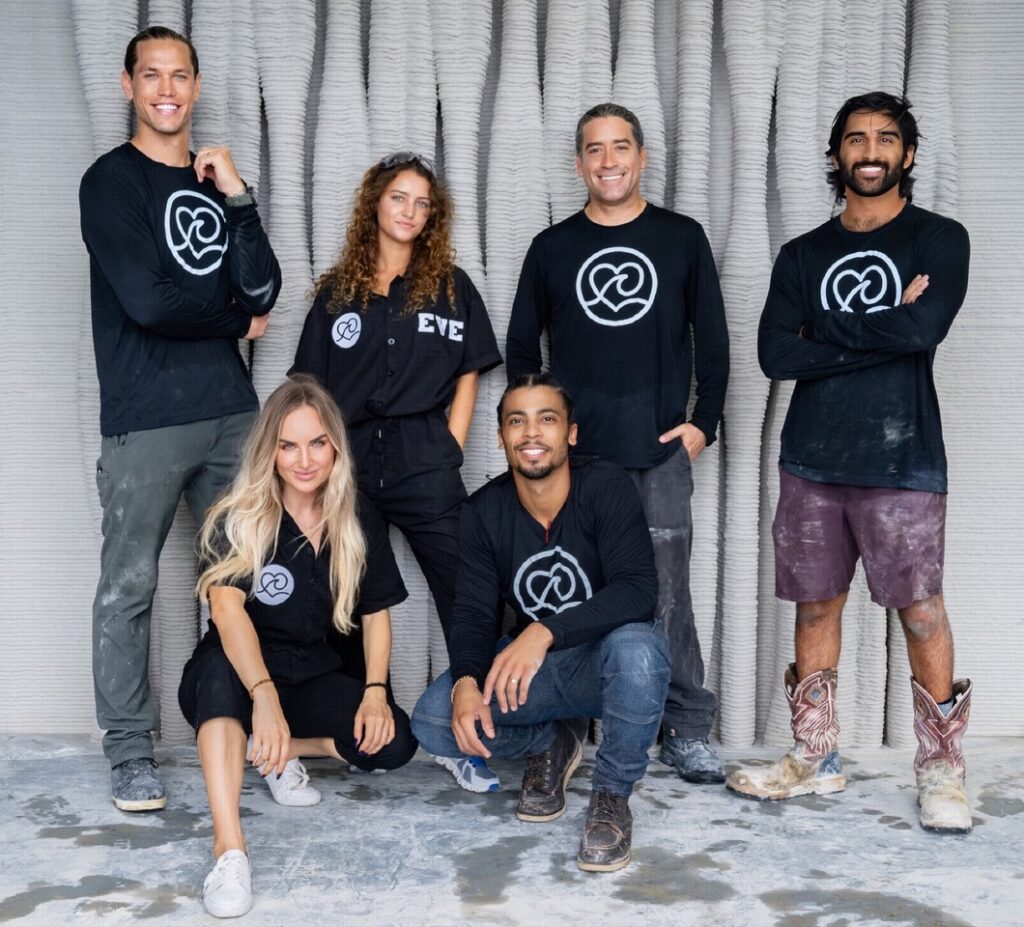
04/10/2023: Miami-based climate-tech startup Kind Designs has the solution for our rising sea levels. Leveraging 3D concrete printing technology as a faster, cheaper, and more sustainable construction method, they will produce Livings Seawalls. These underwater structures protect our shores, improve the ocean’s biodiversity, and monitor water quality.
Miami Startup Sets Out to Rescue our Oceans
The sea levels are rising. The ocean’s water quality is getting worse. Marine biodiversity is decreasing. Coral reefs are facing extinction. All these environmental challenges are threatening our oceans’ wellbeing. One Florida-based climate-tech startup is taking the problem head-on: Kind Designs. Operating from Miami, a city experiencing this issue firsthand, Kind Designs was established to address the challenges posed by the deteriorating state of our oceans. For CEO and founder Anya Freeman, issues related to sea-level rise in Miami became a part of her everyday life. Instead of dwelling on the problem, she decided to seek a remedy. Therefore, Kind Designs was instituted with just that goal: finding a solution to address the challenges faced by our oceans. Their solution? Living Seawalls.
Living Seawalls: Technology Hand in Hand with Nature
Just like ordinary seawalls, Kind Designs’ structures are made to be placed underwater in order to improve the local marine environment. They protect the land from erosion, flooding, and storm surges, and help counteract sea-level rise. However, Kind Designs elevated the concept of seawalls by designing them to include distinctive, nature-like shapes. These Living Seawalls offer support to local marine life, enhancing the ocean’s biodiversity. Their rough texture and curvy design offer shelter for marine life like fish and crustaceans while providing a stable foundation for marine plants to grow on. Additionally, Living Seawalls are embedded with sensors that measure water quality using 15 different parameters, such as pH levels and salinity. Currently, this data needs to be collected manually by Florida counties. However, once these sensors are deployed, they will provide readily available data, saving the state many hours of manual labor.
Affordable, Fast, and Sustainable Production
One of the reasons seawalls aren’t more common is their price tag. These underwater structures are generally quite expensive to produce, so Kind Designs had to find an affordable way to construct them. Having conducted research on cost-efficient construction methods, they opted for 3D concrete printing to create their Living Seawalls. 3D concrete printing is generally seen as a cheaper, faster, and more sustainable alternative to conventional construction. Kind Designs has already proven the fact that it is much faster: using a 3D concrete printer, they manufacture a Living Seawall in under two hours. The hardware, software, and material for 3D printing were provided by CyBe Construction, a Dutch construction company. CyBe, founded in the legacy of a 100-year-old giant in the construction industry, has a decade of experience in 3D concrete printing. They develop their proprietary hardware, software, and material tailored for additive manufacturing. The company was founded with a vision for an improved and more sustainable society, aligning perfectly with Kind Designs’ goal for a better world.
Image: Kind Designs and CyBe Construction team members next to a Living Seawall and a CyBe Robot Crawler
Funding Kind Design’s Journey to Save the Ocean
After their printer was delivered, Kind Designs also received a three-week training from CyBe. With this experience in hand, they could start printing their Living Seawalls. Their production process was kickstarted by a seed funding round, co-led by GOVO Venture Partners, M4 Investing, and the Florida Opportunity Fund. During this funding round, Kind Designs raised a total of $5 million. With these funds, Kind Designs will be able to “protect all coastal cities with Kind’s Living Seawalls and grow far beyond our home state of Florida,” as Anya commented. Specifically, these funds will be applied to speed up their production. Kind Designs had received letters of intent for purchases totaling $4 million; hence, this additional capital to enable faster production was more than welcome. Now that Kind Designs has the proper equipment to make their Living Seawalls and the proper funding to do so efficiently, they are ready to protect America’s coastlines for the better and improve its oceans.
Watch ICON Co-founder and CEO’s Featured Talk at SXSW 2022
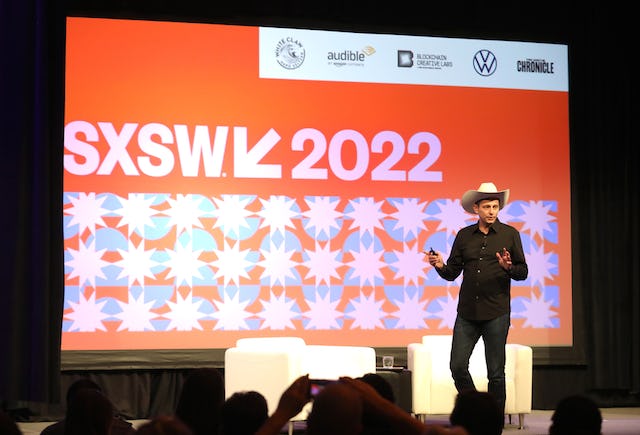
“It’s Time to Build” on ICON’s YouTube channel
We are excited to announce that the SXSW 2022 Featured Talk, “It’s Time To Build” by Jason Ballard, co-founder and CEO of ICON, as well as the subsequent moderated discussion with PBSNewsHour anchor Stephanie Sy is available on ICON’s YouTube channel.
In this inspirational talk, Ballard discusses what ICON is currently doing on Earth, the goal of building one billion homes in our lifetime to end the global housing crisis, and how the answers to problems we face may be found in the work ICON is planning for off-world construction.
[embedded content]
It’s Time to Build
One billion homes. To put a dent in the global housing crisis, we need to build one billion homes in a lifetime and today we simply aren’t solving the problem fast enough. To build the future, we must change the way we design and build for a world that will enhance human happiness and flourishing. The future starts with 3D printing. The technology that can create a more sustainable and beautiful world will be the same technology that helps us become a spacefaring civilization.
Will cities of the future be built by robots and drones? Will humans colonize the Moon and Mars? Ballard’s featured talk “It’s Time to Build” discusses humanity’s future and how architecture, design, robotics and sustainability can be in service to humanity and help us reimagine worlds.
Diego Donamaria/Getty Images for SXSW
PBS NewsHour anchor Stephanie Sy joined Ballard on stage to discuss the future of home construction and dig in deeper on ICON’s past, present and future.
Diego Donamaria/Getty Images for SXSW
Watch Melodie Yashar’s TED Talk: How to Build for Human Life on Mars
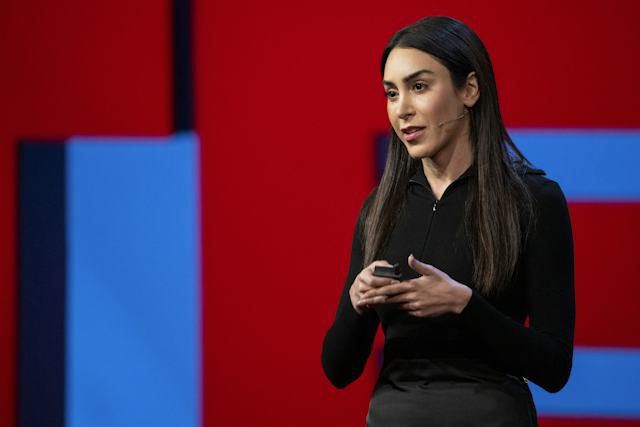
“How to build for human life on Mars”
We are delighted to announce that the TED Talk “How to build for human life on Mars” by Melodie Yashar, Vice President of Building Performance & Design at ICON, is now available for viewing at TED or in the embedded video below.
TED is a global phenomenon that has captivated the hearts and minds of its audience for nearly 40 years by offering unique perspectives on topics that people may or not be familiar with. Since its founding, TED has rapidly increased its global presence by inviting people from different backgrounds to share their interests and expertise with the world. Similar to those who came before her, Melodie was invited to share her passion for space exploration and architecture – with the TED community.
Melodie Yashar, ICON’s Director of Building Design & Performance, delivers her TED Talk. Photo credit: TED / Ryan Lash
Learning to live and work on Mars will be no small feat. During her visionary TED talk, Melodie introduces work to design off-world shelters with autonomous robots and 3D printers and explores how it might help uncover radical solutions to some of the problems troubling humans on Earth today. Melodie underscores the importance of creating an architecture that evolves with the needs of humanity, especially in the midst of climate change and the urban housing shortage.
Melodie Yashar, ICON’s Director of Building Design & Performance, delivers her TED Talk. Photo credit: TED / Ryan Lash
For more video of ICON’s off-world construction work, visit ‘ICON 3D Prints Simulated Mars Surface Habitat at NASA’s Johnson Space Center’
ICON’s House Zero Receives Top Honors in Architizer’s Annual A+ Awards
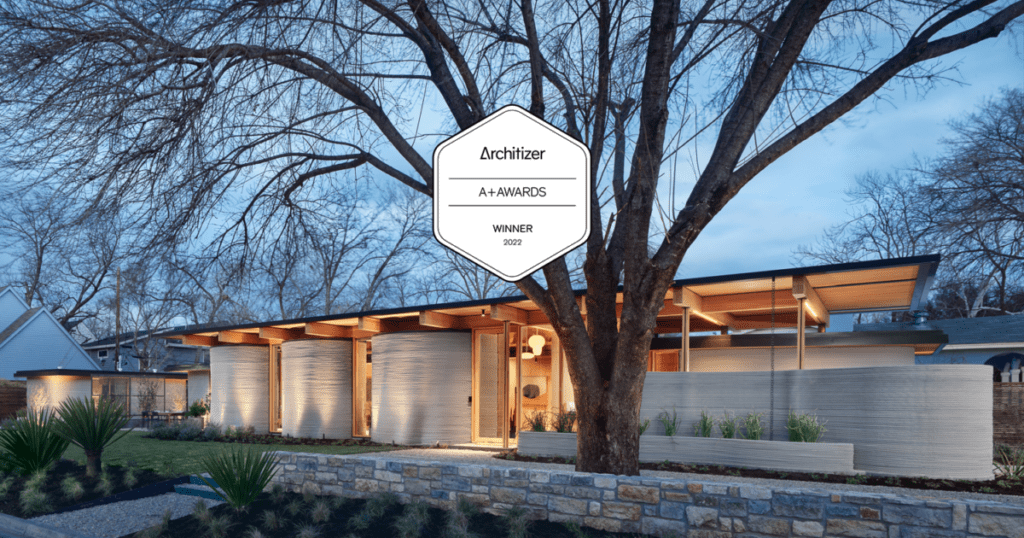
3D-printed home in Austin recognized as one of the world’s best buildings and spaces.
We are ecstatic to share that ICON’s House Zero was selected as the winner of the Architecture +Experimental Design and +New Technology award categories in Architizer’s esteemed A+Awards for 2022. This list bestows honor on firms and companies that have sought to cultivate and advance society’s appreciation of meaningful architecture and design while simultaneously shining a light on the individuals behind these innovative ideas.
Our inclusion in these categories was based on a review by a 250+ member jury along with a round of voting that was open to the public. ICON’s goal of incorporating its noteworthy 3D printing technology and software into the homebuilding process gave them the opportunity to cut back on the time, materials, and costs that are needed to build a traditional home.
House Zero, 3D printed by ICON and designed by Lake|Flato Architects, is ICON’s most innovative home yet, pushing the boundaries of what’s possible with architecture through automated construction only achievable through 3D printing. The 2,000+ sq ft home is the first project in ICON’s Exploration Series and illustrates the development of new design languages and architectural vernaculars created by construction scale 3D printing. By introducing biophilic principles into the design process and taking them to heights that we have never seen before, House Zero was able to revamp modern architecture by breathing new life into the movement and changing the face of the housing landscape as we know it.
Read More at https://architizer.com/projects/house-zero/
Construction and Technology: ICONArchitecture: Lake|Flato ArchitectsStructural Engineer: GNAStructural Engineer: WJEMEP Engineer: Integral GroupLandscape Architect: Word + CarrInterior Design: Lake|Flato Architects + ICONLighting Design Consultant: Studio Lumina
ICON’s House Zero Named to TIME’s List of the Best Inventions of 2022
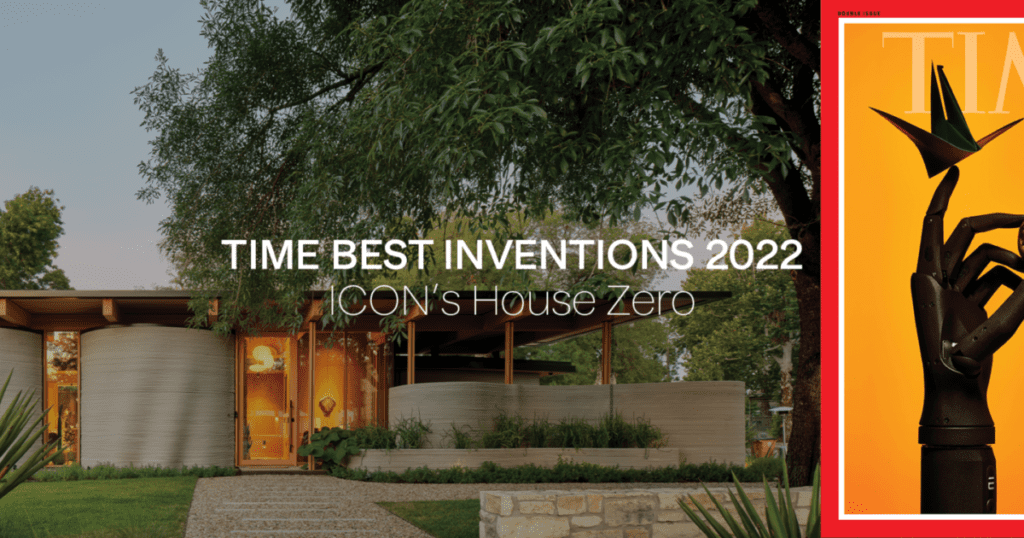
3D-printed Home Designed by Lake|Flato Architects joins ranks of TIME’s Best Inventions featuring extraordinary innovations changing lives
We are honored to share that ICON’s House Zero, designed by Lake|Flato Architects, has been selected as a recipient of TIME’s Best Inventions 2022 in the Design category!
TIME Best Inventions was founded in an effort to bring awareness to the products, software, and services that are solving complex problems in compelling and innovative ways. Each year, thousands of individuals and companies submit their products and services for review across 33 categories ranging from accessibility, connectivity, and apps & software to wellness, beauty, and social good. Once submitted, each of these inventions is reviewed extensively by a panel of judges to determine a product’s impact, not only as it relates to the now, but also in regards to how it will hold up in the future. House Zero is one of the only residential home projects to ever receive this prestigious award.
House Zero’s inclusion on this esteemed list is a cherished stepping stone for ICON as it underscores ICON’s mission of putting robotics, software and advanced materials in service to humanity. Using innovative technologies in the form of the next-generation Vulcan construction system enabled ICON to build a home that was optimized specifically for 3D printing. The future of homebuilding is here.
To view ICON’s profile, visit TIME.
First on site 3D printed house in California

The 1,200 SF (112 m2) house was 3D printed with locally made real concrete mixed on site and erected in the area of Redding, Northern California which lost 1,100 houses in the 2018 wildfires The one-story house is 8 feet tall, with cavity concrete walls each of 50 mm and was permitted according to the […]
ICON and Lennar to Build Largest Neighborhood of 3D-printed Homes…

Innovative 100-home Community Breaks Ground in Austin Area in 2022
Lennar, one of the nation’s leading homebuilders, and ICON, a construction technologies company pioneering large-scale 3D printing, today announced a commitment to build the largest community of 3D-printed homes to date using ICON’s innovative robotics, software and advanced materials. Breaking ground in 2022, the 100-home community will be codesigned by the acclaimed architecture firm, BIG-Bjarke Ingels Group.
The announcement deepens a relationship that began with Lennar’s investment in Austin-based ICON’s recent $207-million financing round and offers a promising path toward delivering affordable, technology-driven homes that meet rising demand.
“Labor and material shortages are two of the biggest factors pushing the dream of home ownership out of reach for many American families,” said Eric Feder, President of LENX. “Lennar has always expanded the boundaries of technological innovation to keep quality homes affordable and 3D printing is an immensely encouraging approach. We are excited to collaborate with ICON to develop solutions to emerging challenges in the coming years.”
ICON’s 3D printing technology produces resilient, energy-efficient homes faster than conventional construction methods with less waste and more design freedom – keeping construction projects on schedule and on budget. Designed and engineered from the ground up for volume 3D printing of homes with precision and speed, ICON’s Vulcan construction system can deliver homes and structures up to 3,000 square feet that are built to the International Building Code (IBC) structural code standard and expected to last as long or longer than standard Concrete Masonry Unit (CMU) built homes. ICON’s proprietary wall system and advanced materials are stronger and longer-lasting than traditional building materials and provide safer, more resilient homes that are designed to withstand extreme weather, greatly reduce the impact of natural disasters, and be printed at high speeds and at scale.
“ICON exists as a response to the global housing crisis and to put our technology in service to the world,” said ICON co-founder and CEO Jason Ballard. “Construction-scale 3D printing not only delivers higher-quality homes faster and more affordably, but fleets of printers can change the way that entire communities are built for the better. The United States faces a deficit of approximately 5 million new homes, so there is a profound need to swiftly increase supply without compromising quality, beauty, or sustainability and that is exactly the strength of our technology. It is an honor and a huge milestone for ICON to partner with Lennar, an elite top-tier homebuilder with a commitment to innovation. We believe this will be a watershed moment in the history of community-scale development and the future breaking into the present.”
“Additive manufacturing has the potential to revolutionize the built environment as it gets adopted by the industry at scale,” said Martin Voelkle, Partner, BIG-Bjarke Ingels Group. “By partnering with ICON and Lennar, we are able to see this new technology roll out to the widest possible audience. The 3D-printed architecture and the photovoltaic roofs are innovations that are significant steps towards reducing waste in the construction process, as well as towards making our homes more resilient, sustainable, and energy self-sufficient.”
Lennar’s investment in ICON’s Series B financing round in August was facilitated by LENX, which drives a focused strategy within Lennar to integrate technology solutions across the homebuilding industry. With a clearly defined strategy of investing in technology companies directly adjacent to Lennar’s core homebuilding operations and a disciplined investment process, LENX provides hands-on mentorship and guidance from senior leaders of Lennar’s management team and a marquee opportunity to provide products and technology to Lennar customers, allowing portfolio companies to scale at an unprecedented pace.
ICON Unveils “House Zero” and Announces 2022 SXSW Activations
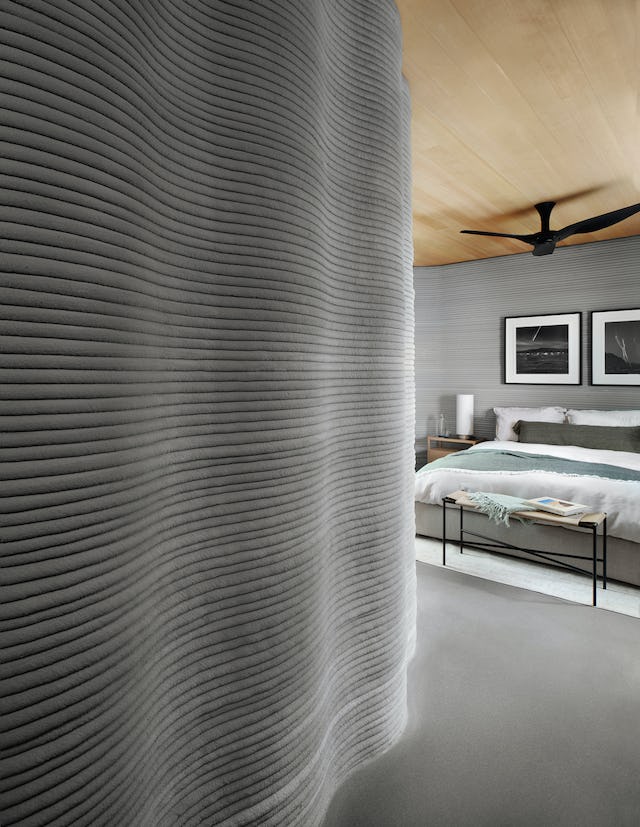
New 3D-printed Home Pushes the Boundaries of Resilient and Sustainable Architecture and Design; Official SXSW Event Tours of ICON’s “House Zero” Revealed for March 13-14, 2022
Photo: Casey Dunn
AUSTIN, TX, March 2, 2022 – ICON, the leader of advanced construction technologies pioneering large-scale 3D printing, today unveiled its newest 3D-printed home, “House Zero” in Austin, Texas. House Zero is the first in what ICON hopes will be an entirely new genre of homes that are specifically designed to utilize opportunities created by 3D printing. For this initial project in ICON’s “Exploration Series,” the team partnered with the award-winning Texas firm, Lake|Flato Architects.
[embedded content]
As an official SXSW partner, ICON will open the doors to “House Zero” for tours March 13-14, 2022 from 9am – 6pm (badge holders will have priority entrance). Sign up today for a tour of the world’s most beautiful 3D-printed home that illustrates the future of homebuilding at https://bit.ly/Tour_ICONHouseZero.
Photo: Casey Dunn
ICON co-founder and CEO, Jason Ballard, will also be delivering a featured talk at SXSW 2022 discussing the role robotics, architecture, materials science will play in solving many of humanity’s current challenges such as housing affordability, community health, sustainability, climate resiliency, and human potential. Moderated by PBS NewsHour correspondent and PBS NewsHour West anchor, Stephanie Sy, the featured session, “It’s Time to Build: a Conversation with Jason Ballard,” will take place on March 15, 2022 at 2:30pm at Hilton Austin Downtown in Salon H. Find out more — > https://bit.ly/SXSW_ICON
_ _ _ _
ICON’s House Zero
Located in East Austin, “House Zero,” was 3D printed by ICON’s next-gen Vulcan construction system and designed by Lake|Flato, known for their sustainable designs. Blending mid-century modernist ranch house aesthetics, the home features an elevated architectural and energy efficient design that highlights the benefits of resiliency and sustainability, with the digital possibilities of additive construction.
Photo: Casey Dunn
“House Zero is ground zero for the emergence of entirely new design languages and architectural vernaculars that will use robotic construction to deliver the things we need most from our housing: comfort, beauty, dignity, sustainability, attainability, and hope,” said Jason Ballard, co-founder and CEO of ICON. “Houses like this are only possible with 3D printing, and this is the new standard of what 3D printing can mean for the world. My hope is that this home will provoke architects, developers, builders, and homeowners to dream alongside ICON about the exciting and hopeful future that robotic construction, and specifically 3D printing, makes possible. The housing of our future must be different from the housing we have known.”
The innovative home, a 2,000+ sq-ft, 3 bedroom/2.5 bath home and a 350 sq-ft, a 1 bedroom/1 bath accessory dwelling unit, features ICON’s resilient 3D-printed wall system, which replaces a building system traditionally made up of multiple steps saving time, waste and cost. The walls of the home are made with a proprietary cementitious-based material, “Lavacrete,” insulation, and steel for reinforcing. Lavacrete provides thermal mass that slows heat transfer into the home and the combination of thermal mass, increased insulation, and an airtight wall increases the energy efficiency and reduces lifecycle costs.
Photo: Casey Dunn
Biophilic principles—the way that humans connect with nature and nature-inspired compositions —are behind much of “House Zero’s” design and best accomplished using ICON’s next-generation 3D-printing technology. The curved walls create structurally efficient self-stability, while rounded corners allow for softer, more naturalistic circulation routes throughout the home. Doorways and windows were strategically placed to accentuate accompanying landscapes; eastern-facing high clerestory windows illuminate the living room with soft, yet dynamic sunlight, minimizing the need for electrical lighting throughout the day.
“The 3D-printed wall design and its inherent biophilic quality conveys an ordered, yet non-rigid pattern invoking a rooted and timeless sense of natural refuge,” said Lewis McNeel, Associate Partner, Lake|Flato.
Photo: Casey Dunn
“While the organic nature of the 3D-printed concrete and curved walls are new design languages for us, House Zero was still entirely in line with the natural connections we seek in our architecture,” said Ashley Heeren, Associate, Lake|Flato. “The home expresses our shared passions for craft and performance in an inviting and comfortable family home constructed through a totally new way of building. It’s been a thrill for our team to work with ICON on such an innovative home design and be a part of the future of homebuilding.”
ICON continues to set new standards for delivering resilient, dignified housing at high-speed and lower cost. Raising $451 million to date in funding, ICON has delivered communities of 3D-printed homes in the U.S. and internationally and forged partnerships with world-renowned architects, builders and housing organizations missionally aligned to shift the paradigm of homebuilding. In fall 2020, ICON was awarded a research contract through the Air Force, which included funding from NASA to begin research and development of an off-world construction system planned to support future exploration of the Moon and beyond.
Photo: Casey Dunn
About ICON
ICON develops advanced construction technologies that advance humanity. Using proprietary 3D printing robotics, software and advanced materials, ICON is shifting the paradigm of homebuilding on Earth and beyond. For more information visit www.iconbuild.com or follow the conversation on Instagram, Twitter, Facebook, YouTube (@ICON3DTech).
About Lake|Flato
Established in 1984, Lake|Flato designs buildings that respond to the culture and climate of each unique place. Lake|Flato believes in creating environments that enrich communities and nurture life. In collaboration with clients, Lake|Flato creates buildings that are tactile and modern, environmentally responsible and authentic, artful and crafted. Lake|Flato’s work has received wide critical acclaim in more than 300 international, national and regional awards, including the American Institute of Architects Firm of the Year Award in 2004 and 13 Top Ten Green Project Awards from the AIA Committee on the Environment. Lake|Flato placed 1st in Architect Magazine’s 2019 Top 50, an annual ranking of the best U.S. firms, and was named one of the Ten Most Innovative Architecture Firms in the World by Fast Company. For more information visit https://www.lakeflato.com/.
ICON and Lennar Announce Community of 3D-printed Homes is Now…

Reservations Begin in 2023 for the 100-home Community Co-designed by BIG-Bjarke Ingels Group
GEORGETOWN, TX – November 10, 2022 – ICON, the leader of advanced construction technologies pioneering large-scale 3D printing, and Lennar, one of the nation’s leading homebuilders, announced today that construction is underway on the largest community of 3D-printed homes and reservations will begin in 2023.
GET ON THE LIST
[embedded content]
Situated north of Austin in the city of Georgetown’s master-planned community of Wolf Ranch by Hillwood Communities, a Perot company, the 100-home community combines innovative robotics, software and advanced materials to create homes that are technologically advanced, environmentally sustainable and architecturally striking. Each Lennar home in Wolf Ranch is co-designed by the renowned architectural firm BIG-Bjarke Ingels Group. Prices are anticipated to start from the mid-$400,000s.
“We are very pleased to partner with ICON and BIG in building a first-of-its-kind, printed home community that combines innovative designs with sustainable features at an affordable price,” said Stuart Miller, Executive Chairman of Lennar. “Given the housing shortage that persists across the country, it has never been more important to innovate in order to find new methods of construction that will enable greater design flexibility and greater production at affordable prices.”Blending contemporary Texas ranch style aesthetics, the community of 3D-printed homes features elevated architectural and energy-efficient designs that highlight the benefits of resiliency and sustainability with the digital possibilities of additive construction. Delivered at speed and at scale using a fleet of ICON’s Vulcan robotic construction systems, software and advanced materials, each home’s full wall system – including interior and exterior walls – are produced with less waste and with more design freedom.
“For the first time in the history of the world, what we’re witnessing here is a fleet of robots building an entire community of homes. And not just any homes, homes that are better in every way… better design, higher strength, higher energy performance and comfort, and increased resiliency,” said Jason Ballard, co-founder and CEO, ICON. “In the future, I believe robots and drones will build entire neighborhoods, towns, and cities, and we’ll look back at Lennar’s Wolf Ranch community as the place where robotic construction at scale began. We still have a long way to go, but I believe this marks a very exciting and hopeful turn in the way we address housing issues in the world.”
Construction at Wolf Ranch deepens a relationship that began with Lennar’s investment in Austin-based ICON’s series B financing round and offers a promising path toward an alternate method of delivering technology-driven homes that meet rising demand in desirable communities. In addition to state-of-the-art homes, Lennar homeowners in Wolf Ranch can enjoy all of the amenities offered in tree-covered hill country – including pools, recreational trails and parks within easy access of downtown Georgetown and a short drive to Austin.
Lennar’s investments are facilitated by LENX, which drives a focused strategy within Lennar to integrate technology solutions across the homebuilding industry. With a clearly defined strategy of investing in technology companies directly adjacent to Lennar’s core homebuilding operations and a disciplined investment process, LENX provides hands-on mentorship and guidance from senior leaders of Lennar’s management team and a marquee opportunity to provide products and technology to Lennar customers, allowing portfolio companies to scale at an unprecedented pace.
The community will offer eight stunning floorplans with 24 unique elevations ranging from 1,574 to 2,112 square feet of thoughtful living space. The homes will offer three to four bedrooms and two to three baths. All homes will be powered by the sun with rooftop solar panels and will feature components from Lennar’s Connected Home package including a Ring Video Doorbell Pro, a Schlage Encode™ Smart WiFi deadbolt and a Honeywell Home T6 Pro WiFi smart thermostat. Plus, each home will come equipped with the Wolf Ranch security package.
“We are excited to welcome Lennar and ICON’s cutting-edge home construction technology to Georgetown,” Georgetown Mayor Josh Schroeder said. “The Georgetown community prides itself on honoring our past and innovating for our future, and we are eager to see the future being built right here.”
“Hillwood Communities is honored that ICON and Lennar chose Wolf Ranch to launch this exciting initiative and we look forward to the positive impact it will bring to the homebuilding industry,” said Fred Balda, president of Hillwood Communities. “This innovative approach aligns with Hillwood’s long history of elevated design and the thoughtful development approach we take to ensure a higher standard of living for the residents of our communities.”
Reservations begin in 2023. Interested homebuyers can join the interest list by clicking here.
About Lennar Corporation
Lennar Corporation, founded in 1954, is one of the nation’s leading builders of quality homes for all generations. Lennar builds affordable, move-up and active adult homes primarily under the Lennar brand name. Lennar’s Financial Services segment provides mortgage financing, title and closing services primarily for buyers of Lennar’s homes and, through LMF Commercial, originates mortgage loans secured primarily by commercial real estate properties throughout the United States. Lennar’s Multifamily segment is a nationwide developer of high-quality multifamily rental properties. LENX drives Lennar’s technology, innovation and strategic investments. For more information about Lennar, please visit www.lennar.com.
About ICON
ICON develops advanced construction technologies that advance humanity. Using proprietary 3D printing robotics, software and advanced materials, ICON is shifting the paradigm of homebuilding on Earth and beyond. For more information visit www.iconbuild.com or follow the conversation on Instagram, Twitter, Facebook, YouTube (@ICON3DTech).
About BIG – Bjarke Ingels Group
BIG-Bjarke Ingels Group is a Copenhagen, New York, London, Barcelona, and Shenzhen-based group of architects, designers, urbanists, landscape professionals, interior and product designers, researchers, and inventors. Led by Bjarke Ingels, the studio is currently involved in projects throughout Europe, the Americas, Asia, and the Middle East. BIG’s architecture emerges out of a careful analysis of how contemporary life constantly evolves and changes. BIG believes that by hitting the fertile overlap between pragmatic and utopia, architects can find the freedom to change the surface of our planet, to better fit contemporary life forms.
About Hillwood
Hillwood, a Perot company, is a premier commercial and residential real estate developer, investor and advisor of properties throughout North America and Europe. Through its Communities division, Hillwood has delivered more than 40,000 single-family lots in more than 100 master-planned communities across 13 states and Costa Rica. These communities continue to raise the bar in terms of quality, innovation and the unmistakable sense of community that sets each property apart. Before laying the physical groundwork for any new residential development, Hillwood Communities takes the time to focus on the ideals that draw people together — and the everyday interactions that strengthen those bonds. By purposefully designing its walkways, gathering spaces, and structural amenities to spark spontaneous encounters and foster shared interests, Hillwood Communities believes in the power of community. For more information, please visit http://www.hillwoodcommunities.com.
About the City of Georgetown
Georgetown is a welcoming, vibrant city that has been ranked No. 1 in Southern Living Magazine’s “South’s Best Cities to Live in” and is home to the “Most Beautiful Town Square in Texas.” Georgetown has a rich history, with Victorian storefronts and a cultural district with a wide selection of restaurants, wineries, shops, art galleries, theaters, and museums, as well as Southwestern University, tied for the No. 1 National Liberal Arts College in Texas in the latest U.S. News & World Report ranking. Outdoor recreation includes 40 parks, 16 miles of hiking and cycling trails, and Lake Georgetown. Georgetown is the fastest growing city in the U.S. with a population of more than 50,000.
ICON Launches Global Architecture Competition ‘Initiative 99’ to…

With a $1,000,000 Prize Fund, Pioneer in Robotic Construction Calls on Architecture Community to Design Homes That Can Be Built for Under $99kLearn More at www.Initiative99.com
AUSTIN, TX, MARCH 15, 2023 – ICON, the global leader in construction-scale 3D printing, has announced Initiative 99, a global architecture competition aimed at designing accessible, beautiful, and dignified homes that can be built for under $99,000.
Registration for the competition opens in the summer of 2023 and architects from all over the world including firms, individuals, and university students are encouraged to participate. The multi-phase, year-long competition offers a total prize purse of $1 million (USD). ICON has committed to building a selection of the winning designs at multiple locations to be announced in the future.
“We need a moonshot for affordable housing, and I believe Initiative 99 will be the most important architectural competition in history,” said Jason Ballard, co-founder and CEO ICON. “The current affordable housing landscape seems to have been designed and built without taking beauty, aesthetics, comfort, sustainability, and resiliency as serious requirements. It’s time we attack this problem just as energetically as we’ve addressed other human challenges in the past.”
The vision of a home with construction costs under $99,000 has inspired and motivated city planners, developers, government officials and non-profit organizations for decades. And yet clear barriers subsist for realizing a truly affordable housing prototype at scale within communities that need them most. The current approach to homebuilding and addressing the global housing crisis is not working as more than 1.2 billion globally lack adequate shelter. Initiative 99 exists to unite the global architectural, design, and building community in a shared mission to build a better future for those that need it most.
Ballard continued, “With Initiative 99, we are changing the way that we talk about affordable housing. When we talk about affordable housing, the conversation is often depressing and so are the results. Our goal is that Initiative 99 would in turn create the conditions for affordable housing to be something hopeful, optimistic and exciting, and furthermore catalyzes the building of some really incredible affordable homes that just years ago would not have even been possible. The future could be a wonder, but we have to all work together to make it so.”
The Initiative 99 jury will consist of an expert panel of architectural practitioners, academic leaders, policy makers and non-profit organizations committed to realizing affordable housing solutions including: Michelle Addington, Architect and Dean of Architecture at University of Texas, Austin; Lucia Athens, Chief Sustainability Officer, City of Austin; Brett Hagler, CEO and Co-Founder, New Story; Bjarke Ingels, Founder and Creative Director of Bjarke Ingels Group; Michael McDaniel, Director of Design, ICON; Melodie Yashar, Vice President of Building Design and Performance, ICON, and others to be announced
Registration for the competition opens Summer 2023 – sign up to learn more at www.Initiative99.com
As an official 2023 SXSW partner, ICON will be hosting a featured program, ‘A Moonshot for Affordable Housing’ on March 15, 2023 at 2:30pm at The Long Center for the Performing Arts, 701 W Riverside Dr. Austin, TX, with an official SXSW special event and concert to follow. Jason Ballard will be joined by Bjarke Ingels (BIG), Michelle Addington (UT School of Architecture) and Sarah Satterlee (Mobile Loaves & Fishes) for a dynamic conversation as they ignite a call to action on the future of accessible housing and share visions that could change the way we design and build for our global community. More details can be found at https://iconofficialsxsw2023.splashthat.com/
About ICON
ICON develops advanced construction technologies that advance humanity. Using proprietary 3D printing robotics, software and advanced materials, ICON is shifting the paradigm of homebuilding on Earth and beyond. For more information visit www.iconbuild.com or follow the conversation on Instagram, Twitter, Facebook, YouTube (@ICON3DTech).
ICON To Develop Lunar Surface Construction System With $57.2 Million…

SBIR Phase III Contract Furthers ICON’s Space-based Construction Technology Developments & Will Target Humanity’s First-ever Construction on Another Planetary Body
AUSTIN, TX, November 29, 2022 – ICON, a leader in advanced construction technologies and large-scale 3D printing, announced today that it has received a contract awarded under Phase III of NASA’s Small Business Innovation Research (SBIR) program. The nearly $60 million contract builds upon previous NASA and Department of Defense funding for ICON’s Project Olympus to research and develop space-based construction systems to support planned exploration of the Moon and beyond. ICON’s Olympus system is intended to be a multi-purpose construction system primarily using local Lunar and Martian resources as building materials to further the efforts of NASA as well as commercial organizations to establish a sustained lunar presence. [embedded content]
“To change the space exploration paradigm from ‘there and back again’ to ‘there to stay,’ we’re going to need robust, resilient, and broadly capable systems that can use the local resources of the Moon and other planetary bodies. We’re pleased that our research and engineering to-date has demonstrated that such systems are indeed possible, and we look forward to now making that possibility a reality,” said Jason Ballard, ICON co-founder and CEO. “The final deliverable of this contract will be humanity’s first construction on another world, and that is going to be a pretty special achievement.”
Highlighting the commonalities between advanced construction on earth and in space, ICON will continue to pioneer methods and technologies to solve some of the most vexing construction challenges facing our species from affordable housing to living on other planets. ICON’s selection for this award is a vote of confidence in the young, growing company and its mission to revolutionize the construction industry both on Earth and off.
In support of NASA’s Artemis program, ICON plans to bring its advanced hardware and software into space via a lunar gravity simulation flight. ICON also intends to work with lunar regolith samples brought back from Apollo missions and various regolith simulants to determine their mechanical behavior in simulated lunar gravity. These findings will yield results that inform future lunar construction approaches for the broader space community, including for critical infrastructure like landing pads, blast shields and roads. This technology will help to establish the critical infrastructure necessary for a sustainable lunar economy including, eventually, longer term lunar habitation.
“In order to explore other worlds, we need innovative new technologies adapted to those environments and our exploration needs,” said Niki Werkheiser, director of technology maturation in NASA’s Space Technology Mission Directorate. “Pushing this development forward with our commercial partners will create the capabilities we need for future missions.”ICON’s vision for Olympus, the multi-purpose ISRU-based lunar construction system.
NASA has signaled that, through the Artemis program, the Moon will be the first off-Earth site for sustainable surface exploration. Building a sustainable presence on the Moon requires more than rockets. For a sustained lunar presence, robust infrastructure will need to be built on the Moon that provide better thermal, radiation, and micrometeorite protection. ICON’s development plans are following a “live off the land” approach by prioritizing the use of in-situ / native materials found on the Moon. From landing pads to habitats, these collective efforts are driven by the need to make humanity a spacefaring civilization.
In 2021, ICON was also awarded a subcontract through Jacobs supporting NASA’s Space Technology Mission Directorate (STMD) as part of NASA’s Crew Health and Performance Exploration Analog (CHAPEA) and delivered the world’s first and only simulated Mars surface 3D-printed habitat. Designed by architecture firm BIG-Bjarke Ingels Group, Mars Dune Alpha is located at NASA’s Johnson Space Center and will aid in long-duration science missions.
Known for its advanced 3D printing technology for homebuilding on Earth, ICON began its journey to transform construction with the delivery of the first, permitted 3D-printed home in the U.S. in 2018. Since then, the team has delivered communities of 3D-printed homes in the U.S. and Mexico and barracks for women and men who serve with the U.S. Army and Air Force, and the Texas Military Department. ICON’s proprietary Vulcan technology produces resilient, energy-efficient homes faster than conventional construction methods with less waste and more design freedom.
For more on ICON’s off-world construction and space-based technology advancements, visit www.iconbuild.com.
About ICON
ICON develops advanced construction technologies that advance humanity. Using proprietary 3D printing robotics, software and advanced materials, ICON is shifting the paradigm of homebuilding on Earth and beyond. For more information visit www.iconbuild.com or follow the conversation on Instagram, Twitter, Facebook and YouTube (@ICON3DTech).
WORLD’S LARGEST 3D PRINTED BUILDING COMPLETED

Florida-based Printed Farms achieves a groundbreaking feat by completing the printing of the world’s largest 3D printed building, a luxury horse barn, using COBOD’s BOD2 construction 3D printer, marking another record for the world’s most used 3D printer. This unique structure has a total floor area of +10,100 SF / ~940 m2, almost 50% larger […]
LTG Makes 3D Printed Communities Reality in Black Buffalo Partnership
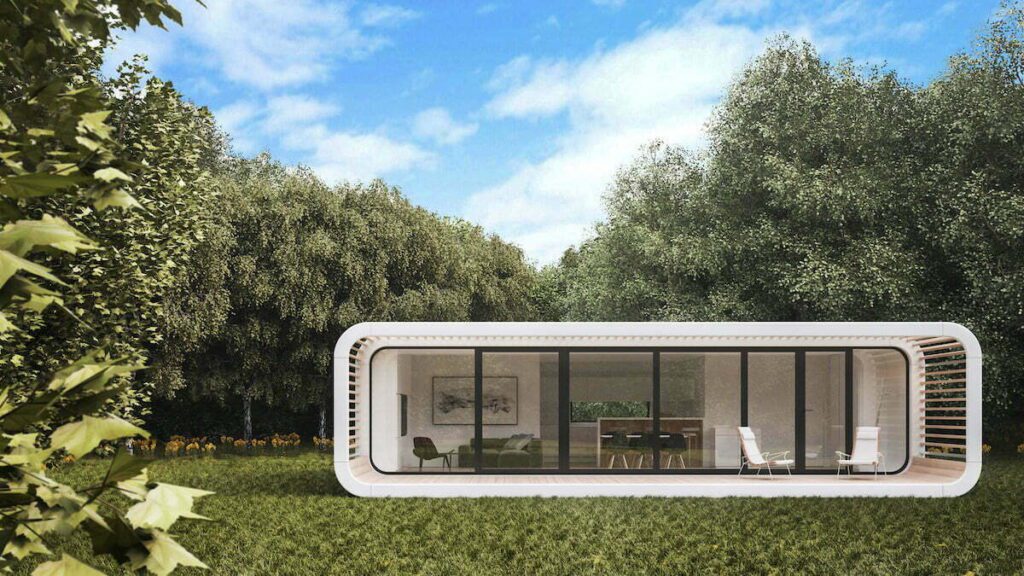
NEW YORK and HAMBURG, Germany, Sept. 16, 2020 /PRNewswire/ — LTG Lofts to go, and Black Buffalo 3D Corporation, A Big Sun Holdings Group company and member of Hyundai BS&C family of companies today announced a strategic partnership to advance production, distribution and availability of 3D printed mobile housing and commercial spaces across the globe.
LTG’s flagship offering, coodo, is a functional, flexible and mobile modular structure used for holiday, living or working. It sets itself apart from traditional pre-fabricated buildings with its contemporary and breathtakingly beautiful patented design. Since 2012, LTG production partners have created white (aluminum/steel) and grey (wood) coodos serving as sustainable resorts and residences, working spaces and stunning booths for events. This partnership increases the availability of coodos and will help bring a new offering— tredee inspired by 3D print innovation—to market.
Black Buffalo will supply 3D construction printers—invented by Mr. Dong-won Shin, CEO of HISYS, a subsidiary of Hyundai BS&C- along with cement “ink” to LTG developers. These construction printers will enable 3D printing- yes, printing- of entire communities, facilities and offices onsite in a matter of days. This innovative approach minimizes freight costs, improves sustainability and eliminates logistical challenges associated with traditional construction and precast buildings or production. This is only the beginning of the 3D construction print revolution.
“The goals of LTG Lofts to go and Black Buffalo 3D align perfectly,” says Michael Woods, CEO & COO of Black Buffalo 3D Corporation. “Our 3D printers will bring LTG offerings wherever they are needed.”
Worldwide interest in obtaining coodos continues to grow and this partnership will help increase supply to meet demand while introducing new designs and finishes to appeal to a wide audience.
“In addition to creating beautiful living and working spaces, Lofts to go introduced coodo to maximize usability of remote destinations and available open spaces in residential areas, cities and even rooftops,” expressed Mark Dare Schmiedel, CEO and Founder of LTG. “3D printers will allow us more opportunities to create holiday resorts, housing communities and modular commercial parks without the challenges of navigating offshore production and international business hurdles. We are eager to bring better living to people regardless of economic status, location or level of luxury.”
Follow each company on social media for interactive walkthroughs, live demonstrations and details on global availability.
About coodo/LTG Lofts to goLTG Lofts to go (www.coodo.com) is a PropTech company from Germany that specializes in the development of minimalistic, beautiful and highly functional mobile modules with a patented design that caters to living, lodging, working or play. LTG offers innovative residential, business and event solutions focused on sustainability, flexibility, design and integration of the latest technology.
About Black Buffalo 3D CorporationBlack Buffalo 3D Corporation (http://www.blackbuffalo.io) is the NY based, US for Hyundai BS&C (http://www.hd-bsnc.com), and subsidiary of Big Sun Holdings Group, Inc. Black Buffalo 3D is poised to revolutionize construction and become the leading global provider of smart 3D construction printers, proprietary construction “ink” and 3D print construction consulting services.
Press ContactHead of Marketing Peter Cooperman646-491-9860247485@email4pr.com
Press ContactHead of Brand, Marketing Sales Jens Rosenthal247485@email4pr.com
SOURCE Black Buffalo 3D Corporation; LTG Lofts to go
Related Linkshttp://www.blackbuffalo.io
ICON Announces Robert Harmon as General Counsel

Tech Innovation Veteran of Amazon and Tesla Joins Leading Construction Tech Company Using 3D Printing Robotics to Deliver Dignified, Resilient Homes Around the World
AUSTIN, TX, July 27, 2023 — ICON, the construction technologies company pioneering large scale 3D printing, today announced that Robert Harmon has joined the company as its General Counsel and member of the senior management team. Harmon will oversee legal affairs, regulatory compliance and policy functions of ICON’s rapidly growing business across private and public sectors.
“Robert understands technology, innovation, real estate, construction, and policy as well as anyone I have ever met or can imagine. We feel incredibly fortunate that he wants to lend his tremendous abilities, experience, and knowledge to ICON.” said Jason Ballard, co-founder and CEO, ICON. “With the addition of yet another accomplished leader to our executive team, I can definitively say we have assembled the best group of senior leaders at any deep tech or construction tech company of which I am aware.”
Harmon brings considerable industry experience as a former leader at Amazon and Tesla. Most recently he served as Associate General Counsel and Director at Amazon where he led a global team supporting Amazon Fresh stores worldwide and online, physical stores, and corporate procurement including benefits, tax, finance, HR and community investments. He advised Amazon Fresh through a number of large strategic investments, including the merger of their online and stores business in 2020. During his time at Amazon, Harmon also held the role of AGC of Economic Development, Energy Transactions and Physical Stores Real Estate where he led as legal counsel for the site selection process and negotiation of Amazon’s new corporate headquarters in Northern Virginia and the Nashville Center of Excellence.
Prior to Amazon, Harmon was Deputy General Counsel and Director at Tesla, serving as the senior legal advisor for all aspects of global real estate and construction. During his tenure, he provided oversight of all aspects of the selection, negotiation, government relations, development strategy and construction of Tesla’s six million sq. ft. battery factory, known as Gigafactory 1 and led strategy for Gigafactory 2 (Buffalo, NY) and Gigafactory 3 (Shanghai, CN).
Harmon is active in several civic, educational and legal organizations and has served on the Board of Directors of Cornerstone Learning in New York, The Children’s Cabinet in Reno, NV and Summer Search Seattle. His accolades have included the Legal 500 GC Powerlist, the 2017 National Bar Association 40 under 40 and the 2016 Tech Diversity – SILICON Valley 40 under 40. Harmon holds a B.S. in Industrial Engineering and Economics from Columbia University and is a graduate of the University of Michigan Law School.
“For far too long, we’ve been limited in how we think about designing, permitting and constructing and it’s time for a dramatic shift. It’s time to build,” said Robert Harmon. “I am excited about joining the incredible team at ICON who are using advanced technology to build a future with affordable, resilient and beautiful homes on this planet and beyond.”
ICON is underway delivering the largest community of 3D-printed homes in the world just outside of Austin alongside one of the nation’s leading homebuilders, Lennar. The 100-home community codesigned by BIG-Bjarke Ingels Group illustrates that construction-scale 3D printing not only delivers higher-quality homes faster and more affordably, but can change the way entire communities are built for the better.
Additionally in 2023, ICON has completed disaster resilient housing along the Gulf Coast, barracks for women and men who serve in the U.S. Army, innovation centers for the Air Force and Texas Military Department and additional homes for those who have experienced chronic homelessness. ICON recently launched Initiative 99, a global architecture competition aimed at designing accessible, beautiful and dignified homes that can be built for under $99,000. The company will break ground on numerous projects over the next year across residential, social affordable housing, public sector and hospitality including a 60+ acre community development in Marfa, TX with visionary Liz Lambert featuring housing, hospitality amenities and the first 3D-printed hotel.
ICON continues to set new standards for delivering resilient, dignified housing at high-speed and lower cost. Raising $451 million to date in funding, ICON has delivered communities of 3D-printed homes in the U.S. and internationally and forged partnerships with world-renowned architects, builders and housing organizations missionally aligned to shift the paradigm of homebuilding. In fall 2022, ICON was awarded $57.2 million from NASA to develop a lunar surface construction system that will target humanity’s first-ever construction on another planetary body.