COBOD Launched VR Solution for 3D Construction Printing
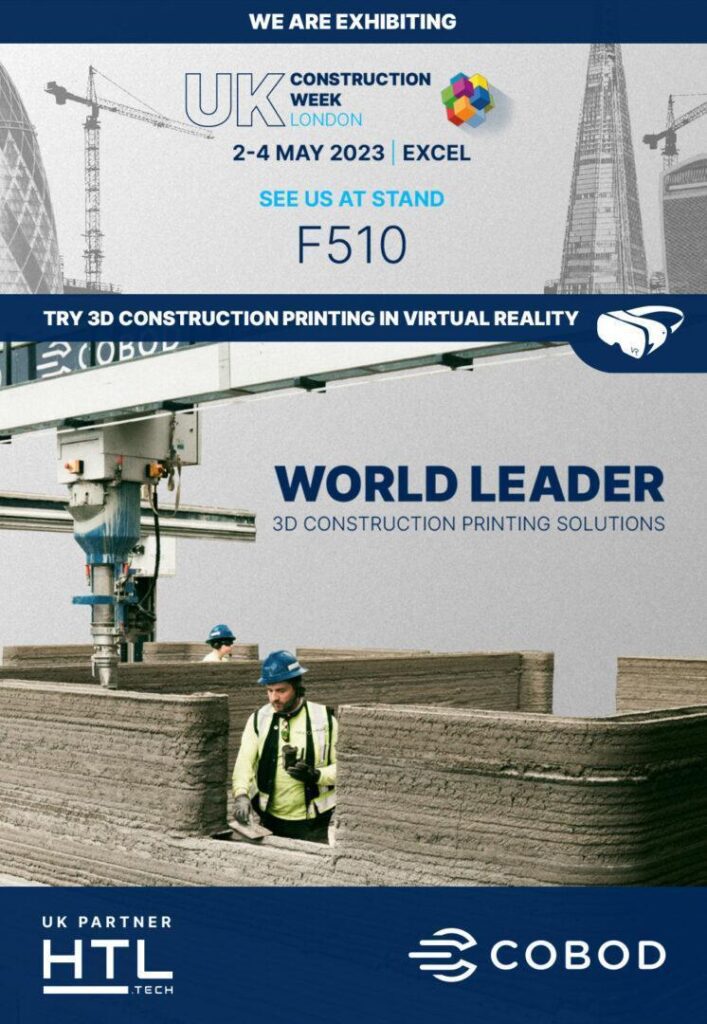
COBOD has launched a VR solution for 3D construction printing, allowing people to experience live 3D printing in virtual reality. The VR solution offers a realistic experience, allowing individuals to watch COBOD’s real printed buildings being constructed in a virtual residential area. COBOD will present the VR solution at UK Construction Week, London, from May […]
Black Buffalo 3D Takes the International Codes to New Heights
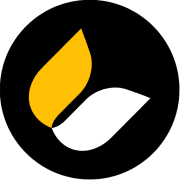
NEW YORK, Feb. 16, 2021 /PRNewswire/ — Black Buffalo 3D Corporation, a leading provider of large scale 3D printers for construction and a member of HN Inc.—formerly Hyundai BS&C Co. Ltd.—today announced its success in working with the International Code Council Evaluation Service (ICC-ES) to revise its ICC-ES AC509 criteria. This update enhances the acceptance criteria (AC) for 3D Automated Construction Technology for 3D printed concrete walls from a single story building construction to multi-story building construction.
Black Buffalo 3D is a global provider of large scale 3D printers for construction and proprietary cement-based ink. Its mission is to increase awareness, efficiency and utility of additive manufacturing in the construction industry. The company continues to invest in its 3D construction printers and material science with the intent to become the first 3D construction printing company to meet ICC-ES AC509. With printers developed by its sister company, Hisys— based in South Korea—the latest model is capable of printing buildings up to 4 stories high.
“We want to build trust and prove the safety of our technology in a way that no other 3D Construction printing company has done before,” remarks Jenn Christman, PE, 3D Product Specialist. “Black Buffalo 3D was created to increase acceptance of 3D printing in the construction industry, revolutionize traditional building techniques and truly showcase the potential of large scale 3D printing.”
Large scale 3D Construction Printing (3DCP) has the potential to help governments, businesses and NGOs address a number of infrastructure needs including closing the gap on affordable housing deficits, speeding up disaster recovery efforts and providing more value to much needed infrastructure improvements throughout the world.
ICC-ES is a nonprofit, limited liability company that performs technical evaluations of building products, components, methods, and materials. Agencies use evaluation reports to help determine code compliance and enforce building regulations; manufacturers use reports as evidence that their products (and this is especially important if the products are new and innovative) meet code requirements and warrant regulatory approval.
As a globally recognized organization, ICC-ES brings legitimacy to code compliance claims and helps developers ensure building regulations are met. 3D Construction printing is a relatively new application with growing interest because when used correctly and safely it has the potential to alleviate affordable housing deficits, speed up disaster recovery efforts and help build much needed infrastructure around the globe.
Black Buffalo 3D will continue to make investments in 3D construction printer technology, material science and form strategic partnerships as it works towards meeting ICC AC 509 acceptance criteria. The company will also continue to capture, analyze and share information regarding the positive impact on reducing the carbon footprint of the construction industry through automation and use of environmentally friendly materials and designs.
For more information on our pilot projects and how to view live demonstrations please follow us on social media or request more information on our website.
About ICC-ESICC Evaluation Service (ICC-ES), a member of the ICC Family of Solutions, is a nonprofit, limited liability company that provides technical evaluations of building products, components, methods and materials. ICC-ES evaluation reports, building product listings and plumbing, mechanical and fuel gas listings provide evidence that products and systems meet requirements of codes and technical standards. Visit their website at https://icc-es.org/
About Black Buffalo 3D CorporationBlack Buffalo 3D Corporation (http://www.blackbuffalo.io) is the NY based, US affiliate of HN Inc. co. Ltd.—formerly Hyundai BS&C Co. Ltd.–and subsidiary of Big Sun Holdings Group, Inc. Black Buffalo 3D is poised to revolutionize construction and become the leading global provider of smart 3D construction printers from one to four stories, proprietary construction “ink” and 3D print construction consulting services.
Press ContactPeter CoopermanHead of Marketing and Strategy311469@email4pr.com(646) 650-5863
Press Contact (ICC-ES)Anna MullenMarketing Manager291515@email4pr.com
ICON’s House Zero Graces the Cover of Austin Home Magazine & Selected…
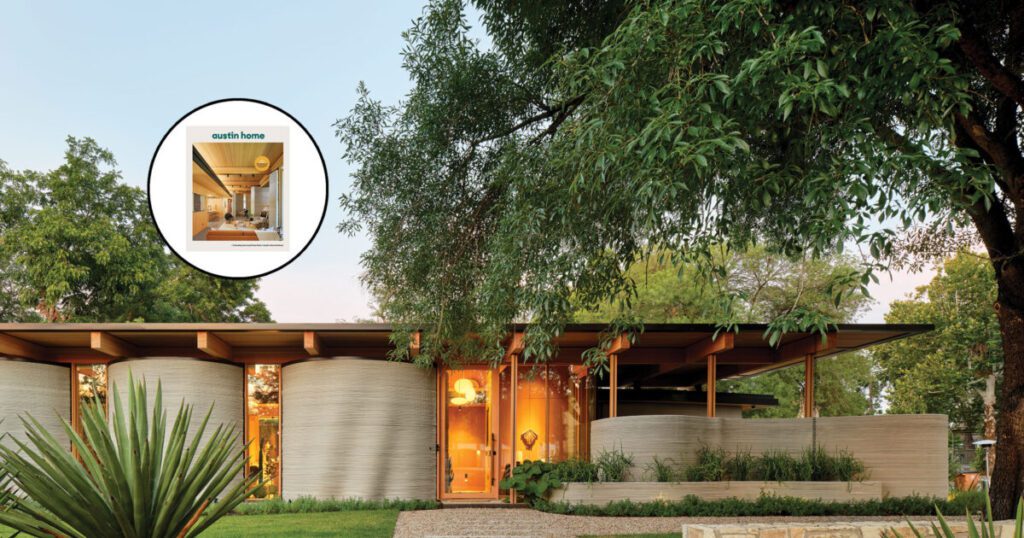
The 36th Annual AIA Austin Homes Tour to feature the innovative 3D-printed home October 22-23, 2022
We are thrilled to share that ICON’s House Zero, designed by Lake|Flato Architects, is featured on the Fall 2022 issue of Austin Home Magazine and has been selected as one of nine homes to be showcased during the 36th annual AIA Austin Homes Tour taking place October 22-23, 2022.
The Austin Home cover story features the most noteworthy people, places, trends and architecture in the design and residential industry. It is an honor for House Zero to be recognized as one of the most “technologically sophisticated” and inviting homes in Austin.
House Zero, unveiled in March 2022, was 3D printed by ICON’s Vulcan construction system and is the first home of its kind and a major advancement in modern architecture. The 2,000+ sq. ft. home with a 350 sq. ft. accessory dwelling unit pushes the boundaries of what’s possible with architecture through automated construction only achievable through 3D printing.
By interweaving biophilic principles with additive construction methods, House Zero was able to create a tranquil and humanistic environment. House Zero blends a mid-century modernist ranch house aesthetic with the digital possibilities of additive construction and is unlike anything that has been designed, to date.
Interested in touring House Zero? Get tickets to the AIA Austin Homes Tour 2022
Read the Austin Home magazine cover story.
PROJECT COLLABORATORSConstruction and Technology: ICONArchitecture: Lake|Flato ArchitectsStructural Engineer: GNAStructural Engineer: WJEMEP Engineer: Integral GroupLandscape Architect: Word + CarrInterior Design: Lake|Flato Architects + ICONLighting Design Consultant: Studio Lumina
ICON’s Receives Honors From Fast Company’s “Brands That Matter”

Awards list honors brands that communicate and demonstrate brand purpose and who have achieved relevance through cultural impact and social engagement
Announced today, ICON has been named an honoree in Fast Company’s second annual “Brands That Matter” list! ICON matters because housing matters.
Fast Company writes that ICON is a company whose “results punch above their weight” and who “has forged their own path in distinct areas–from standing up for employees to homebuilding innovation.”
Fast Company’s “Brands That Matter” list is an extension of the company’s broad-reaching mission and seeks to commemorate companies and nonprofits that have altered the corporate landscape by infusing it with unique takes on culture, social engagement, and purpose while simultaneously creating timeless content that positively impacts our communities.
The Brands That Matter list recognizes 145 brands across 24 categories that have trailblazed and defined what it means to be an impactful company in an ever-changing world. All of the companies on this list have succeeded in devising a way to forge an intimate connection with the public.
ICON is proud to be included among such ingenious changemakers. It is our mission to develop advanced construction technologies in service to humanity in order to solve great problems and pursue grand opportunities. We exist as a response to the global housing crisis. Construction-scale 3D printing not only delivers higher-quality homes faster and more affordably, but fleets of printers can change the way that entire communities are built for the better. The U.S. faces a deficit of 5 million new homes and worldwide there are 1.2 billion humans that lack adequate shelter. There is a profound need to swiftly increase supply without compromising quality, beauty, or sustainability and that is exactly the strength of ICON’s technology.
To read more → visit Fast Company’s Brands That Matter
First fully 3D printed home completed in Paremoremo
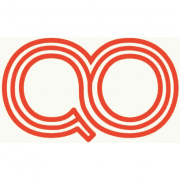
QOROX’s 3D printed concrete technology has achieved yet another first for New Zealand – the completion of the first fully 3D-printed residential home in the Auckland suburb of Paremoremo.
This also becomes the largest fully 3D printed building in the Southern Hemisphere another groundbreaking achievement for Waikato-based QOROX.
The 252m2 family home was designed for a family of four to complement the site’s natural contours and peaceful setting, and features 3D-printed concrete wall panels which provide the perfect backdrop for modern living.
The mastermind behind the home’s unique design features was multi-award-winning architectural firm, Dorrington Atcheson Architects, who said the use of 3D printed technology provided more flexibility than traditional concrete builds.
“It’s pretty cost effective, and you can get the geometric proportions and shapes that you would have to spend a lot of money to get if you did it in traditional concrete construction,” said Tim, director of DAA.
Qorox managing director Wafaey Swelim, said the design provided by DAA allowed them to fully utilise the design capabilities of their 3D printer.
“DAA provided an amazing design which enabled us to fully utilise the design capabilities of our 3D concrete printer and produce a strong, secure and warm home for the owners to enjoy for many generations to come. People who visit the home are so impressed by its calmness and warmth.”
To create the ‘printing ink’ for the home, QOROX utilises its own mortar recipe that is 80% locally sourced. The final product was rendered internally and externally, using full Resene Construction Systems hand applied ROCKCOTE exterior and interior plaster and finishing coats, providing a ‘natural look’ to the wall panels and providing the clients with their desired finish.
Swelim said the flexibility of 3D printed concrete allowed homeowners to add their own personal flair to their homes, without an additional price-tag.
Paremoremo house’s 63 panels, with a total area of 360m2, were prefabricated in Hamilton and transported to site for installation by Qorox’s experienced team, with Senior Construction undertaking the rest of the build.
With 30% less emissions than traditional concrete builds, Swelim said achieving the fully 3D-printed home was another tick in the box for the next evolution in building.
“3D printed concrete is the next evolution in building, and it’s happening right now, right here in New Zealand.
“There are so many advantages to 3D printed technology. Our system allows the formation of wall cavities for insulation, plumbing and electrical wiring, and apply patterns and design elements directly, without the need for additional work.”
The QOROX 3D printed wall solution provides excellent thermal mass qualities helping to create more climate resilient homes that are warmer during the winter months, delivering more comfortable living environments.
“The best part is all of these elements this can be completed without compromising the R-Value (thermal rating) or the overall strength of the build.”
Swelim encouraged architects and homeowners interested in 3D printed concrete to head to www.qorox.co.nz to learn more.
ICON Featured on NBC’s TODAY Show
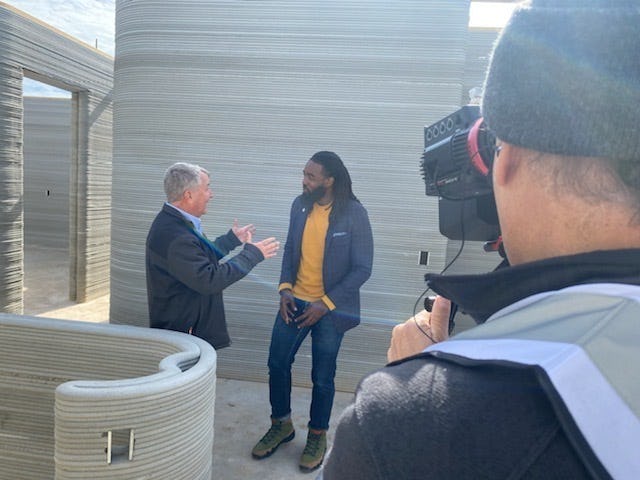
[embedded content]
The #1 morning show in America, TODAY, went behind the scenes with ICON and Lennar to get a sneak peek at a 100-home community of 3D-printed homes located in Georgetown, Texas, just 20 minutes outside of Austin. Codesigned by BIG-Bjarke Ingels Group, the homes range from 1,500 – 2,100+ square feet and feature 8 floorplans, 24 elevations and will be powered by the sun with rooftop solar panels.
ICON’s Dmitri Julius speaking with Today Show correspondent Kerry Sanders at Wolf Ranch in Georgetown, TX.
Correspondent Kerry Sanders watches in real time as these one-of-a-kind, resilient homes are brought to life and speaks to ICON and Lennar leaders about what this project means for the future of homebuilding.
To view the full segment, visit TODAY. To be the first to hear when home reservations open, join the list.
Detroit’s First 3-D Printed Home Has Been Completed
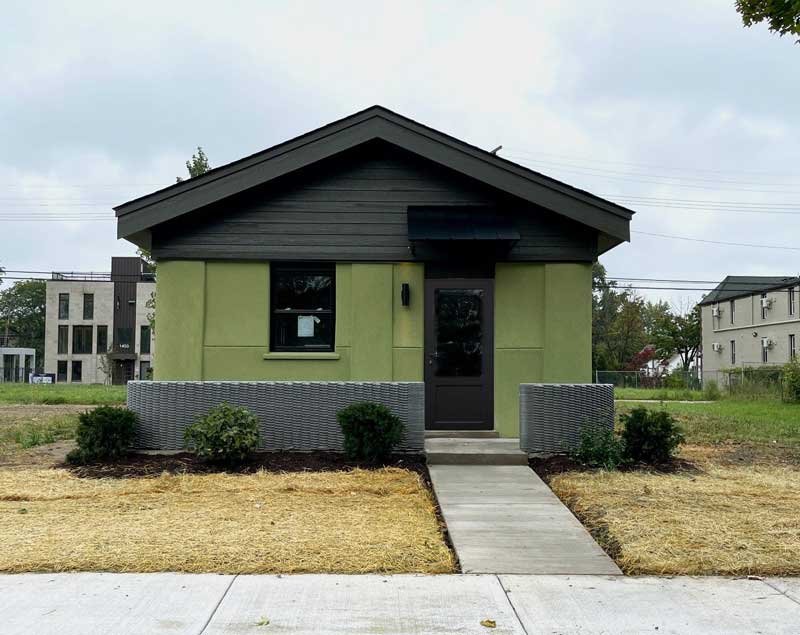
Citizen Robotics and developArchitecture have completed Detroit’s first 3D-printed home. // Photo courtesy of Citizen RoboticsCitizen Robotics in Detroit and Detroit-based architectural firm “developArchitecture” have completed Detroit’s first 3D-printed home, located at 1444 Sheridan in Detroit’s Islandview neighborhood (west of Indian Village).Construction for the 988-square-foot, two-bedroom home began in October 2022, and is the first of many 3-D-printed homes meant to be affordable and more efficient in lowering utility costs for residents. To celebrate the project’s completion, Citizen Robotics will host a ribbon-cutting event at 4:30 p.m. on Feb. 22“This home proves by leveraging digitalization and robotics, we can solve many of the problems plaguing the homebuilding industry,” says Tom Woodman, co-founder and executive director of Citizen Robotics. “We can build right-sized homes, with fewer workers, that cost less to heat and cool. We can build homes with features to support living at any stage of life.”The home began as a 3-D design and was printed with a cementitious mortar using a robotic arm. The innovation behind this method of architecture makes for a more efficient build process that involves less labor, fewer expenses, and more sustainable materials, according to the manufacturer.“It’s rewarding to finally share our pilot home because 3-D printing is the future of architecture,” says Bryan Cook, founder and CEO of developArchitecture. “3-D printing will eventually become a standard method across the industry and Detroit is the perfect landscape for this type of innovation.”The home also received nearly $160,000 in funding from the Michigan State Housing Development Authority’s Neighborhood Stabilization Program to cover the construction materials for the house.Gardner White in Warren is another partner for the project. The company staged the home, including two 3-D-printed tables from its soon-to-be-released collaboration with artist and designer Mike Han.As part of Citizen Robotics and developArchitecture’s mission to increase diversity and inclusion, they partnered with BIPOC individuals across 12 different aspects of the home building process.Future plans for Citizen Robotics include two upcoming workshop series — a 3-D printing roadshow funded by MEDC will travel across six counties in northern Michigan demonstrating 3-D printing for the environment, while a workshop series also is in the works to educate Detroiters about design for 3-D printing and the 3-D printing process.To learn more about the 1444 Sheridan St. home or the ribbon-cutting event, visit citizenrobotics.org or developarchitecture.com.
World’s First 3D Printed Living Seawall gets installed
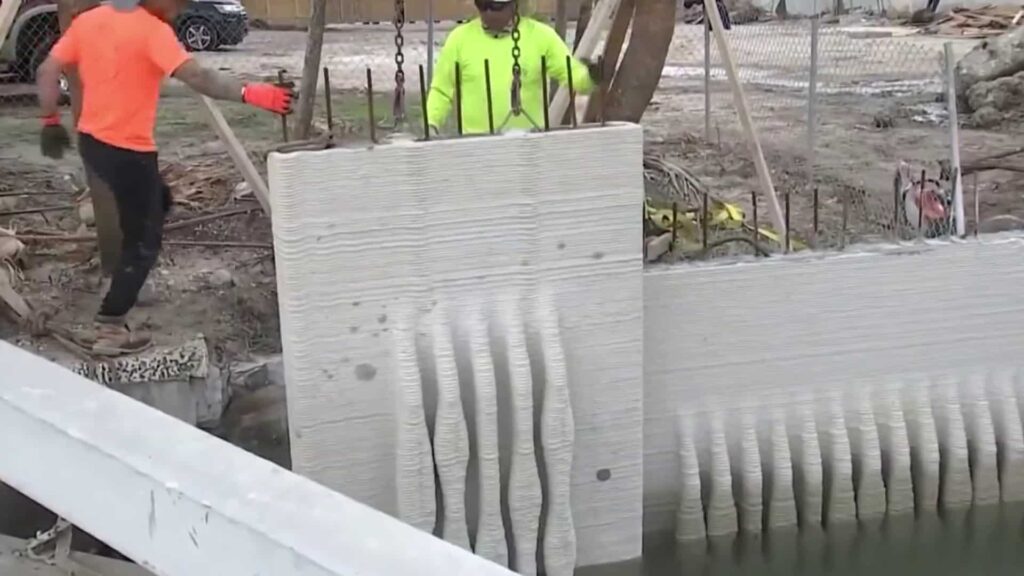
A future homeowner in Miami Beach has become the first to have Kind Designs’ Living Seawalls installed. Opting for this structure specifically to support the environment, they are the recipient of the world’s first 3D printed seawalls. While seawalls to prevent flooding are necessary along the Miami coastline, these Living Seawalls go a step further in environmental protection. In addition to safeguarding the land from erosion, flooding, storm surges, and sea-level rise, Kind Designs‘ Living Seawalls actively contribute to improving the local marine environment. Once installed along the shoreline, the Living Seawalls seamlessly support the needs of local marine ecosystems. Moreover, in addition to enhancing the sea, the seawalls also monitor its quality. Embedded sensors enable the Living Seawalls to measure information on water quality across as many as 15 different parameters.
Code Service report paves path to multi-story, 3D-printed structural concrete
Black Buffalo 3D Corp., a global provider of large scale, building-grade printers and proprietary cement-based ink, has worked with the International Code Council Evaluation Service in Itasca, Ill., to expand criteria in the ICC-ES AC509 – 3D Automated Construction Technology for 3D Concrete Walls report from single- to multi-story building.
Black Buffalo is raising the stakes in 3D-printed structural concrete, engineering equipment capable of placing up to four-story projects.
Operating until recently as Hyundai BS&C Co. Ltd., New York-based Black Buffalo 3D aims to increase awareness, efficiency and utility of additive manufacturing in construction. It continues to invest in printers and material science, intent on becoming the first to meet ICC-ES AC509 criteria. With printers developed by sister company Hisys, based in South Korea, its latest model is capable of printing up to four-story buildings.
“We want to build trust and prove the safety of our technology in a way that no other 3D construction printing company has done before,” says Product Specialist Jenn Christman. “Black Buffalo 3D was created to increase acceptance of printing in the construction industry, revolutionize traditional building techniques, and showcase the potential of large scale printing.” The latter concept has the potential to help governments, businesses and non-governmental organizations address a number of infrastructure or affordable housing needs and speed disaster recovery efforts, she adds.
ICC-ES is a nonprofit, limited liability company that performs technical evaluations of building products, components, methods, and materials. Agencies use evaluation reports to help determine code compliance and enforce building regulations. Manufacturers or suppliers use reports as evidence that their equipment, products and materials meet code requirements and warrant regulatory approval. — Black Buffalo 3D Corp., U.S. affiliate of HN Inc. co. Ltd., www.blackbuffalo.io
PRINTING TECHNOLOGY PRIMER FOR BUILDINGSThe Ohio University Russ College of Engineering and Technology presents concrete methods in “3D Printed Buildings Guide: Required Materials, Tips, and Resources” as part of a Master of Science in Civil Engineering degree overview, posted under Engineering & Technology Degrees at https://onlinemasters.ohio.edu. The guide provides an overview of 3D-printed buildings; project scheduling and labor-saving advantages; challenges for adoption of the casting/fabrication method; and, construction-grade printing materials.
“3D printing technology has had a revolutionary impact on enterprises around the world. It enables businesses to quickly develop models and prototypes, expediting their ability to test and fine-tune new products. It also makes it easy and affordable to manufacture pieces and components that keep important machinery working as intended,” guide authors explain. “One of the most exciting applications of 3D printing technology is in the construction industry, where it being used to construct entire homes, office buildings, and other structures. 3D-printed buildings can span thousands of square feet and multiple stories, and they can be made with lower costs and less waste than traditionally constructed buildings. [They] represent one of the most significant construction and design trends for civil engineers.”
Authors describe the basic process flow: 3D printing employs large-scale machinery into which an engineer inputs floor plans and building designs, and operators feed concrete ink or other printable building material; a software-guided extendable arm, or nozzle, then applies the material or mix in thin layers; the entirety of the building or structure emerges according to the engineer’s specifications, one layer at a time. Among benefits of 3D printing methods: Materials are consumed at exact volume requirements, free of waste, as printers can precisely follow blueprint dimensions and specs.
Construction tech startup partners with NASA on otherworldly 3D-printed homes that can sustain natural disasters — and possibly even space
Journalist Lesley Stahl’s introduction to her recent “60 Minutes” story about 3D printers sums up the initial promise of the unique technology.
“There was a time when futurists were predicting that the advent of 3D printing was going to change our lives — that each of our houses would have a 3D printer to make whatever items we need,” she said in a video clip.
While that isn’t yet the reality, the tech has taken perhaps an even more interesting path. 3D printers are actually building homes around the country.
[embedded content]
What’s more, Texas-based ICON has earned a nearly $60 million contract from NASA for its Project Olympus, to develop space-based 3D construction processes for an eventual trip to the Moon — and farther. The project builds upon other space-based research ICON has completed, per a company press release.
“To change the space exploration paradigm from ‘there and back again’ to ‘there to stay,’ we’re going to need robust, resilient, and broadly capable systems that can use the local resources of the Moon and other planetary bodies,” ICON CEO Jason Ballard said in the statement.
ICON has already made a name for itself in 3D printing. The company is working on a project in its home state that will be the world’s largest 3D community. There are 46-foot-wide printers deployed on-site to create the 100 homes, which have solar panels to maximize sustainability, as CNN reported.
#cool_newsletter_374fb93f-e633-47a3-9403-16a81b6718e0 .cool_newsletter__inner span{color:#000000}
JOIN OUR NEWSLETTER
Good news, green hacks, and the latest cool clean tech — straight to your inbox every week!
The tech is touted as creating less air pollution than traditional building methods, with a host of other benefits, including withstanding 200-mile-an-hour winds and being fire-resistant and termite-proof, according to 60 Minutes.
“That’s why this feels like lightning in a bottle,” Ballard told 60 Minutes.
As part of the NASA job order, ICON’s team will be working in support of the agency’s Artemis program, aimed at putting the first woman and person of color on the Moon for new types of exploration, according to NASA.
“In order to explore other worlds, we need innovative new technologies adapted to those environments and our exploration needs,” Niki Werkheiser, from NASA’s Space Technology Mission Directorate, said in the ICON press release. “Pushing this development forward with our commercial partners will create the capabilities we need for future missions.”
ICON’s advanced hardware and software will be leveraged. The team will have access to lunar rock samples from Apollo missions to study their properties in simulated lunar gravity, to use as much material sourced from the Moon (or one day Mars) as possible.What they learn about the Moon’s rocks will help the team determine how their 3D equipment can one day build “landing pads, blast shields, and roads,” all per ICON. It’s the infrastructure needed for human existence on foreign worlds.
“The final deliverable of this contract will be humanity’s first construction on another world, and that is going to be a pretty special achievement,” Ballard said.
Join our free newsletter for weekly updates on the coolest innovations improving our lives and saving our planet.
Cool Picks
Open-Air Kenyan Holiday Homes
Italian design studio PAT works together with fellow architect Ferdinando Fagnola on the Falcon House renovation project that is located on Kenya’s Manda Island. The holiday home is defined by open-air bedrooms and terraces that are raised to overlook the lush surroundings over the treetops. The self-sufficient building provides its water and electricity with passive […]
Monticello business aims to 3D print biggest building in the Midwest with new technology
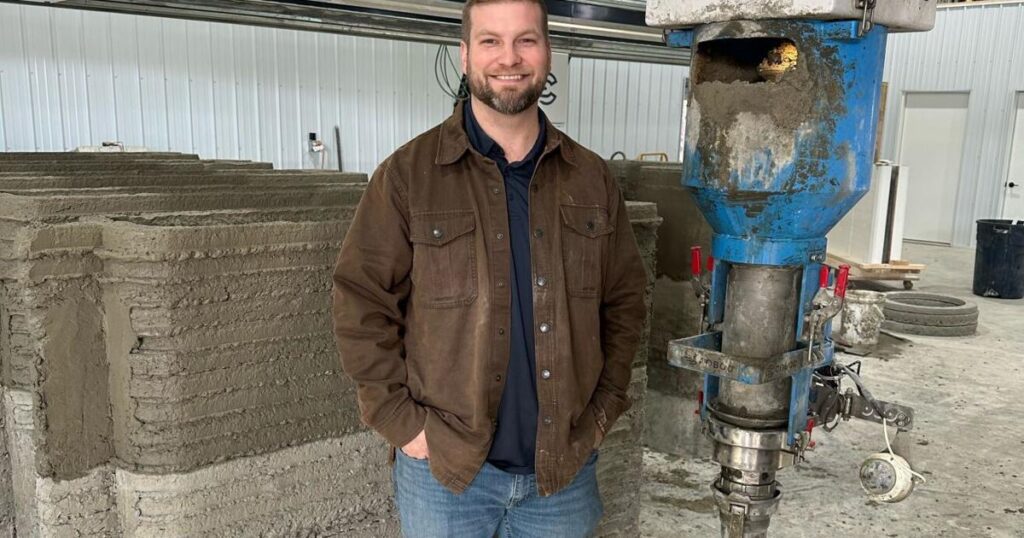
MONTICELLO — Monticello will soon be home to the largest 3D-printed building in the Midwest.At least that’s what Nathan Lilly, founder of LX 3D Concrete Printing, plans to make happen, and he’s only just getting started.His company uses a large-scale 3D-printing machine equipped with a patented nozzle and custom concrete recipe to print buildings that Lilly said are more resistant to flood, mold, fires and tornadoes than structures made out of typical materials.
The buildings are also more energy- and cost-efficient, and require significantly less time to construct. The printer can lay down 10 inches of concrete a second, so the walls of a 2,000-square-foot building can be built in less than 20 hours.The method, Lilly said, carries the potential to revolutionize housing to become more affordable, durable and less supply-chain dependent.“We’re really making a structure that would be prohibitively expensive to compete with if it was truly in wood,” Lilly said.“Here’s an easy way to explain it. There’s a book called ‘The Three Little Pigs,’ right? We’re on house number two and we’re changing it to house number three.”Lilly printed his first building, a 1,500-square-foot structure in Monticello, last fall. He said he’s now only waiting on permits to be approved before he starts printing an 8,000-square-foot combination-industrial-office building this spring that he plans to later lease.Born in central Illinois, Lilly said he worked in real-estate investment and development — most recently as the chief financial officer for the student housing company JSM Living in Champaign — before he started LX two and a half years ago.The idea started, in part, after his parent company, Lilly Capital, a private-investment firm, began looking at acquiring a chain of local hardware stores.But a team member posited that hardware stores would probably be put out of business, Lilly said, if a shop could print whatever part a customer needs right then and there and not have to carry inventory.Lilly said he then decided to look into printer technology and acquired a $1 million concrete printer from the Danish company Cobod. The machine can print 25-foot-tall walls without being moved.
Though the machine runs with typical-grade concrete, Lilly said he tinkered with the ratio of its ingredients and developed a special nozzle to allow the machine to print buildings that look like they’ve been constructed using traditional methods.A common critique of concrete construction is that cement requires high heat and a large carbon footprint in order to bind to local aggregates. Lilly said he’s conducted tests with more environmentally sustainable alternatives, but those alternatives have not been structurally approved yet.“The printer is really just a delivery vehicle,” Lilly said. “So it’s very easy for us to adapt and change to any material design improvements, whether it’s fly-ash or some alternative that dramatically reduces the carbon footprint of actual cement.”Further, the construction of 3D-printed buildings nets less waste because the company only manufactures what materials they need from a mixer on-site, Lilly said. And concrete buildings can last much longer than structures made primarily of wood or plastic.Lilly’s number one goal in starting LX was to create homes, but he added that it would be foolish to restrict the company to only use. That’s because printing technology has the potential to create other concrete items more efficiently, like concrete tubes for city utilities.For example, Lily said he already scoped plans to mass-produce a three-year’s supply of lids for a septic tank company in one day.“Initially, we were just planning to subcontract for larger volume home buildings, but we kind of realized that the only way to add value to the most people possible is to not turn people down,” Lilly said.“Really, if anyone wants a structure built, we’re certainly going to be open to it. Our goal is to invest really heavily into the space and shelter the whole world if we can — at least the Midwest.”
Printing Swedish houses with algae
For the first time, a new material made from tiny cellulose fibers and algae has been tried as a more environmentally friendly option for construction.
Researchers from Chalmers University of Technology and the Wallenberg Wood Science Center in Sweden experimented with this sustainable material and found it can be used to create various architectural components using less energy than traditional methods.
The construction industry is a major contributor to global pollution, using half of the world’s fossil fuels, generating 40% of waste, and producing 39% of carbon dioxide emissions. To combat this, scientists are exploring biomaterials like nanocellulose, which is already used in biomedicine for its ability to be 3D printed into structures for tissue growth. This study marks the first attempt to use dried nanocellulose in architecture.
By mixing nanocellulose fibers with water and an algae-based substance called alginate, the researchers created a material that could be 3D printed. This blend provided flexibility to the material when it dried, enabling its use in architectural applications.
The use of 3D printing in architecture is seen as a resource-efficient method. Unlike traditional methods that produce waste, 3D printing requires fewer materials and less energy, particularly when using a robotic system that operates at room temperature. The properties of the nanocellulose hydrogel allow it to be easily printed and maintain its shape without requiring high temperatures.
The researchers tested various printing techniques to understand how the material behaves when dried in different shapes. These dried shapes could be used to create lightweight architectural elements such as room dividers, blinds, wall panels, and coatings for existing building components.
This study lays the groundwork for further exploration of nanocellulose in architectural design, highlighting the need for new approaches to incorporate biobased materials into buildings. Understanding the properties and design possibilities of these materials is crucial for creating sustainable and aesthetically pleasing structures that align with the goals of a circular economy.
Robotically 3D printed architectural membranes from ambient dried cellulose nanofibril-alginate hydrogel“, published in the journal Materials and Design.
#GreenBuilding #SustainableDesign #Nanocellulose #Architecture
Completed Data Center Is Europe’s Largest 3D Printed Building – 3DPrint.com | The Voice of 3D Printing / Additive Manufacturing
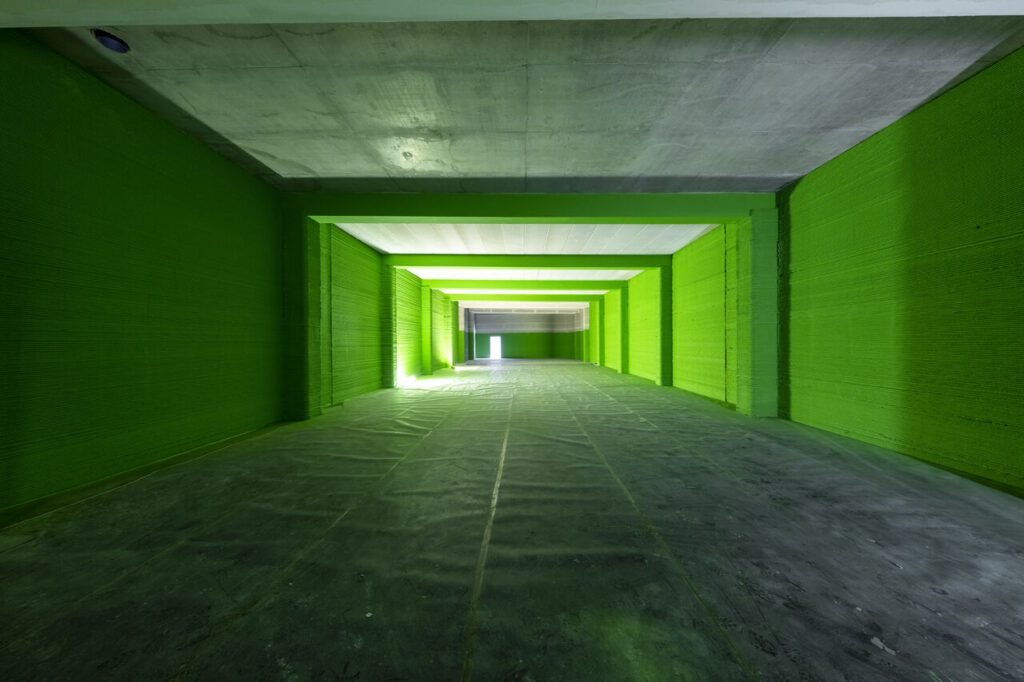
As exciting as 3D printed homes are, particularly when part of a feel-good story, it is the industrial applications of the technology that may represent the maturity of the additive construction (AC) sector. This is made evident with the completion of Europe’s largest 3D printed building, the Wavehouse data center in Germany, which is described as the first of its kind in the industrial and data center sectors globally.
Developed by Kraus Group, with participation from architecture firms Mense-Korte and SSV, this single-story facility is situated in the Baden-Württemberg region of Heidelberg. It took the PERI Group, an investor in AC firm COBOD, about 140 hours to complete the nearly 600-square-meter building using a BOD2 3D printer. According to the companies involved, about 450 tons of printing concrete, provided by Heidelberg Materials, were used. This material is described as both 100% recyclable and featuring a binder capable of achieving a 55% CO2 reduction compared to traditional Portland cement.
Building Leaders Serious about Construction 3D Printing
Founded in 1874, Heidelberg Materials is a €21.095 billion company, with 57,000 employees working at 3,000 production sites across 60 countries. This puts it on par with COBOD investor and materials company Holcim and somewhat ahead of COBOD investor and materials company CEMEX, as well as Swiss AC backer and materials company Sika. All are less than half the size of the €51.2 billion French materials giant Saint-Gobain, which is pursuing AC through its Weber Beamix subsidiary. There are only some of the leading construction businesses exploring the technology, but they are representative enough to demonstrate just how serious the sector has become.
What’s also interesting is the overlap by these firms in the AC space. As noted, several are COBOD investors, while both PERI Group and Sika have backed another construction 3D printing startup, Mesh AG. The technology of COBOD and Mesh are complementary, in that Mesh can 3D print steel reinforcement for 3D printed buildings, such as those made with COBOD’s machines. However, one would think of Sika, Holcim, and CEMEX as competitors. Obviously in global business, multinational corporations share much in common and similar goals in terms of “growing the pie,” but the extent to which these frenemies can coexist investing in the same startup is difficult to foresee.
Construction 3D Printing and Infrastructure, Growing Together
The Wavehouse will be operated by Heidelberg iT Management, a local cloud and data center provider with a history dating back to 2001. The center is expected to offer 500kW of power and accommodate around 100 racks. While the facility’s 3D printed shell has been completed, the total job is expected to be finished by the end of the summer.
While the Wavehouse is a more traditional form of data center, EdgeCloudLink in the United States plans to pursue the construction of hydrogen-powered, off-grid modular data centers built using 3D printing. The market for data center construction is massive, with some analysts projecting a seven percent growth from $250.4 billion in 2023 to $270.07 billion in 2024. This makes sense given the growing need for servers in general, thanks to such technologies as artificial intelligence and cloud computing.
In order to keep up with demand, builders will likely turn increasingly to AC as a means of constructing these structures more quickly, while also demonstrating the ability of 3D printing to make facilities that can meet the requirements of data centers in terms of cooling and structural integrity. This trend would complement other infrastructure projects that AC will certainly play a role in, such as new rail systems, power generation, disaster relief, and general construction.
All images courtesy of Heidelberg Materials.
Subscribe to Our Email Newsletter
Stay up-to-date on all the latest news from the 3D printing industry and receive information and offers from third party vendors.
Please enable JavaScript to view the comments powered by Disqus.
Guatemala receives first 3D printed building
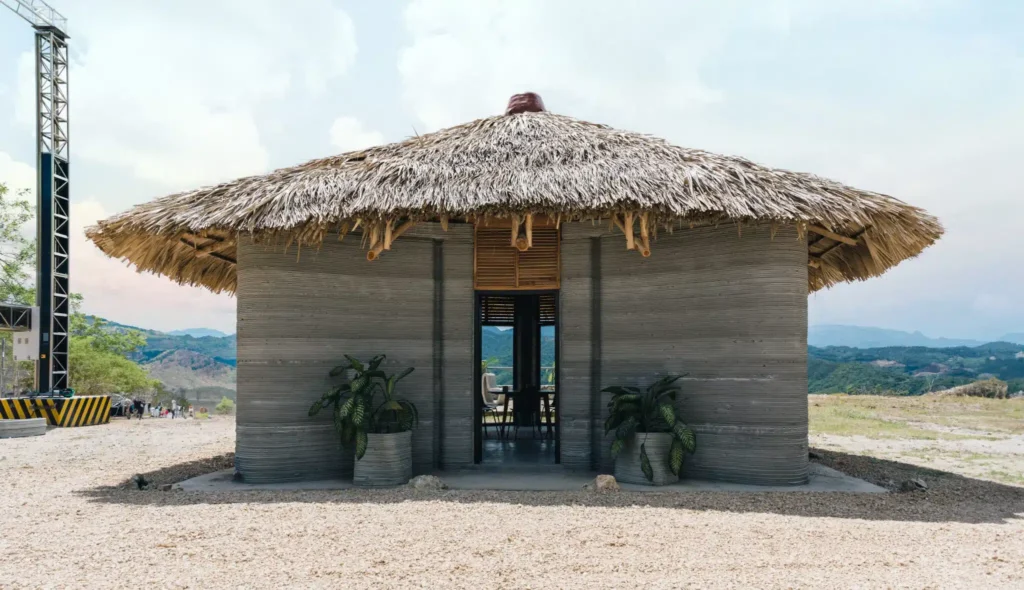
Stay up to date with everything that is happening in the wonderful world of AM via our LinkedIn community.
Progreso, a leader in Central and South America’s cement industry, has inaugurated Guatemala’s first-ever 3D printed building, through its corporate accelerator, Progreso X. The milestone was achieved in collaboration with Danish 3DCP Group, utilizing COBOD International’s BOD2 construction 3D printer.
The project has successfully taken steps to validate the structural viability of 3D construction printing in a seismic-prone region. The build, featuring 3m (9 feet) high 3D printed walls, was completed in just 26 printing hours, over seven days.
Due to the use of 3D printing, the house features highly organic-shaped walls that would otherwise be extremely expensive, or even unfeasible to complete with concrete blocks – the region’s predominant building material.
The 3D printed concrete walls are complemented by a “Rancho” type palm leaves roof. This roof type has been used for generations in Latin America, as it is inexpensive, provides thermal comfort, and is well-suited for seismic regions due to the flexible and lightweight nature of the material.
“With immense satisfaction, we completed this unique project using 3D printing technology, once deemed distant. Progreso’s enduring spirit of innovation led us to explore new methods, culminating in a collaboratively designed building featuring a sustainable “rancho” roof, ensuring natural cooling in seismic regions. This achievement, a testament to our teamwork, harmoniously blends advanced technology with local traditions, thanks to the unwavering support of 3DCP Group and COBOD,” said Plinio Estuardo Herrera, Manager of Concrete R&D at Progreso.
The project, representing Guatemala’s entry into the world of advanced global construction methods, was achieved through a partnership with Denmark’s 3DCP Group, widely known for 3D printing the first school in Ukraine as part of the reconstruction of the country. The partners will reportedly be working on more projects in the region.
“The completion of Guatemala’s first 3D printed house living up to all seismic requirements marks a significant milestone for construction 3D printing in Latin America. The region has adopted 3D construction printing slower than others, but the interest is growing rapidly. We expect interesting new developments to happen shortly, including in Mexico, especially now that successful steps have been taken to verify the suitability of the printing technology in a seismic region,” said Philip Lund-Nielsen, Co-Founder and Head of Americas of COBOD.
Rogers OKs 3D-Printed Housing Development, the First in Arkansas
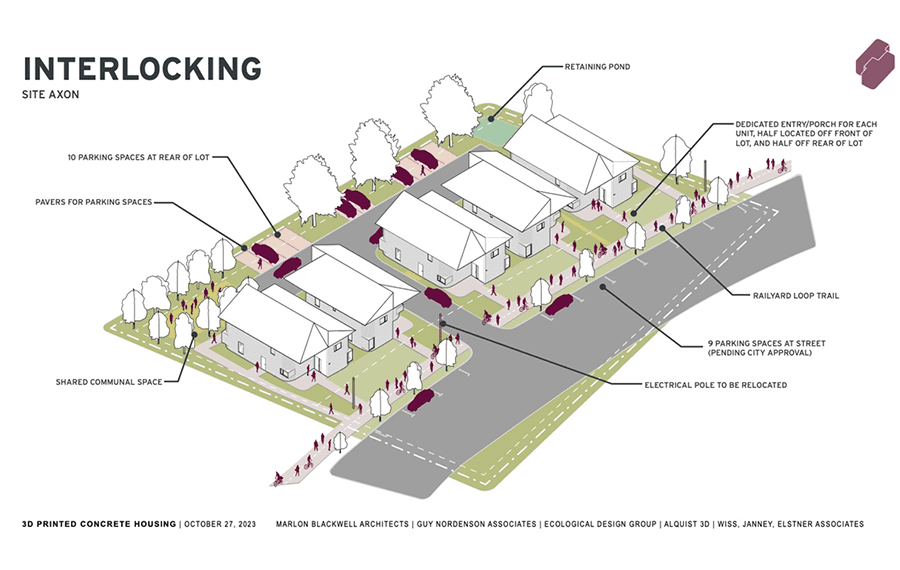
Plans for a 3D-printed housing development in Rogers (Rogers Lowell Chamber)
A 3D-printed housing development said to be the first of its kind in Arkansas is moving forward, the Rogers Lowell Chamber announced.
The Rogers City Council recently approved the $50,000 sale of an acre of land for the project, which will use 3D-printed concrete to construct at least four two-story duplexes with eight units apiece. The duplexes will range from 1,300 SF to 1,600 SF.
Construction is scheduled to begin in late spring or summer, with occupancy targeted by late 2024.
Groundwork Northwest Arkansas, the Northwest Arkansas Council’s workforce housing center, is leading the project. The organization is collaborating with Alquist 3D of Greeley, Colorado, which is known for using robotic technology capable of building a 1,500-SF home in 30 hours.
The project at 920 S. First Street near downtown Rogers aims to help address the region’s lack of affordable housing. The homes will be sold to buyers who earn below more than 80% of the area’s median income.
Home prices in northwest Arkansas have surged as the region’s population has grown. In Benton County, where Rogers is located, the average sale price in the second half of 2022 was $423,564, up more than 77% from five years ago.
“We’ve got to look for ways to build more efficiently that will bring these building costs down,” Duke McLarty, director of Arkansas Groundworks, told Arkansas Business news partner KFSM.
People looking to rent have few options. The multifamily vacancy rate in the region is “functionally zero,” according to the latest Arvest Bank Skyline Report.
Groundwork is also behind a housing development in Springdale called “Big Emma.” Thirty of the development’s 77 units will be permanently reserved for households earning below the region’s median income. The project is supported by a grant from the Walton Family Foundation.
Arkansas’s First-Ever 3D-Printed Homes Project Gets Approved
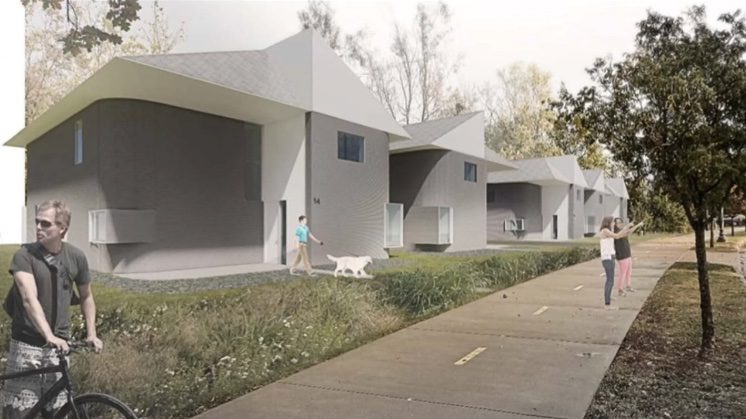
Arkansas’s first-ever inaugural 3D-printed housing project has received the green light from the Rogers City Council, which approved selling an acre of land to the Northwest Arkansas Council Foundation for the development. The project is aimed at addressing housing affordability.The foundation’s affordable housing division, Groundwork Northwest Arkansas, will use 3D-printed concrete technology to build two-story duplexes at 920 S First Street for those earning below 80 percent of the area’s median income. The sale of land was sanctioned at $50,000.“This will be one of, if not THE, first two-story residential 3D-printed homes in the U.S., and it is the first 3D-printed home in Arkansas,” Groundworks Executive Director Duke McLarty said.For the project, Groundwork will partner up with Alquist 3D, a company known for using robotic technology to create 3D-printed concrete homes, capable of building a 1,500-square-foot home in 30 hours.“At least four structures” comprising “at least eight units of housing” are expected to come from the project. These will feature two-story duplexes ranging from 1,300 to 1,600 square feet.Construction is expected to begin in late spring or summer, with occupancy anticipated by late 2024.To learn even more information about this groundbreaking project, click here.READ ALSO: ASO PLACES FINAL BEAM ON NEW $11.75M MUSIC CENTER
Godrej & Boyce builds 500-sq-ft office in 40 hours with 3D construction printing technology
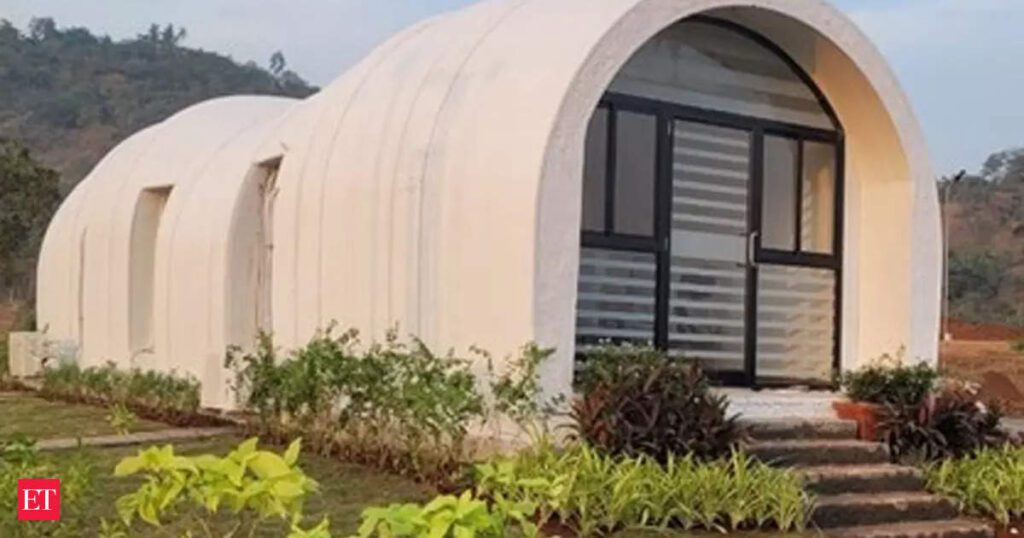
Godrej & Boyce, the flagship company of the Godrej Group, has constructed a 500 sq ft office in the company’s own greenfield campus at Khalapur near Mumbai in a 40-hour timeframe.
The First House Made With 3D Printing and AI Announced In Portugal
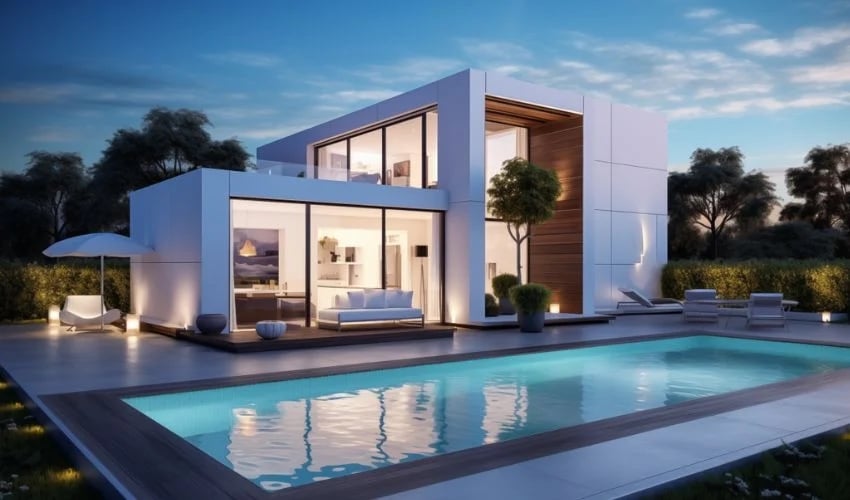
As we all know, additive manufacturing is being implemented in a growing number of sectors. One example is construction, where 3D printed housing is booming. In fact, soon we may see the first 3D printed house in Portugal. Not only that, but the house will be made not just using 3D printing but also artificial intelligence (AI).If you have been following us for a while, you must know that in the past two years there have been all kinds of 3D printed homes unveiled. This of course ranges from low-cost housing designed to alleviate the housing crisis to homes that have been optimized and designed to be more sustainable. In fact, it has grown so significantly that the construction 3D printing market is expected to grow in value from $3.5B in 2023 to $400 billion by 2030. Now, the company Litehaus has also decided to put its hat in the range by focusing on sustainable construction for luxury housing.A mock-up of what the house is expected to look likeMaking a House With 3D Printing and AITo be located in Torres Vedras, Portugal (only 30 minutes from Lisbon!), this house, as mentioned, will be made by combining 3D printing and AI. During the initial creation and design phase, Litheaus, has made use of AI to create the interior and exterior design of the home. This is a significant breakthrough for the construction and 3D printing industry.The manufacture of this type of modular buildings with 3D printing has a number of very important benefits. One of them is related to energy consumption. As we can well imagine, the energy consumption of a 3D printed house is lower than that of a house built by traditional methods, but how low is it in comparison? The answer is that 67% less energy is needed if the house is built in 3D. This will hopefully put a dent in the estimated 42% of carbon emissions for which the construction sector is responsible.Another big advantage is speed, as Simi Launay, creative director of Litehaus, explains, “This technology [allows] us to produce as much as 45m2 of walls in only 20 hours.” As most of the 3D printing of this home will be focus on the walls, this is not insignificant. Indeed, the hope is to build up to 100 houses a year in the country, starting from a complex of thirteen houses!Launey further explained the purpose of this project, concluding: “Litehaus is embarking on a mission to redefine living spaces, fusing AI technology, 3D printing and modular homes to create buildings that resonate with simplicity, innovation and sustainability. Our goal is to build 70% faster and 20% cheaper, delivering residences that epitomize elegance and minimalism harmonized with Portugal’s natural beauty.” You can find out more on the company’s website HERE.A look at the backyard, including a poolWhat do you think about the use of 3D printing and AI in building construction? Let us know in a comment below or on our LinkedIn, Facebook, and Twitter pages! Don’t forget to sign up for our free weekly newsletter here, the latest 3D printing news straight to your inbox! You can also find all our videos on our YouTube channel.*All Photo Credits: Liethaus
‘First-ever’ 3D printed low CO2 concrete building unveiled
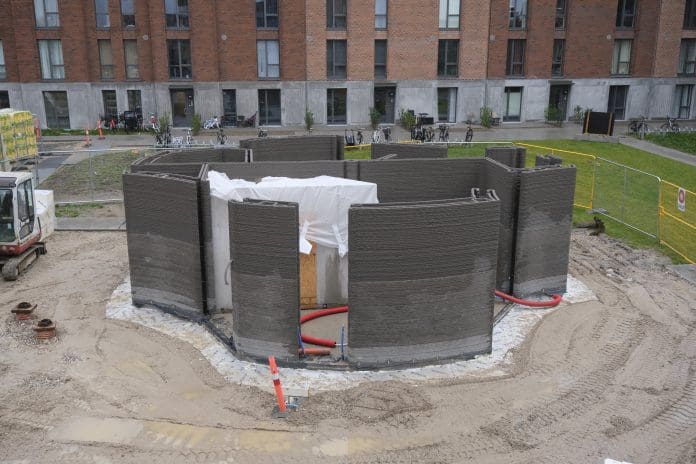
First low CO2 concrete building 3D printed in Copenhagen made by 3DCP Group – a 72 m2 (775 SF) community building.
The debut of a 3D-printed, low CO2 concrete building in Copenhagen marks a transformative leap in construction methods
Partnering with 3DCP Group, AKF introduces a pioneering structure featuring environmentally friendly materials and an adaptive construction process.
Once complete, the low CO2 concrete building will house a gym, a guest room and a common laundry facility for residents.
Special low CO2 cement with 30% lower CO2 footprint was used in the concrete
To further reduce the CO2 footprint, the entire AKF project was printed using low CO2 cement, which has a carbon footprint of 30% lower than normal cement.
The low CO2 cement was mixed with local sand and gravel and turned into 3D printable concrete using the D.fab admixtures method developed by Cemex and COBOD.
Compared to 3D printing of mortars, the low CO2 cement 3D printable concrete reduces the CO2 footprint by 50%.
The low CO2 concrete building was printed using five printing days
AKF sees significant potential in 3D printing technology that goes beyond concrete and envisions a future where natural resources like clay-rich soil can be used for 3D-printed construction.
Vibeke Lorenzen, the technical director at AKF, said: “3D printing opens the door to a world of possibilities, and hopefully, we can contribute to pushing the industry’s traditional construction methods”.
Saga Architects, who also designed the first building 3DCP Group made in Denmark, strived to make the community building appear forthcoming and friendly by using a lot of wood for the decorative parts and organic shapes for the walls, a detail virtually impossible to make with conventional methods.