3D printed concrete housing coming to Rogers
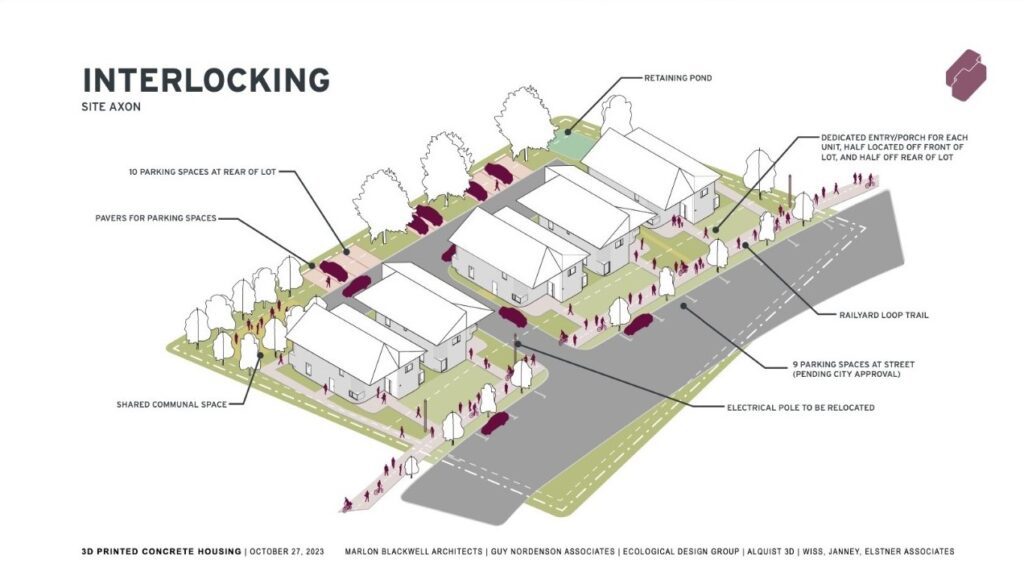
ROGERS, Ark. (KNWA/KFTA) — The city of Rogers approved to sell city-owned land to the Northwest Arkansas Council’s subgroup “Groundwork” to develop and produce a 3D-printed home.
This will be the first 3D-printed home in the state of Arkansas and the first two-story printed homes in the entire country according to Duke McLarty, executive director of Groundwork Workforce Housing for Northwest Arkansas.
He says there’s going to be a lot of people who are learning a lot through this process.
“With the goal that if a developer identifies cost savings through using 3D printed concrete as opposed to a normal just lumber approach, a lot of the barriers and potential constraints of that construction will have already been identified and worked out through our demonstration process,” McLarty said.
Renderings of 3D Printed concrete housing, provided by Duke McLarty, executive director of Groundwork Workforce Housing for Northwest Arkansas.
McLarty says Groundwork is the business community’s response to affordability. They are trying to raise awareness and work with municipalities, cities, and major employers and identify roles that each of them can play to try to bring some level of affordability back to the region.
“We think about it a lot as bringing some level of affordability back to each community in our region, because right now, many communities are not affordable for much of our population,” he said.
McLarty says the site is designed for four or five duplexes that are two stories located on 920 South 1st Street in Rogers.
He says he chose this location because it was close to downtown Rogers.
“They each have their own appeal, but many of them are no longer affordable for a lot of people in our region.”
There is also a bike path in front of the land, which McLarty sees as a huge advantage.
“People who work in the downtown Rogers Restaurants and bars and coffee shops and retail establishments could easily live in one of these and get to and from work on a bicycle and really would lessen their reliance on an automobile,” McLarty said.
Stormie Kuth is a renter in Downtown Rogers and she says ‘for something new like this to come in would be amazing.’
She says she would like to be a homeowner one day but renting might be her reality for the rest of her life because of unaffordable housing.
Kuth says she is happy that there will be more affordable housing in the area because it is an issue.
“I’m lucky that I am paying what I am paying. But I know a lot of people are struggling right now,” Kuth said.
She says she’s heard stories of local children having to stop going to school in the area and move into rural areas instead because it was more affordable for their families.
“Which is absolutely terrible and traumatizing,” she said.
Kuth says she would consider living in a 3D printed home but it would depend on the affordability and sustainability of it.
3D-printed homes have electrical and plumbing installed similarly to a traditional home but there are some differences.
McLarty says “So instead of, you know, lumber and drywall or a printer comes on site, it has a robot arm and it layers concrete to build these walls.”
He continues saying once the concrete dries, drywall can be put on the inside.
“It would feel and look no different than most homes that we’re used to in northwest Arkansas. It can be painted, it can be, you know, a typical and normal roof can be put on it,” he said.
He says 3D printed homes take a lot less manpower, less time to construct, and can be more affordable than traditional homes.
“They’re much stronger, you know, to say, extreme weather events, tornadoes, hurricanes. They’re also much more energy efficient; they’re just a tighter seal, so they’re not as drafty. Studies have shown them to be as much as 30% more energy efficient,” he said.
They’re also more fire-resistant than a wood-built home and don’t rot.
McLarty says, “I think it’s likely to catch on in the US and I’m doing my best to prepare at least our region to be in a good place, when that happens, we’re in a good place to capitalize.”
3D-printed homes are a little cooler than traditional homes and have echoes.
“I think folks will find ways to put rugs down and things like that to kind of dampen echoes, but I’m excited about it as well,” McLarty said.
He says their goal is to have eight to ten families who couldn’t afford to live in Rogers, call it home one day.
Their second goal is to get the development community, municipal community, real estate community, fire inspectors, and building inspectors comfortable with this new approach.
“So that when the next developer comes in and wants to use 3D printed concrete, all of those entities say, “No problem, we know what this is. You know, we’ve experienced it. We’ve seen it print. We’ve been on-site when electrical was being run through the wires,” he said.
He hopes this will give developers another tool to expedite development and keep growth going in Northwest Arkansas.
He says the sale price of the home is unknown but they are currently working on trying to find a builder to build the duplexes and they’re expecting some bids back in the upcoming weeks.
But they are targeting someone that makes around 80% of the area’s median income which is about $75,000 or $80,000 a year.
McLarty says, “We will income verify them to ensure that that the end product is going to the family that really needs it and it’s not someone who just thinks it’s cool and you know likes the location and likes the design it will have a mission focused buyer in the end.”
McLarty says they’re also narrowing in on a developer and finalizing their land purchase from the city of Rogers.
“There are a few things on the site that need to be done that we were hesitant to do until we had ownership of that land,” he said.
He says this project should be underway in late spring or summer with dirt work, roads, parking spots, and then the homes.
He hopes everything will be completely finished by the end of the year or early 2025.
McLarty says, “I mean that’s one of the advantages of using this approach is once, you know, kind of the plumbing and the underground work is in place, the robot can show up and they can print a 2000 square foot home in 36 hours or so with as few as two people.”
There will be an opportunity for the public to come by, look inside the walls, and get comfortable with this approach.
“I think some residents, if asked, do you want a traditionally built home or a 3D printed home, they might, you know, just opt for the traditionally built home because they don’t know. This will give them an opportunity,” he said.
Kuth says she thanks the city of Rogers for doing this and hopes surrounding areas and towns would follow their lead.
“Especially in lower-income towns, like Lowell especially,” she said.
The 3D-Printed Affordable Housing of the Future Will Be Recyclable
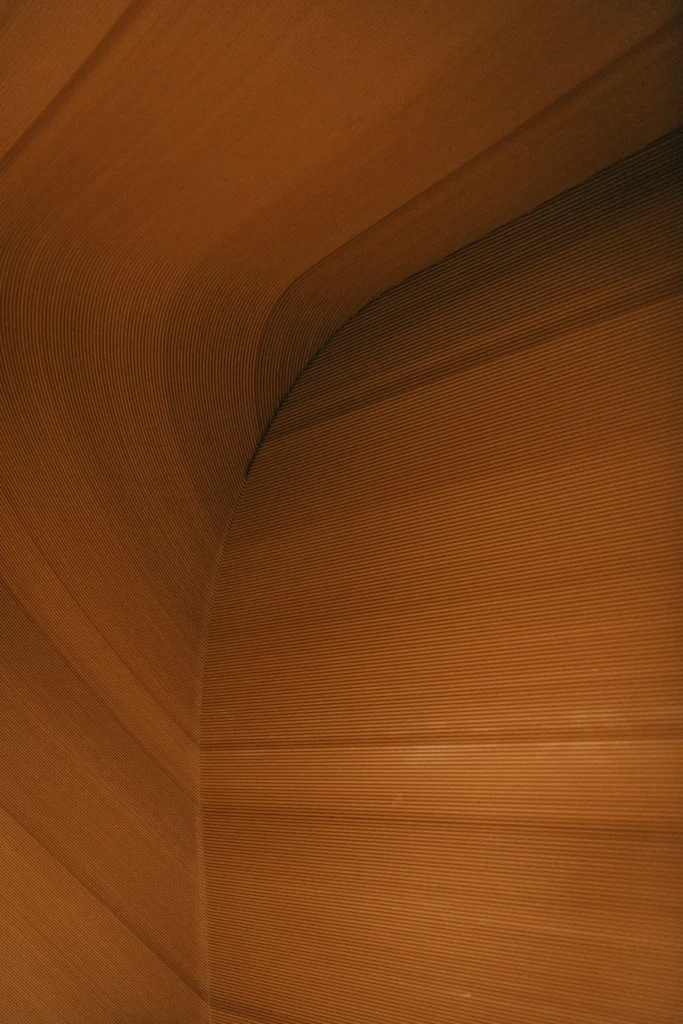
According to the University of Maine, the state’s sawmills produce nearly one million tons of wood residuals every year. Since each 600-square-foot unit requires approximately 10 tons of wood residuals, 100,000 housing units could theoretically be produced every year using just sawmill residuals.
Crushed by negative news?
Sign up for the Reasons to be Cheerful newsletter.
The University of Maine’s Advanced Structures and Composites Center received $3.3 million in funding for this project last year, and its collaboration with Penquis has set out to build a ready-to-live neighborhood with nine 3D-printed homes for people experiencing houselessness. As the team undergoes the final regulatory hurdles, Bird anticipates that houses could be ready to live in as early as this spring.
“The wood fiber material that’s used in the mix is essentially waste wood here in Maine,” says Jason Bird. Courtesy of the University of Maine ASCC
Once this pilot project is completed and the team at the University of Maine reaches full commercial capacity, Bird says the team will be able to print a home in as little as two days.
“That would include the shell of the house — the roof, walls, floors system,” Bird explains. “Long-term [infrastructure projects] could include cabinets, countertops, bath fixtures. And what gets me so excited about this project is that the technology isn’t just solving a local problem, it could be replicated around the world.”
Dr. Habib Dagher, executive director of the Advanced Structures and Composites Center, confirms that the technology is intended to be widely replicated.
“The goal of this research is to create a system for constructing homes that alleviates strains on the supply chain and addresses labor shortages, while providing economical and sustainable housing,” says Dr. Dagher. “This technology can be used anywhere in the world that has access to bio-based raw materials. We are focused on scaling up production technology to drive down costs and increase availability.”
And after enduring a year of extreme weather in Maine, with sensors reporting temperatures ranging from 1 degree to 105 degrees Fahrenheit, BioHome3D met all sustainability, strength, and durability requirements for US building codes, as well as the design requirements of the International Code Council code.
“Doing this project in a place like Maine, which has some of the most extreme temperatures in the continental US, is vital because it can prove that this material can endure huge temperature swings,” says Sarah Goehrke, founder of Additive Integrity, a consulting service that focuses on the examination and sustainable acceleration of industrial 3D printing. “The fact that BioHome3D survived for a year is very important proof going forward.”
Lafarge Canada supporting Canada’s largest 3D-printed housing project in Alberta
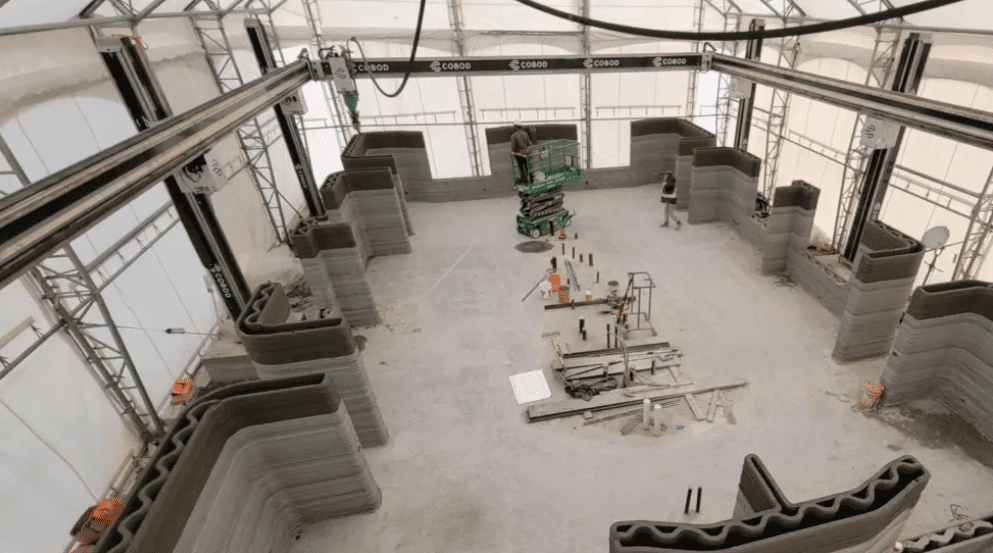
Ontario Construction News staff writer Lafarge Canada will supply its OneCem low-carbon cement and work with nidus3D to build Canada’s largest 3D-printed housing project, aimed at addressing an acute housing challenges faced by the SikSika Nation. While nidus3D has successfully completed 3D-printed housing projects in Ontario, this is the first project in Alberta. Construction is […]
3D-printed housing development planned for Rogers
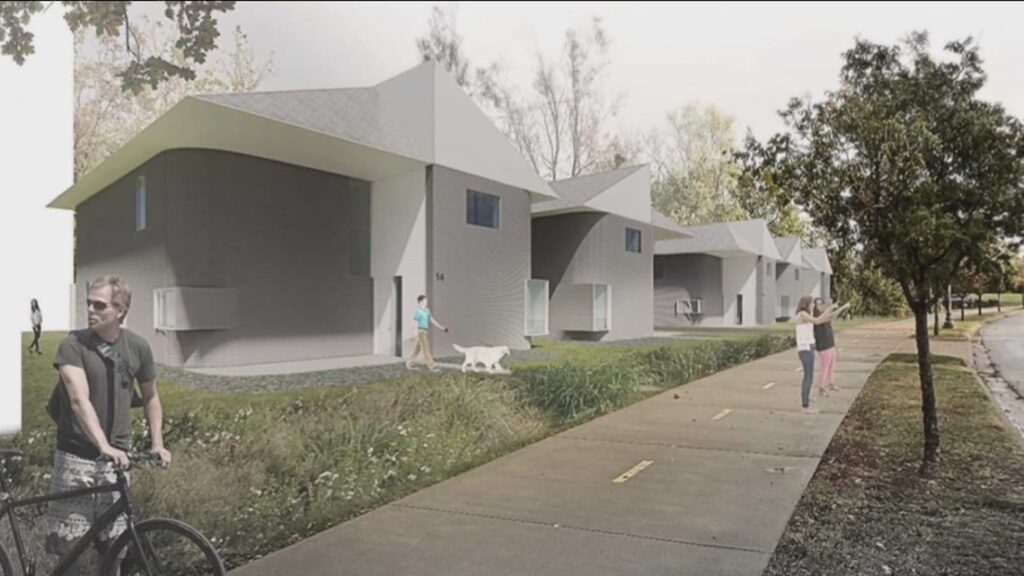
Rogers City Council sold $50,000 worth of land to the Northwest Arkansas Council to head this project.
ROGERS, Ark. — The Rogers City Council voted Tuesday night to sell a piece of land to the Northwest Arkansas Council subgroup “Groundwork” to build the first 3D-printed homes in the state.
The city voted to sell the land on South 1st St. for $50,000 on Jan. 23. These homes will be sold to buyers whose annual income does not exceed 80% of the area median income. Right now, the group plans for four to five duplexes on the site that are two stories.
“One of our goals is for this housing to provide some level of affordability with some proximity to one of our downtown’s. So, in theory, someone could potentially live there, work at a coffee shop, or work at one of the restaurants in Downtown Rogers and have a short walk or a short bike ride or short commute to and from work,” Duke McLarty, Executive Director for Groundwork, said.
McLarty said things like plumbing and electrical will be installed in these houses in a traditional manner, but the walls will be made out of concrete.
“Where the 3D printing part comes in is essentially the outside walls. A robot will show up on site, it has an arm, and concrete comes out of this arm in a way that almost looks like soft serve ice cream. It’s layered on top of each other to build those walls,” McLarty said.
One of the organization’s goals for this development is to show that housing can be affordably produced using these technologies and be a blueprint for similar projects in the area.
“Studies have shown that they’re 30% more energy efficient. It’s very resilient to extreme weather. It doesn’t rot. There’s no risk of termites there’s no risk of water damage,” McLarty said. “This is really going to be an educational journey that the City of Rogers is proving to be a great partner on. We’re going to bring building officials and fire officials from not just Arkansas, but throughout the heartland, to come here, see this and experience it at different stages.”
The first-of-its-kind project has officials for the city excited and hopeful, as they see the need.
“We’ve put a lot of work into making Rogers as developer friendly as we can be for affordable housing projects. And we’re talking about workforce housing projects that so many of our citizens need,” John McCurdy, Director of Community Development for the City of Rogers, said.
“The more that we can have people who live close to where they work, and where they spend their money, the fewer people on the streets, and I mean, it’s just it’s a win-win for everybody,” McCurdy said.
McLarty said they’re hoping to break ground on the development by late spring or early summer and hopefully have residents move in by the end of the year.
[embedded content]
Watch 5NEWS on YouTube.
Download the 5NEWS app on your smartphone:
Stream 5NEWS 24/7 on the 5+ app: How to watch the 5+ app on your streaming device
To report a typo or grammatical error, please email KFSMDigitalTeam@tegna.com and detail which story you’re referring to.
First 3D printed house in Portugal
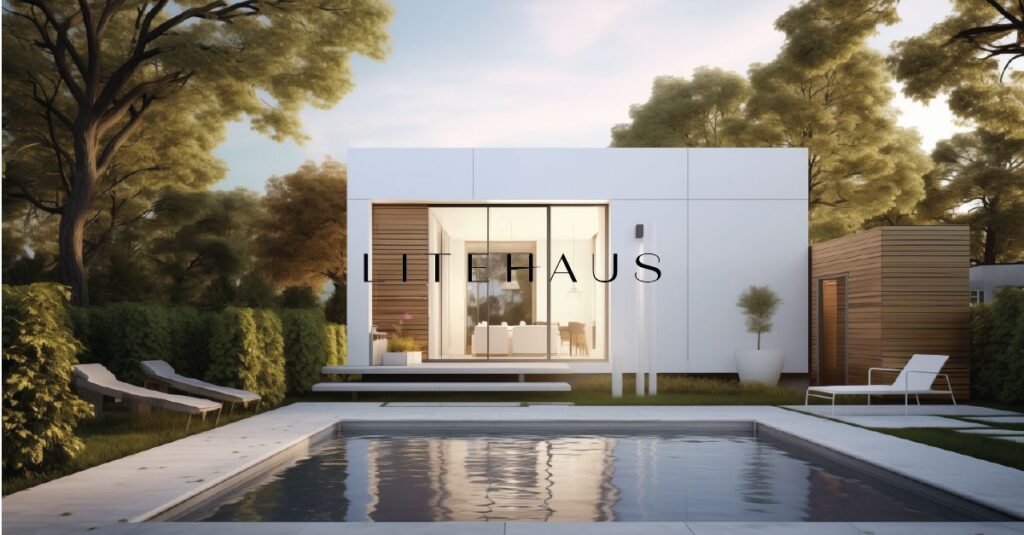
The property will be located in Portela da Villa, in Torres Vedras, 30 minutes from Lisbon.3D printing focuses mainly on walls. “This technology allows us to produce up to 45m2 of walls in just 20 hours”, says Simi Launay, chief creative officer at Litehaus, quoted in a statement to which Notícias ao Minuto had access.“The process of creating this housing unit is carried out using technologies such as Artificial Intelligence, during the initial creative and design phase, and 3D printing, during the construction phase,” according to the company.3D printing is focused primarily on walls. “We are here to take away the distrust of the sector. This technology allow us to produce as much as 45m2 of walls in only 20 hours,” says Simi Launay, Litehaus’ Chief Creative Officer.Litehaus aims to build 100 homes a year in Portugal: “Our goal is to build 70% faster and 20% cheaper, delivering residences that epitomize elegance and minimalism harmonized with Portugal’s natural beauty,” adds Simi Launay.
Couple living in 3D printed concrete home for $1,400 a month reveal what it’s like
With 3D printing becoming increasingly popular, it seems a logical step that people would try to 3D print a house.One project in the Netherlands has done just, building five houses using the process in 2021, and couple Elize Lutz and Harrie Dekkers receiving their ‘digital key’.The bungalow, owned by real-estate investment company Vesteda, was being leased on six-month contracts at about $1,400 a month, Business Insider reported in 2021.Loading…The homes are certainly a departure from a bricks and mortar house, with a summary of the project describing how it wants to explore the design possibilities from 3D printing.Now obviously this is a bit different from a 3D printer you would have at home. The crane-mounted printer lays several thin layers of concrete which are stacked on top of each other, starting from the ground up.There’s no steel frame or reinforced concrete, it’s just layer after layer of concrete mix, with the 3D printing also creating cavities to provide insulation and space for wiring and plumbing.They look a bit like the filling of an oreo or an ice cream sandwich.But what are they like to actually live in?Lutz said: “I saw the drawing of this house and it was exactly like a fairytale garden,” adding: “It is beautiful.”The end result of a 3D printed house. Credit: ROB ENGELAAR/ANP/AFP via Getty ImagesDekkers added: “It has the feel of a bunker – it feels safe.”It is hoped that the structure will help provide affordable housing that’s quick to construct.In a press release, housing and spatial development alderman at the municipality of Eindhoven, Yasin Torunoglu, said: “In addition to affordable homes, the market increasingly demands innovative housing concepts.”With the 3D-printed home, we’re now setting the tone for the future: the rapid realization of affordable homes with control over the shape of your own house.”At present, this process of building houses is still not more cost effective than older ways of doing so, despite reduced labour costs.However, this is something that they hope to change in the future.This is what the houses look like when they’re finished. Credit: OB ENGELAAR/ANP/AFP via Getty ImagesIt is also hoped in the construction industry that the use of 3D printed construction could reduce the environmental impact, and also cut costs.In the Netherlands it is also a way to keep up construction as the country faces a shortage of skilled bricklayers.Construction company executive Bas Huysmans said: “If you look at what time we actually needed to print this house it was only 120 hours.“So all the elements, if we would have printed them in one go, it would have taken us less than five days because the big benefit is that the printer does not need to eat, does not need to sleep, it doesn’t need to rest.”So if we would start tomorrow, and learned how to do it, we can print the next house five days from now.”
Why this 3D-printed house could be a gamechanger
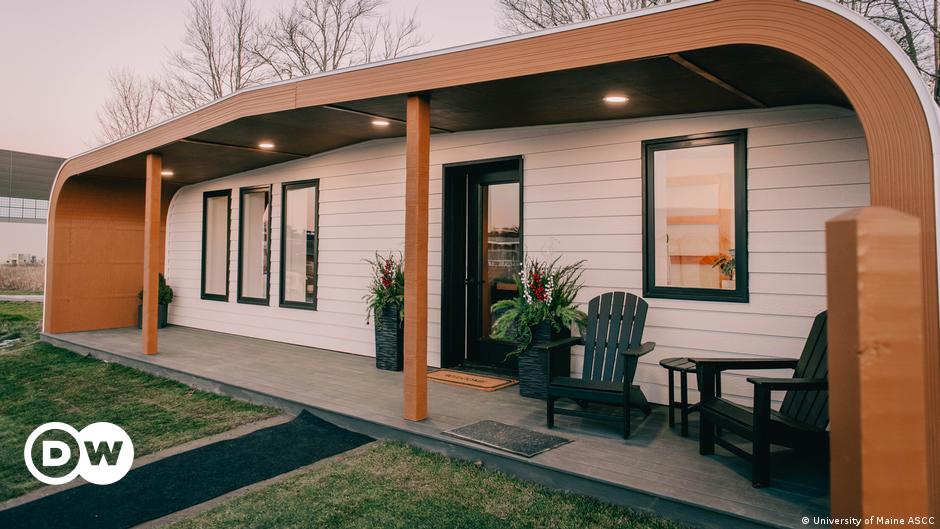
In this episode of Living Planet, we’re delving into a story about a remarkable 3D-printed house in the US state of Maine. It was made of 100% bio-based materials, which is good news for the construction sector, which accounted for nearly 40% of energy and cross-related CO2 emissions in 2021, according to the United Nation’s Environment Program.But this story is about much more than technology and innovation. Maine is one of the US states that has become a magnet for Americans searching for affordable houses in the wake of the pandemic. It’s also a state that’s seen its once booming paper industry dwindle to a handful of papermills, leaving a glut of sawdust from the timber industry with nowhere to go.
And as it turns out, a research team at the University of Maine was working on another project that turned out to be part of the solution to both of these problems.
In this episode, we speak with Mark Wiesendanger, director of development at MaineHousing; Habib Dagher, the executive director of the Advances Structures and Composites Center at the University of Maine; and Dr. Halil Tekinalp of the Department of Energy’s Oak Ridge National Laboratory.
You can read more about BioHome 3D here.
SikSika Nation to Receive 3D Printed Housing Community in Canada – 3DPrint.com | The Voice of 3D Printing / Additive Manufacturing
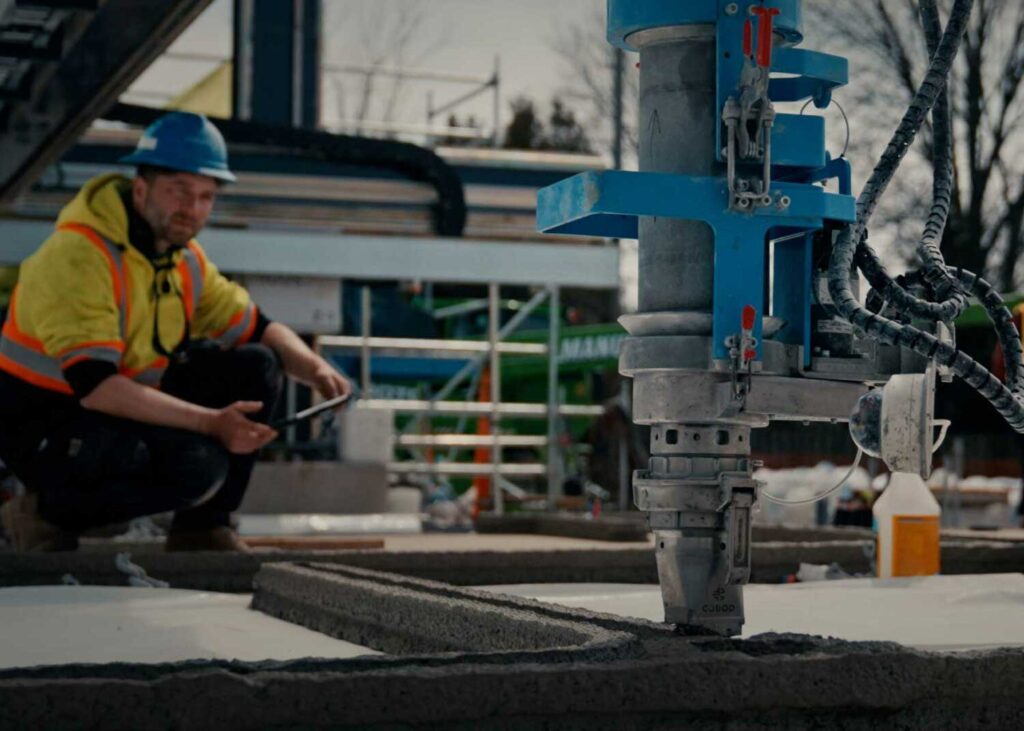
In Canada, the soaring prices of homes have become one of the if not the biggest political issue at the moment, sparking widespread interest in possible solutions like 3D printing homes. In this area, the Canadian subsidiary of French cement giant Lafarge, is collaborating with nidus3D, a on-site 3D construction service firm, to make homes in the country.
nidus3D utilizes COBOD 3D printers for its construction projects. The firm’s latest endeavor involves creating 16 housing units in the SikSika Nation, a First Nation community located in southern Alberta. This initiative is particularly noteworthy because it aims to provide shelter to individuals facing domestic violence and those at risk of homelessness.
“Our shared goal with nidus3D extends beyond mere innovation. This project is about helping address the critical housing needs of the nation and foster a resilient, inclusive future through sustainable construction practices. We were proud to contribute to this project,” stated Lafarge Canada (West) president and CEO Brad Kohl.
Lafarge plans to use its OneCem cement for the project, which is meant to be 10% less polluting in terms of emissions compared to traditional Portland cement.
“This multi-build development will not only provide much needed housing but show the immense potential of 3D construction printing to address Canada’s housing crisis. This project will demonstrate efficiencies and savings the technology can deliver through rapid, repeatable construction,” said nidus3D President Ian Arthur.
nidus has a track record of printing units for Habitat for Humanity and creating North America’s first two-story 3D printed building. This approach to construction might reduce costs for homebuilders due to its lower labor requirements. Simultaneously, it can minimize material use and significantly cut down on formwork, potentially lowering expenses and diminishing the environmental impact of home building. Nevertheless, as our Editor in Chief Michael Molitch-Hou previously pointed out, this technology is unlikely to completely solve the housing crisis.
In the past decade, house prices in Canada have more than doubled. For those fortunate enough to afford a house in a major city, mortgage payments can consume a staggering 59% of household income. In a market like Ontario, the average sold price of a home was $750,000 in December 2018, which has now escalated to over $1 million. Since 2000, house prices in the country have increased more than fourfold. While GDP per capita has doubled during this period, incomes and disposable income haven’t kept pace with the soaring house prices.
Although the entry of foreign buyers and new immigrants adds pressure to the market, the primary driver appears to be the perception of homes as a sound long-term investment. This belief, increasingly shared by individuals and firms, fuels the conviction that house prices will continue to rise. The result is a surge in investment activity, with investors buying properties and developers focusing on high-end properties. Consequently, the existing market, particularly more affordable segments, is not adequately addressed.
Currently, Canadian society lacks a mechanism to swiftly increase income or to collectively construct low-cost housing on a large scale. In contrast, post-World War II Europe saw governments actively stimulating mass house building to meet the demand. Additionally, many countries have established housing associations specifically to provide low-cost housing. It appears that Canada has yet to devise a comparable solution for its current situation. According to some estimates, the housing shortfall in Canada could exceed 3 million units by 2030.
Unfortunately, I share the skepticism that 3D printing alone can magically alleviate the housing crisis, especially considering the vast scale required for impact and the current state of the industry. Moreover, the central issue is the high cost of houses, making them unaffordable for many, yet essential for everyone. This paradox turns houses into attractive investment assets, further driving up prices. However, there’s hope that Canada and other nations will develop a comprehensive set of incentives and plans to address this challenge. Despite no wealthy country currently appearing to work on a holistic solution to what is a major concern for voters, the future housing market will likely include more mature 3D printing solutions in some capacity. While 3D printed construction may not be the silver bullet for the housing crisis, it certainly has the potential to play a role in any future solution.
Subscribe to Our Email Newsletter
Stay up-to-date on all the latest news from the 3D printing industry and receive information and offers from third party vendors.
Please enable JavaScript to view the comments powered by Disqus.
South Africa’s first 3D printed building
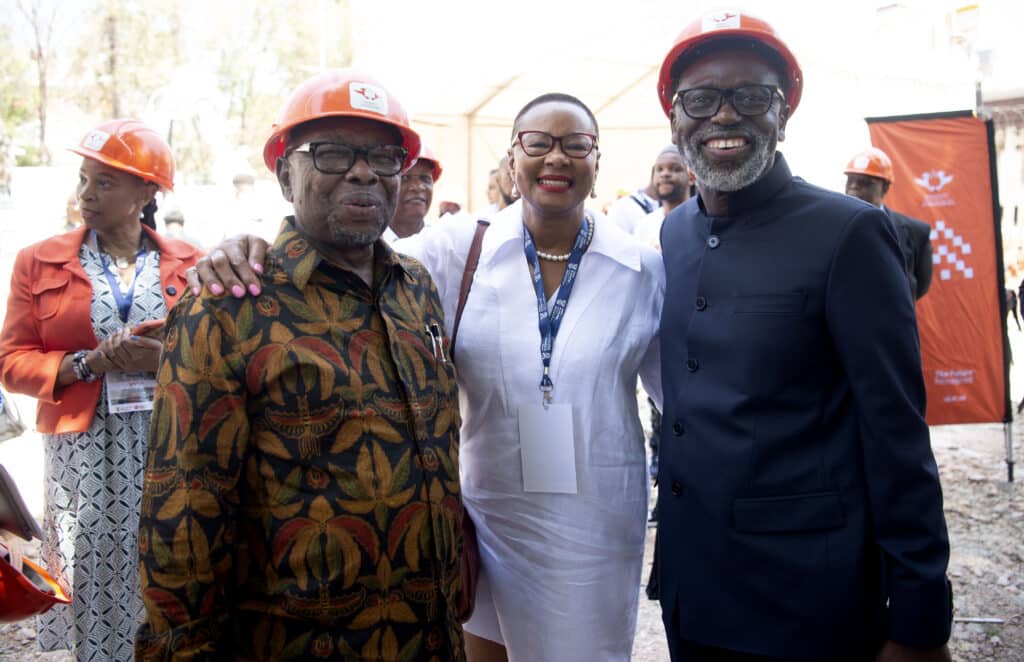
First South African printed buildingAt the start of this year, the University of Johannesburg (UJ) made history by finishing South Africa’s first-ever 3D printed building. The project was a collaboration between UJ’s Department of Architecture and Design, and the Department of Science and Innovation (DSI). The building, which is a one-room structure, was completed in under eight hours using 3D printing technology on UJ’s Doornfontein campus. The process employed a CyBe Robot Crawler, which used a cement-based material to create the walls of the building layer by layer. The printer was operated by a team of experts, including outgoing UJ Vice-Chancellor and Principal Professor Tshilidzi Marwala, who ensured that the printing process was smooth and accurate. The experts were really impressed with the printer’s construction time, as it can produce buildings much faster than traditional construction methods. “This is among the last projects that will be rolled out during my tenure as Vice-Chancellor of this University, and it is one I am particularly excited about!”, said Prof. Marwala at the launch event at UJ’s Doornfontein Campus.
Quick and cheap production
Apart from the production speed of 3D concrete printing, the relatively low costs of the technique also had an impact on the university’s staff. Professor Jeffrey Mahachi, head of the Civil Engineering & The Built Environment School at UJ, was dazzled by how cheap it was to print the project. “The interesting thing is you can print a house in 8 hours, the quality is excellent, and the product is cost-effective,” Mahachi noted about the structure. In that statement he was more than right, as the entire house was built within the span of a day, much faster than traditional construction. Furthermore, the production speed and costs could very well improve in the future. Dr. Khululekani Ntakana, lecturer at UJ, correctly mentioned that the technology is still in its infant stages, and that research is still being conducted every day. It is uncertain what the future holds for 3D concrete printing, but with UJ joining the worldwide research on the construction technique, the future sure looks promising!
An improvement to South African construction
The completion of the 3D printed building is a significant milestone for the South African construction industry. It demonstrates that 3D printing technology can be used to build structures quickly and efficiently. As this innovative technology is so efficient, the UJ project is expected to pave the way for future developments in the construction industry. The use of 3D printing technology in construction could lead to faster construction times, reduced costs, and improved quality. Due to all these advantages, the technology has the potential to address the housing shortage in South Africa by providing affordable and sustainable housing solutions. As Dr Blade Nzimande said, the country currently faces a shortage of over 2.3 million houses. The backlog of affordable housing has been going on for over two decades, and local experts on the subject are excited that 3D printing technology could offer a possible solution to this problem.
Worldwide experience
As CyBe Construction is getting ready for its 10 year anniversary, its track record of worldwide projects has grown to look very promising. Since being founded in the legacy of Hendriks Construction, a 100-year-old industry leader, CyBe has had partners all around the world. Time after time, the company has proven to be able to offer faster, cheaper, and more sustainable construction solutions. The company’s collaboration with Johannesburg, therefore, marks a significant milestone for South Africa’s construction industry. The completion of the country’s first 3D printed building demonstrates the potential of 3D printing technology in providing quick, efficient, cost-effective, and high-quality building solutions. The use of this technology could help address the critical issue of housing shortage in the country, providing affordable and sustainable housing solutions. As CyBe’s CEO and founder, Berry Hendriks, and the company share a vision for an improved society, the company is happy to be able to lend a hand in solving this crisis. With the completion of the first 3D printed building and the ongoing research in the field, the future looks promising for the construction industry in South Africa.
CyBe and SAHIF to tackle South African housing crisis
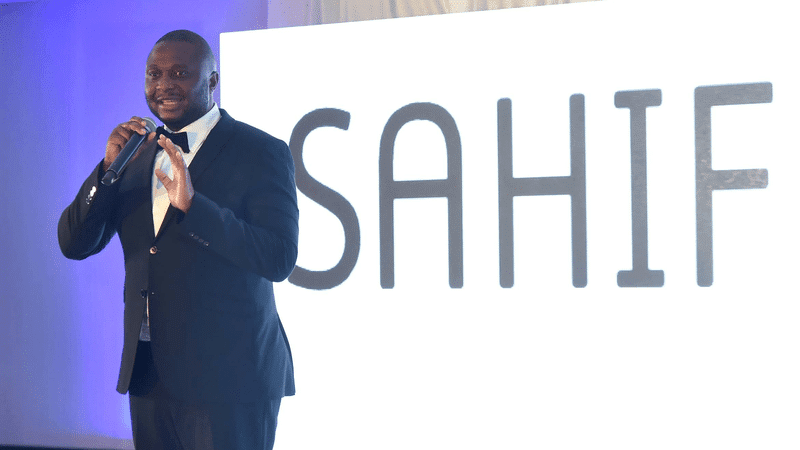
20/06/2023: CyBe Construction, a leading provider of 3D concrete printers, and the South African Housing & Infrastructure Fund (SAHIF) have joined forces in a groundbreaking collaboration aimed at tackling the pressing housing shortage in South Africa. The joint effort will leverage innovative 3D concrete printing technology to deliver faster, cheaper, and more sustainable homes. This strategic cooperation comes in response to the urgent need for affordable housing and represents a significant step toward achieving the United Nations’ goal of providing safe and accessible housing for all by 2030.
South Africa’s Critical Housing Crisis
South Africa is currently facing a severe housing crisis, with an ever-increasing backlog that has persisted for years. According to Dr. Blade Nzimande, Minister of Higher Education, Science and Technology, the country currently faces a shortage of over 2.3 million houses. This backlog of affordable housing has now reached the dark milestone of persisting for over two decades, highlighting the urgent need for affordable housing solutions. Though the government is making significant progress in the provision of homes in the country, the demand for housing keeps rising every day. Unfortunately, the country’s housing crisis isn’t unique. Indonesia, for example, currently faces a shortage of over 10 million homes. Mexico needs to scale up its housing construction to 800,000 units a year to keep up with demand. India is estimated to have a housing shortage of over 38 million by 2030. It is evident that something needs to be done.
Building the Future Together
To address this critical issue, CyBe Construction (CyBe.eu) and SAHIF (sahiffund.co.za) have signed a Memorandum of Understanding (MoU), combining their expertise and resources to come to a solution. This solution can be accredited to an alternative building method to substitute conventional construction: 3D concrete printing (3DCP). 3DCP has the ability to deliver homes quicker, cheaper, and more sustainable. “We believe that construction 3D printing will significantly alter and positively disrupt how human settlements will be delivered in South Africa,” said Minister Nzimande during a demonstration of the technology by the University of Johannesburg (UJ). The university’s demonstration showcased the capabilities of the CyBe Robot Crawler: a mobile 3D printer capable of efficiently constructing homes within hours. This printer is a product of CyBe Construction, the provider of 3D printing software and hardware in the MoU issued to solve the South-African housing crisis. As a market-leading 3D concrete printer company with a decade of experience, the company has demonstrated time after time being able to offer faster, cheaper, and more sustainable construction solutions. Their demonstration at UJ reaffirmed their expertise once again, making them the ideal candidate for the cooperation with SAHIF. The South African Housing and Infrastructure Fund (SAHIF) specializes in the development and application of sustainable materials and innovative technologies in the construction sector. SAHIF is the first fund in South Africa to embrace 3DCP in their approach. The collaboration between the two sustainable innovators, planning on rolling out large-scale development projects around the country, is poised to transform South Africa’s construction industry.
Turning Adversity into Progress
Though the collaboration between Cybe and SAHIF was being planned and prepared for some time now, the inauguration of the MoU still had a rather coercive trigger. The occurrence that lifted the agreement of the ground was a recent earthquake in South Africa. The seismic event, of which the epicenter is believed to be in Johannesburg’s neighboring city Boksburg, caused extensive damage to buildings in a large scale around the city. The earthquake served as the final push for the initiation of the MoU. SAHIF’s CEO, Rali Mampeule, emphasized the pressing need for affordable but resilient housing by stressing that “not only are 3D printed houses more affordable and quicker to build, but we also know they are sturdy enough to withstand seismic forces that took us by surprise this week.”
Earthquake-Proof Structures with 3D Printing
The adoption of 3D concrete printing technology provides a groundbreaking solution for constructing earthquake-resistant houses in South Africa. The inherent flexibility of 3DCP allows for the customization of structures, specifically tailored to withstand seismic activity. The technique also allows for the creation of intricate shapes that are reinforced with earthquake-resistant materials such as steel or polymer. The key factor in the method’s ability to absorb the seismic energy of an earthquake, however, can be attributed to CyBe Construction’s building material. The company has developed its own CyBe Mortar, an earthquake-proof mortar specifically formulated for 3D printing. This material combines high-strength aggregates and fibers, significantly bolstering its resistance to seismic forces. With superior durability and flexibility, this material stands out as an ideal option for constructing earthquake-proof houses. Additionally, its reduction of CO2 emissions by 32% as compared to traditional cement-based mortars promotes sustainability in the construction industry. This earthquake-resistant material, when combined with the precision, efficiency, and flexibility of 3D concrete printing, creates homes that not only prioritize safety but also showcase sustainability and style.
Fast, Affordable, and Sustainable Construction
The benefits of 3D concrete printing extend far beyond earthquake-proofing. The technique enables faster, cheaper, and more sustainable construction, making it an ideal solution for addressing the housing shortage in South Africa. The method almost entirely automates construction, resulting in significant time and labor hour savings. It also ensures optimal material usage, meaning less waste and lower material costs. This lower waste, along with the use of eco-friendly materials, contributes to more sustainable construction practices. CyBe Construction brings over ten years of experience in 3D concrete printing, offering a wealth of expertise and know-how in this cost-effective, efficient, and sustainable construction method. This makes them the perfect entity to work together with SAHIF. Combining SAHIF’s proficiency in South African construction and CyBe Construction’s competence in 3D concrete printing, the parties are well-equipped to address the pressing housing crisis in the country.
A Blueprint for Housing Success
The collaboration between CyBe Construction and SAHIF represents a significant milestone in addressing South Africa’s housing shortage. The transformative power of 3D concrete printing technology, with its ability to deliver faster, cheaper, and more sustainable homes, holds immense promise for the construction industry. As the urgent need for affordable housing is not bound to South Africa, as demonstrated by the housing backlogs in countries like Indonesia, Mexico, and India, the cooperation is poised to revolutionize the way homes are built not only in South Africa but also worldwide. With its proven effectiveness, 3D concrete printing can offer a scalable and efficient solution to this pressing global challenge, and the collaboration between CyBe and SAHIF can be seen as a precedent for solving the global housing crisis. By combining innovation, expertise, and a shared vision, CyBe Construction and the South African Housing and Infrastructure Fund are leading the way towards a future where safe, accessible, and sustainable housing is within reach for all.
Press Release – Game-Changer in Additive Manufacturing: Mixed on Site Carbon Neutral Alternative to Cement Unveiled
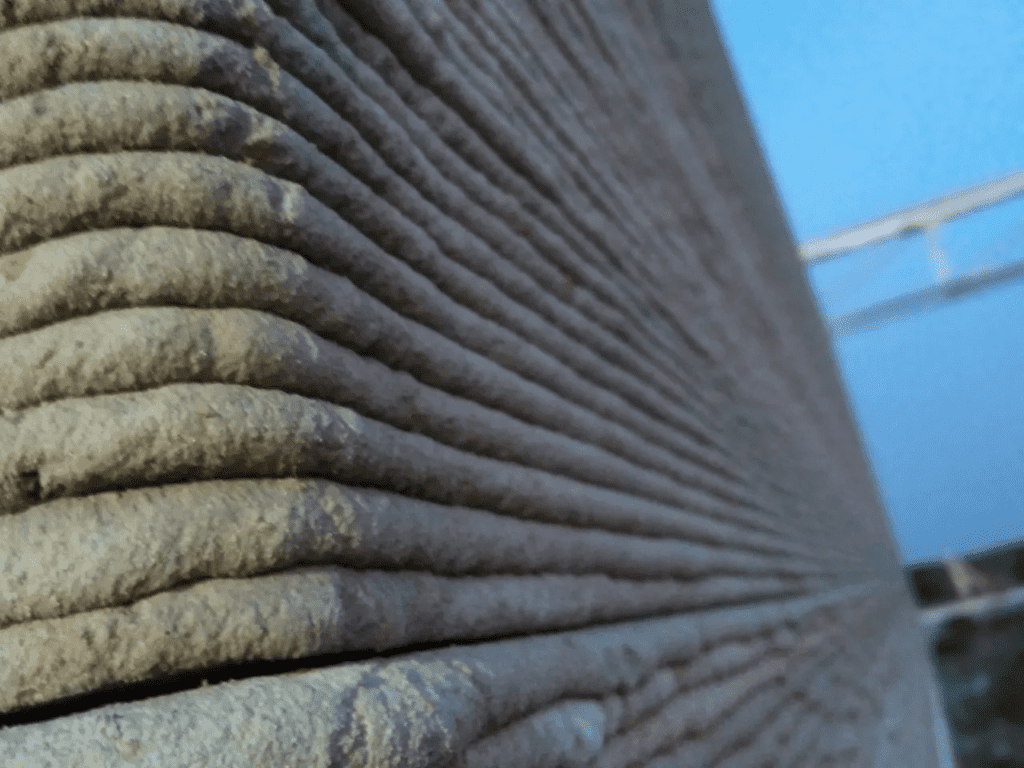
10/07/2023: Additive manufacturing company, Hive3D Builders, has developed a remarkable mixed on site carbon-neutral and stronger alternative to traditional cement. The printing material, which substitutes the mortar normally used in 3D concrete printing, is able to reduce construction’s CO2 emissions by 93%. Hive3D Builders is currently using this sustainable material to produce over 200 near-net-zero homes. This substance makes the already eco-friendly practice of additive manufacturing even more sustainable and is poised to revolutionize global construction.
Polluting Construction
The construction industry has long grappled with environmental challenges. Traditional concrete production contributes to 8% of global greenhouse gas emissions. 3D concrete printing technology generally has a lower carbon footprint than conventional building methods, mainly due to lower material usage, as well as a lower waste production rate. Along with the eco-friendly technology, additive manufacturing companies often strive to innovatively find sustainable solutions. An example of this is the manufacturer of Hive3D Builders’ printers, CyBe Construction. In the early days of 3D concrete printing, CyBe developed its own eco-friendly building material by using material that has up to 32% less CO2 emissions. Additionally, the material has the possibility to be produced locally.
Carbon-Neutral Material
Hive3D Builders (www.hive3dbuilders.com) take the production of eco-friendly building material one step further. By working with Eco Materials and Green Cement, they managed to develop a low-cost geopolymer cement replacement that has up to 93% less CO2 emissions. Due to geopolymer’s environmentally friendly properties, the substitute for the mortar that 3D concrete printing traditionally uses is almost completely carbon-neutral. Geopolymers have gained attention as a sustainable building material because they require less energy and produce fewer carbon dioxide emissions compared to traditional cement production. They can also utilize industrial waste materials such as fly ash, slag, and mining tailings, reducing the demand for natural resources and providing a solution for waste disposal. By combining this newfound material with the already eco-friendly properties of 3DCP, Hive3D Builders has unlocked tremendous potential for reducing carbon emissions in the building process. The current estimate is a reduction of 93% of the construction’s CO2 emissions. With this tremendous cut in greenhouse emissions, Hive3D Builders is at the forefront of sustainable construction technology.
Superior Strength
The implications of this innovation extend beyond its environmental benefits. Along with its reduction in CO2 emissions, the carbon-neutral material also offers superior strength and durability. This increased adhesion makes it an attractive alternative to traditional cement, offering immense potential for building more resilient structures. The strength of the material can be accredited to the geopolymer’s desirable properties. It is no wonder that geopolymers, oftentimes used as construction materials, were a key component in Hive3D Builders’ material. They exhibit advantages like excellent strength, high durability, and outstanding fire resistance.
Material Costs
3D concrete printing material generally has a significantly higher cost than regular concrete. This is because 3DCP does not use regular cement, but a mortar that dries notably quicker than regular concrete does. CyBe Mortar, for example, sets in three minutes and achieves structural strength in only one hour. This fast drying speed is needed because the bottom layers need to be strong enough to print the rest of the structure on. This special, fast-drying mortar, however, often comes at a higher cost than regular concrete does. Still, 3DCP is generally cheaper than regular construction. The technique has unique cost-saving properties due to a lower material need, as well as less necessary construction workers.
Hive3D Builders’ newly developed material, however, enjoys yet another advantage in this regard. Hive3D developed a unique system to automatically mix the cement replacement onsite with hyper-locally sourced aggregates to lower their material costs exponentially. By creating this system to automatically mix the cement replacement product onsite with locally sourced aggregates, the company is able to lower the cost of its printing mortar to a third of the price of other commercially available printing mortars. This low cost might pave the way for many hesitant construction companies to finally make the switch to 3DCP. The development of this new low-cost, carbon-neutral material is poised to shape the additive manufacturing industry.
Revolutionizing the Construction Industry
One of the main reasons that 3D concrete printing is not as common as you would expect it to be after hearing the advantages, is the fact that construction companies are often hesitant to change their way of working. The construction industry is booming, so big companies in the industry often don’t have the time or need to properly consider new building technologies like 3DCP. When they hear about the technique’s higher material price, they often lose interest, without taking into account the cost savings on other aspects. With Hive3D Builders adding a low material price to the material’s already impressive list of better sustainability and superior strength, the sustainable innovators might be able to convince headstrong construction giants to consider additive manufacturing as a cheaper, faster, and more sustainable alternative to their current construction methods. Using their partner CyBe Construction’s printer and Hive3D Builders’ carbon-neutral material, the company is set out to revolutionize the construction industry on a global scale.
Press Release – Miami Startup, Kind Designs, Leverages 3D Concrete Printing to Rescue our Oceans
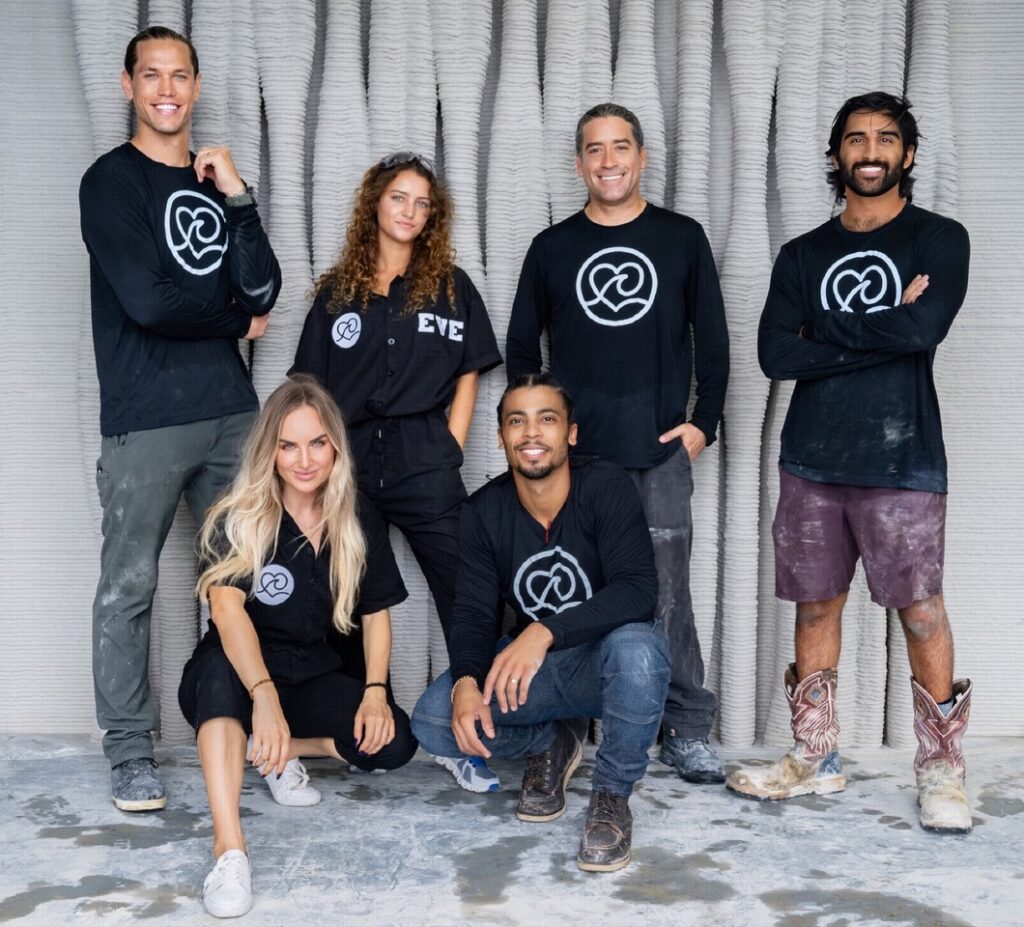
04/10/2023: Miami-based climate-tech startup Kind Designs has the solution for our rising sea levels. Leveraging 3D concrete printing technology as a faster, cheaper, and more sustainable construction method, they will produce Livings Seawalls. These underwater structures protect our shores, improve the ocean’s biodiversity, and monitor water quality.
Miami Startup Sets Out to Rescue our Oceans
The sea levels are rising. The ocean’s water quality is getting worse. Marine biodiversity is decreasing. Coral reefs are facing extinction. All these environmental challenges are threatening our oceans’ wellbeing. One Florida-based climate-tech startup is taking the problem head-on: Kind Designs. Operating from Miami, a city experiencing this issue firsthand, Kind Designs was established to address the challenges posed by the deteriorating state of our oceans. For CEO and founder Anya Freeman, issues related to sea-level rise in Miami became a part of her everyday life. Instead of dwelling on the problem, she decided to seek a remedy. Therefore, Kind Designs was instituted with just that goal: finding a solution to address the challenges faced by our oceans. Their solution? Living Seawalls.
Living Seawalls: Technology Hand in Hand with Nature
Just like ordinary seawalls, Kind Designs’ structures are made to be placed underwater in order to improve the local marine environment. They protect the land from erosion, flooding, and storm surges, and help counteract sea-level rise. However, Kind Designs elevated the concept of seawalls by designing them to include distinctive, nature-like shapes. These Living Seawalls offer support to local marine life, enhancing the ocean’s biodiversity. Their rough texture and curvy design offer shelter for marine life like fish and crustaceans while providing a stable foundation for marine plants to grow on. Additionally, Living Seawalls are embedded with sensors that measure water quality using 15 different parameters, such as pH levels and salinity. Currently, this data needs to be collected manually by Florida counties. However, once these sensors are deployed, they will provide readily available data, saving the state many hours of manual labor.
Affordable, Fast, and Sustainable Production
One of the reasons seawalls aren’t more common is their price tag. These underwater structures are generally quite expensive to produce, so Kind Designs had to find an affordable way to construct them. Having conducted research on cost-efficient construction methods, they opted for 3D concrete printing to create their Living Seawalls. 3D concrete printing is generally seen as a cheaper, faster, and more sustainable alternative to conventional construction. Kind Designs has already proven the fact that it is much faster: using a 3D concrete printer, they manufacture a Living Seawall in under two hours. The hardware, software, and material for 3D printing were provided by CyBe Construction, a Dutch construction company. CyBe, founded in the legacy of a 100-year-old giant in the construction industry, has a decade of experience in 3D concrete printing. They develop their proprietary hardware, software, and material tailored for additive manufacturing. The company was founded with a vision for an improved and more sustainable society, aligning perfectly with Kind Designs’ goal for a better world.
Image: Kind Designs and CyBe Construction team members next to a Living Seawall and a CyBe Robot Crawler
Funding Kind Design’s Journey to Save the Ocean
After their printer was delivered, Kind Designs also received a three-week training from CyBe. With this experience in hand, they could start printing their Living Seawalls. Their production process was kickstarted by a seed funding round, co-led by GOVO Venture Partners, M4 Investing, and the Florida Opportunity Fund. During this funding round, Kind Designs raised a total of $5 million. With these funds, Kind Designs will be able to “protect all coastal cities with Kind’s Living Seawalls and grow far beyond our home state of Florida,” as Anya commented. Specifically, these funds will be applied to speed up their production. Kind Designs had received letters of intent for purchases totaling $4 million; hence, this additional capital to enable faster production was more than welcome. Now that Kind Designs has the proper equipment to make their Living Seawalls and the proper funding to do so efficiently, they are ready to protect America’s coastlines for the better and improve its oceans.
Watch ICON Co-founder and CEO’s Featured Talk at SXSW 2022
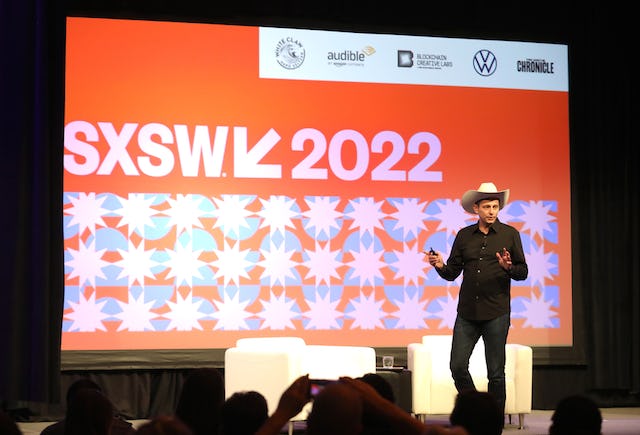
“It’s Time to Build” on ICON’s YouTube channel
We are excited to announce that the SXSW 2022 Featured Talk, “It’s Time To Build” by Jason Ballard, co-founder and CEO of ICON, as well as the subsequent moderated discussion with PBSNewsHour anchor Stephanie Sy is available on ICON’s YouTube channel.
In this inspirational talk, Ballard discusses what ICON is currently doing on Earth, the goal of building one billion homes in our lifetime to end the global housing crisis, and how the answers to problems we face may be found in the work ICON is planning for off-world construction.
[embedded content]
It’s Time to Build
One billion homes. To put a dent in the global housing crisis, we need to build one billion homes in a lifetime and today we simply aren’t solving the problem fast enough. To build the future, we must change the way we design and build for a world that will enhance human happiness and flourishing. The future starts with 3D printing. The technology that can create a more sustainable and beautiful world will be the same technology that helps us become a spacefaring civilization.
Will cities of the future be built by robots and drones? Will humans colonize the Moon and Mars? Ballard’s featured talk “It’s Time to Build” discusses humanity’s future and how architecture, design, robotics and sustainability can be in service to humanity and help us reimagine worlds.
Diego Donamaria/Getty Images for SXSW
PBS NewsHour anchor Stephanie Sy joined Ballard on stage to discuss the future of home construction and dig in deeper on ICON’s past, present and future.
Diego Donamaria/Getty Images for SXSW
Southern Hemisphere’s Largest Fully 3D Printed Building Completed
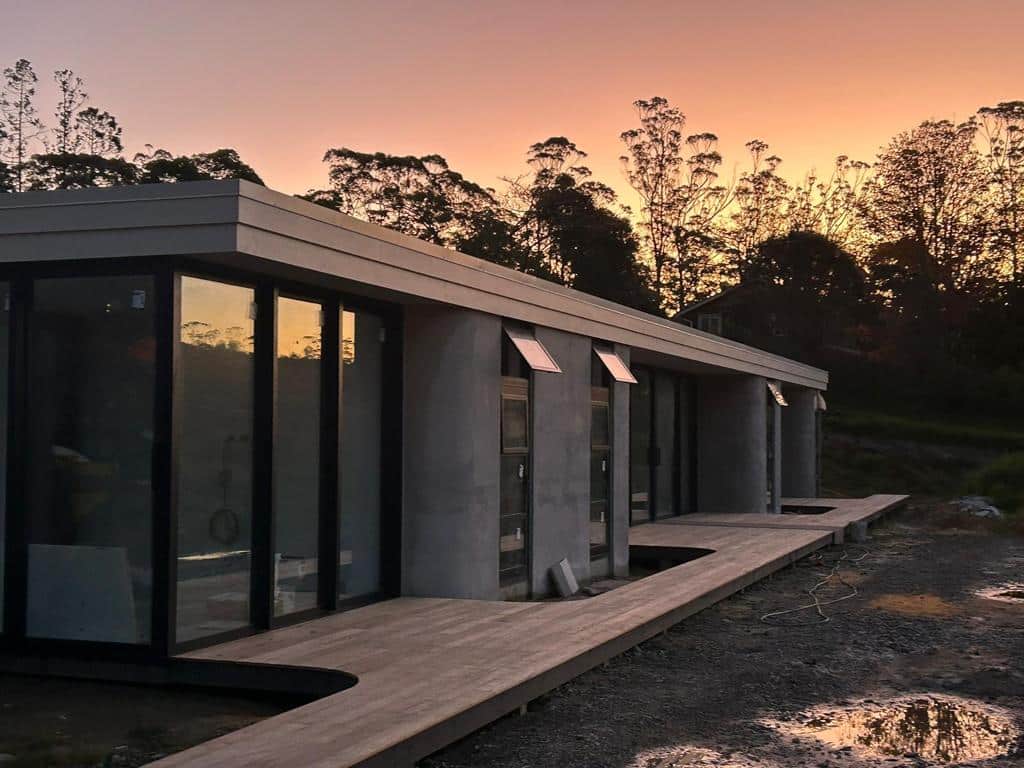
10/11/2023: New Zealand’s leading 3D concrete printing company, QOROX, has successfully completed the Southern Hemisphere’s largest 3D printed building. Their advanced 3D concrete printing technology enabled them to complete the project more cost-effectively and sustainably. The CEO of QOROX sees 3D concrete printing as the next evolutionary step in the construction industry and intends to further advance this technology by entering the business of selling 3D concrete printers.
Southern Hemisphere’s Largest 3D Printed Building
New Zealand just got a new milestone: the largest 3D concrete printing building in the Southern Hemisphere. The print was carried out by QOROX, a Waikato-based 3D printing company that has been revolutionizing the Kiwi construction industry since 2018. The recently completed ‘Paremoremo House’ is also the first fully 3D-printed residential home in the Auckland suburb it was named after. The home was constructed using 3D printed concrete panels and, with a total area of 252m², will accommodate a family of four. By harnessing the design capabilities of 3D concrete printing, QOROX was able to bring to life a unique design that complements the site’s natural contours and serene setting. This distinctive design was crafted by the multi-award-winning Dorrington Atcheson Architects (DAA). QOROX’s CEO, Wafaey Swelim: “DAA provided an amazing design which enabled us to fully utilize the design capabilities of our 3D concrete printer and produce a strong, secure and warm home for the owners to enjoy for many generations to come. People who visit the home are so impressed by its calmness and warmth.”
Cheaper, More Sustainable, and Disaster-Proof
Besides its flexibility in design, QOROX’s 3D printing technology provided several other advantages for the construction of the Paremoremo House. Firstly, QOROX’s 3D printing technology enabled the construction to be carried out in a more sustainable manner. The home’s 63 panels, totaling an area of 360m², were printed using its own material that is 80% locally sourced. Before being installed on-site by QOROX and Senior Construction, the walls were printed in the prefabrication facility in Hamilton, ensuring optimal print conditions. Combining this with 3D concrete printing’s general environmental advantages, QOROX was able to achieve construction with 30% fewer emissions than traditional concrete builds.
Swelim added that the technology also enabled “the formation of wall cavities for insulation, plumbing and electrical wiring.” By incorporating these typically essential production processes, QOROX was able to save money on these additional production steps. The flexibility of 3D concrete printing also allowed the future owners of the Paremoremo House to add their personal touches without incurring additional costs. “It’s pretty cost effective, and you can get the geometric proportions and shapes that you would have to spend a lot of money to get if you did it in traditional concrete construction,” noted DAA director Tim Dorrington about the technique.
Lastly, the house is equipped perfectly to withstand New Zealand’s natural environment. The 3D printed walls provide excellent thermal mass quality, making it an exceptionally climate-resilient home. This quality allows the Paremoremo home to stay warm during the cold winter months. The house in Auckland was also built in a region prone to both flooding and earthquakes. By ingeniously applying 3D concrete printing, QOROX was able to build the home completely flood-proof, while also meeting the world’s highest standards of earthquake-proofing.
Driving the Next Evolution in Building
Wafaey Swelim believes that 3D printing is the next essential step for the construction industry to evolve. “3D printed concrete is the next evolution in building, and it’s happening right now, right here in New Zealand.” Besides carrying out 3D prints like clockwork, QOROX has recently started advancing the technology even further in New Zealand by entering the business of selling printers. The 3D construction company sources their hardware and software from the Dutch 3D-tech company CyBe Construction. By entering into a reseller agreement earlier this year, QOROX has officially become an authorized reseller of CyBe printers. This way, they can expand the evolution of 3D concrete printing in New Zealand even more effectively. With their recent achievement of the Southern Hemisphere’s largest 3D printed building and their efforts to advance 3DCP by utilizing and selling more CyBe printers, QOROX is ready to drive the next evolution in the New Zealand construction industry.
The world’s tallest 3D printed building
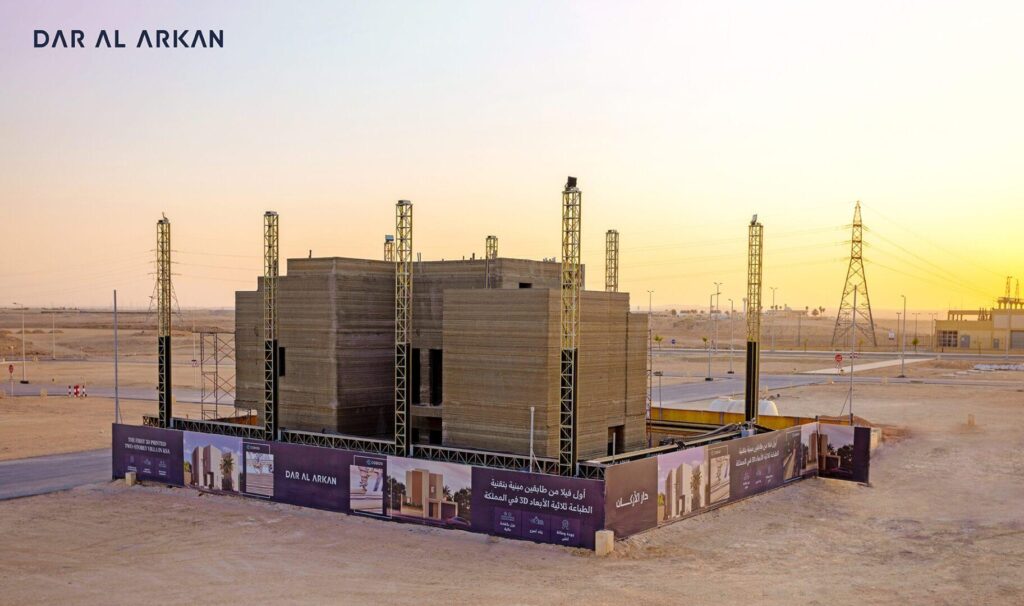
The 345 m2 building was 3D printed by the leading Saudi Arabian real estate developer, Dar Al Arkan, using a COBOD 3D construction printer The building has a total height of 9.9m and is therefore also the tallest on-site 3D printed building in the world Low cost local materials were used at a cost of […]
Watch Melodie Yashar’s TED Talk: How to Build for Human Life on Mars
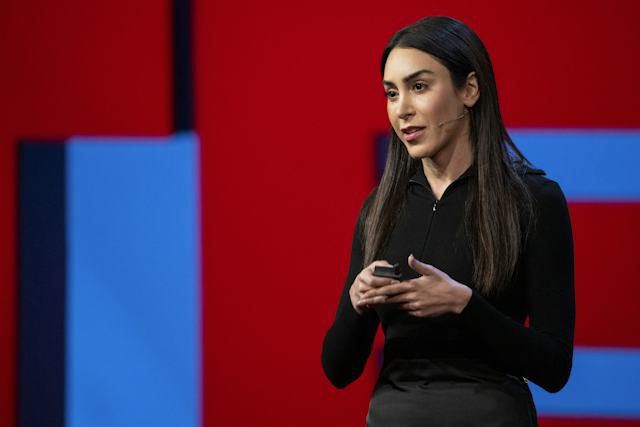
“How to build for human life on Mars”
We are delighted to announce that the TED Talk “How to build for human life on Mars” by Melodie Yashar, Vice President of Building Performance & Design at ICON, is now available for viewing at TED or in the embedded video below.
TED is a global phenomenon that has captivated the hearts and minds of its audience for nearly 40 years by offering unique perspectives on topics that people may or not be familiar with. Since its founding, TED has rapidly increased its global presence by inviting people from different backgrounds to share their interests and expertise with the world. Similar to those who came before her, Melodie was invited to share her passion for space exploration and architecture – with the TED community.
Melodie Yashar, ICON’s Director of Building Design & Performance, delivers her TED Talk. Photo credit: TED / Ryan Lash
Learning to live and work on Mars will be no small feat. During her visionary TED talk, Melodie introduces work to design off-world shelters with autonomous robots and 3D printers and explores how it might help uncover radical solutions to some of the problems troubling humans on Earth today. Melodie underscores the importance of creating an architecture that evolves with the needs of humanity, especially in the midst of climate change and the urban housing shortage.
Melodie Yashar, ICON’s Director of Building Design & Performance, delivers her TED Talk. Photo credit: TED / Ryan Lash
For more video of ICON’s off-world construction work, visit ‘ICON 3D Prints Simulated Mars Surface Habitat at NASA’s Johnson Space Center’
ICON’s House Zero Receives Top Honors in Architizer’s Annual A+ Awards
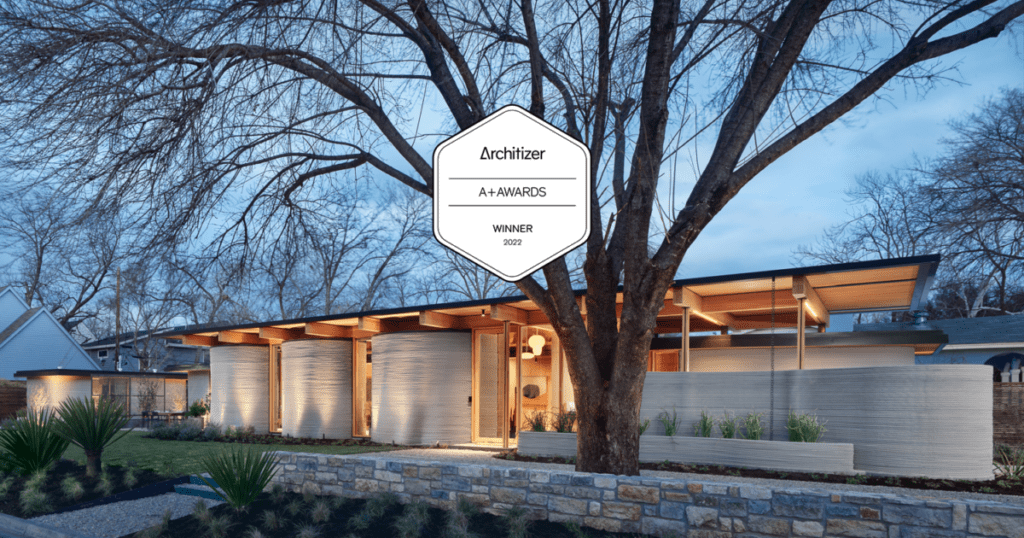
3D-printed home in Austin recognized as one of the world’s best buildings and spaces.
We are ecstatic to share that ICON’s House Zero was selected as the winner of the Architecture +Experimental Design and +New Technology award categories in Architizer’s esteemed A+Awards for 2022. This list bestows honor on firms and companies that have sought to cultivate and advance society’s appreciation of meaningful architecture and design while simultaneously shining a light on the individuals behind these innovative ideas.
Our inclusion in these categories was based on a review by a 250+ member jury along with a round of voting that was open to the public. ICON’s goal of incorporating its noteworthy 3D printing technology and software into the homebuilding process gave them the opportunity to cut back on the time, materials, and costs that are needed to build a traditional home.
House Zero, 3D printed by ICON and designed by Lake|Flato Architects, is ICON’s most innovative home yet, pushing the boundaries of what’s possible with architecture through automated construction only achievable through 3D printing. The 2,000+ sq ft home is the first project in ICON’s Exploration Series and illustrates the development of new design languages and architectural vernaculars created by construction scale 3D printing. By introducing biophilic principles into the design process and taking them to heights that we have never seen before, House Zero was able to revamp modern architecture by breathing new life into the movement and changing the face of the housing landscape as we know it.
Read More at https://architizer.com/projects/house-zero/
Construction and Technology: ICONArchitecture: Lake|Flato ArchitectsStructural Engineer: GNAStructural Engineer: WJEMEP Engineer: Integral GroupLandscape Architect: Word + CarrInterior Design: Lake|Flato Architects + ICONLighting Design Consultant: Studio Lumina
ICON’s House Zero Named to TIME’s List of the Best Inventions of 2022
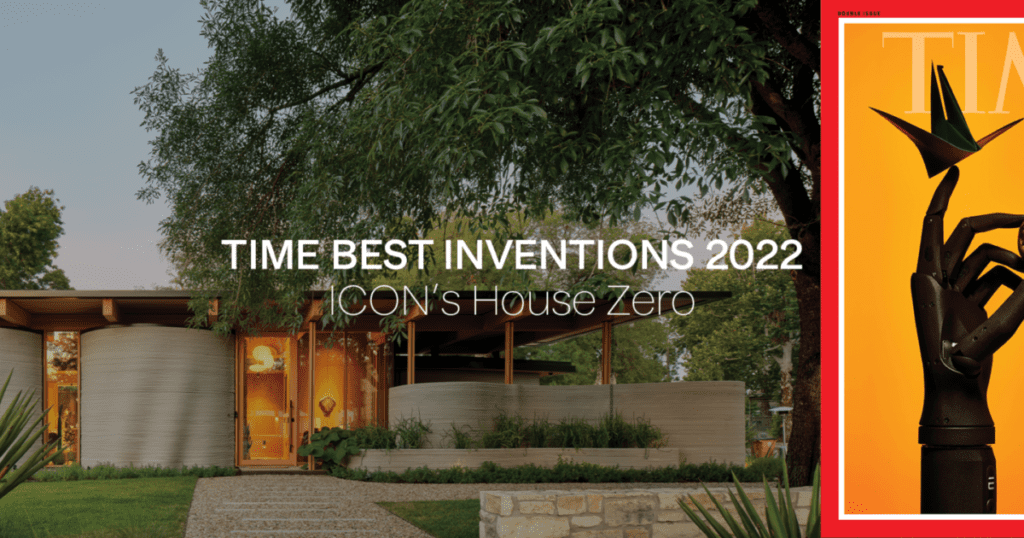
3D-printed Home Designed by Lake|Flato Architects joins ranks of TIME’s Best Inventions featuring extraordinary innovations changing lives
We are honored to share that ICON’s House Zero, designed by Lake|Flato Architects, has been selected as a recipient of TIME’s Best Inventions 2022 in the Design category!
TIME Best Inventions was founded in an effort to bring awareness to the products, software, and services that are solving complex problems in compelling and innovative ways. Each year, thousands of individuals and companies submit their products and services for review across 33 categories ranging from accessibility, connectivity, and apps & software to wellness, beauty, and social good. Once submitted, each of these inventions is reviewed extensively by a panel of judges to determine a product’s impact, not only as it relates to the now, but also in regards to how it will hold up in the future. House Zero is one of the only residential home projects to ever receive this prestigious award.
House Zero’s inclusion on this esteemed list is a cherished stepping stone for ICON as it underscores ICON’s mission of putting robotics, software and advanced materials in service to humanity. Using innovative technologies in the form of the next-generation Vulcan construction system enabled ICON to build a home that was optimized specifically for 3D printing. The future of homebuilding is here.
To view ICON’s profile, visit TIME.
PERI live 3D printing with COBOD printer was the highlight at bauma
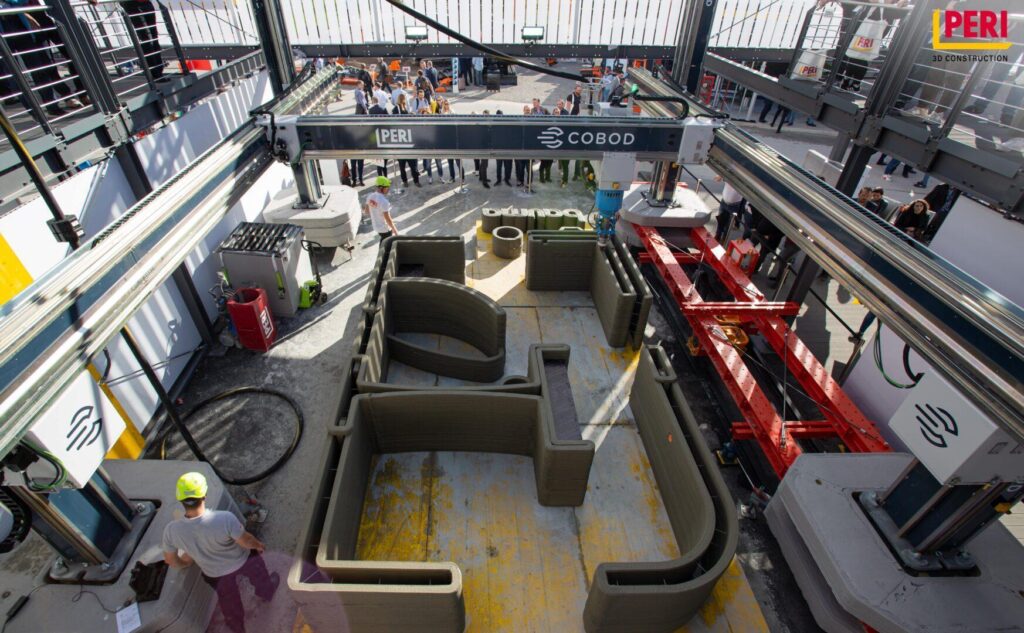
In an unprecedented showcase PERI took it upon themselves to live 3D print the walls of a small house each day for 7 days at the Bauma exhibition last week in Munich, Germany the largest construction exhibition in the world More than 600,000 visitors from 200 countries attended the exhibition, with over 300,000 coming to […]
Bakrie and COBOD establish JV for 3DCP
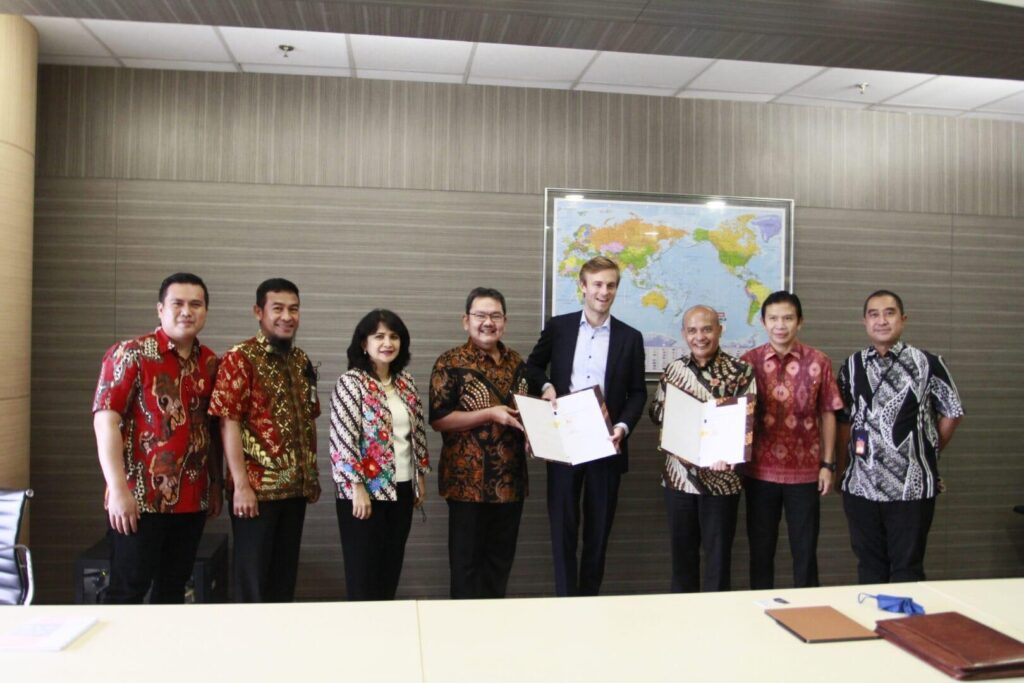
Director of PT Bakrie & Brothers Tbk (BNBR) Roy Hendrajanto M. Sakti, at the event said the agreement was made to forge the collaboration between Modula and COBOD, to focus on developing business in the construction industry with 3DCP technology in Indonesia. This collaboration will be realized in the establishment of a new company called […]