World’s First 3D Printed Living Seawall gets installed
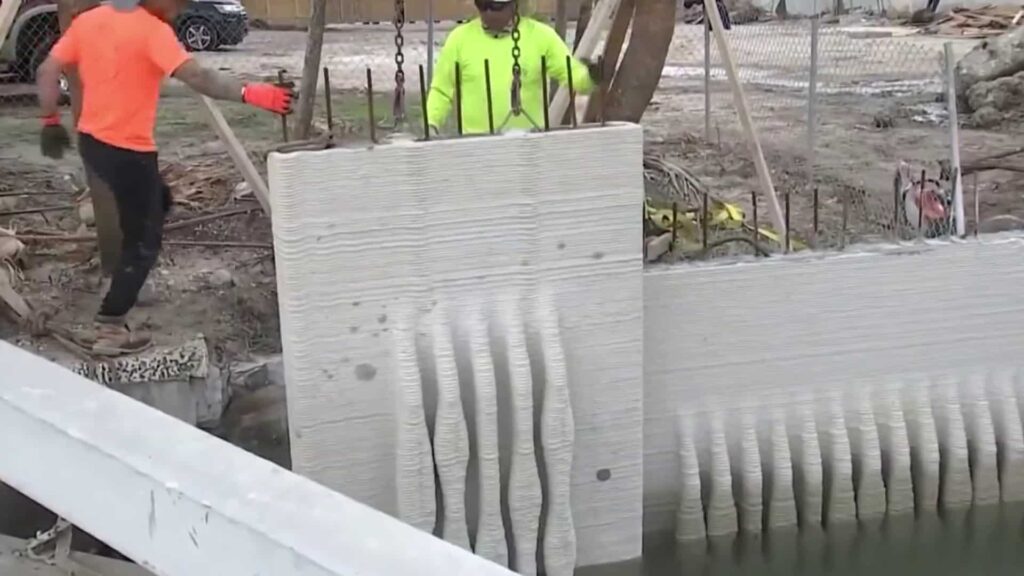
A future homeowner in Miami Beach has become the first to have Kind Designs’ Living Seawalls installed. Opting for this structure specifically to support the environment, they are the recipient of the world’s first 3D printed seawalls. While seawalls to prevent flooding are necessary along the Miami coastline, these Living Seawalls go a step further in environmental protection. In addition to safeguarding the land from erosion, flooding, storm surges, and sea-level rise, Kind Designs‘ Living Seawalls actively contribute to improving the local marine environment. Once installed along the shoreline, the Living Seawalls seamlessly support the needs of local marine ecosystems. Moreover, in addition to enhancing the sea, the seawalls also monitor its quality. Embedded sensors enable the Living Seawalls to measure information on water quality across as many as 15 different parameters.
Code Service report paves path to multi-story, 3D-printed structural concrete
Black Buffalo 3D Corp., a global provider of large scale, building-grade printers and proprietary cement-based ink, has worked with the International Code Council Evaluation Service in Itasca, Ill., to expand criteria in the ICC-ES AC509 – 3D Automated Construction Technology for 3D Concrete Walls report from single- to multi-story building.
Black Buffalo is raising the stakes in 3D-printed structural concrete, engineering equipment capable of placing up to four-story projects.
Operating until recently as Hyundai BS&C Co. Ltd., New York-based Black Buffalo 3D aims to increase awareness, efficiency and utility of additive manufacturing in construction. It continues to invest in printers and material science, intent on becoming the first to meet ICC-ES AC509 criteria. With printers developed by sister company Hisys, based in South Korea, its latest model is capable of printing up to four-story buildings.
“We want to build trust and prove the safety of our technology in a way that no other 3D construction printing company has done before,” says Product Specialist Jenn Christman. “Black Buffalo 3D was created to increase acceptance of printing in the construction industry, revolutionize traditional building techniques, and showcase the potential of large scale printing.” The latter concept has the potential to help governments, businesses and non-governmental organizations address a number of infrastructure or affordable housing needs and speed disaster recovery efforts, she adds.
ICC-ES is a nonprofit, limited liability company that performs technical evaluations of building products, components, methods, and materials. Agencies use evaluation reports to help determine code compliance and enforce building regulations. Manufacturers or suppliers use reports as evidence that their equipment, products and materials meet code requirements and warrant regulatory approval. — Black Buffalo 3D Corp., U.S. affiliate of HN Inc. co. Ltd., www.blackbuffalo.io
PRINTING TECHNOLOGY PRIMER FOR BUILDINGSThe Ohio University Russ College of Engineering and Technology presents concrete methods in “3D Printed Buildings Guide: Required Materials, Tips, and Resources” as part of a Master of Science in Civil Engineering degree overview, posted under Engineering & Technology Degrees at https://onlinemasters.ohio.edu. The guide provides an overview of 3D-printed buildings; project scheduling and labor-saving advantages; challenges for adoption of the casting/fabrication method; and, construction-grade printing materials.
“3D printing technology has had a revolutionary impact on enterprises around the world. It enables businesses to quickly develop models and prototypes, expediting their ability to test and fine-tune new products. It also makes it easy and affordable to manufacture pieces and components that keep important machinery working as intended,” guide authors explain. “One of the most exciting applications of 3D printing technology is in the construction industry, where it being used to construct entire homes, office buildings, and other structures. 3D-printed buildings can span thousands of square feet and multiple stories, and they can be made with lower costs and less waste than traditionally constructed buildings. [They] represent one of the most significant construction and design trends for civil engineers.”
Authors describe the basic process flow: 3D printing employs large-scale machinery into which an engineer inputs floor plans and building designs, and operators feed concrete ink or other printable building material; a software-guided extendable arm, or nozzle, then applies the material or mix in thin layers; the entirety of the building or structure emerges according to the engineer’s specifications, one layer at a time. Among benefits of 3D printing methods: Materials are consumed at exact volume requirements, free of waste, as printers can precisely follow blueprint dimensions and specs.
Construction tech startup partners with NASA on otherworldly 3D-printed homes that can sustain natural disasters — and possibly even space
Journalist Lesley Stahl’s introduction to her recent “60 Minutes” story about 3D printers sums up the initial promise of the unique technology.
“There was a time when futurists were predicting that the advent of 3D printing was going to change our lives — that each of our houses would have a 3D printer to make whatever items we need,” she said in a video clip.
While that isn’t yet the reality, the tech has taken perhaps an even more interesting path. 3D printers are actually building homes around the country.
[embedded content]
What’s more, Texas-based ICON has earned a nearly $60 million contract from NASA for its Project Olympus, to develop space-based 3D construction processes for an eventual trip to the Moon — and farther. The project builds upon other space-based research ICON has completed, per a company press release.
“To change the space exploration paradigm from ‘there and back again’ to ‘there to stay,’ we’re going to need robust, resilient, and broadly capable systems that can use the local resources of the Moon and other planetary bodies,” ICON CEO Jason Ballard said in the statement.
ICON has already made a name for itself in 3D printing. The company is working on a project in its home state that will be the world’s largest 3D community. There are 46-foot-wide printers deployed on-site to create the 100 homes, which have solar panels to maximize sustainability, as CNN reported.
#cool_newsletter_374fb93f-e633-47a3-9403-16a81b6718e0 .cool_newsletter__inner span{color:#000000}
JOIN OUR NEWSLETTER
Good news, green hacks, and the latest cool clean tech — straight to your inbox every week!
The tech is touted as creating less air pollution than traditional building methods, with a host of other benefits, including withstanding 200-mile-an-hour winds and being fire-resistant and termite-proof, according to 60 Minutes.
“That’s why this feels like lightning in a bottle,” Ballard told 60 Minutes.
As part of the NASA job order, ICON’s team will be working in support of the agency’s Artemis program, aimed at putting the first woman and person of color on the Moon for new types of exploration, according to NASA.
“In order to explore other worlds, we need innovative new technologies adapted to those environments and our exploration needs,” Niki Werkheiser, from NASA’s Space Technology Mission Directorate, said in the ICON press release. “Pushing this development forward with our commercial partners will create the capabilities we need for future missions.”
ICON’s advanced hardware and software will be leveraged. The team will have access to lunar rock samples from Apollo missions to study their properties in simulated lunar gravity, to use as much material sourced from the Moon (or one day Mars) as possible.What they learn about the Moon’s rocks will help the team determine how their 3D equipment can one day build “landing pads, blast shields, and roads,” all per ICON. It’s the infrastructure needed for human existence on foreign worlds.
“The final deliverable of this contract will be humanity’s first construction on another world, and that is going to be a pretty special achievement,” Ballard said.
Join our free newsletter for weekly updates on the coolest innovations improving our lives and saving our planet.
Cool Picks
Open-Air Kenyan Holiday Homes
Italian design studio PAT works together with fellow architect Ferdinando Fagnola on the Falcon House renovation project that is located on Kenya’s Manda Island. The holiday home is defined by open-air bedrooms and terraces that are raised to overlook the lush surroundings over the treetops. The self-sufficient building provides its water and electricity with passive […]
A first Passive House retrofit in Halifax
A circa-1850s two-storey home is being converted into an office space for Habit Studio, a women-led architecture firm based in Halifax, Nova Scotia. The project is unique as it’s the first Passive House retrofit in the province. Once complete, it will serve as an inspiration for others pursuing deep retrofits of existing buildings, an endeavour […]
Recovering heat from shower water and 3D printed homes: the future of house building in Ireland
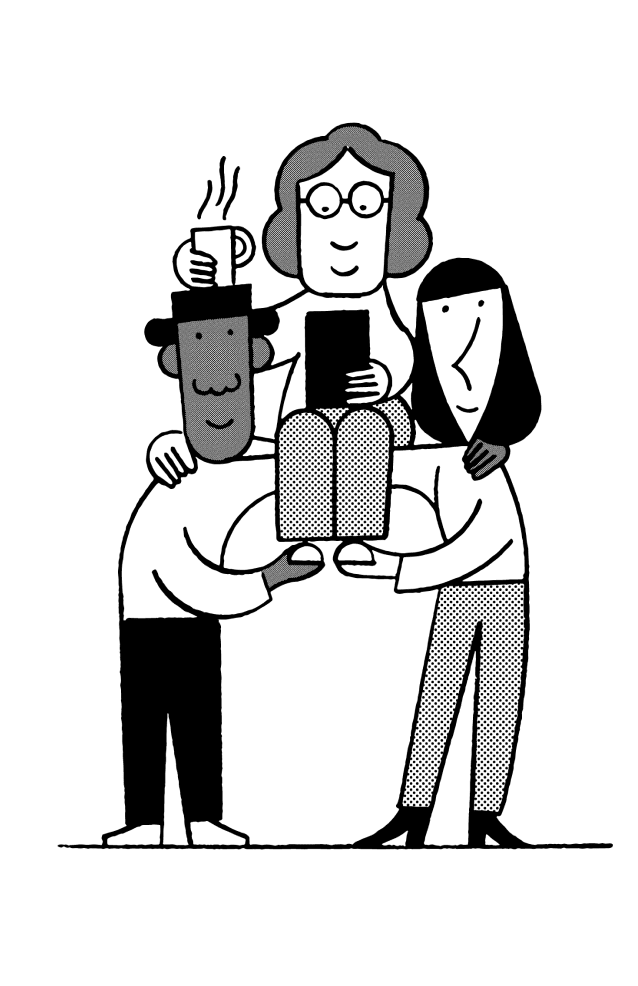
PLANT-BASED INSULATION, technology to recover the heat from shower waste waster, and 3D-printed homes are some of the innovations being explored as the EU moves to tackle emissions in its buildings.
A conference being held in Dublin later this month – the Zero Emissions Buildings (ZEB) Summit – aims to discuss and explore the ways to make old and new buildings in Ireland more environmentally sustainable.
According to estimates, over a third of all of the EU’s planet-warming greenhouse gas (GHG) emissions come from buildings, many of which are old, poorly insulated and heated and powered by fossil fuels.
Under its international commitments, the EU aims to be fully climate-neutral by 2050 – an economy with net-zero greenhouse gas emissions. This will require large-scale changes to almost every sector of society, many of which are already underway.
For buildings, the EU has set two key targets. The first is to bring all older public and private buildings across the continent up to a proper environmental standard through a massive retrofitting programme (at a potential cost of €1 trillion).
In Ireland, the National Retrofit Plan aims to support the retrofitting of the equivalent of 500,000 homes by 2030, in order to bring them to a suitable standard. Progress has been slow however, with just under 48,000 homes supported last year, though this is a significant increase on 2022.
The second major EU target is to ensure that all new builds on the continent are zero-emission buildings (ZEBs) by 2030. Essentially, ZEBs are buildings that produce the same amount of energy per year that they use.
It will fall to individual countries to put in place the laws and regulations to meet these targets. In Ireland, a number of innovations and avenues are being explored at industry level in order to make building more sustainable.
“Buildings in the future are not going to be consumers of energy but prosumers of energy,” said Tomás O’Leary, the managing director of Irish architecture firm Mosart.
So a home in the future will be like a mini power plant. And the idea of those mini power plants is they should be brought to such an efficient level that they start to even out the energy consumption of the old buildings.
MosArt specialises in designing passive housing: buildings that meet very high environmental and sustainability standards.
The firm is also behind the upcoming ZEB Summit, which it is arranging in partnership with a number of groups, including Dún Laoghire Rathdown County Council.
DLRCC is currently building 597 new social and affordable homes at Shanganagh in Shankill. The scheme is supported by the Land Development Agency (LDA) and when completed will be one of the largest passive housing social schemes in Europe.
O’Leary says he designed the first passive house in the English speaking world in Wicklow in 2004, and since then he’s watched as buildings that meet a high environmental standard have become “a nice to have to a need to have”.
ZEB Summit aims to explore the shifting landscape of sustainable construction, with talks and panel discussions on a variety of different topics centred around sustainable housing construction and retrofitting programmes.
Advertisement
Among these, will be the use of 3D printing in home building, the use of plant-based insulation to lower emissions, and methods to recover the heat from drain water.
“Right now, every time you take a shower, all that heat and energy goes into the sewer and is completely lost,” said O’Leary.
“It’s as bad as using a plastic bottle just one time. It’s almost like single use energy.
But in the future every house will have a very simple device that can recapture about 50-60% of the heat of the water that is going out into the sewer.
Up for discussion will also be how to manage and reduce the “embodied carbon” of buildings, that is the the greenhouse gas emissions arising from the manufacturing, transportation, installation, maintenance, and disposal of building materials.
EU changes
The EU is in the process of passing a new Energy Performance of Buildings Directive (EPBD) which will enshrine its new building targets into law, and it will then fall to each individual state to implement measures to achieve them.
The EPBD was agreed in principal in December last year, but it still needs to be voted on in the EU Parliament. That vote is due to take place later this month but work is already underway to start adapting home building for the future.
“We have achieved something remarkable… created a blueprint for the world to decarbonise its building stock,” Green Party MEP Ciarán Cuffe – who was the lead negotiator of the deal – said in December.
With this plan, we add an essential pillar to the EU’s decarbonisation plans and begin the long journey towards reducing 36% of Europe’s CO2 emissions.
Climate scepticism
While the EU pushes ahead with its Green Deal and aims to decarbonise its economy, there is growing discontent from different sectors of society.
In countries across the union, there has been a reaction against the implementation of green policies. The recent tractor protests by farmers’ groups are one indication of this.
Some experts are predicting that the upcoming European Parliament elections will see a shift towards parties and MEPs hostile to an environmental agenda.
What this means for the future of homebuilding in Europe and Ireland remains to be seen, however O’Leary of MosArt says that the drive towards sustainability is not solely being pushed by EU regulations, but by customers’ preference and, crucially, international finance.
“It’s interesting, it’s almost like the building regulations are not driving performance anymore, it’s the global drive for sustainability.
Essentially, if you don’t have the know how to deliver high performance homes you’re going to get left on the roadside.
Zeb Summit takes place on 21-21 February
A mix of advertising and supporting contributions helps keep paywalls away from valuable information like this article.
Over 5,000 readers like you have already stepped up and support us with a monthly payment or a once-off donation.
For the price of one cup of coffee each week you can make sure we can keep reliable, meaningful news open to everyone regardless of their ability to pay.
The Best Eco Homes On The Market Right Now
Solar-powered swimming pools? Air-source heat pumps? Wildflowers on the roof? You name it, these homes have got it. If you’re searching for a luxurious contemporary property with an eco-friendly twist, look no further: these are best eco homes on the market. The Best Eco Homes on the Market Right Now Hollow Way Lane, Amersham This […]
Monticello business aims to 3D print biggest building in the Midwest with new technology
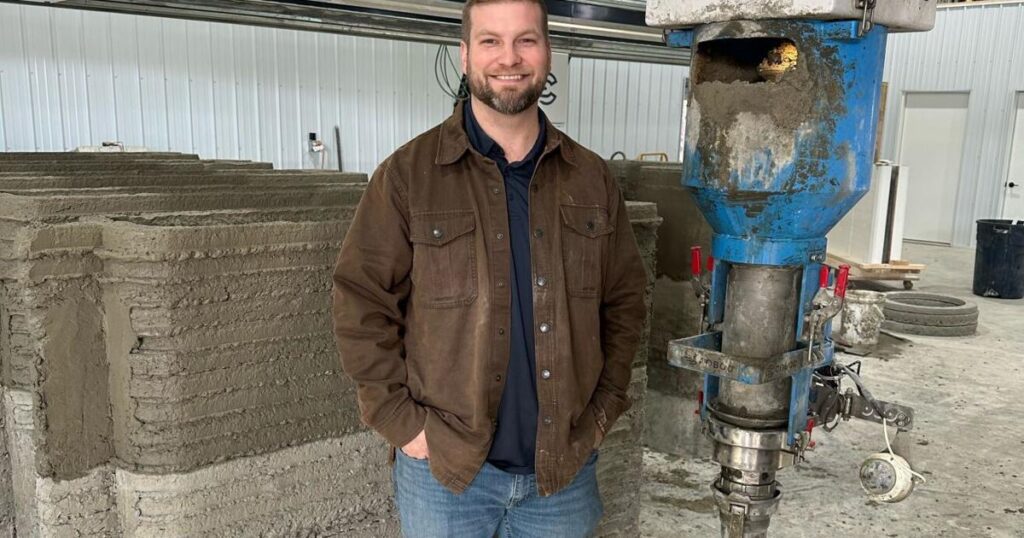
MONTICELLO — Monticello will soon be home to the largest 3D-printed building in the Midwest.At least that’s what Nathan Lilly, founder of LX 3D Concrete Printing, plans to make happen, and he’s only just getting started.His company uses a large-scale 3D-printing machine equipped with a patented nozzle and custom concrete recipe to print buildings that Lilly said are more resistant to flood, mold, fires and tornadoes than structures made out of typical materials.
The buildings are also more energy- and cost-efficient, and require significantly less time to construct. The printer can lay down 10 inches of concrete a second, so the walls of a 2,000-square-foot building can be built in less than 20 hours.The method, Lilly said, carries the potential to revolutionize housing to become more affordable, durable and less supply-chain dependent.“We’re really making a structure that would be prohibitively expensive to compete with if it was truly in wood,” Lilly said.“Here’s an easy way to explain it. There’s a book called ‘The Three Little Pigs,’ right? We’re on house number two and we’re changing it to house number three.”Lilly printed his first building, a 1,500-square-foot structure in Monticello, last fall. He said he’s now only waiting on permits to be approved before he starts printing an 8,000-square-foot combination-industrial-office building this spring that he plans to later lease.Born in central Illinois, Lilly said he worked in real-estate investment and development — most recently as the chief financial officer for the student housing company JSM Living in Champaign — before he started LX two and a half years ago.The idea started, in part, after his parent company, Lilly Capital, a private-investment firm, began looking at acquiring a chain of local hardware stores.But a team member posited that hardware stores would probably be put out of business, Lilly said, if a shop could print whatever part a customer needs right then and there and not have to carry inventory.Lilly said he then decided to look into printer technology and acquired a $1 million concrete printer from the Danish company Cobod. The machine can print 25-foot-tall walls without being moved.
Though the machine runs with typical-grade concrete, Lilly said he tinkered with the ratio of its ingredients and developed a special nozzle to allow the machine to print buildings that look like they’ve been constructed using traditional methods.A common critique of concrete construction is that cement requires high heat and a large carbon footprint in order to bind to local aggregates. Lilly said he’s conducted tests with more environmentally sustainable alternatives, but those alternatives have not been structurally approved yet.“The printer is really just a delivery vehicle,” Lilly said. “So it’s very easy for us to adapt and change to any material design improvements, whether it’s fly-ash or some alternative that dramatically reduces the carbon footprint of actual cement.”Further, the construction of 3D-printed buildings nets less waste because the company only manufactures what materials they need from a mixer on-site, Lilly said. And concrete buildings can last much longer than structures made primarily of wood or plastic.Lilly’s number one goal in starting LX was to create homes, but he added that it would be foolish to restrict the company to only use. That’s because printing technology has the potential to create other concrete items more efficiently, like concrete tubes for city utilities.For example, Lily said he already scoped plans to mass-produce a three-year’s supply of lids for a septic tank company in one day.“Initially, we were just planning to subcontract for larger volume home buildings, but we kind of realized that the only way to add value to the most people possible is to not turn people down,” Lilly said.“Really, if anyone wants a structure built, we’re certainly going to be open to it. Our goal is to invest really heavily into the space and shelter the whole world if we can — at least the Midwest.”
Texan builds stunning ‘passive house’ that uses 75% less electricity than most homes: ‘The best way to build’
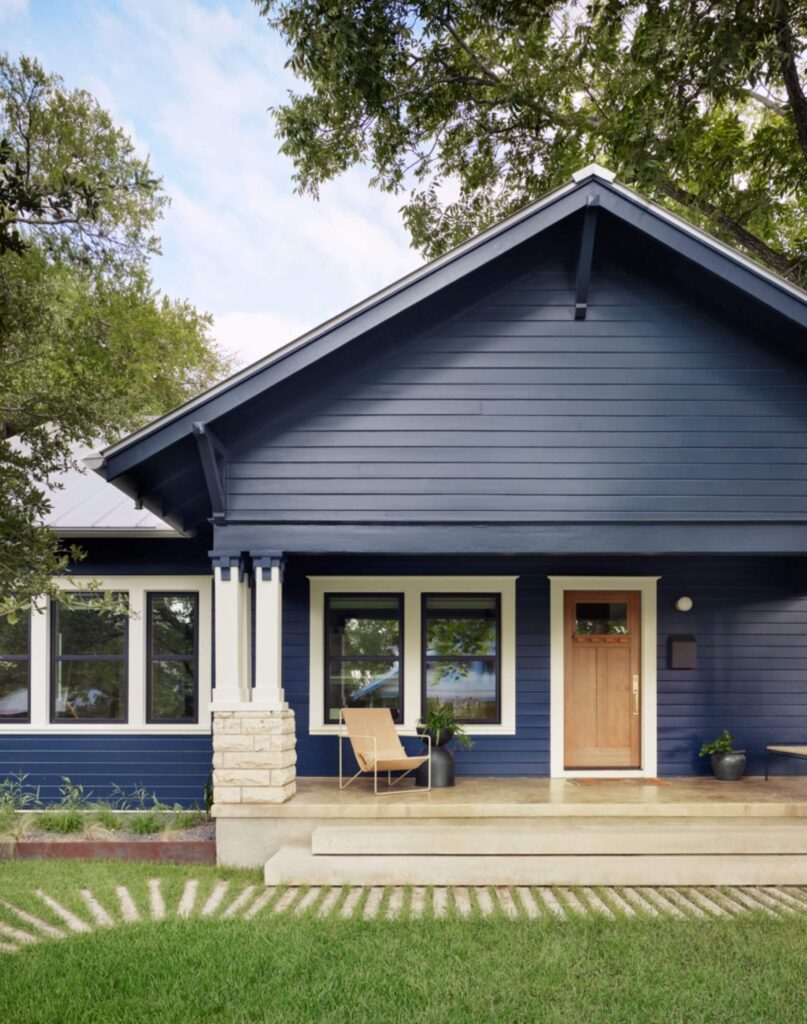
As far as Trey Farmer is concerned, every new home should be a passive house. Passive houses are made to be as airtight and insulated as possible. This helps lock in the comfortable temperature inside, protecting residents from both heat and cold, while dramatically lowering the need for heating and air conditioning. They’re a specialty […]
Printing Swedish houses with algae
For the first time, a new material made from tiny cellulose fibers and algae has been tried as a more environmentally friendly option for construction.
Researchers from Chalmers University of Technology and the Wallenberg Wood Science Center in Sweden experimented with this sustainable material and found it can be used to create various architectural components using less energy than traditional methods.
The construction industry is a major contributor to global pollution, using half of the world’s fossil fuels, generating 40% of waste, and producing 39% of carbon dioxide emissions. To combat this, scientists are exploring biomaterials like nanocellulose, which is already used in biomedicine for its ability to be 3D printed into structures for tissue growth. This study marks the first attempt to use dried nanocellulose in architecture.
By mixing nanocellulose fibers with water and an algae-based substance called alginate, the researchers created a material that could be 3D printed. This blend provided flexibility to the material when it dried, enabling its use in architectural applications.
The use of 3D printing in architecture is seen as a resource-efficient method. Unlike traditional methods that produce waste, 3D printing requires fewer materials and less energy, particularly when using a robotic system that operates at room temperature. The properties of the nanocellulose hydrogel allow it to be easily printed and maintain its shape without requiring high temperatures.
The researchers tested various printing techniques to understand how the material behaves when dried in different shapes. These dried shapes could be used to create lightweight architectural elements such as room dividers, blinds, wall panels, and coatings for existing building components.
This study lays the groundwork for further exploration of nanocellulose in architectural design, highlighting the need for new approaches to incorporate biobased materials into buildings. Understanding the properties and design possibilities of these materials is crucial for creating sustainable and aesthetically pleasing structures that align with the goals of a circular economy.
Robotically 3D printed architectural membranes from ambient dried cellulose nanofibril-alginate hydrogel“, published in the journal Materials and Design.
#GreenBuilding #SustainableDesign #Nanocellulose #Architecture
Custom Home Design: The “Quiet Luxury”
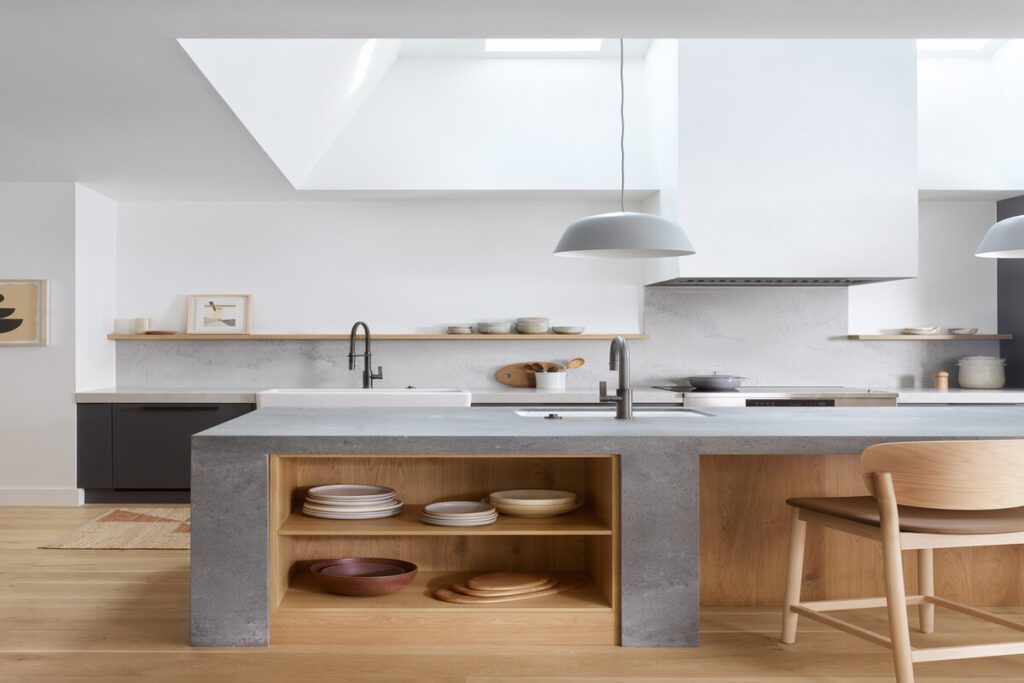
In fashion, ‘Quiet Luxury’ emphasizes minimalist, supreme-quality pieces with timeless appeal. The trend also champions sustainability by advocating for buying apparel that’s versatile and not limited to a season (i.e., fewer clothes = less waste). Over the last decade or more, these considerations have steadily permeated every aspect of our physical lives. We buy organic, […]
Buffalo Crossing visitor centre first Manitoba Passive House project
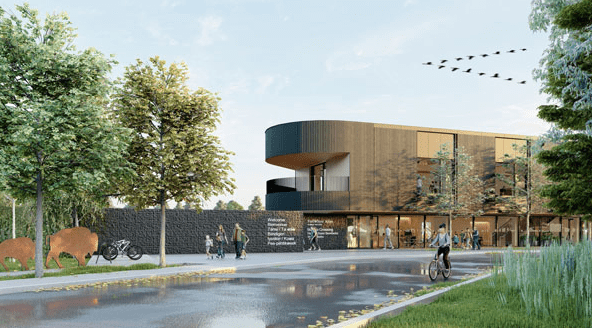
Buffalo Crossing, the new year-round visitor centre currently under construction at FortWhyte Alive, Winnipeg’s best-known nature reserve, is the first commercial project in Manitoba being built using a Passive House construction model. “Using the Passive Housing standard is part of our mission to be a leader in sustainability development,” comments FortWhyte Alive vice-president Ian Barnett. […]
#3DExpress: The First Metal 3D Printer Is Going to Outer Space
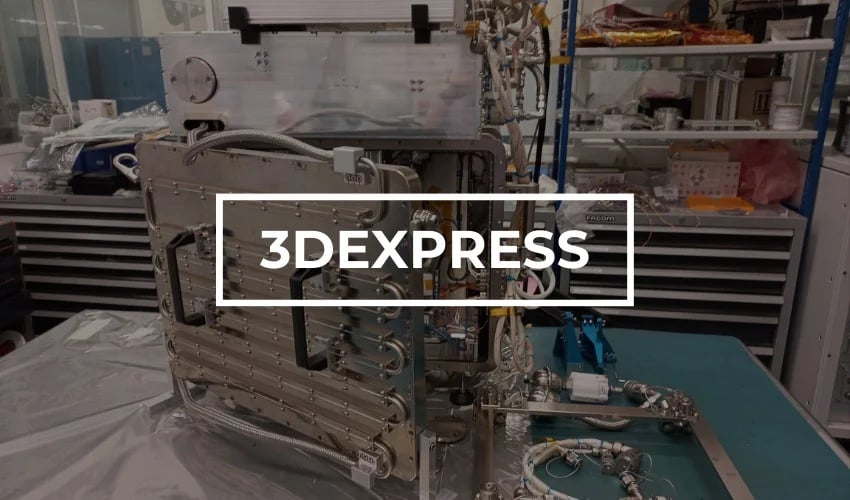
Once again, it is time to take a look back at some of the news that has marked the additive manufacturing sector this week. And we’re starting with a piece of news that truly does show that not even the sky can be a limit for 3D printing, as it involves exploring space. French company AddUp has announced, in collaboration with Airbus Defense & Space, that it will be sending the first metal 3D printer into space! It should enable the creation of spare parts aboard the International Space Station. We also take a look at the first FDA-certified 3D-printed gastric device, an unprecedented achievement in the medical sector. We’ll also be talking about Boston Micro Fabrication’s growth, submicron 3D printing and the completion of the largest 3D printed house in Europe. Happy reading and have a great weekend!Airbus Will Send a Metal 3D Printer into SpaceMetals 3D printing solutions manufacturer AddUp has just announced the delivery of a working metal 3D printer in space to the European Space Agency. In collaboration with Airbus Defense & Space, the company has developed a customized metal solution capable of designing parts in microgravity conditions aboard the International Space Station. The project, which began in 2016, marks a milestone in space exploration. The machine is due to be installed on board the Columbus scientific module and will enable the production of four parts. These will then be returned to Earth for analysis, the aim being to make metal additive manufacturing viable in space. This could open up a host of possibilities for astronauts, including the manufacture of spare parts on demand.Test parts made by the metal 3D printer before its launch into space (photo credits: ESA)Triastek’s 3D Printed Gastric Device Receives FDA ClearanceWe continue this #3DExpress with Triastek, which announced recently that its 3D-printed gastric device has received FDA clearance. Named T22, the model has become the first 3D-printed gastric retention device to receive this certification. The component was created using Triastek’s proprietary melt extrusion and micro-injection molding (MED&MIM) process. This development could benefit the treatment of pulmonary arterial hypertension and chronic thromboembolic pulmonary hypertension. T22 could reduce the frequency of administration to once-daily, simplifying the dosing regimen and improving compliance. Following this approval, Triastek said it was preparing to launch clinical studies with T22 to accelerate product development.The 3D-printed gastric device (photo credits: Triastek)Scrona and Avantama Enable Submicron 3D PrintingA collaboration between Scrona and Avantama has recently produced satisfactory results: the technology of ETH spin-off Scrona, combined with Avantama’s materials, has proven capable of 3D printing on a sub-micron scale for the manufacture of MicroLED displays. Avantama manufactures high-performance quantum dot inks with very high absorption coefficients, which are particularly well suited to Scrona’s 3D printing process. Meanwhile, Scrona’s electrohydrodynamic (EHD) inkjet technology enables very high-viscosity inks to be processed. Viscosity can be much higher than that of conventional printheads. With EHD technology, the material does not drip from the nozzle, but is extracted from it, enabling micrometer resolutions to be achieved. This makes the process particularly attractive for the manufacture of semiconductors and microdisplays.Photo Credits: ScronaBoston Micro Fabrication Has Achieved 30% YoY GrowthBoston Micro Fabrication, which is well-known for its microscale additive manufacturing solutions for ultra-high precision applications, has announced that it achieved 30% year-on-year growth after a landmark 2023. While many in the AM market have been struggling, BMF, it se ems, has been soaring. Indeed, in the same press release, the company notes that it also recently secured its Series D Funding, launched in new markets including dental, and expanded its San Diego Research Insititute (SDRI). Expanding on the news, John Kawlo, CEO of BMF, commented, “Amid a challenging economic environment on both a global stage and for the 3D printing industry, we are very proud of the progress made over the last year to help our customers push the boundaries on what is possible with our technology. And while a lot of this success is due to strong execution from our team, much of it is based on our product-market focus and the fact that we are building a high value, differentiated business.” BMF is known for its additive manufacturing solutions for microscale parts (photo credits: BMF)Europe’s Largest 3D Printed House Completed in HeidelbergEurope’s largest 3D-printed house is finally ready. Located in Heidelberg, Germany, it took 170 hours to print using a special concrete developed by Heidelberg Materials. It’s worth noting that it wasn’t easy for the owners to fit a roof over the undulating shape of the house. Nevertheless, the project has now been completed and the keys handed over this week. IT company HeidelbergiT is now moving into the building. Despite the challenges, this 3D-printed house can be considered a pilot project for home 3D printing.Photo Credits: Heidelberg MaterialsWhat do you think of this metal 3D printer from Airbus and AddUp which will be going into Outer Space? Let us know in a comment below or on our LinkedIn, Facebook, and Twitter pages! Don’t forget to sign up for our free weekly Newsletter here, the latest 3D printing news straight to your inbox! You can also find all our videos on our YouTube channel.
Super-Sustainable L.A. Home With Cutting-Edge Eco-Friendly Features Lists for $3.89 Million
A newly constructed contemporary-style “healthy” home in Los Angeles, the first in the city to meet the stringent sustainable building standards of the Passive House Institute US, is being listed Friday for $3.895 million. “Buyers here haven’t seen passive houses before,” said Dayna Campbell of Berkshire Hathaway HomeServices California Properties Encino Office, who is co-listing […]
Completed Data Center Is Europe’s Largest 3D Printed Building – 3DPrint.com | The Voice of 3D Printing / Additive Manufacturing
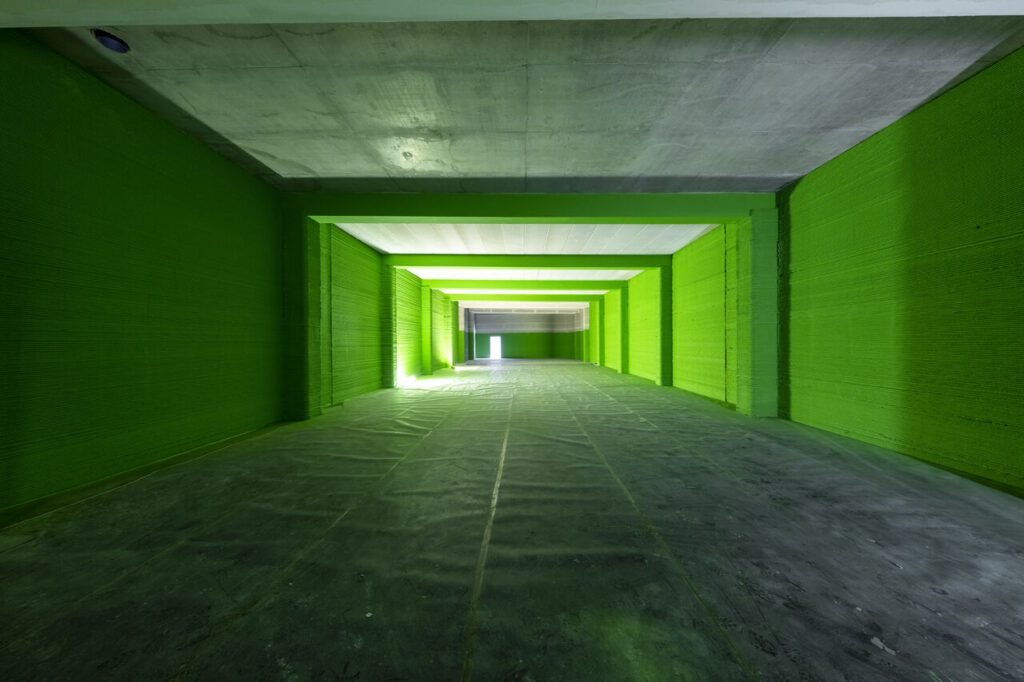
As exciting as 3D printed homes are, particularly when part of a feel-good story, it is the industrial applications of the technology that may represent the maturity of the additive construction (AC) sector. This is made evident with the completion of Europe’s largest 3D printed building, the Wavehouse data center in Germany, which is described as the first of its kind in the industrial and data center sectors globally.
Developed by Kraus Group, with participation from architecture firms Mense-Korte and SSV, this single-story facility is situated in the Baden-Württemberg region of Heidelberg. It took the PERI Group, an investor in AC firm COBOD, about 140 hours to complete the nearly 600-square-meter building using a BOD2 3D printer. According to the companies involved, about 450 tons of printing concrete, provided by Heidelberg Materials, were used. This material is described as both 100% recyclable and featuring a binder capable of achieving a 55% CO2 reduction compared to traditional Portland cement.
Building Leaders Serious about Construction 3D Printing
Founded in 1874, Heidelberg Materials is a €21.095 billion company, with 57,000 employees working at 3,000 production sites across 60 countries. This puts it on par with COBOD investor and materials company Holcim and somewhat ahead of COBOD investor and materials company CEMEX, as well as Swiss AC backer and materials company Sika. All are less than half the size of the €51.2 billion French materials giant Saint-Gobain, which is pursuing AC through its Weber Beamix subsidiary. There are only some of the leading construction businesses exploring the technology, but they are representative enough to demonstrate just how serious the sector has become.
What’s also interesting is the overlap by these firms in the AC space. As noted, several are COBOD investors, while both PERI Group and Sika have backed another construction 3D printing startup, Mesh AG. The technology of COBOD and Mesh are complementary, in that Mesh can 3D print steel reinforcement for 3D printed buildings, such as those made with COBOD’s machines. However, one would think of Sika, Holcim, and CEMEX as competitors. Obviously in global business, multinational corporations share much in common and similar goals in terms of “growing the pie,” but the extent to which these frenemies can coexist investing in the same startup is difficult to foresee.
Construction 3D Printing and Infrastructure, Growing Together
The Wavehouse will be operated by Heidelberg iT Management, a local cloud and data center provider with a history dating back to 2001. The center is expected to offer 500kW of power and accommodate around 100 racks. While the facility’s 3D printed shell has been completed, the total job is expected to be finished by the end of the summer.
While the Wavehouse is a more traditional form of data center, EdgeCloudLink in the United States plans to pursue the construction of hydrogen-powered, off-grid modular data centers built using 3D printing. The market for data center construction is massive, with some analysts projecting a seven percent growth from $250.4 billion in 2023 to $270.07 billion in 2024. This makes sense given the growing need for servers in general, thanks to such technologies as artificial intelligence and cloud computing.
In order to keep up with demand, builders will likely turn increasingly to AC as a means of constructing these structures more quickly, while also demonstrating the ability of 3D printing to make facilities that can meet the requirements of data centers in terms of cooling and structural integrity. This trend would complement other infrastructure projects that AC will certainly play a role in, such as new rail systems, power generation, disaster relief, and general construction.
All images courtesy of Heidelberg Materials.
Subscribe to Our Email Newsletter
Stay up-to-date on all the latest news from the 3D printing industry and receive information and offers from third party vendors.
Please enable JavaScript to view the comments powered by Disqus.
Guatemala receives first 3D printed building
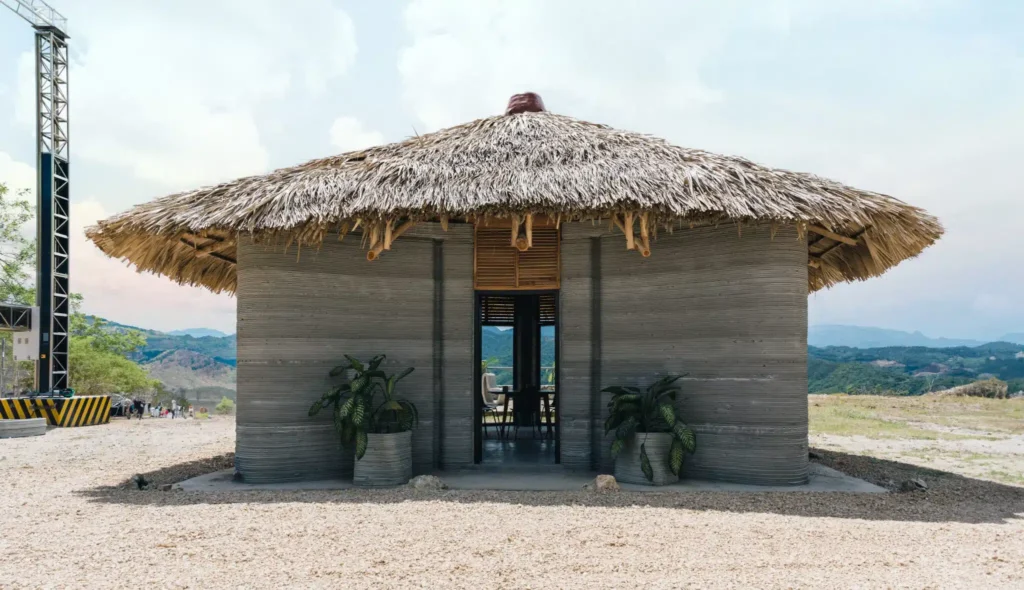
Stay up to date with everything that is happening in the wonderful world of AM via our LinkedIn community.
Progreso, a leader in Central and South America’s cement industry, has inaugurated Guatemala’s first-ever 3D printed building, through its corporate accelerator, Progreso X. The milestone was achieved in collaboration with Danish 3DCP Group, utilizing COBOD International’s BOD2 construction 3D printer.
The project has successfully taken steps to validate the structural viability of 3D construction printing in a seismic-prone region. The build, featuring 3m (9 feet) high 3D printed walls, was completed in just 26 printing hours, over seven days.
Due to the use of 3D printing, the house features highly organic-shaped walls that would otherwise be extremely expensive, or even unfeasible to complete with concrete blocks – the region’s predominant building material.
The 3D printed concrete walls are complemented by a “Rancho” type palm leaves roof. This roof type has been used for generations in Latin America, as it is inexpensive, provides thermal comfort, and is well-suited for seismic regions due to the flexible and lightweight nature of the material.
“With immense satisfaction, we completed this unique project using 3D printing technology, once deemed distant. Progreso’s enduring spirit of innovation led us to explore new methods, culminating in a collaboratively designed building featuring a sustainable “rancho” roof, ensuring natural cooling in seismic regions. This achievement, a testament to our teamwork, harmoniously blends advanced technology with local traditions, thanks to the unwavering support of 3DCP Group and COBOD,” said Plinio Estuardo Herrera, Manager of Concrete R&D at Progreso.
The project, representing Guatemala’s entry into the world of advanced global construction methods, was achieved through a partnership with Denmark’s 3DCP Group, widely known for 3D printing the first school in Ukraine as part of the reconstruction of the country. The partners will reportedly be working on more projects in the region.
“The completion of Guatemala’s first 3D printed house living up to all seismic requirements marks a significant milestone for construction 3D printing in Latin America. The region has adopted 3D construction printing slower than others, but the interest is growing rapidly. We expect interesting new developments to happen shortly, including in Mexico, especially now that successful steps have been taken to verify the suitability of the printing technology in a seismic region,” said Philip Lund-Nielsen, Co-Founder and Head of Americas of COBOD.
Rogers OKs 3D-Printed Housing Development, the First in Arkansas
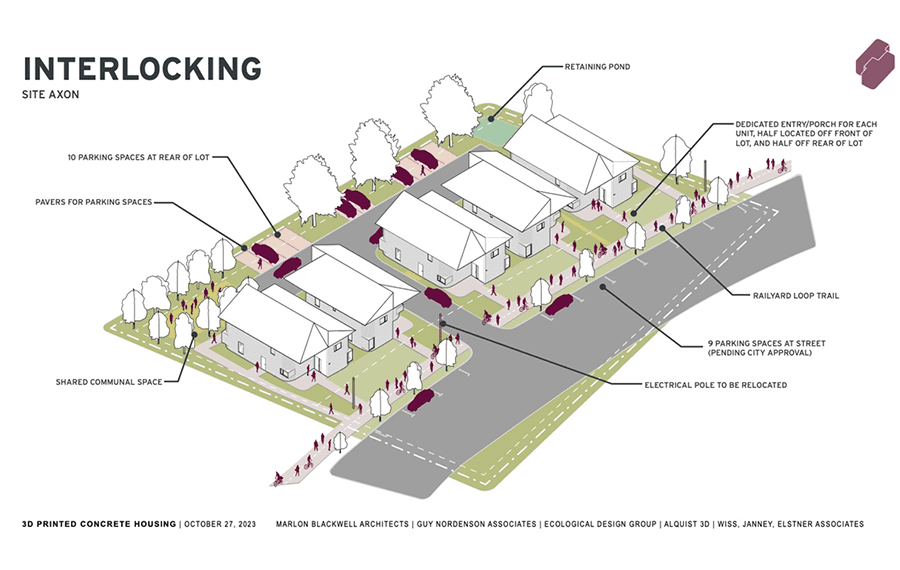
Plans for a 3D-printed housing development in Rogers (Rogers Lowell Chamber)
A 3D-printed housing development said to be the first of its kind in Arkansas is moving forward, the Rogers Lowell Chamber announced.
The Rogers City Council recently approved the $50,000 sale of an acre of land for the project, which will use 3D-printed concrete to construct at least four two-story duplexes with eight units apiece. The duplexes will range from 1,300 SF to 1,600 SF.
Construction is scheduled to begin in late spring or summer, with occupancy targeted by late 2024.
Groundwork Northwest Arkansas, the Northwest Arkansas Council’s workforce housing center, is leading the project. The organization is collaborating with Alquist 3D of Greeley, Colorado, which is known for using robotic technology capable of building a 1,500-SF home in 30 hours.
The project at 920 S. First Street near downtown Rogers aims to help address the region’s lack of affordable housing. The homes will be sold to buyers who earn below more than 80% of the area’s median income.
Home prices in northwest Arkansas have surged as the region’s population has grown. In Benton County, where Rogers is located, the average sale price in the second half of 2022 was $423,564, up more than 77% from five years ago.
“We’ve got to look for ways to build more efficiently that will bring these building costs down,” Duke McLarty, director of Arkansas Groundworks, told Arkansas Business news partner KFSM.
People looking to rent have few options. The multifamily vacancy rate in the region is “functionally zero,” according to the latest Arvest Bank Skyline Report.
Groundwork is also behind a housing development in Springdale called “Big Emma.” Thirty of the development’s 77 units will be permanently reserved for households earning below the region’s median income. The project is supported by a grant from the Walton Family Foundation.
Arkansas’s First-Ever 3D-Printed Homes Project Gets Approved
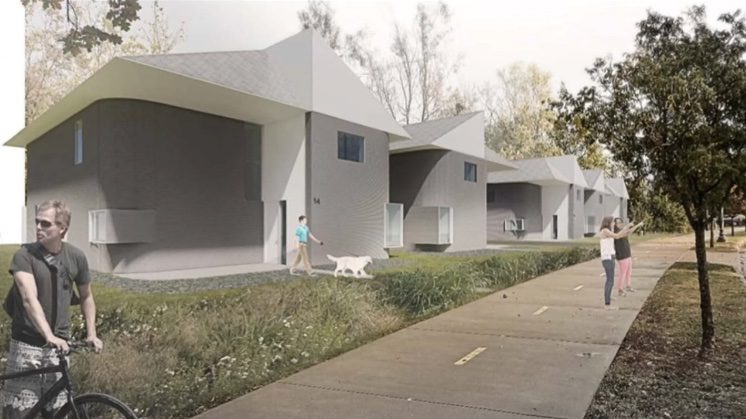
Arkansas’s first-ever inaugural 3D-printed housing project has received the green light from the Rogers City Council, which approved selling an acre of land to the Northwest Arkansas Council Foundation for the development. The project is aimed at addressing housing affordability.The foundation’s affordable housing division, Groundwork Northwest Arkansas, will use 3D-printed concrete technology to build two-story duplexes at 920 S First Street for those earning below 80 percent of the area’s median income. The sale of land was sanctioned at $50,000.“This will be one of, if not THE, first two-story residential 3D-printed homes in the U.S., and it is the first 3D-printed home in Arkansas,” Groundworks Executive Director Duke McLarty said.For the project, Groundwork will partner up with Alquist 3D, a company known for using robotic technology to create 3D-printed concrete homes, capable of building a 1,500-square-foot home in 30 hours.“At least four structures” comprising “at least eight units of housing” are expected to come from the project. These will feature two-story duplexes ranging from 1,300 to 1,600 square feet.Construction is expected to begin in late spring or summer, with occupancy anticipated by late 2024.To learn even more information about this groundbreaking project, click here.READ ALSO: ASO PLACES FINAL BEAM ON NEW $11.75M MUSIC CENTER
Godrej & Boyce builds 500-sq-ft office in 40 hours with 3D construction printing technology
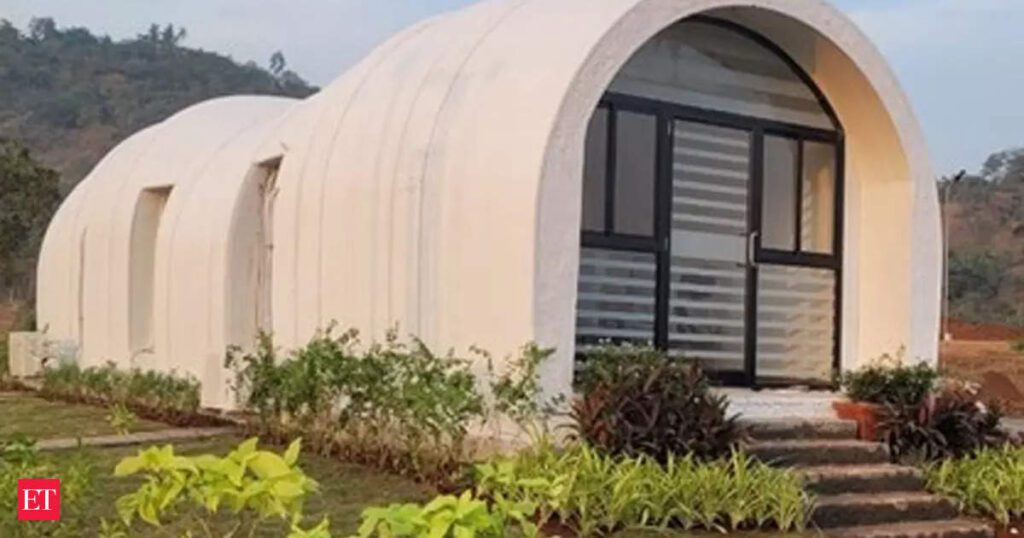
Godrej & Boyce, the flagship company of the Godrej Group, has constructed a 500 sq ft office in the company’s own greenfield campus at Khalapur near Mumbai in a 40-hour timeframe.
The First House Made With 3D Printing and AI Announced In Portugal
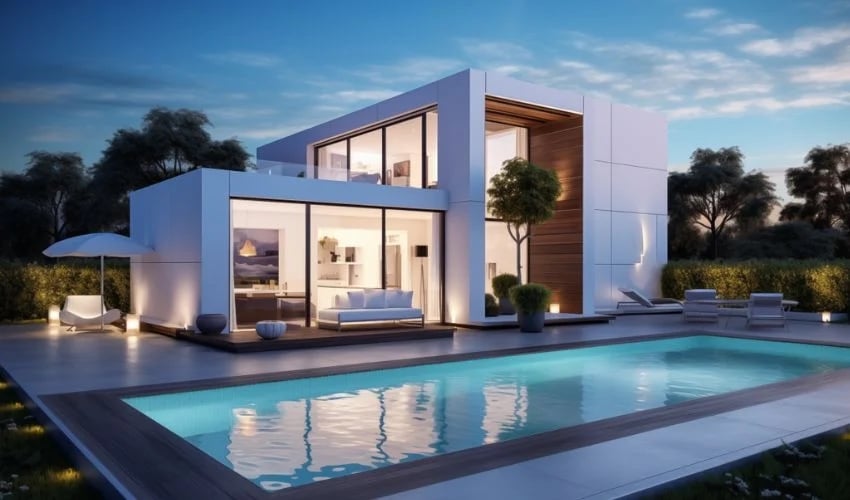
As we all know, additive manufacturing is being implemented in a growing number of sectors. One example is construction, where 3D printed housing is booming. In fact, soon we may see the first 3D printed house in Portugal. Not only that, but the house will be made not just using 3D printing but also artificial intelligence (AI).If you have been following us for a while, you must know that in the past two years there have been all kinds of 3D printed homes unveiled. This of course ranges from low-cost housing designed to alleviate the housing crisis to homes that have been optimized and designed to be more sustainable. In fact, it has grown so significantly that the construction 3D printing market is expected to grow in value from $3.5B in 2023 to $400 billion by 2030. Now, the company Litehaus has also decided to put its hat in the range by focusing on sustainable construction for luxury housing.A mock-up of what the house is expected to look likeMaking a House With 3D Printing and AITo be located in Torres Vedras, Portugal (only 30 minutes from Lisbon!), this house, as mentioned, will be made by combining 3D printing and AI. During the initial creation and design phase, Litheaus, has made use of AI to create the interior and exterior design of the home. This is a significant breakthrough for the construction and 3D printing industry.The manufacture of this type of modular buildings with 3D printing has a number of very important benefits. One of them is related to energy consumption. As we can well imagine, the energy consumption of a 3D printed house is lower than that of a house built by traditional methods, but how low is it in comparison? The answer is that 67% less energy is needed if the house is built in 3D. This will hopefully put a dent in the estimated 42% of carbon emissions for which the construction sector is responsible.Another big advantage is speed, as Simi Launay, creative director of Litehaus, explains, “This technology [allows] us to produce as much as 45m2 of walls in only 20 hours.” As most of the 3D printing of this home will be focus on the walls, this is not insignificant. Indeed, the hope is to build up to 100 houses a year in the country, starting from a complex of thirteen houses!Launey further explained the purpose of this project, concluding: “Litehaus is embarking on a mission to redefine living spaces, fusing AI technology, 3D printing and modular homes to create buildings that resonate with simplicity, innovation and sustainability. Our goal is to build 70% faster and 20% cheaper, delivering residences that epitomize elegance and minimalism harmonized with Portugal’s natural beauty.” You can find out more on the company’s website HERE.A look at the backyard, including a poolWhat do you think about the use of 3D printing and AI in building construction? Let us know in a comment below or on our LinkedIn, Facebook, and Twitter pages! Don’t forget to sign up for our free weekly newsletter here, the latest 3D printing news straight to your inbox! You can also find all our videos on our YouTube channel.*All Photo Credits: Liethaus