DARPA Selects ICON For LunA-10 Lunar Architecture Study
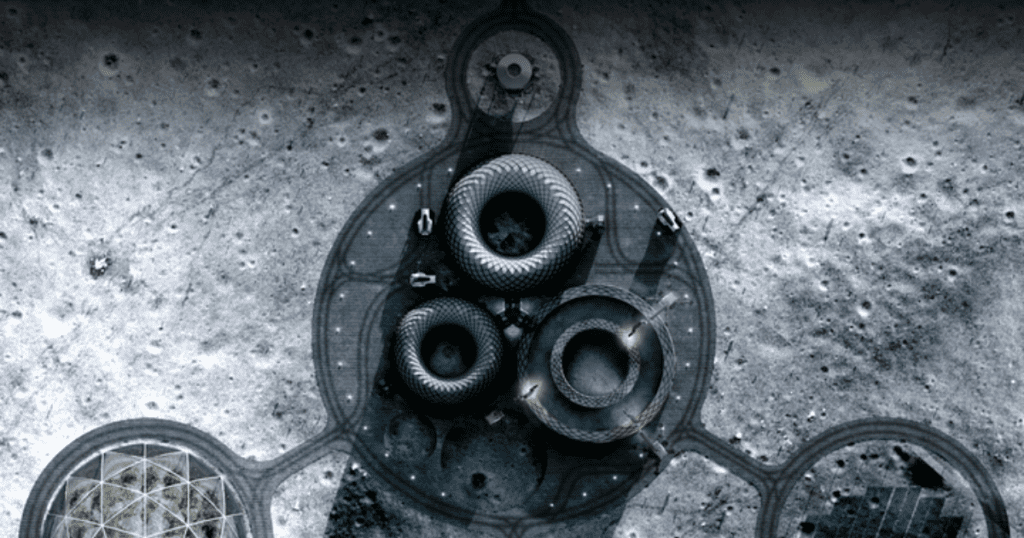
Robotic Construction Company Among Awardees Selected to Chart Path & Create Framework for Lunar Economy in Next Ten Years
AUSTIN, TX, December 5, 2023 – ICON, a leader in advanced construction technologies and large-scale 3D printing, announced today that the Defense Advanced Research Projects Agency (DARPA) has selected the company to take part in the agency’s 10-year Lunar Architecture (LunA-10) capability study. ICON is among a group of 14 performers that DARPA selected through a competitive solicitation process.
DARPA, a division of the U.S. Department of Defense founded in 1958, is one of the most storied research institutions in history. They are responsible for seeding many technologies we rely on in our daily lives, from GPS to the Internet to mRNA vaccines, and military capabilities like stealth technology. The agency is known for developing breakthrough ideas that disrupt or massively accelerate technology roadmaps.
LunA-10 aims to convene a group of companies within the space industry whose products and services collectively represent the foundational elements of a burgeoning lunar economy. The seven-month study will aim to create a framework for interoperable commercial lunar architecture that will help to guide lunar research and investment over the next ten years.
“It is inspiring to see DARPA doing what it does best – moving fast on hard problems and catalyzing commercial innovation for the good of the country and humanity,” said ICON co-founder and CEO Jason Ballard. “ICON is honored to be selected as part of the LunA-10 study to accelerate economic vibrancy on the Moon.”
ICON’s vision for building on other worlds requires inputs from adjacent technology providers and innovators, from power to communications to mobility providers. Participating in the LunA-10 study puts ICON’s space and off-world R&D team in direct contact with these providers.
“By participating in LunA-10, we can understand what inputs are going to be available, when, at what cost, and in what quantities. Similarly, those same providers will now understand what ICON capabilities they can rely on to enable their capabilities and services in the lunar economy,” said Evan Jensen, ICON’s Vice President of Strategic R&D.
This latest accomplishment complements ICON’s work for research and development on the lunar surface. In 2022, under Phase III of NASA’s Small Business Innovation Research (SBIR) program, ICON was awarded a nearly $60 million contract for ICON’s Project Olympus to research and develop space-based construction systems to support planned exploration of the Moon and beyond. ICON’s Olympus system is intended to be a multi-purpose construction system primarily using local Lunar and Martian resources as building materials to further the efforts of NASA as well as commercial organizations to establish a sustained lunar presence.
In 2021, ICON was also awarded a subcontract through Jacobs supporting NASA’s Space Technology Mission Directorate (STMD) as part of NASA’s Crew Health and Performance Exploration Analog (CHAPEA) and delivered the world’s first and only simulated Mars surface 3D-printed habitat. Designed in collaboration with architecture firm BIG-Bjarke Ingels Group, Mars Dune Alpha is located at NASA’s Johnson Space Center and will aid in long-duration science missions.
Known for its advanced 3D printing technology for homebuilding on Earth, ICON began its journey to transform construction with the delivery of the first, permitted 3D-printed home in the U.S. in 2018. Since then, the team has delivered communities of 3D-printed homes in the U.S. and Mexico and barracks for women and men who serve with the U.S. Army and Air Force, and the Texas Military Department. ICON’s proprietary robotics, software and materials deliver resilient, energy-efficient homes faster than conventional construction methods with less waste and more design freedom.
For more on ICON’s off-world construction and space-based technology advancements, visit https://www.iconbuild.com/off-…
First 3D Printed Home Completed in California
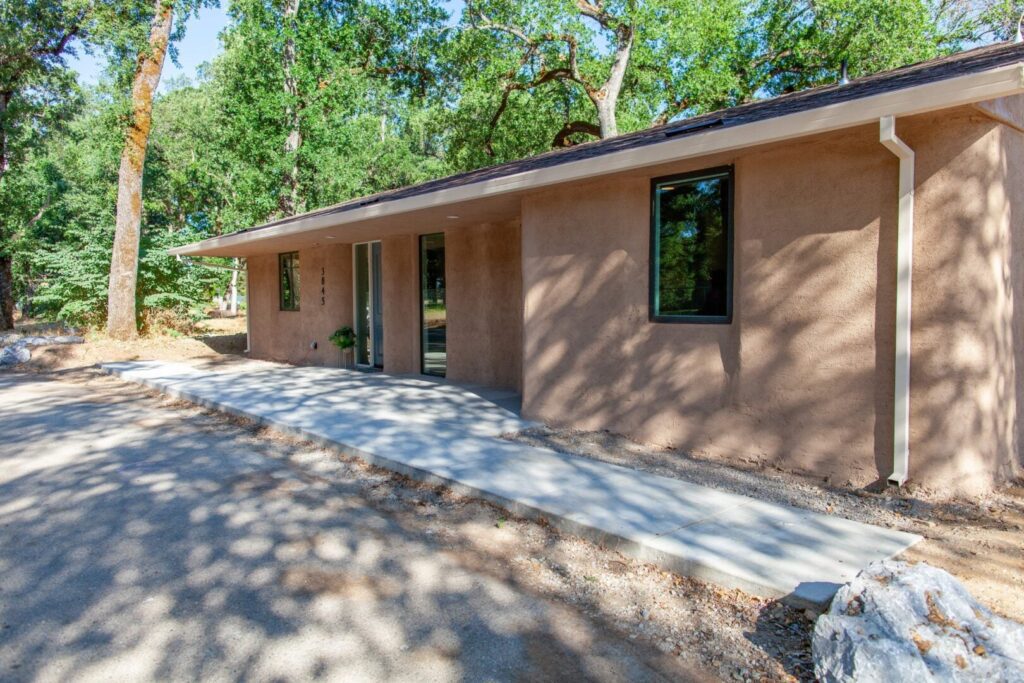
Emergent, a 3D printing company from California, has just completed and last week inaugurated the State’s first fully code compliant 3D printed house at 1,200 SF (110 m2) using technology from COBOD International. The house is one of multiple in a project seeking to alleviate housing challenges due to homeowners losing their properties to California […]
First 3D Printed Net Zero Energy Home Made in Los Angeles
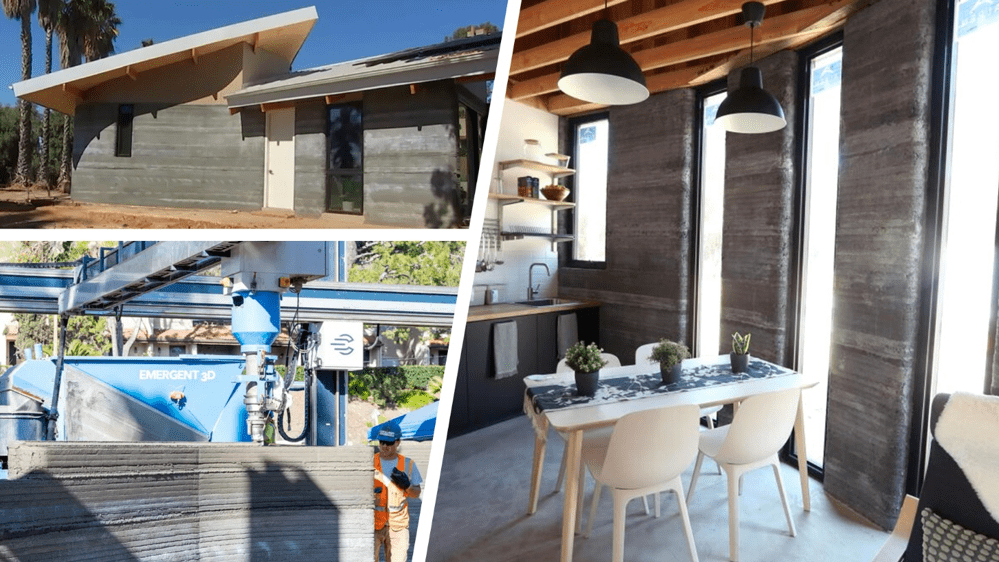
LA’s first 3D printed net zero house completed by Woodbury university students in collaboration with Emergent. Architecture Students from Woodbury University completed Los Angeles’ first fully permitted 3D printed net zero energy house. The house was part of a nationwide collegiate contest by the US Department of Energy. The walls of the 425 square-foot (40 m2) house, […]
Can 3D printing help solve North Texas’ affordable housing crisis?
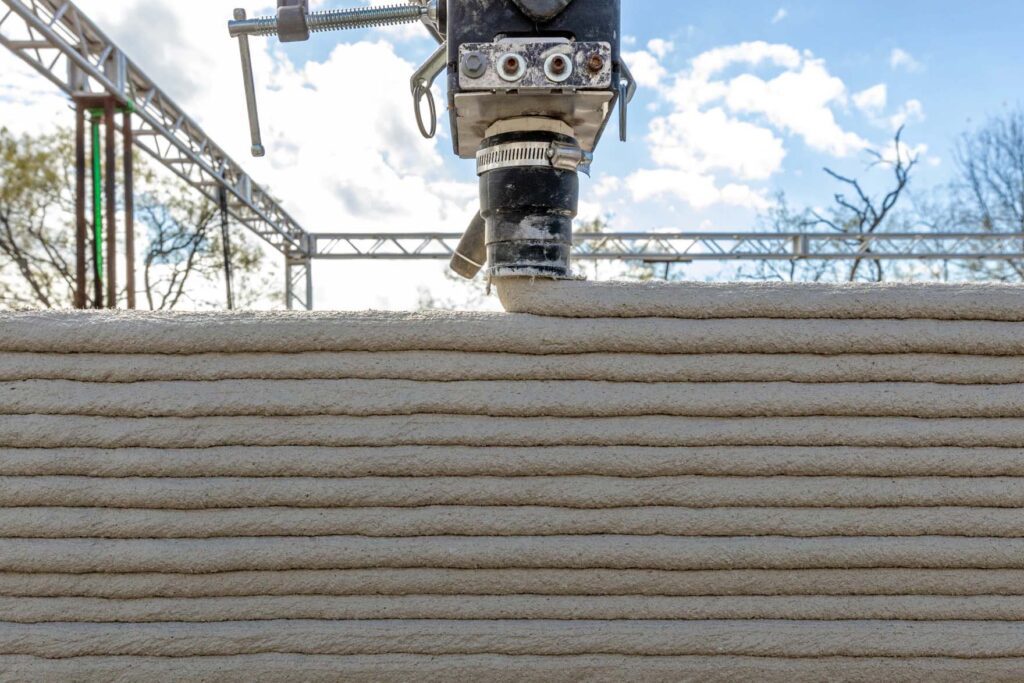
From KERA News:
On a sunny winter morning at a property off a rural dirty road in Kaufman, southeast of Dallas, a construction crew is working on building a barn — but this isn’t your traditional building site.
Instead of working with hammers and power drills, this small crew is letting a robot do most of the work.
“Probably the easiest way to describe it is a robot that has a soft serve ice cream cone machine at the end of it,” said Craig Pettit, CEO of Printed Technologies, a company that builds 3D printed homes, “and so we’re just pushing concrete out just like that, like ice cream cone machine would.”
As North Texas continues to see unprecedented growth, entrepreneurs like Pettit are hoping to solve the housing affordability crisis by turning to this innovative, automated technology.
Pettit and his business partner Lance Thrailkill say their crew is constantly improving the concrete mix used to print.
“That’s what we’ve really been tinkering with is different mixes and every mix is different,” Thrailkill said. “The print comes out different and dries quicker or slower depending on how much water is in there.”
The company has so far built at least six structures with a 3D printer, including houses, throughout North Texas.
A 3D printing nozzle layers the walls of a barn in Kaufman, Texas, on Dec. 20, 2023. “Probably the easiest way to describe it is a robot that has a soft serve ice cream cone machine at the end of it, and so we’re just pushing concrete out just like that,” Printed Technologies CEO Craig Pettit said.Johnathan Johnson / KERA
Thrailkill said the new technology could soon change the housing market. It’s one of the reasons he’s invested in the business.
“We really want to help solve the affordable housing crisis here in America and really, worldwide,” he said.
Right now, the cost of 3D printing a house is about the same as building with traditional methods. Pettit said many start-ups, like Printed Technologies, are racing to develop a more affordable way to build.
“One of the things that I’ve done over the past three years is just simplify everything within the technology to make it easy to set up, make it easy to take down,” Pettit said.
Tim Landau is another industry entrepreneur and the owner and CEO of Hive 3D Builders. His company built what could be one of the largest single family homes made by a 3D printer in Burton, east of Austin.
Like Thrailkill, Landau says what sparked his interest in 3D printing was trying to solve the affordability gap.
“That gap is, you know, specifically, it’s the difference between what the median income person can afford for a house and what the median price for a house is,” Landau said.
A completed 3D printed house in Burton, Texas, between Austin and Houston.Courtesy Hive 3D Builders
Another issue is the supply gap — how many houses are on the market. A recent report found Dallas alone needs as many as 60,000 more homes to meet demand.
“It’s kind of a solvable problem,” Laundau said. “You know, your big production builders, they can ramp up and build more houses to close that gap.”
But when newly built houses are upwards of half a million dollars or more, Landau said the only solution is to do something different.
“Everything points to more automation, whether it’s 3D printing or other forms of automation to help narrow those gaps,” Landau said.
3D printing also reduces the number of people needed to build a house. It usually only takes a two- to four-person crew.
It’s also a quicker process — Printed Technologies can print the frame of a 1,700-square-foot home in about two weeks.
That might sound like it’s replacing much-needed jobs, but according to Associated Builders and Contractors, there’s a shortage of more than half a million workers in construction.
Landau says 3D printing helps alleviate that labor shortage.
“So it’s supposed to not eliminate jobs,” he said. “It’s supposed to take the place of jobs that right now we don’t have anyone to do.”
3D printing nozzle layering the walls to a barn in Kaufman, TX on Dec 20, 2023.Johnathan Johnson / KERA News
Still, this new, burgeoning industry does face its challenges. Right now, the cost of printing a home is just as much as building one traditionally. There also isn’t a huge demand for 3D printed homes in the Dallas area, according to the Dallas Builders Association.
A spokesperson for the association said the technology does have the potential to solve the ongoing housing and labor shortages.
Landau says right now the industry could go one of two ways — one is that it becomes a niche industry for people who can afford customized 3D printed homes. The other is, if companies find ways to lower the extra cost, it could become the new normal.
That’s what Lance Thraillkill at Printed Technologies sees happening.
“In the next five to ten years, it’ll be adopted, across, you know, the entire United States and worldwide would be my expectation,” he said. “And how much that is embraced will be dependent on the cost.”
That means someday in the not too distant future, houses and even entire neighborhoods could be built — at least partially — by robots.
Can 3D printing help solve North Texas’ affordable housing crisis?
On a sunny winter morning at a property off a rural dirty road in Kaufman, southeast of Dallas, a construction crew is working on building a barn — but this isn’t your traditional building site. Instead of working with hammers and power drills, this small crew is letting a robot do most of the work.“Probably the easiest way to describe it is a robot that has a soft serve ice cream cone machine at the end of it,” said Craig Pettit, CEO of Printed Technologies, a company that builds 3D printed homes, “and so we’re just pushing concrete out just like that, like ice cream cone machine would.”As North Texas continues to see unprecedented growth, entrepreneurs like Pettit are hoping to solve the housing affordability crisis by turning to this innovative, automated technology.Pettit and his business partner Lance Thrailkill say their crew is constantly improving the concrete mix used to print.“That’s what we’ve really been tinkering with is different mixes and every mix is different,” Thrailkill said. “The print comes out different and dries quicker or slower depending on how much water is in there.”
Johnathan Johnson
/
KERAA 3D printing nozzle layers the walls of a barn in Kaufman, Texas, on Dec. 20, 2023. “Probably the easiest way to describe it is a robot that has a soft serve ice cream cone machine at the end of it, and so we’re just pushing concrete out just like that,” Printed Technologies CEO Craig Pettit said.
The company has so far built at least six structures with a 3D printer, including houses, throughout North Texas.Thrailkill said the new technology could soon change the housing market. It’s one of the reasons he’s invested in the business.“We really want to help solve the affordable housing crisis here in America and really, worldwide,” he said.Right now, the cost of 3D printing a house is about the same as building with traditional methods. Pettit said many start-ups, like Printed Technologies, are racing to develop a more affordable way to build.“One of the things that I’ve done over the past three years is just simplify everything within the technology to make it easy to set up, make it easy to take down,” Pettit said.Tim Landau is another industry entrepreneur and the owner and CEO of Hive 3D Builders. His company built what could be one of the largest single family homes made by a 3D printer in Burton, east of Austin.Like Thrailkill, Landau says what sparked his interest in 3D printing was trying to solve the affordability gap.“That gap is, you know, specifically, it’s the difference between what the median income person can afford for a house and what the median price for a house is,” Landau said.
Courtesy
/
Hive 3D BuildersA completed 3D printed house in Burton, Texas between Austin and Houston.
Another issue is the supply gap — how many houses are on the market. A recent report found Dallas alone needs as many as 60,000 more homes to meet demand.“It’s kind of a solvable problem,” Laundau said. “You know, your big production builders, they can ramp up and build more houses to close that gap.”But when newly built houses are upwards of half a million dollars or more, Landau said the only solution is to do something different.“Everything points to more automation, whether it’s 3D printing or other forms of automation to help narrow those gaps,” Landau said.3D printing also reduces the number of people needed to build a house. It usually only takes a two- to four-person crew.It’s also a quicker process — Printed Technologies can print the frame of a 1,700-square-foot home in about two weeks.That might sound like it’s replacing much-needed jobs, but according to Associated Builders and Contractors, there’s a shortage of more than half a million workers in construction.Landau says 3D printing helps alleviate that labor shortage.“So it’s supposed to not eliminate jobs,” he said. “It’s supposed to take the place of jobs that right now we don’t have anyone to do.”
Johnathan Johnson
/
KERA News3D printing nozzle layering the walls to a barn in Kaufman, TX on Dec 20, 2023.
Still, this new, burgeoning industry does face its challenges. Right now, the cost of printing a home is just as much as building one traditionally. There also isn’t a huge demand for 3D printed homes in the Dallas area, according to the Dallas Builders Association.A spokesperson for the association said the technology does have the potential to solve the ongoing housing and labor shortages.Landau says right now the industry could go one of two ways — one is that it becomes a niche industry for people who can afford customized 3D printed homes. The other is, if companies find ways to lower the extra cost, it could become the new normal.That’s what Lance Thraillkill at Printed Technologies sees happening.“In the next five to ten years, it’ll be adopted, across, you know, the entire United States and worldwide would be my expectation,” he said. “And how much that is embraced will be dependent on the cost.”That means someday in the not too distant future, houses and even entire neighborhoods could be built — at least partially — by robots.Got a tip? Email Pablo Arauz Peña at parauzpena@kera.orgKERA News is made possible through the generosity of our members. If you find this reporting valuable, consider making a tax-deductible gift today. Thank you.
Partners break ground on state’s first multifamily passive housing project
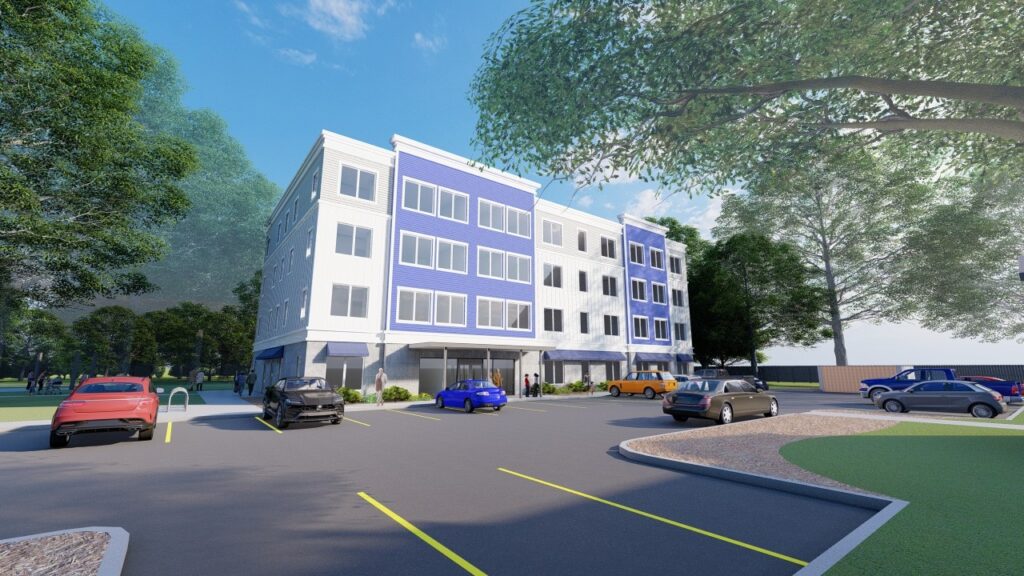
Pinnacle Construction Group has started building what will be the first multifamily certified passive housing development in the state of Michigan. The Grand Rapids-based design-build firm began site work last month and will hold a groundbreaking Jan. 12 for Samaritas Spring Lake, a 53-unit affordable housing rental project at 734 E. Savidge St. in Spring […]
This wildly massive 3D-printed home is the first of its kind: ‘[It] can withstand the hurricanes and heavy storms’
This January, design studio Hannah constructed the first multistory building in the U.S. made by a 3D printer, reports Evan Garcia of Reuters.The process of 3D printing creates objects from a digital blueprint. “Working entirely automatically, the printer creates a model over a period of hours by turning a 3D CAD drawing into lots of two-dimensional, cross-sectional layers — effectively separate 2D prints that sit one on top of another,” says Chris Woodford of Explain That Stuff! The machine puts down many layers of liquid material such as melted plastic, slowly building up a precise shape as each layer hardens.In most cases, this technique is used on a small scale to make figurines, household items, and parts for manufacturing companies. Using 3D printing technology for concrete buildings is newer, but companies like Gensler and WinSun have been doing it since the mid-2010s, as Architect Magazine reports.What makes this project different is that it’s the first multistory house constructed using this method in the U.S. “One of the things about printing a second story is you require, you know, the machine,” says architect Leslie Lok, who designed the new home. “And of course, there are other challenges: structural challenges, logistic challenges when we print a second-story building.”The home Hannah built is a two-story, three-bedroom, 4,000-square-foot house, Garcia reports. The design takes about 330 hours total to print, using a machine that weighs more than 12 tons.The use of 3D printing could represent a major shift in the construction industry. A 3D building takes fewer workers to construct since most of the materials are actually put in place by the machine.The printer also works faster than the average construction crew, which takes about seven months on average, according to the U.S. Census Bureau. This could mean faster, cheaper home construction.Meanwhile, concrete is a strong material, which Garcia says, “can withstand the hurricanes, heavy storms, and other severe weather in Texas that is becoming more frequent and severe due to climate change.”Investing in a sturdy 3D-printed house could be a smart choice for residents. Garcia reports that this 3D-printed house has already been sold.Join our free newsletter for weekly updates on the coolest innovations improving our lives and saving our planet.
3D printed home built in Muscatine using robotic printing system
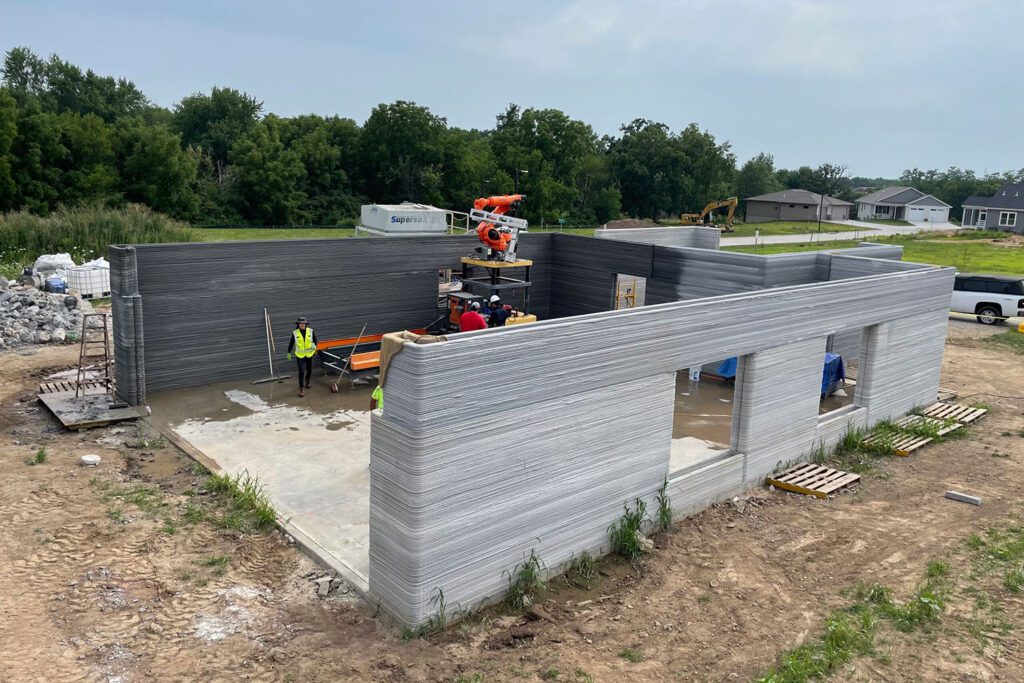
3D printing technology has the potential to transform the US homebuilding industry by offering faster, cheaper, and better solutions for housing. Surprisingly, 3D-printed structures that were once considered impossible to build are now becoming a reality, and progress is happening at an impressive speed.
Alquist 3D, a leading 3D construction company, recently completed the first 3D-printed house in Muscatine, Iowa, using RIC Technology’s advanced robotic arm-based 3D printing system. The construction began in October of this year, and the company finished printing the home’s ten-foot-tall exterior walls in November.
The new 3D printing system by RIC Technology employs advanced robotic arms to build the entire house in a highly automated process, freeing up human labor from dangerous and tiring work.
Compared to conventional gantry-based 3D construction systems that can cost thousands of dollars in labor and equipment rental fees and take up to 3 days to set up, the new system eliminates the need for a massive framework to support the printer head during the printing process. Transporting the gigantic gantry-based system to a construction site typically requires disassembly and the use of three semi-trucks, a large-scale crane, and a telehandler.
RIC Technology’s robotic arm system has some unique advantages over other systems on the market. Its retractable design and compact size make it easy to transport and quick to set up, which can significantly reduce labor and transportation costs. The robotic arm system requires no assembly and can be operational in 2-4 hours. Additionally, this system can cut construction costs in multiple areas, including transportation, setup, and daily operations.
“Compared to gantry-based 3D printing, our robotic arms can reduce costs by about $16,000 per home,” said Ziyou Xu, founder of RIC Technology. “Robotic arm-based 3D printing is one of the most promising solutions to address the global housing shortage crisis.”
In addition, 3D-printed houses promise significant energy savings, lowering the energy expenses of the occupants by 30% due to the insulation features of the houses. 3D-printed homes are also very resilient to withstand natural disasters and extreme weather conditions, such as the harsh winter in Iowa.
According to Xu, the technology enables builders to construct more affordable, resilient, and durable homes with fewer resources and lower costs. That is why the City of Muscatine, in partnership with The Community Foundation and Alquist 3D, began building a set of 10 homes in Muscatine, Iowa, using RIC’s groundbreaking system.
It was the second site Alquist 3D built on in Muscatine. The first house, which initially broke ground in May, was supposed to showcase the company’s innovative technology, which had already been used for Habitat for Humanity projects. However, the project faced a setback in late November when Alquist had to demolish the first of these ten homes before it could be completed. The reason was that the printing mix failed to reach the required 5,000-psi strength level, raising doubts among structural engineers about the durability of the material.
RIC Technology’s innovative technology is not only being used in Muscatine but also in other parts of the world, such as Australia and Rwanda. The company is committed to revolutionizing the 3D printing industry by providing cost-effective, time-saving, and labor-reducing solutions for the global housing market.
This 20-foot tall 3D printer can produce entire homes in just 24 hours — all thanks to this surprising material
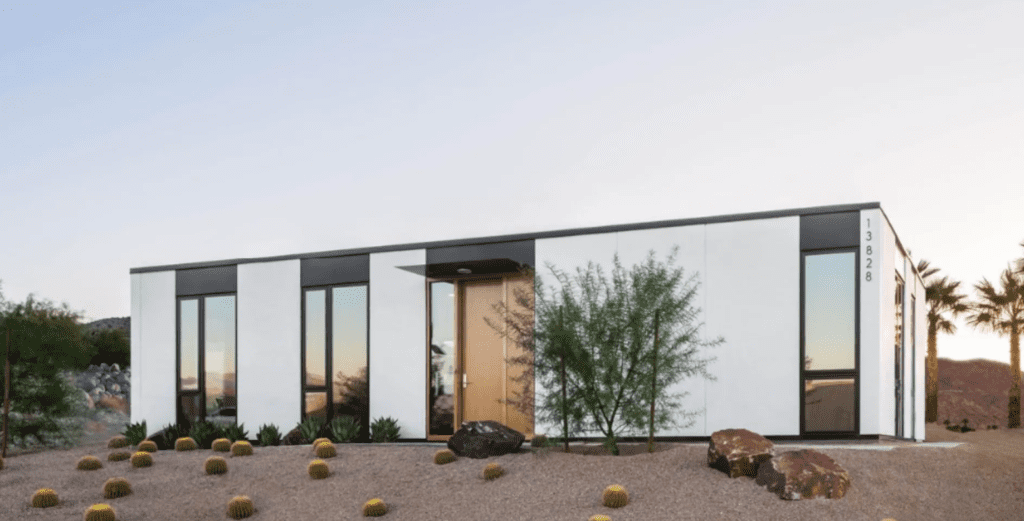
Mighty Buildings, a new business from Oakland, California, promises to build — or really, print — a house in 24 hours.
It’s part of an innovation in the home construction sector that’s five years in the making, according to the company’s website.
Warp News reports that Mighty Buildings is different from similar companies because the team can print the roof, ceiling, and other parts of the home with extreme speed.
“Because we’re building homes for people to live in, we’ve been very deliberate in carrying out our vision to make housing better. This isn’t software that can be debugged on the fly,” Slava Solonitsyn, the CEO and co-founder of Mighty Buildings, told Dwell. “We’re now ready to scale our production with full confidence in our certifications and code compliance of both our material and technology.”
The printer, which is 20 feet tall, produces composite stone panels from recycled materials. The process automates much of the work — around 80% — in large part because the company can print a home’s entire structural shell, reducing the amount of assembly needed later, Dwell reports.
The company cites several global problems that this method is meant to address, including high home prices, population growth outpacing construction projects, and supply chain shortages.
#cool_newsletter_53e74c5a-ee3d-46f7-9b1c-f120b3daa4ca .cool_newsletter__inner span{color:#000000}
JOIN OUR NEWSLETTER
Good news, green hacks, and the latest cool clean tech — straight to your inbox every week!
Sustainability is another major goal. The company claims its process and materials produce just 1% as much waste compared to homes constructed by conventional means. The printing process uses 60% recycled materials at this point, and the team hopes to create zero air pollution by the year 2028.
These advancements also cut costs, saving prices for homebuyers. Mighty Buildings claims that its printed homes cost 45% less than comparable houses in the California market.
Dwell reports that available models include 350-square-foot studios and a three-bedroom, two-bathroom home. The latter option is priced at around $285,000.
Mighty Buildings is currently taking orders. The company’s website showcases a community in Southern California with 30 printed homes in the desert. The houses look futuristic in design, combining modern hardware with sustainable technology, including rooftop solar panels. Soon, the company hopes to take its concept nationwide.
“With a strong foundation in robotics, manufacturing, and sustainability, the Mighty Buildings founding team knows the different facets of the issues that face modern housing,” Eric Migicovsky, a partner at the startup accelerator Y Combinator, told Dwell. “Accessory dwelling units are just the start in further building out their unique approach to building.”
Join our free newsletter for weekly updates on the coolest innovations improving our lives and saving our planet.
Cool Picks
Granite Geek: How Maine is using 3D printers for houses made of wood pulp
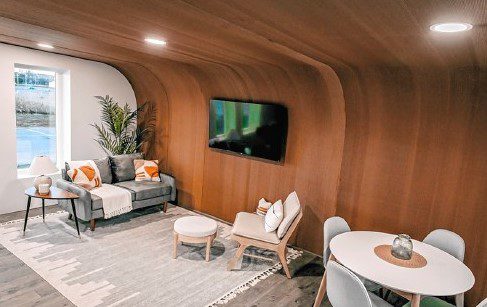
In my career, I’ve encountered several non-traditional ways to build a home, from stacking hay bales to rolling out plastic tubes to using 3D-printed concrete. They’ve been fun to talk about but never made the slightest dent in the industry. The labor-intensive process of “stick-building” houses onsite remains the norm.That failure doesn’t mean we should stop trying, however, so let’s look at an intriguing idea being developed at the University of Maine.The school’s Advanced Structures and Composite Center in Orono recently wrapped up the first year’s outdoor test of BioHome2, a 3D-printed house made entirely of wood fibers impregnated with resin and squeezed out of an industrial-sized printer head. And I mean entirely: They even used it to print the roof of the small but serviceable (600 square feet) one-bedroom home.“We wanted to see how it does through a Maine winter. We’ve done a lot of testing in lab, weathering tests and material tests, but there’s nothing like putting it out there,” said Habib Dagher, executive director of the center. They were worried about it collapsing under snow load or blowing away in a Nor’Easter, of course, but also more subtle potential issues. “One of our big concerns was how it would expand and contract under different temperatures. We had some drywall attached – would it stay? Would it shift by differential expansion? But we didn’t see that,” said Dagher.The basic idea behind BioHome is as old as the first mobile home: It’s cheaper and often better to build a house in a controlled indoor facility and then move it to the final location, instead of gathering materials at each housing site and getting a crew to assemble them in the wind and rain and snow. That sounds obvious but such modular construction has never quite caught on for many reasons, from the low-rent reputation of “trailer parks” to the width limitations of moving structures along the highway.BioHome adds two potential advantages to modular construction. One is 3D-printing, which reduces the number of people needed to build a house. That’s even more of an advantage in the post-pandemic labor market, where trained construction workers are worth their weight in Snap-On tools. Printing also provides more flexibility in design, one reason the BioHome with its sloping corners looks so unusual.The other potential benefit is its unusual material. The lab has created a mix of wood fiber and “bio-resin” in pellet form to feed its printers. The result is wood – you can cut it or drill holes in it, hang pictures or drywall on it, and paint it, Dagher said – but it’s wood created in large forms, very different than the balloon structure of most homes.The raw material is valuable from the point of view of Maine (and New Hampshire) since it uses waste wood, the forestry and sawmill byproduct that once fed New England’s massive paper mills before that business moved away. Creating a new market for waste wood would be a big benefit for New England’s forest industry. All this is fine and dandy but BioHome will just be another in a long list of “futuristic” houses that never move past novelty status if it can’t be built in large numbers at reasonable cost. That’s the next stage at Orono.The Advanced Structures and Composite Center will break ground this summer on an expansion they’re calling the Green Engineering and Materials (GEM) Factory of the Future, the next step in BioHome development.“Cost is a function of how fast you can print it,” said Dagher. Currently, the extruder head can print 120 pounds an hour, moved around by an overhead gantry crane. The next generation should go to 500 pounds an hour, he said. The one-bedroom home requires around 40,000 pounds of material so if they get a couple of the new printers going in the new factory they could in theory produce a home every 2 days with an estimated material cost of $40,000, although that doesn’t include moving, installation and what is often the biggest cost, land.The lab is working on a plan to print nine homes with the next generation of their BioHome3D technology and put them in Bangor to provide housing for individuals experiencing or at risk of homelessness. And importantly, they’re working on standards and training so that local building inspectors, often a stumbling block for unusual housing designs, can be confident about the safety of these weird objects.All this reflects the fact that new technology is just the start of making a difference in something as sweeping and important as our housing.“We don’t anticipate that this would be the only way to make houses. It’s just another tool, another solution, that can add to the housing stock,” said Dagher.And we all know the nation’s housing crisis needs all the tools and solutions it can get. Even if they come oozing out of a gigantic printer.
Despite regulatory barriers, 3D-printed houses can revolutionize the construction industry
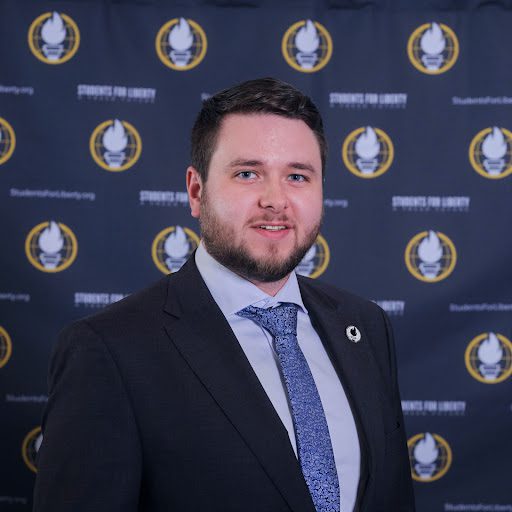
The United States and other Western nations are capitalist, right? Well, not really. It is thankfully not socialism, where the economy is designed and controlled by central planners. However, the economy is far too burdened with regulatory barriers to even approach a free-market system that thrives on competition, innovation, and ever-increasing efficiency.
These regulatory barriers, often originating as attempts to ensure consumer protection, have created a system that erodes many of the benefits associated with true free markets — and chief among these benefits is innovation.
Breaking regulatory barriers to bring you one-week house construction
What if we could revolutionize transportation to make it not only faster but also more sustainable? What if we could create educational systems that are not only more accessible but also tailored to individual learning needs?
Or, how about building new homes in a matter of days, at a fraction of the cost?
ICON Technologies is able to do just that — if not for regulatory barriers.
Using its pioneering, 3D-printing Vulcan construction system, ICON has the capability to construct the main framework of a new house within a mere 24 hours. Moreover, they can complete the entire project in only eight days, all at a significantly lower cost than a conventional house.
Their innovative technology promises to radically transform the construction industry. But they came up against a formidable challenge in the form of a regressive housing code ill-equipped for major technological advances.
Fortunately, in this case, ICON Technologies was able to work with Trust Ventures, a venture capital firm specializing in helping start-ups navigate and challenge regulatory barriers. They were ultimately successful in receiving the first-ever permit to 3D-print houses, before overcoming further regulatory barriers preventing them from building at scale.
The company was finally able to take reservations for their first 3D-printed housing development, outside Austin, Texas.
But how many more potentially life-changing innovations are stuck in the waiting room because of rigid, backward regulatory barriers?
Entrepreneurs with a flair for innovation can conceive remarkable products and services that hold the potential to redefine the market. Yet, without the ability to navigate the intricate web of bureaucracy, characterized by burdensome regulations and red tape, these groundbreaking ideas may remain unrealized.
This important theme will be a topic of discussion at Students For Liberty’s upcoming LibertyCon International. Whole Foods co-founder and former CEO, John Mackey and Bitcoin podcaster, Stephan Livera will discuss the cost of compliance and the negative consequences of regulatory barriers in a panel moderated by Students For Liberty’s CEO, Dr. Wolf von Laer.
Students For Liberty’s flagship annual event, LibertyCon International will be held in Washington, D.C., on February 2-4, 2024. It promises to be the place for engaging with leading experts and connecting with others who share a dedication to advancing pro-liberty ideas and creating a freer future.
Click the button below to sign up for updates and secure your spot at this exciting event. We can’t wait to see you there!
This piece solely expresses the opinion of the author and not necessarily the organization as a whole. Students For Liberty is committed to facilitating a broad dialogue for liberty, representing a variety of opinions.
Russell Coates
Editor-in-Chief, Learn Liberty Blog
Russell is the Editor-in-Chief of the Learn Liberty blog, having also served as Students For Liberty’s Global Content Marketing Specialist. He enjoys researching and reading about a wide variety of topics, including the history of liberalism, philosophy, politics and current events, emerging technologies, and conservationism. Russell obtained a B.A. in…
3D-printed neighborhoods are popping up across America: ‘[This] is not science fiction’
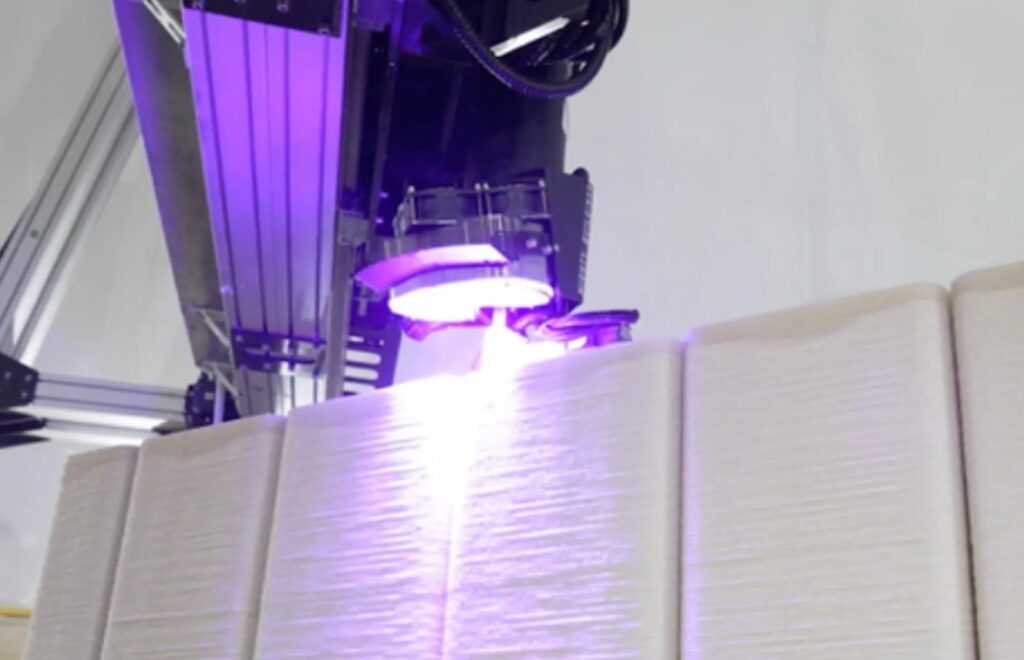
The keystroke “cmd + print” is producing an unlikely result around the country: an explosion in the appearance of 3D-printed homes.
And while the startup sequence is likely a little more involved than pushing a few buttons, the process in fact involves giant printers that put down layers of concrete mixture — that form home exteriors — with speed and precision.
Forbes and other news agencies are reporting on the trend, which includes neighborhoods of printed homes popping up in numerous states. Proponents of the tech see it as a faster, cheaper, and cleaner way to build houses, according to the Forbes report.
“I see 3D printing as a transformational disruptive technology,” Basil Starr, founder of Beverly Hills-based Palari Group — the developer of a 3D community in Desert Hot Springs, California — said in the news story. These dwellings can be constructed in about half the time as a traditional build, per the report.
What is a 3D-printed home?
Though the technology and details vary by developer, the concept is fairly constant.
High-tech, automated, and pre-programmed machines jet out layers of a concrete building slurry that hardens to form a home’s exterior. The printers, like a 20-foot-tall one used by California’s Mighty Buildings, are large.
#cool_newsletter_53e74c5a-ee3d-46f7-9b1c-f120b3daa4ca .cool_newsletter__inner span{color:#000000}
JOIN OUR NEWSLETTER
Good news, green hacks, and the latest cool clean tech — straight to your inbox every week!
Why is this important news?
Building our homes and facilities is dirty work. In the United States, about 40% of air pollution comes from building construction and daily heating, cooling, and lighting, according to the American Institute of Architects.
3D tech is one solution as we develop better ways to build. A Singapore study from 2020 found that a 3D bathroom produced nearly 86% less air pollution than one made with regular methods, according to ScienceDirect.
“It’s about having a better process for how we build our homes,” Evelyn Woodman, co-founder of Citizen Robotics, told the Detroit Free Press. The nonprofit finished Michigan’s first 3D home earlier this year.
How will the tech impact me?
If you are planning to build a home the traditional way, it will cost an average of $329,000, not including the land, per Forbes. The process will also contribute to the industry’s major air pollution tally.
The homes come in a variety of sizes and stories, offering all the modern amenities. Many seem to have flat roofs and chic interior design concepts, though styles vary.
“We can typically do it quicker than a normal concrete or stick-built home would be,” Mannheimer told the Free Press. “We can do it with less labor. We can do it with less expensive material, and the material that we’re using tends to be more sustainable. It’s stronger than traditional concrete by at least two or three times, which means it can stand up to most major storms. It doesn’t burn.”
Even if you aren’t in the market, you might notice this tech at work in a nearby community soon. In addition to Michigan, printers are making homes in a growing number of states:
In California, Mighty Buildings is pumping out house exteriors in Desert Hot Springs and Rancho Mirage. The company’s printers use 60% recycled composite stone. That is of note, as critics referenced by CNN question the use of concrete in 3D builds, citing air pollution.
Texas is home to the world’s largest 3D community, planned for 100 dwellings, per CNN. There are 46-foot-wide printers at work on walls on the site. To maximize sustainability, the homes have solar panels. The 1,500-square-foot to 2,100-square-foot homes with three or four bedrooms can be listed for nearly $600,000, according to CNN.
On the East Coast, the first 3D home in Richmond, Virginia, was printed in 2022. The exterior of the three-bedroom, two-bath house was printed in about 15 hours with “less labor and … materials” than lumber builds, according to TV station 12 On Your Side. The project was made possible in part by a $500,000 grant from Virginia Housing.
A company in Japan might make the tech accessible to most people everywhere — if it travels overseas. Serendix uses 3D printers and CNC machining to create homes for under $40,000. They might not be for everyone, as one model is less than 600 square feet, Fast Company reports. It looks like a dwelling from Star Wars.
What’s next?
While more 3D neighborhoods are likely on the way, ICON (the company working on the Texas community) CEO Jason Ballard told CNN that the tech could also be a solution to homelessness, as well as a way to provide sanctuary after disasters.
The CNN report notes that 3D building codes have yet to be “widely adopted,” a benchmark that will earn confidence for the tech’s strength and stability.
“3D printing is not science fiction,” Ballard said to the news agency. “In the future, our bet is that this will be humanity’s best hope for a housing solution that matches our highest values and ideals.”
Join our free newsletter for weekly updates on the coolest innovations improving our lives and saving our planet.
Cool Picks
Habitat for Humanity announces plans to build Tuolumne County’s first 3D-printed homes
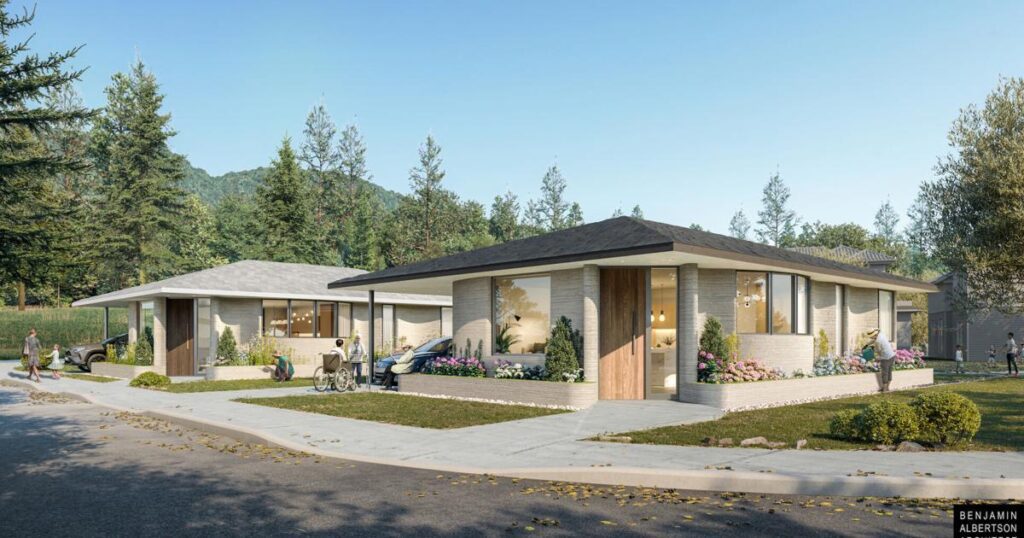
A local nonprofit group affiliated with the global Habitat for Humanity organization has announced plans to build the first 3D-printed homes in Tuolumne County that would house aging-in-place individuals at its current workforce housing development near Columbia.Habitat for Humanity of Tuolumne County first announced plans for 3D-printed homes at its Parrotts Ferry Village in May, and Trinity Abila, the nonprofit’s chief executive officer, presented the plans during an annual meeting of the California County Planning Commissioners Association at Black Oak Casino Resort in October.
Granite Geek: How Maine is using 3D printers for houses made of wood pulp
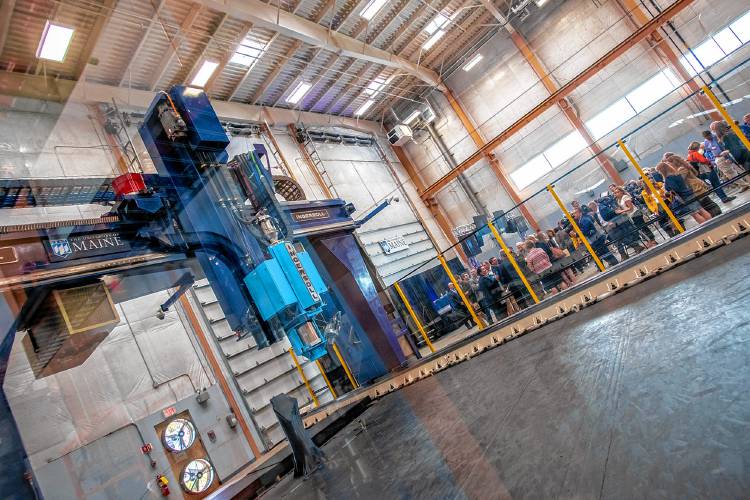
In my career, I’ve encountered several non-traditional ways to build a home, from stacking hay bales to rolling out plastic tubes to using 3D-printed concrete. They’ve been fun to talk about but never made the slightest dent in the industry. The labor-intensive process of “stick-building” houses onsite remains the norm. That failure doesn’t mean we should […]
Compact 3D printer to build fire-resistant house in California
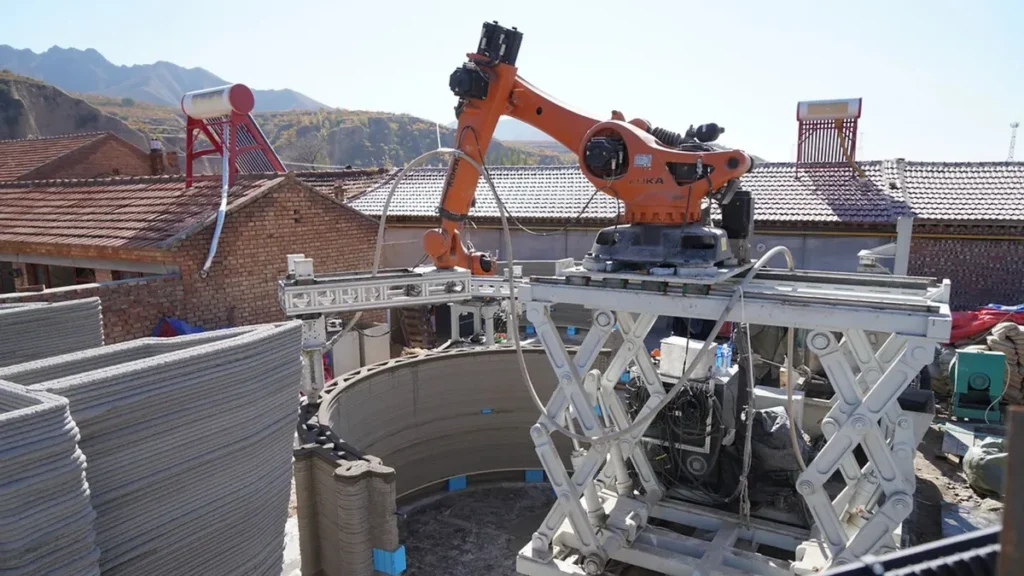
RIC Technology’s compact 3D printer can be used in crowded neighborhoods tooRIC Technology A compact robotic 3D printer will help build a fire-resistant house in Walnut, California, early next year. The first-of-its-kind project is expected to set an example for the technique’s utility in areas severely impacted by wildfires. Additive manufacturing is the industrial name for 3D printing that is being used for a variety of applications around the world. Whether making small machine parts or large bridges, additive manufacturing has proven to be a reliable technique to build quickly. This is why construction firms have also used this approach to make schools and houses with a short turnaround time. Interesting Engineering has previously covered how 3D printing is used to build a large-scale housing complex. These have typically been new projects in empty spaces without much difficulty determining how the printing equipment can be placed. However, the same approach becomes difficult to deploy when reconstructing an old house or building an accessory dwelling unit (ADU) in crowded neighborhoods.
Printing a place to live: In Central Texas, homes are being built wit…
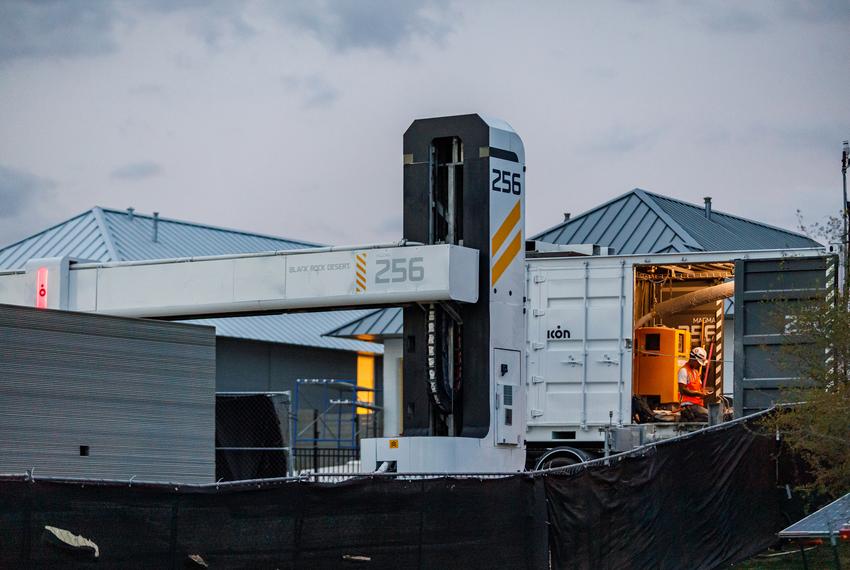
Sign up for The Brief, The Texas Tribune’s daily newsletter that keeps readers up to speed on the most essential Texas news.
ROUND TOP — Layer by layer, a robotic arm lays streaks of concrete that rise to become the walls of five small vacation rentals tucked in the corner of The Halles event center in this Central Texas town.
Round Top is no stranger to short-term rentals. The town of less than 100 residents draws tourists for its antique events and live music scene and has more than 200 rentals listed on Airbnb.
But these new additions, named the Casitas at the Halles, represent what Hive3D founder and CEO Timothy Lankau hopes is a revolution in construction — 3D printed homes built mostly by machines. His Houston-based company, was launched in 2022 and has built six homes.
“There’s something of a housing crisis in America, which I think is the stupidest crisis I can possibly imagine, ” Lankau said. “With all of the ingenuity and resources we have, as a people, the fact that we can’t figure out a better way to build walls and roofs so that everyone has a nice house seems just baffling to me.”
While the technology is new, Lankau as well as others embarking on this endeavor believe 3D homes can eventually help lessen the housing crisis, and do it in a climate-friendly way.
3D printing of residential structures is still a new concept. The first one, a 3,000-square-foot home in Yaroslavl, Russia, was completed in 2017.
A year later, an Austin-based startup called Icon showcased its first 3D-printed structure at the technology portion of South by Southwest.
“We ultimately needed to find ways to build a lot more homes a lot faster. And we landed on 3D printing, using concrete-like material,” said Tom vonReichbauer, the CFO of Icon, which is building an entire subdivision near Austin using 3D printing technology. “Advanced robotic construction is the most promising path forward.”
A small 3D-printed home’s walls can be built in under 24 hours, with printing on larger single-family homes’ walls ranging from 10 to 45 days.
The average single-family home using traditional methods takes six to eight months to construct, according to eXp Realty.
A large 3D-printer is used to build the walls and structure of a new home in the Wolf Ranch neighborhood of Georgetown.
Credit:
Julius Shieh/The Texas Tribune
“When you take construction, and you bring automated technologies to it and do robotic construction, you’re able to help shrink the timeline it takes to build a home,” VonReichbauer said. “You’re able to print [a house] with far less waste. If you’ve been to a traditional construction site, you’ve seen the amount of waste that’s produced there.”
Just like with traditional construction, the foundation is laid first. After that, rebar is put in place to support the interior and exterior walls, which are printed over the rebar. The robotic arm of the 3D printing machine lays the cement like layers of frosting — leaving a hollow space for electrical wiring and plumbing that’s later filled in with more concrete. Once a wall is complete, the robot is moved to the next wall. The finished walls have a horizontal ribbed texture.
After the walls are finished, workers install doors, windows and a roof.
Both Hive3D and Icon use alternatives to portland cement — cement production is one of the biggest sources of greenhouse gases in the construction industry and is responsible for about 8% of the world’s CO2 emissions per year.
Hive3D partnered with Utah-based Eco Material Technologies, which creates a range of eco-friendly alternatives to concrete called “green cement,” which includes fly ash — a common byproduct from coal-fired power plants.
Unlike portland cement, their mixes don’t require milling and heating limestone, which accounts for most of the product’s pollutants, so it creates 92% to 99% fewer emissions, said Eco Material Technologies CEO Grant Quasha.
Quasha said the green cement doesn’t have an entirely carbon-neutral footprint because the mix requires transportation to the work site and electricity is used to run the mill to mix the materials together once it arrives, but the company claims it keeps over 6 million tons of CO2 out of the environment each year with its cement alternatives.
Icon makes its own concrete alternative called Lavacrete, which vonReichbauer says uses some portland cement. He said the company is looking for ways to make it more eco-friendly.
Built for the climate
Walking through the first single-family home that Hive3D is building in Burton, which is about halfway between Austin and Houston, Lankau noted that the house was significantly cooler than the outside temperature on a blazing August day — even though the air conditioner had not yet been installed.
Lankau said the thick foamed concrete walls help give the homes an above-average R-value — which refers to a material’s resistance to heat transfer. Even as Texas experiences more extreme heat, the insulating properties of concrete construction should keep the homes cooler inside, which can help keep utility bills lower.
Lankau added that the concrete walls make the homes much more wind-resistant and safer during extreme weather events like hurricanes and tornados.
“We prefer to build with more curved shapes and less flat surfaces for wind to push against. The roofs are tied all the way down to the foundation and into concrete rebar,” Lankau said. “It’s a serious structure when it comes to wind.”
Concrete structures are also more likely to survive flooding without sustaining major structural damage or mold infestation, Lankau said. Traditional frame homes often require significant restoration when sheetrock, insulation and wooden framing gets inundated with water in a flood.
Large 3D-printers sit in a row in a construction zone in the Wolf Ranch neighborhood of Georgetown.
Credit:
Julius Shieh/The Texas Tribune
“When you have these foot-thick concrete walls, they are bulletproof, everything-proof. From the foundation up to the roof line, everything is inorganic, so there’s nothing to rot and degrade over time,” Lankau said. “So it should, over time, not change much, this house should look the same today as it’s going to look in 100 years.”
Addressing affordability and the shelter crisis
About 30 miles north of Austin in Georgetown, Icon is printing an entire 100-home subdivision called Wolf Ranch in collaboration with Florida-based major developer Lennar.
VonReichbauer said the city “has been incredibly receptive to what we’re doing” and the first homes sold within a few days of being listed.
Lennar is listing the homes for roughly $470,000 to $579,000; the average cost of a home in Georgetown sits at $459,932.
VonReichbauer said the company has also built 3D-printed homes in Mexico with New Story, an organization focused on aiding the shelter crisis across the globe.
In what New Story calls the world’s first 3D printed community, 10 homes were built just outside of Nacajuca in the state of Tabasco for financially needy families in the region who moved into the homes in November 2021.
Icon also partnered with Austin’s Mobile Loaves & Fishes to build six 400-square-foot homes in an east Austin community run by the nonprofit for chronically unhoused people.
Lankau hopes to do something similar as Hive3D expands. He believes his Round Top rentals — which range from 450-square-foot studios to 850-square-foot two-bedrooms — can serve as a model for building affordable homes in a state with a growing housing shortage.
Lankau said Hive3D will work as its own developer when necessary to make sure their homes are sold at affordable prices and wants the company to sell to a range of consumers.
“There are different bands of affordability. There’s government-subsidized housing and there’s housing that is just built for people on median incomes to afford. We’re open to all of that,” Lankau said.
However, James Tate, an assistant architecture professor at Texas A&M University, expressed skepticism about the long-term ability of these companies to keep their prices affordable and compete in the Texas housing market.
“In this state, there is no requirement for developers to have affordable housing units, there’s no incentive other than individual developers who say, ‘I believe that there should be fair housing,’” Tate said. “This state is very willing to allow housing discrimination to happen all the time.”
Tate is also skeptical that 3D printing can change the construction industry and address the housing crisis.
“As a researcher and design faculty at a university. I can’t help but feel a need to be optimistic,” he said. “But I know enough about the history of architecture and construction. In every attempt that has been made to address our housing challenges, when we take a step forward another challenge arises … all property and real property is subject to forces of capitalism.”
Todd Wiseman contributed to this story.
Look inside the world’s largest 3D-printed neighborhood in Texas
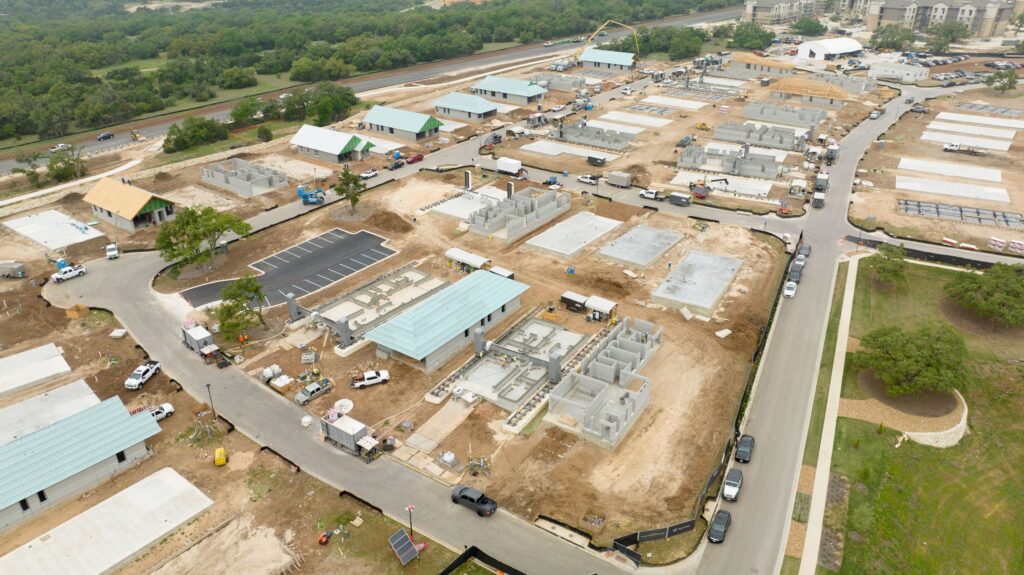
CNN
—
The world’s largest community of 3D-printed homes is being built in Texas — and the neighborhood just unveiled its first completed house.
With walls “printed” using a concrete-based material, the single-story structure is the first of 100 such homes set to welcome residents starting September.
The community is part of a wider development in Georgetown, Texas called Wolf Ranch. It’s located about 30 miles north of Austin, the state capital, and is a collaboration between Texas construction firm ICON, homebuilding company Lennar and Danish architecture practice Bjarke Ingels Group (BIG).
On Saturday prospective buyers toured around the finished model home at the project’s grand opening, and some of the units have already sold, ICON spokesperson Cara Caulkins told CNN via email.
Images of the newly completed building shared by the company show brightly lit interiors and curved gray walls. The walls are made from a concrete mix called Lavacrete, which is piped into place using 46-foot-wide robotic printers. After the walls are printed, the doors, windows and roofs — all of which are equipped with solar panels — are installed.
ICON says more than a third of the homes’ walls have now been printed, and the properties currently on offer are being sold at $475,000 to $599,000.
The 3D-printed homes range in size from 1,500 to 2,100 square feet and have three to four bedrooms.
Faster, cleaner and more affordable
When ICON announced the project in 2021, its co-founder and CEO Jason Ballard described the community as a “watershed moment in the history of community-scale development.” 3D-printing, he said, delivers high-quality homes faster and more affordably than conventional building methods.
With the United States facing a deficit of approximately five million new homes, Ballard said there’s a “profound need to swiftly increase supply without compromising quality, beauty, or sustainability, and that is exactly the strength of our technology.”
Meanwhile, Martin Voelkle, a partner at Bjarke Ingels Group said in a statement that the 3D-printed buildings were “significant steps towards reducing waste in the construction process, as well as towards making our homes more resilient, sustainable and energy self-sufficient.”
Independent research suggests that printing homes can reduce carbon dioxide emissions and construction waste. 3D printers can construct buildings without formwork (the concrete molds that cement is typically poured into), which can significantly reduce overall use of the material. Cement is responsible for about 8% of global CO2 emissions annually.
A 2020 study from Singapore found a bathroom unit constructed using 3D printing was both 25.4% cheaper and produced almost 86% less carbon dioxide than one made with conventional construction methods.
However, critics have pointed out that 3D-printed homes still rely on carbon-intensive concrete, and that building codes addressing the structures’ safety and stability have not yet been widely adopted.
Wolf Ranch is ICON’s largest project to date, though the firm has already used 3D printing to build social, or subsidized, housing in Mexico and Texas.
Ballard told CNN in 2019 his company’s technology could also be used to combat homelessness or provide shelter following natural disasters.
“3D printing is not science fiction,” he said. “We have crossed that threshold from science fiction into reality. In the future, our bet is that this will be humanity’s best hope for a housing solution that matches our highest values and ideals.”
9 Examples of 3D-Printed Houses
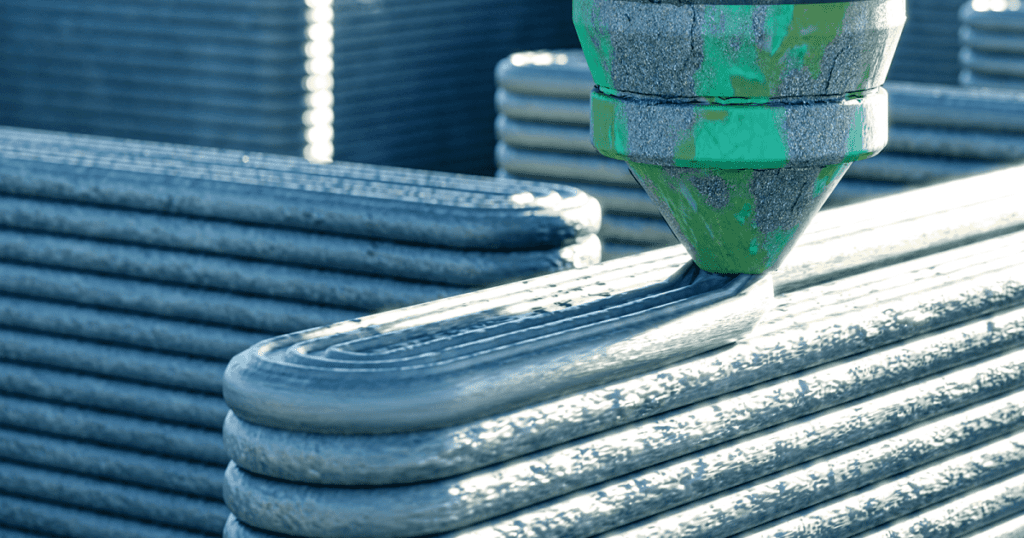
It’s a rare occasion when something debunks the “too good to be true” principle, such as 3D printing an entire house in less than 24 hours. And yet, here we are.What Are 3D-Printed Houses?Three-dimensional-printed houses are structures that are built layer by layer using an industrial-grade, 3D-printing technology. This method of additive manufacturing is also known as construction 3D printing.As tenants move into 3D-printed houses in the first years of their commercial listing debut, 3D printing is on a 23 percent compound annual growth rate over the decade to come, according to Grand View Research. These dwellings — often sharing a gray, shapely appearance with a ribbed texture — are even piquing the interest of NASA, which funded a $57 million project to develop tech for moonside 3D-printed infrastructure.Highly customizable and free of form, construction 3D printing is a new-age tech on the verge of market disruption, holding the potential to mass produce housing.What Are 3D-Printed Houses?Three-dimensional-printed houses are life-size dwellings that use 3D printing as its primary means of construction. With minimal human oversight, these highly customizable structures can be built on-site or off-site within a matter of hours at a fraction of the cost.Typically, 3D-printed houses feature free-form, curvilinear shapes made out of a cement mix. Projects span from inhabitable beta prototypes under study to move-in-ready affordable housing and even high-end luxury homes.Aside from time and money, several other reasons explain additive manufacturing’s disruption to the construction market. Many see this type of low-waste, computerized homebuilding delivered from an industrial-scale printer as a way to shelter unhoused communities and a gateway to sustainable, biodegradable housing solutions.How Are 3D-Printed Houses Built?Industrial-sized 3D printers build entire multi-unit housing developments one tiny layer at a time. This repetitive process puts the “additive” in “additive manufacturing.”Following a digital blueprint, a 3D printer will dispense a paste-like mixture. This will consist of choice ingredients — often a cement blend — but can range from sand and special polymers to bio-resins, like soil, clay or wood flour, which is a fine sawdust mixed with a corn-based binder.How Long Does It Take To 3D Print a House?Nowadays, industrial-sized 3D printers have made it possible to print an entire house in less than 24 hours.Keep in mind that a project’s “printing time” may exclude time for any second-fix installations or construction time necessary to piece together a project printed on-site and transported to its final location.And if you’re trying to build something of scale, like a house, the 3D printer itself has to outsize it. Made out of a steel, quad-truss framework — the kind you’d see as part of a concert stage — these industrial-grade 3D printers form a sort of hollow cube. On top, a robotic arm zips along a track, following pre-programmed instructions being read from the blueprint.Much like your desk-side inkjet printer, the mixture is then heated during a thermal extraction process. The paste squeezes through a nozzle, bringing the digital rendering into physical form. Before the next layer is applied, the mixture is solidified by a concrete dryer. This process repeats until all uploaded building elements are complete.It’s important to note that additive construction work sites are not entirely autonomous. Aside from the setup and breakdown of the equipment, human oversight is necessary to ensure there are no technical hiccups. Specialists must be on-site to cut holes for second-fix installments, such as plumbing, electrical wiring, doors and windows.How Much Does a 3D-Printed House Cost?Of course, this number will vary from project to project, and face further price contingencies based on the hired companies and materials used (let alone geographic location, size, amenities, design complexity, and so on). With that being said, developers stateside and abroad report average cost savings of 30 percent.Three-dimensional-printed houses first hit the U.S. market at the start of 2021. The 1,407-square-foot house — complete with three bedrooms, two baths and a two-car garage in Riverhead, New York — listed as “the world’s first 3D-printed home for sale” for $299,999 on Zillow.com.ICON, a 3D-printing construction company, said it could produce a 600 to 800-square-foot, economy-sized building for as low as $4,000 in 24 hours, as reported by Business Insider.Models on the more affluent side of the market can surpass $1 million. Known as House Zero, the mid-century, ranch-style luxury home is a 2,000-square-foot property with a 350-square-foot accessory dwelling unit. Just based on size and location, Zillow estimated the price of this four bedroom, three-and-a-half bath estate at $723,000 to $908,000, according to online specialty magazine All3DP. However, its one-of-a-kind, exceptional design may push it into the seven-digit price range.When Will 3D-Printed Houses Become Available?Examples of 3D-Printed Houses[embedded content]An error occurred.Unable to execute JavaScript. Try watching this video on www.youtube.com, or enable JavaScript if it is disabled in your browser.BioHome3D is a 3D-printed house constructed out of 100 percent bio-based materials. | Video: 3DPrint.comBioHome3DThe University of Maine Advanced Structures and Composites Center is 3D-printing housing structures exclusively from bio-resins and wood fibers to combat labor shortages and widen access to affordable housing. The demo project, known as BioHome3D, begins with a 600-square-foot prototype that features a fully 3D-printed floor and roof. As a whole, the one-bedroom, one-bathroom building is 100-percent recyclable, made up entirely of biodegradable materials, including wood flour. As a prototype, BioHome3D is equipped with monitoring sensors, measuring thermal, environmental and structural elements, to gather resilience-based data to better inform future designs.[embedded content]An error occurred.Unable to execute JavaScript. Try watching this video on www.youtube.com, or enable JavaScript if it is disabled in your browser.All East 17th Street Residences feature minimal architectural aesthetics. | Video: FindYourDENEast 17th Street ResidencesThese four Austin, Texas properties by construction 3D-printing company ICON feature open-floor plans, minimal architectural aesthetics and private yards. Varying in size, these residences feature two to four bedrooms and range from 1,000 to 2,000-square-foot homes. Each ground floor level is built with a proprietary cement-based material, dubbed “Lavacrete,” to last longer than traditional construction materials, according to the company’s website. The second story incorporates old-school methods, and is constructed out of black metal cladding and rich-colored timber. They share a color palette of green, white and terracotta and have all been sold.[embedded content]An error occurred.Unable to execute JavaScript. Try watching this video on www.youtube.com, or enable JavaScript if it is disabled in your browser.Mikkel Brich, CEO and founder of 3DCP, talks about the future of 3D-printed construction. | Video: COBODHouse 1.0With the help of 3D-printing construction manufacturer COBOD, Danish startup 3DCP Group constructed Europe’s first 3D-printed tiny house last year in just five weeks; however, the structure itself printed in just 22 hours. Located in Hostelbro, Denmark, this 398-square-foot structure is composed of three sections that merge at an open, triangular-shaped core. Inspired by the no-frills aspect of student living, the space is economically laid out and contains all the necessary amenities — a bathroom, open-plan kitchen, living room and loft-style bedroom on a raised level. Sebastian Aristotelis, architect at Saga Space Architects who designed House 1.0, said that the project was built at the lowest possible cost, with developers opting for inexpensive materials, like concrete, and constructing the project using a low-to-no waste approach.More on 3D Printing 25 3D-Printing Companies to Know[embedded content]An error occurred.Unable to execute JavaScript. Try watching this video on www.youtube.com, or enable JavaScript if it is disabled in your browser.Watch 3D-printing construction company ICON build House Zero, a luxury 3D-printed house. | Video: ICONHouse ZeroICON teamed with architectural firm Lake|Flato to build a three-bedroom, two-and-a-half bath residence just outside of downtown Austin, Texas. Its curved walls and rounded corners are insulated with Lavacrete and reinforced with steel. Paired with a one-bedroom, one-bath accessory dwelling unit, ICON’s website styles the 2,350-square-foot property — which printed in under two weeks — as a “mid-century modernist ranch house aesthetics.” Given its design to consume net-zero energy, Time named House Zero to its Best Inventions of 2022 list. In the months since, ICON has broken ground on a 100-home project, projected to be the largest 3D-printed residential community in the United States.[embedded content]An error occurred.Unable to execute JavaScript. Try watching this video on www.youtube.com, or enable JavaScript if it is disabled in your browser.Kamp C was built in one piece. | Video: Kamp CKamp CIn just three weeks, Belgian company Kamp C 3D printed its namesake demo house in one piece, at the property location. Developers claim that the building holds a compressive strength three times greater than conventional brick, which is largely credited to a special printer supplied by COBOD, a 3D-printing construction company. Smooth surfaces and thick layers fortify the trial model. Unlike other projects at the time — and even now — this house features two stories and was constructed in one piece. It’s just under 27 feet tall, about the size of a residential telephone pole, and spans 967 square feet. Its sustainable design uses low-energy floor and ceiling heating, sourced from solar panels and a heat pump.[embedded content]An error occurred.Unable to execute JavaScript. Try watching this video on www.youtube.com, or enable JavaScript if it is disabled in your browser.Mense-Korte is the first 3D-printed house to pass the building regulations of a national government. | Video: The B1MMense-KorteMense-Korte’s 3D-printed house, located in Beckum, Germany, is the first in the world to become fully certified by a national government’s building regulation. This modernist, three-bedroom, three-bathroom home measures 1,722 square feet of living space, complete with a sophisticated interior and smart-home technology. Fortified by multi-shell walls casted with in-situ concrete, the curvy structure took nearly eight months to build, including 100 hours of active printing time. Amenities like a fireplace, bathtubs and a balcony are integral to the design, with spaces specifically molded for second-fix installations.More on 3D Printing Utility 5 3D Printing Applications in Construction[embedded content]An error occurred.Unable to execute JavaScript. Try watching this video on www.youtube.com, or enable JavaScript if it is disabled in your browser.The Quatro residences are built to consume as much energy as they generate. | Video: Mighty BuildingsMighty House QuatroNestled away in a gated, hilltop community in southern California, Ehrlich Yanai Rhee Chaney Architects have built a 20-home, net-zero development that aims to consume as much energy as it generates. Constructed in around four months, each home includes two bedrooms and two bathrooms across a 1,171-square-foot space built on top of a hot spring aquifer. Fitted in a modern, minimal aesthetic, these properties include a swimming pool, hot tub, fire pit and floor-to-ceiling windows. The project collaborator, construction company Mighty Buildings, models its manufacturing process after the automotive industry. Operating highly scalable micro-factories, its 3D-printing methods perform at twice the speed of traditional construction, and, as an additive manufacturer, its projects generate 99 percent less waste, according to the company’s website. Mighty Buildings has also developed a proprietary light stone material that cures into a stone-like composite with four times the tensile and flexural strength of concrete materials currently in common practice of architectural 3D printing.[embedded content]An error occurred.Unable to execute JavaScript. Try watching this video on www.youtube.com, or enable JavaScript if it is disabled in your browser.Project Milestone was printed in five days and 24 separate parts. | Video: Real Estate & Interior Design Project MilestoneProject Milestone — which consists of five 3D-printed concrete dwellings — was the world’s first commercial housing project in its medium, with full intent to legally house residents. The first of these 1,011-square-foot dwellings was printed in 120 hours on-site as 24 separate parts. Matching their backdrop of Eindhoven, a techy city in the Netherlands known for its cutting-edge design, Project Milestone houses resemble elongated boulders with smooth, rounded edges. With extra-thick insulation and a connection to the heat grid, these structures score high marks in energy efficiency, according to online media platform 3D Natives. Its first tenants, Dutch couple Elize Lutz and Harrie Dekkers, received their key on April 30, 2021.[embedded content]An error occurred.Unable to execute JavaScript. Try watching this video on www.youtube.com, or enable JavaScript if it is disabled in your browser.Sourced from local clay, Tecla serves as a proof of concept for sustainable architecture. | Video: WASP TeamTeclaIn development with 3D-printing firm WASP, Italy-based studio Mario Cucinella Architects set out to create bioclimatic, low-carbon proof-of-concept housing in response to escalating climate emergencies and housing crises worldwide. Standing out from the crowd, Tecla’s tan, double-dome structure is constructed out of 350 layers of locally sourced clay from a nearby riverbed. A portmanteau of “technology” and “clay,” Tecla is a 538-square-foot structure that stands at about 15 feet tall and features two skylights. The eco-habitat is made entirely out of organic, bio-materials. Of the 200 hours it took to fully construct the project, the active printing time lasted 72 hours.How much does a 3D-printed house cost?3D-printed houses cost about $10,000 to $400,000 on average, but pricing can vary based on the house’s location, size, amenities and materials used.How long does it take to 3D print a house?To 3D print a house, it may take about 24 hours to three weeks, excluding time for second-fix installations or material transportation if pieces are not printed at the final house location.Where can I buy a 3D-printed house?Some real estate marketplaces like Zillow, or some homeownership assistance programs like Habitat for Humanity, can sell 3D-printed houses.